Maximize quality with FMEA
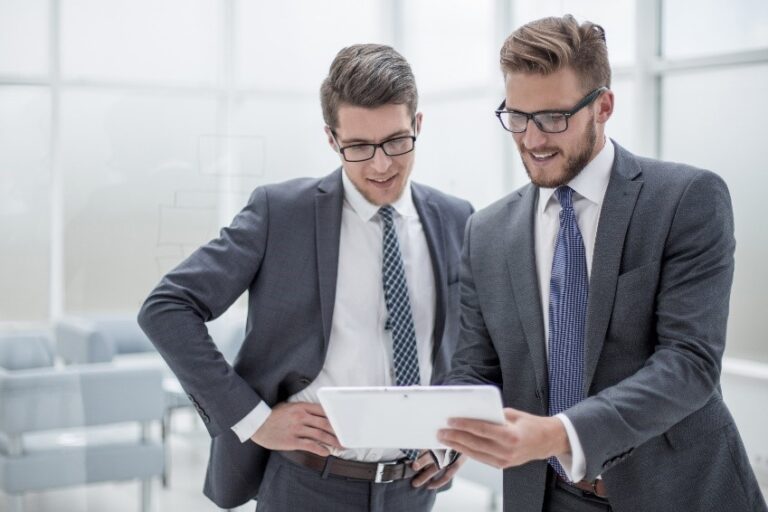
Why do we need FMEA to address quality requirements?
How do you, as a manufacturer, stay competitive?
The answer is fairly obvious – you need to decrease product and operational costs, and cultivate product quality.
Easier said that done! It requires a trade-off between cost, time, and the necessity to meet customer requirements.
A new product starts its lifecycle as a requirement. You need to consider all customer expectations and then build quality into the design of both the product and the process.
You must fully address the quality requirements before the final product rolls off the production line.
It truly helps avoid deviations.
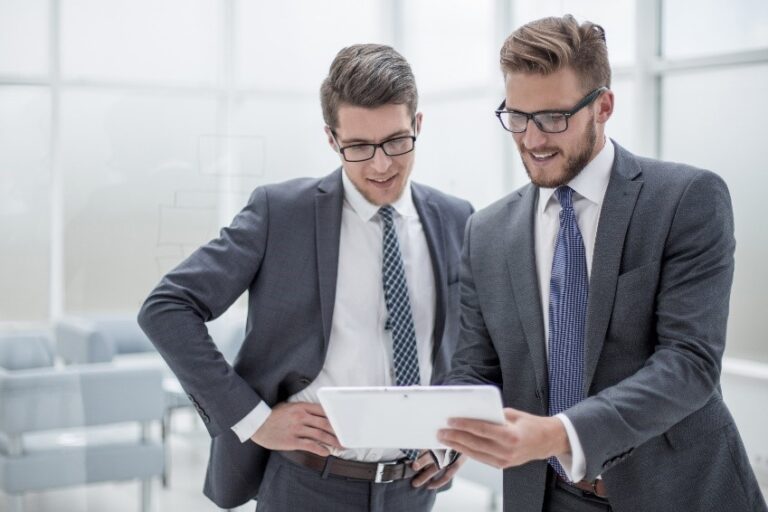
Why not to do it later?
Deviations in later product phases can be expensive and less effective in delivering high-quality results. Making the wrong decisions early in the process can have a long-term negative impact on your business.
How to achieve fast and cost-effective development?
The answer is with FMEA – a forward-thinking Failure Modes and Effects Analysis solution.
It is one of the best tools a company can use to avoid product defects and process faults.
FMEA provides the toolset to recognize and moderate risks in the virtual product and process structures. The FMEA is a cross-functional methodology touching the entire product realization process.
It is possible to distinguish between Design FMEA (D-FMEA) and Process FMEA (P-FMEA).
Siemens shapes its systems to support digital transformation across the entire product lifecycle with the involvement of FMEA. This holistic vision allows manufacturers to assess effects caused by potential defects and risks early in the planning stage by seeing all the pertinent domains and steps.
What’s the first step?
On Teamcenter collaboration platform, the value of analysis is extended. You have direct access to all engineering data such as BOMs, BOPs, drawings and 3D models.
You can manage FMEA throughout the product lifecycle and utilizing Teamcenter Quality FMEA.
Teamcenter Quality FMEA allows you to support FMEA planning in accordance with the specification of the new harmonized AIAG and VDA standard.
Use the capabilities of quality project management solutions – assess and reduce identified risks with an action tracking and alert mechanism. Organize people and responsibilities in a project around FMEA.
Manage residual risks can be by using the control plan and closing the loop with problem-solving and change management processes.
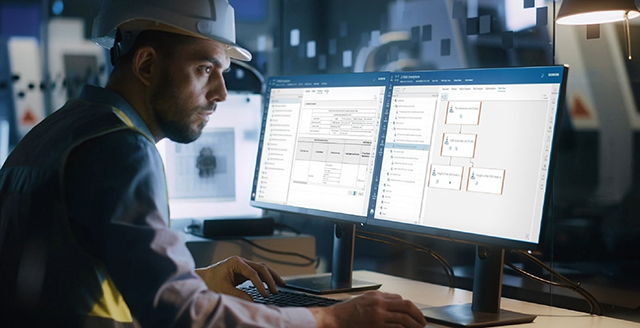
FMEA within PLM system
Behind the advantages of the methodology itself, it is essential to gather data in a comprehensive knowledge database that can be accessed by all relevant experts.
Applying past experience to new projects to shorten the development process cycle and minimize defects at the launch of the production cycle.
Leverage a quality solution natively built in a PLM platform to benefit from:
- One single system of record and a unique source for product information
- Feedback in context of PLM data with full traceability and linkages
- Quality actions and tasks are defined, and managed, as part of quality issues and change management processes
Learn more about the FMEA at our upcoming webinar!
Our special guest, Axel Eicker – Senior Product Manager, Teamcenter Quality FMEA, will guide us in a deeper understanding of the process and explain how Siemens solution can support quality initiatives.
How to maximize the value of quality management within PLM?
Quality Management. Closed-loop quality solution leverages Teamcenter backbone.