How to Reduce Your CO2 Footprint with Advanced Planning and Scheduling: A Guide to Green Manufacturing
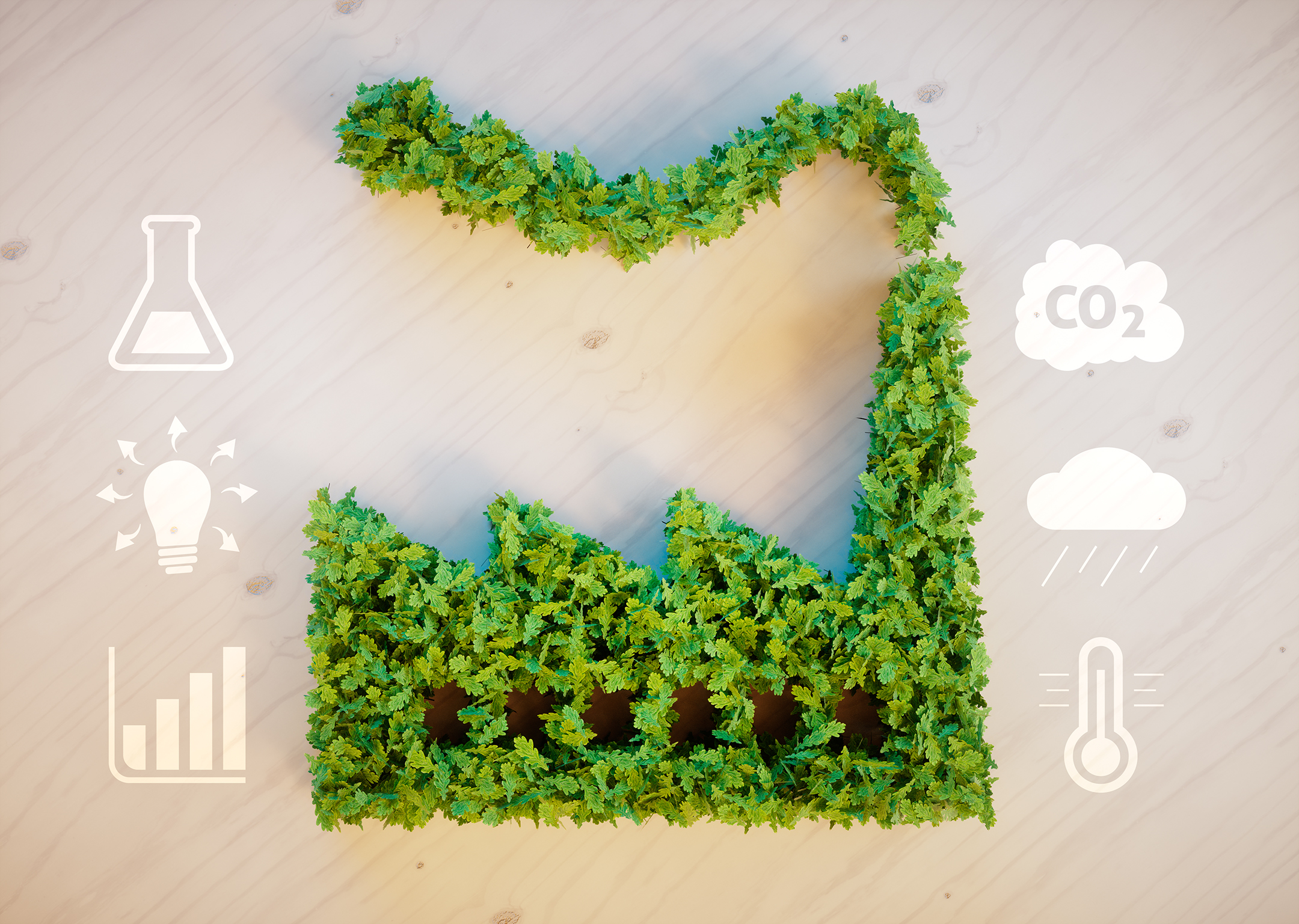
The Urgency of Sustainable Manufacturing
The manufacturing sector is a cornerstone of the global economy, driving innovation and progress. However, this progress comes with a significant environmental cost. Manufacturing processes are a major contributor to greenhouse gas emissions, particularly carbon dioxide (CO2). As the urgency to combat climate change intensifies, manufacturers face a growing imperative: reduce their environmental impact while maintaining operational excellence.
This is where Green Scheduling emerges as a transformative approach. Green Scheduling goes beyond traditional production planning methods by integrating sustainability principles with efficient scheduling practices. It’s a win-win scenario, allowing manufacturers to significantly reduce their CO2 footprint while optimizing production processes and potentially improving overall profitability.
Understanding the CO2 Footprint of Manufacturing
Before diving into Green Scheduling, it’s crucial to understand how traditional scheduling practices can contribute to a larger CO2 footprint. Here are some key areas of concern:
- Inefficient Production Sequencing: Frequent machine switching and unnecessary travel distances during production consume excessive energy.
- Excessive Idle Time: Periods where machines are not actively working lead to wasted energy.
- Poor Resource Utilization: Frequent machine reconfiguration for jobs requiring different resources consumes additional energy.
These inefficiencies translate directly to higher energy consumption, leading to a larger CO2 footprint associated with your manufacturing operations.
How Green Scheduling Optimizes for Sustainability
Green Scheduling tackles these inefficiencies head-on, focusing on several key areas to make your production process more environmentally friendly:
- Production Sequence Optimization: Green Scheduling prioritizes arranging jobs to minimize machine switching and travel distances. This reduces the energy required for equipment operation, leading to lower CO2 emissions. Imagine a scenario where you need to drill holes in different parts. Traditionally, you might switch the drill bit for each part, leading to multiple switch-ons and -offs. Green Scheduling would group jobs requiring the same drill bit together, minimizing these energy-consuming transitions.
- Minimizing Idle Time: Green Scheduling aims to keep machines running efficiently, minimizing periods of inactivity. This translates to a more streamlined production flow and reduced overall energy demand. Imagine a scenario where a machine sits idle for extended periods between jobs. Green Scheduling would optimize the schedule to ensure minimal gaps between tasks, maximizing machine utilization and reducing wasted energy.
- Batching Similar Jobs: Grouping jobs that require the same resources together optimizes energy usage compared to frequent machine reconfiguration. This reduces the number of times a machine needs to be adjusted for different settings, minimizing energy consumption associated with these transitions. Imagine a scenario where you need to paint components in different colors. Green Scheduling would batch jobs requiring the same paint color together, minimizing the need for cleaning and color changes between jobs.
Beyond CO2 Reduction: Additional Benefits of Green Scheduling
While the environmental benefits of Green Scheduling are significant, the advantages extend far beyond CO2 reduction:
- Reduced Operational Costs: Lower energy consumption translates to lower energy bills. Green Scheduling can also minimize waste by optimizing production processes, leading to further cost savings.
- Improved Production Efficiency: Optimized scheduling minimizes disruptions and downtime, resulting in smoother production flow and potentially increased output. Green Scheduling helps eliminate bottlenecks and ensure resources are used optimally, leading to faster production times and improved efficiency.
- Enhanced Brand Reputation: Consumers are increasingly environmentally conscious. Implementing Green Scheduling demonstrates your commitment to sustainability, attracting new customers and boosting brand loyalty. Consumers are more likely to choose brands that prioritize environmental responsibility. Green Scheduling allows you to showcase your commitment to sustainability and build a positive brand image.
Siemens Opcenter APS: Empowering Green Scheduling
Siemens Opcenter Advanced Planning and Scheduling (APS) software provides manufacturers with the tools and capabilities to implement Green Scheduling effectively. Opcenter goes beyond traditional scheduling tools, offering several key features that support a sustainable manufacturing strategy:
- Real-Time Data Integration: Opcenter integrates with various data sources, including energy consumption data, allowing for scheduling decisions that optimize both production efficiency and energy usage.
- Scenario Modeling: Opcenter allows you to simulate different scheduling scenarios, enabling you to assess the environmental impact of different production plans and choose the most sustainable option.
- Resource Optimization: Opcenter helps optimize resource utilization across your entire production process, minimizing energy waste and ensuring efficient use of equipment and materials.
Taking Action Towards a Sustainable Future
The path towards a greener future for manufacturing starts with adopting sustainable practices today. By implementing Green Scheduling with the help of Siemens Opcenter APS, you can significantly reduce your CO2 footprint while gaining a competitive edge:
- Download our White Paper: “Greening Production: How Advanced Planning and Scheduling minimizes CO2 footprint” This paper provides a comprehensive guide to Green Scheduling and its benefits.
- Contact us today for a personalized consultation on how Siemens Opcenter APS can optimize your production for sustainability and efficiency. Our experts will help you evaluate your specific needs.