Discover the benefits of using PLM software for design reviews
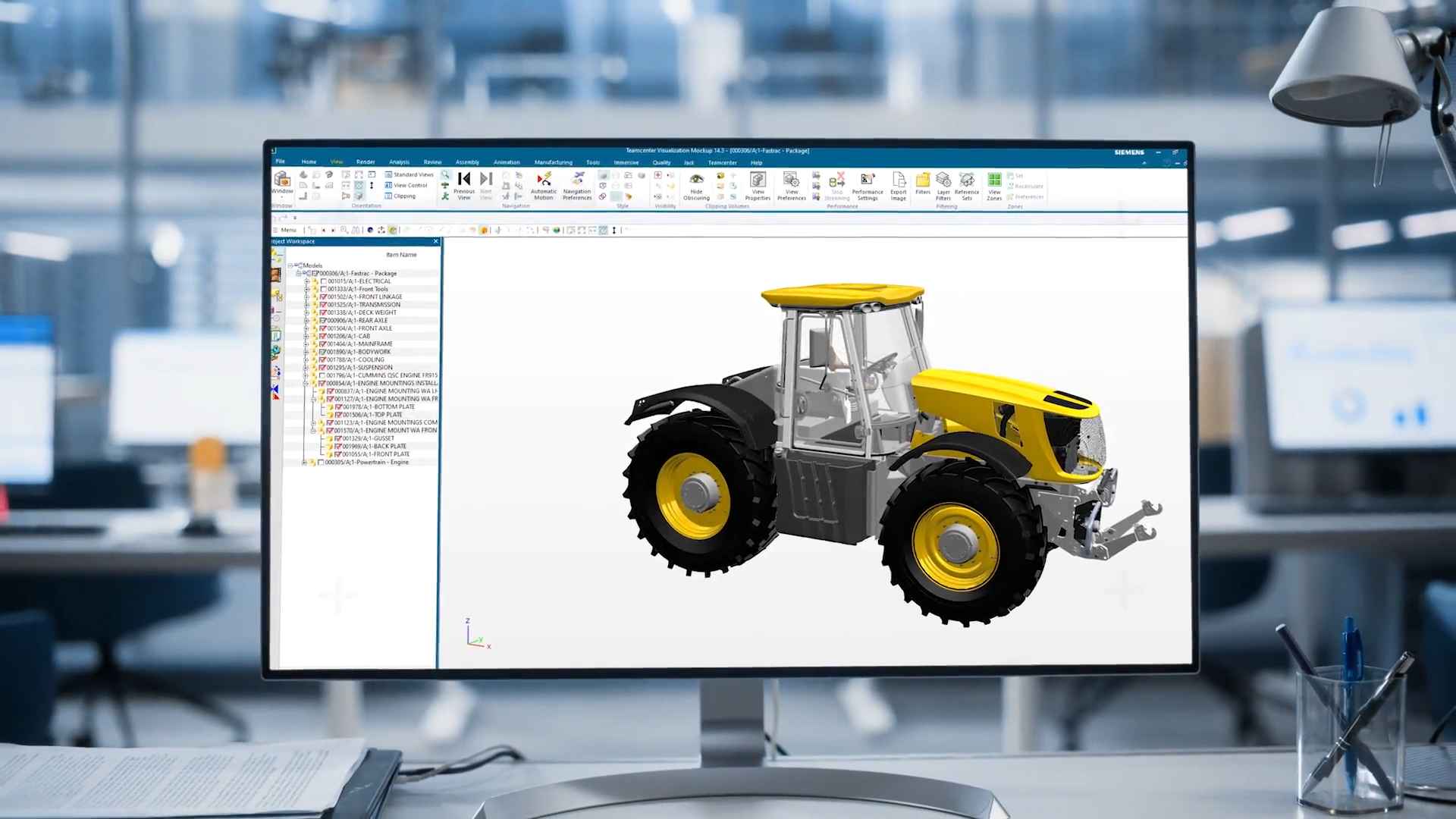
Introduction
In the fast-paced world of product development, ensuring that product designs meet requirements and are âproduction readyâ is paramount. Design reviews play a pivotal role here. They allow product teams to scrutinize designs, exchange feedback, and optimize product specifications. But the tools and processes that organizations use to manage design reviews makes a big difference. This article explores why product teams should conduct and manage design reviews using PLM software.
Main components of PLM for design reviews
PLM software includes several components and many of them may come into play for design reviews. In this section weâll describe the four PLM software components that are essential to utilizing PLM for design reviews.
Document and model visualization
Advanced, multi-CAD, multi-BOM visualization is an essential PLM component for viewing the wide variety of content types encountered in design reviews. Design review participants need to be able to view and interact with a range of design documents, 2D drawings, 3D models, and other relevant project files. Further, they need a system thatâs capable of supporting basic analysis and interrogation of 3D models, such as measurement, sectioning and viewing product manufacturing information (PMI). And as products are typically represented by their various bill of materials (BOM), itâs critical to have a tight coupling between model visualization and the BOM system. A BOM-driven visualization system enables design review participants to view any BOM in any configuration.
All of these capabilities enable a range of design review use cases. For example, engineers can closely examine drawings to identify potential design flaws, while marketers can visualize the productâs aesthetics and user experience. This shared understanding enhances collaboration among diverse teams, promoting a holistic evaluation of the designâs strengths and weaknesses.
Collaboration and communication
Collaboration is at the core of successful design reviews. With PLM software, participants can collaborate in the context of their product data, which provides significant advantages over other collaboration tools. Stakeholders can engage in real-time or asynchronous discussions, tag participants, and receive notifications. They can also add markups such as annotations, measurements, and callouts directly onto the models, as well as capture and share snapshots.
Taken together, these features improve the quality and efficiency of collaboration amongst reviewers. And by consolidating all collaboration and communication activities onto a single platform, ensures no communication is lost.
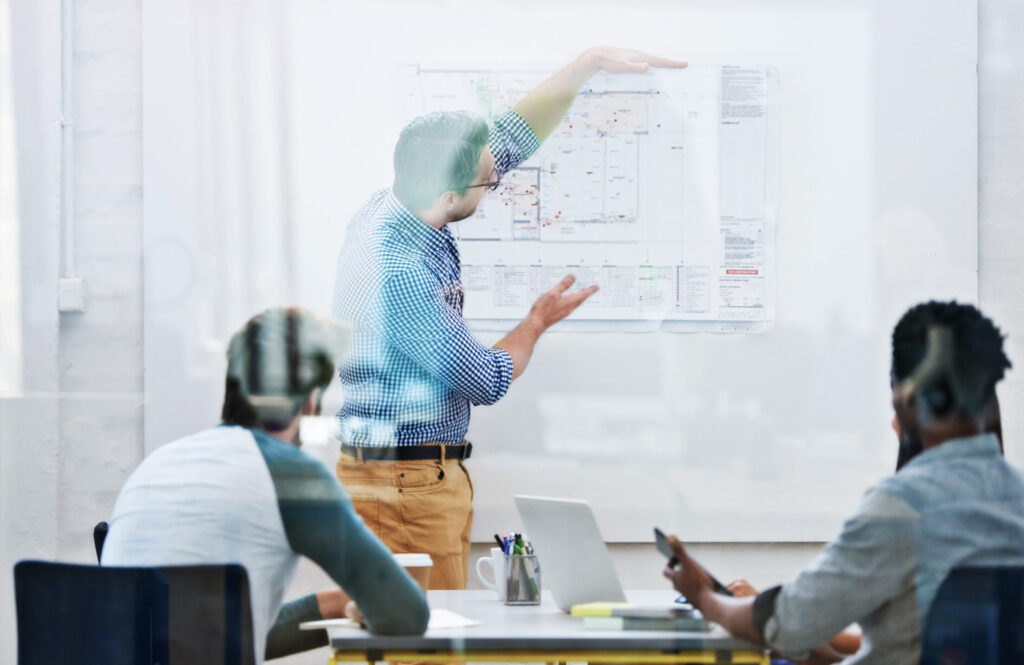
DMU analysis
Most design review tools are limited in functionality to visualization and collaboration. Any further analysis typically needs to be performed outside the design review environment using domain specific tools, such as CAD, CAE, and manufacturing planning. With Teamcenter Visualization, design review participants can analyze and validate products against domain-specific criteria â all from a single visual context. It consolidates DMU analysis capabilities from across domains and engineering disciplines â so users can perform a range of DMU analysis in context of their product data, directly from their PLM environment.
By leveraging DMU analysis tools, product teams can perform in-depth evaluations of the designâs functionality, performance, and adherence to industry standards, as well as validate the design against domain-specific criteria, such as quality, cost, manufacturability, and serviceability.
Integrated environment
While each of the above components is essential, the true power of utilizing PLM for design reviews is that all activity is managed in the system of record for product data. An integrated DMU environment represents a unified, centralized platform where product information and changes are managed comprehensively. It serves as the source of truth for all product-related data and orchestrates design review processes seamlessly. Design review activities are tightly integrated with other PLM capabilities, such as product data management, change management, and workflow automation. This ensures that design reviews are conducted within the broader context of the product lifecycle, aligning design decisions with overall project objectives and requirements.
Benefits of utilizing PLM for design reviews
Now that weâve explored the four essential components of PLM for design reviews, letâs discuss the benefits of using PLM software to conduct and manage design reviews.
Holistic product lifecycle management: PLM software offers a comprehensive platform for managing the entire product lifecycle, from concept to end-of-life. It provides a holistic view that encompasses design, engineering, manufacturing, and maintenance; ensuring that design reviews consider broader implications and align with the productâs long-term goals.
Efficient collaboration: Unlike tools such as PowerPoint or Excel, which are primarily designed for documentation and presentation, PLM softwareâs collaboration and communication tools are purpose-built for the iterative and collaborative nature of design reviews. Real-time collaboration, comments, markups, and notifications are seamlessly integrated into the review process.
Version control and traceability: PLM systems excel in version control and traceability. They maintain a clear audit trail of design review activities, ensuring accountability and compliance. This is in contrast to standalone tools that may lack version control capabilities, leading to confusion over document versions.
Robust analysis: The advanced DMU technology of today offers significant advantages over physical mockups. It allows design review participants to analyze and validate products in a realistic and virtual environment, enabling thorough evaluations of functionality, manufacturability, and serviceability. This reduces the need for costly physical prototypes and accelerates the development timeline.
Integration and data management: PLM software acts as a central repository for all product-related data, including design files, specifications, and review records. This integration enhances data consistency, security, and accessibility. In contrast, using file management systems that are disconnected from your PLM system may result in fragmented data and increased risk of data loss.
Streamlined workflows: PLM software includes workflow management capabilities that guide the design review process from initiation to completion. This ensures that reviews follow a structured sequence, approvals are obtained, and actions are taken promptly, minimizing delays and bottlenecks.
Conclusion
In the fast-paced world of product development, conducting effective design reviews is critical to creating successful products. Leveraging the design review capabilities of your PLM environment, offers a comprehensive solution to meet this goal. With its components for document and model visualization, collaboration and communication, DMU analysis, and an integrated DMU environment, PLM software streamlines the review process, enhances collaboration, and ensures that design decisions align with overall project objectives. Ultimately, this approach leads to more efficient, cost-effective, and successful product development outcomes.
Ready to explore Teamcenter X, the leading cloud PLM?
No matter how you choose to deploy Teamcenter,
you get the same proven solutions designed to help you innovate faster.