Getting a Handle on Design Data Exchange and Supplier Program Management
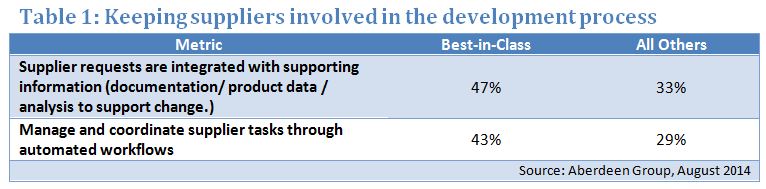
In this post in our Supplier Integration blog series, Aberdeen Group guest blogger Reid Paquin examines high-value business processes where supplier participation is integral – Design Data Exchange and Supplier Program Management.
In my last blog Are your suppliers integrated with your PLM processes? I explored the importance of supplier integration to PLM processes. In this blog, I wanted to examine two more high-value business processes where supplier participation is integral – design data exchange and supplier program management, and see what our Best-in-Class companies are doing to be successful.
Design Data Exchange:
Sharing design data with suppliers has always been a challenge. What information does the supplier actually need, how can you ensure your IP stays secure, what is the best way to enable data exchange with those outside the enterprise? How can you coordinate design change control and serialized configuration control? Best-in-Class companies realize that it all starts with how they manage and store their design or CAD data, it must be centralized and managed holistically to provide optimal support for collaborative engineering processes.
The Best-in-Class are 50% more likely to store and provide their product data in a centralized database. They have a holistic view of their product structure which is provided through their PLM systems; this is the backbone for an efficient, secure, and scalable solution for engineering data exchange. Beyond this, a secure publish and subscribe methodology into a supplier portal, integrated into the common enterprise workflow and change processes bring the suppliers into the design data exchange process. This common framework for suppliers, especially those suppliers that may not be tightly integrated with your company, is critical for collaboration with these suppliers. All others on the other hand rely on multiple databases (spreadsheets normally), emails, FTP utilities which results in inefficient and ad-hoc data exchange processes and supplier data being out of sync with your product BOM or the serialized design configurations of products in the field. Additionally, these ad-hoc exchange mechanisms are not entirely secure and cannot be easily audited and tracked.
Supplier Program Management:
Suppliers play a major role in the effectiveness of a company’s NPI process and can make or break a successful release. For poor performers, suppliers are seen as necessary speed bumps— third parties who can potentially derail the launch of a new product with one non-conforming part or late shipment. For the Best-in-Class, suppliers are viewed as strategic partners— key contributors to NPI and capturing maximum market share.
Successful companies back up that thinking with the capabilities they possess, shown in the table above. First, the Best-in-Class are 43% more likely to integrate supplier requests with supporting information. This is really just an extension of the design data exchange we looked at earlier and provides a common PLM-based framework to help OEMs and suppliers share data and collaborate throughout the development cycle tracking miscellaneous supplier deliverables (like PPAP in Automotive), keeping projects on target and this data tracked. The Best-in-Class are also 48% more likely to manage and coordinate supplier tasks through automated workflows. The use of PLM to manage supplier tasks keeps the supply chain tightly integrated into the development process, greatly reducing risk in your business. To ensure that suppliers, and projects as a whole, are going to stay on target visibility needs to be stressed between you and your supplier.
These two business processes, plus direct materials sourcing (which I will examine in my next blog), are high value processes in a company. Simply stated supplier collaboration is critical. If improving time to market, meeting development budget targets and improved quality are key metrics for your company, then improved supplier interactions should be a focus. Look towards a system that can provide the capabilities highlighted earlier. Investments in PLM and the cloud are being utilized by the Best-in-Class to provide suppliers, a standard platform that enables collaboration and coordination with teams from product introduction to field service.
About the Blogger: As a Research Analyst in Aberdeen, Reid studies how manufacturing enterprises manage processes, people, and technologies to address continually changing market pressures. His current research at Aberdeen focuses on steps companies must take during the development process, from concept to design release, to ensure the success of its products.
Prior to Aberdeen, Reid worked in the Industrial Engineering department at a textile manufacturer. Reid holds a Bachelor of Science in Mathematics with a Minor in Economics, a graduate certificate in Industrial Statistics, and a M.S. in Statistics from the University of New Hampshire (UNH).
For more information, please visit the Siemens PLM Teamcenter web page at http://www.plm.automation.siemens.com/en_us/products/teamcenter/supplier-integration/index.shtml
Comments