Use clash detection to resolve clearance issues
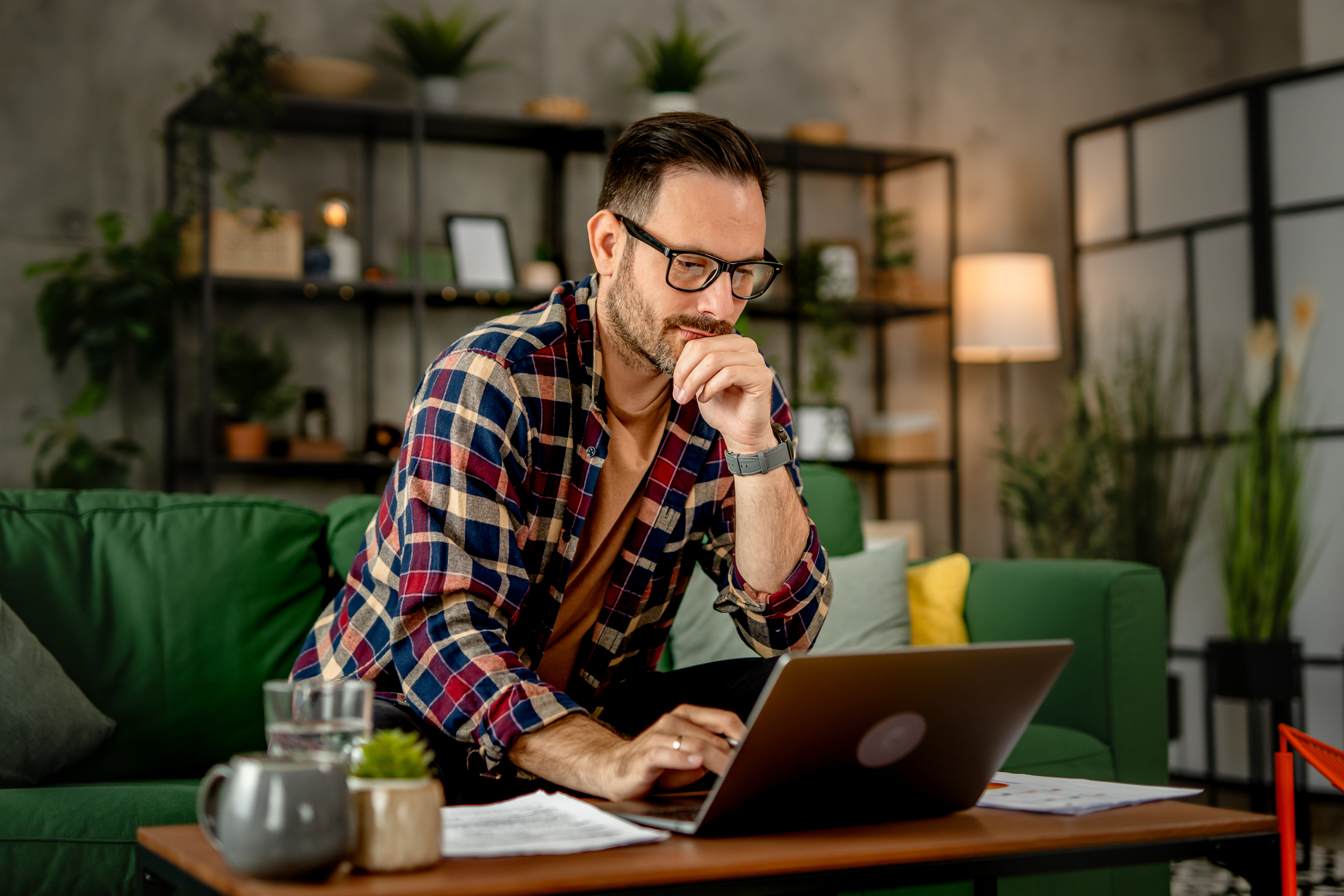
Streamline your design process
Easily manage and resolve clearance issues across your enterprise with Teamcenterβs integrated clash detection.
Integrated clash detection plays a vital role in industries focused on ensuring design integrity and manufacturing efficiency. Available within the Teamcenter Visualization Analysis Option, this feature automates the detection of clashes between components during the design phase, preventing costly errors and rework downstream. The Teamcenter 2406 release introduces exciting enhancements to this capability that will enable you to further accelerate the clash and clearance analysis and disposition workflow.
Expanded stakeholder access through Active Workspace integration
In the Teamcenter 2406 release, Siemens expands clearance management by integrating clash results into Teamcenter Active Workspace. Now, users can load and filter existing clearance results, analyze individual incidents, and disposition them directly within the web client. This enables stakeholders across the enterprise to streamline their design process by identifying and addressing issues early in the process, enhancing teamwork efficiency and reducing potential delays.
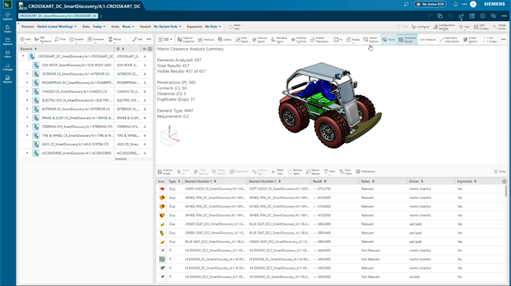
Key features for accelerated clash and clearance analysis
Clearance results in Active Workspace
Clearance results stored in the Teamcenter Clearance database are now accessible in Active Workspace, appearing as a list at the bottom of the graphics window. Each row represents a specific clash, clearance, or contact event, with adjustable columns tailored to your requirements. The list is powered by the data stored in the clearance database.
Graphical clash assessment
To evaluate a clash, simply enable analysis mode and select the corresponding row. Each incident can be evaluated in a graphical, interactive manner, with penetration points clearly marked. Additional annotations, such as penetration vectors or measurement labels, can be added to provide further context.
Image gallery support
For every clearance incidentβwhether a penetration, contact, or distance violationβpictures are generated as part of the background process and stored in the clearance database. These images can be added to the incident report in order to improve your understanding of the clash and accelerate the time to resolution.
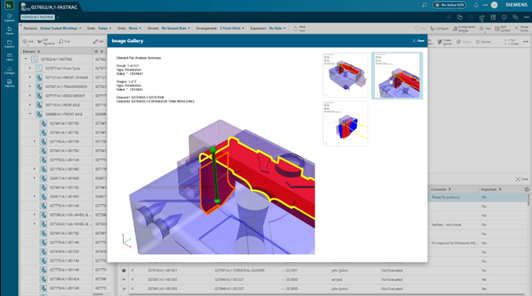
Disposition clearance incidents
Once an incident is evaluated, users can proceed with dispositioning. You can assign a severity level, update the status, add comments, or assign an owner to track the issue. This information is stored in the clearance database, aligning with future batch calculations for easy tracking and resolution by project milestones.
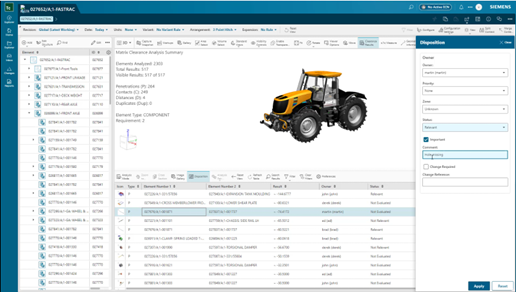
Flexible filtering options
To help users focus on relevant incidents, Teamcenter offers several filtering methods:
- Column-based filtering for specific data
- Filtering based on visible or selected components
- Smart discovery filters that adjust the results list accordingly
Key benefits of integrated clash detection in Teamcenter
By embedding clash analysis into the product lifecycle, Teamcenter delivers several critical benefits:
Design validation and verification
- Identify and resolve clashes early in the design phase.
- Ensure parts fit together correctly and can be assembled without issues.
Improved quality and reliability
- Eliminate potential manufacturing errors caused by clashes.
- Enhance overall product quality by minimizing design flaws or assembly errors.
Cost reduction
- Catch design issues before physical prototyping or production, avoiding costly rework.
- Reduce waste and scrap by preventing manufacturing defects caused by clashes.
Time savings and efficiency
- Streamline the design process by automating clash detection and resolution.
- Accelerate time-to-market by resolving design issues promptly.
Enhanced collaboration
- Facilitate better collaboration among design, engineering, and manufacturing teams by providing a common platform to identify and resolve clashes.
- Improve communication and understanding of design constraints across different departments.
Compliance and safety
- Ensure compliance with safety and regulatory standards by addressing potential clashes that could affect product performance or safety.
Deliver higher quality products while reducing time-to-market
Integrating clash detection within Teamcenter helps organizations design better products, minimize risks, and reduce costs throughout the product lifecycle. By identifying potential clashes early, teams can optimize designs, ensure compliance, and maintain a competitive edge in the market.
Learn more about lifecycle visualization
Explore Teamcenterβs product visualization solutions
Ready to explore Teamcenter X, the leading cloud PLM?
No matter how you choose to deploy Teamcenter,
you get the same proven solutions designed to help you innovate faster.