Supplier Integration: Are Your Suppliers Integrated with Your PLM Processes?
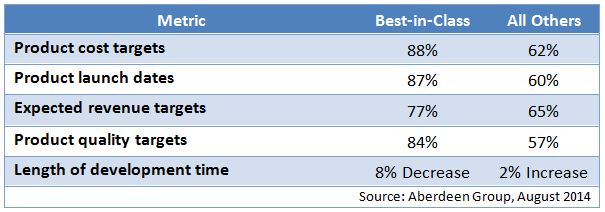
I’m pleased to introduce to you our guest blogger, Reid Paquin, Research Analyst, Manufacturing from the Aberdeen Group. Reid will highlight the importance of supplier integration with your PLM processes to keep your business on schedule and avoid unplanned disruptions.
The pressure to get new products to market faster and at the lowest possible cost is driving companies to take whatever measures necessary to meet those demands. Rather than everything being done in house, companies have recognized the option of leveraging external resources where they are constrained or do not have the expertise internally. Managing all of the touch points with suppliers in a comprehensive, coordinated manner is a growing challenge. A company may have a few select “key” suppliers that are tightly integrated and viewed more as an extension of the organization than an outside partner, but what about the many lower tier suppliers that make up your network?
While it’s true that these lower level suppliers do not provide a similar volume of work to the company, they are still critical to success. Particularly when the on-time complete of even low volume components and subassemblies can impact high value final assemblies and key high volume customers. Not enough companies adequately connect and coordinate with these suppliers, greatly increasing risk in the business. EVERY supplier needs to be viewed as a strategic partner in the design process. Even though the amount of suppliers employed by companies is increasing, Aberdeen’s recent research has identified supply chain management as one of the most inefficient areas for product developers (Figure 1).
Figure 1: State of Working with the Supply Chain
As you can see in the chart, less than 10% of respondents indicated that they are satisfied (not needing improvement) in the key processes affecting supply chain interactions. Issues within the supply chain can have impacts on the more overall product goals like launch, cost, or revenue targets. For instance, missed targets due to errors in design data, not understanding cost drivers early in the product lifecycle, or not understanding supply chain impact before changes are approved. Another concern is compliance. It only takes one node of the supply chain to become noncompliant and one small design flaw or component to halt production. Worst of all, companies are usually not aware there is an issue until it is too late. Product design and supplier collaboration is needed, how do you do it effectively is the bigger question.
Getting these fundamentals aligned is critical in keeping the business on schedule and avoiding unplanned disruptions. It is about breaking down the silos between these groups to run the business more successfully and ingraining collaboration into the DNA of the enterprise. The way that Best-in-Class companies are addressing this issue is by utilizing technology. Investments in PLM and the cloud can be utilized to provide lower tier suppliers a platform that enables collaboration and coordination. The table below shows how the Best-in-Class are performing as a group, clearly they are doing something right.
Table 1: Best-in-Class Outperforming their Peers
So this begs the question, are your suppliers, even the lower volume ones, integrated with your PLM processes?
In my upcoming blogs we will examine four use cases (exchanging design data, direct material sourcing, supplier substance declarations, and supplier program management) to illustrate what the Best-in-Class are doing and why tight integration with your supplier base is so important.
About the Blogger: As a Research Analyst in Aberdeen, Reid studies how manufacturing enterprises manage processes, people, and technologies to address continually changing market pressures. His current research at Aberdeen focuses on steps companies must take during the development process, from concept to design release, to ensure the success of its products.
Prior to Aberdeen, Reid worked in the Industrial Engineering department at a textile manufacturer. Reid holds a Bachelor of Science in Mathematics with a Minor in Economics, a graduate certificate in Industrial Statistics, and a M.S. in Statistics from the University of New Hampshire (UNH).