Shop Floor Work Instructions Made Easier
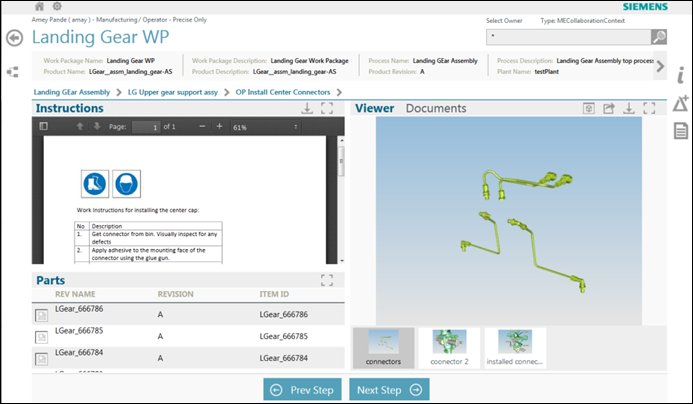
How do you create the work instructions for your shop floor workers? How do you reconcile them with the manufacturing structure? How do you communicate changes?
If you’re using paper-based methods to create and communicate work instructions or finding your electronic methods cumbersome, you may want to consider switching to interactive, PLM-based electronic work instruction.
Electronic work instruction (EWI) refers to computerized visual tools to instruct shop floor workers to perform their jobs. Unlike paper-based work instructions, electronic work instructions may also include 3D models of the parts to be assembled, information about the tools as well as product and manufacturing information (PMI). In addition, EWI may be interactive, allowing the reader to manipulate the 3D view, play animated assembly sequences as well as browse through a sequential list of steps to be performed per job order.
EWI is in use by many manufacturers from various industry segments. Any production line that requires manual operations requires a certain level of shop floor documentation. Regulated industries such as aerospace and shipbuilding must invest significant efforts to define and implement high standards for shop floor documentation. In many cases, government regulations mandate that shop floor documents meet certain criteria.
There is no single way to author work instructions. Some manufacturers may use inexpensive Microsoft Office® software tools to author documents, while others implement integrated work instruction and routing planning tools. In general, work instructions are tightly connected to the engineering design and manufacturing planning processes, constituting a significant component of the communication flow. Authoring of work instructions requires the availability of engineering and manufacturing information, as well as the validity of assembly processes. In some cases, work instructions may include instructions for machine operators. Shop floor work instructions also have to satisfy intra-company formatting and layout standards. Therefore, customized template creation is a key requirement of any work instructions solution.
Traditionally, work instructions would be printed and distributed to the shop floor with accompanying 2D engineering drawings. Many manufacturers still use that method, at least partially. Electronic work instruction, however, may be embedded into the enterprise manufacturing execution system (MES). This allows manufacturers to combine all manufacturing execution tasks and information into a single backbone, and to link the work instructions to work orders, resources and parts stock. MES systems also allow data collection which is required for many processes (for example, nonconformance).
Building on the value of MES-based electronic work instructions, Siemens PLM Software now offers an end-to-end, PLM-based solution for work instruction authoring and publishing. With the new release of the Active Workspace 2.1 client for Teamcenter, the Tecnomatix EWI 2.1 solution is now available on any smart device in a simple, task-specific user interface.
The basic concept is that the entire authoring process – from engineering design through manufacturing planning to shop floor execution – is performed using product lifecycle management (PLM) software. PLM applications support the workflow, and the work instruction data, including CAD-neutral visualization using the JT format. The PLM system manages electronic work instructions in one single source that spans the lifecycle, from Design to Manufacturing Planning to Process Instructions Planning to Execution.
Because the authoring process is managed using a single PLM backbone, your company reduces the risk of quality escapes, increases engineering efficiency and eliminates the need for data conversion. The PLM system supports smooth change management, minimizes data conversion and provides state-of-the-art 3D-based interactive authoring. Your company can realize significant savings in engineering time, as well as minimize time spent by manufacturing experts on the shop floor.