(Part 1 of 2) A&D and Operational Excellence: Myths versus Reality
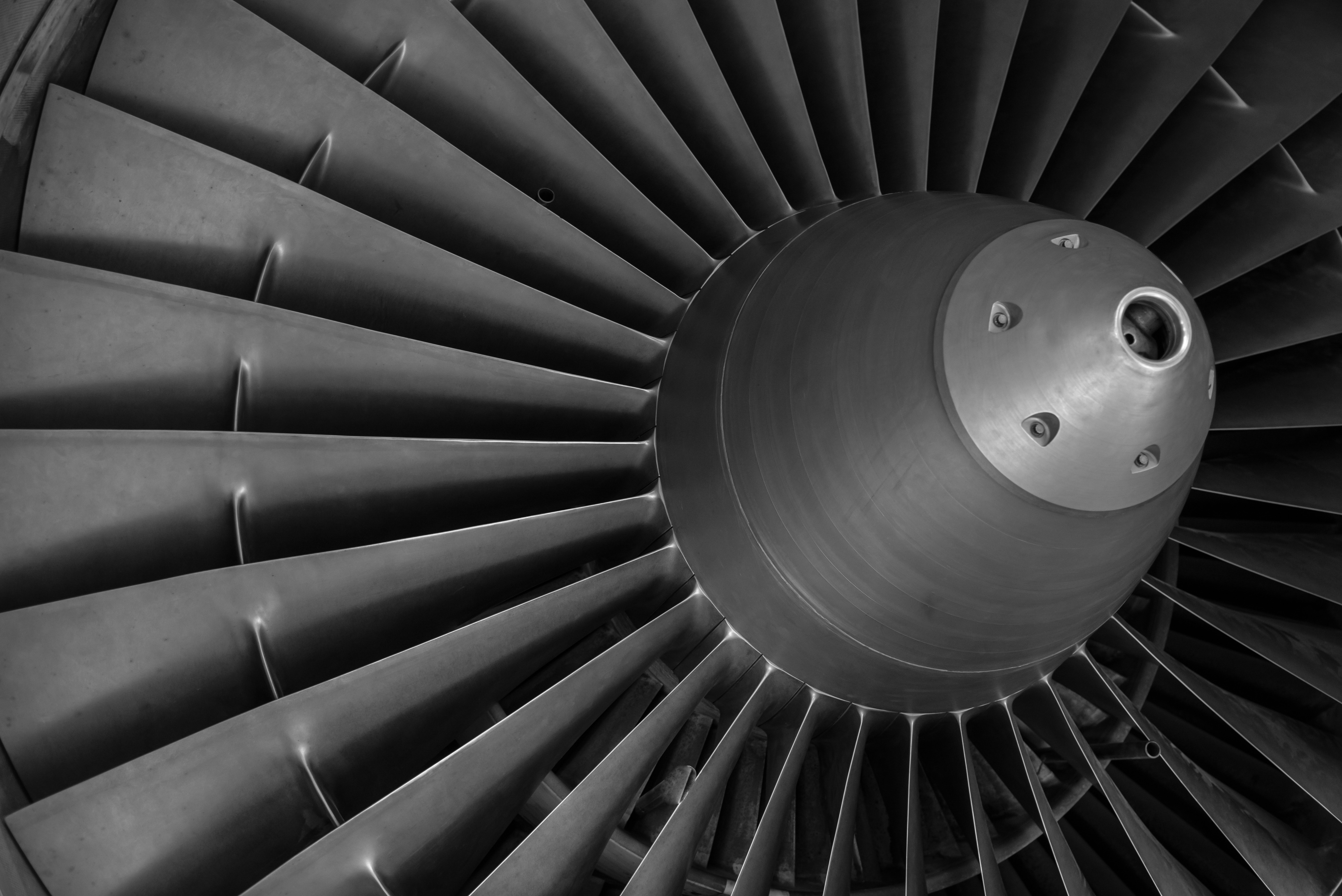
Having worked with A&D manufacturers for a couple of decades in their journey for manufacturing solutions across PLM/MOM/ERP, I have come to understand what is real and what is fiction (or at least somewhat fictitious) surrounding Operational Excellence in this industry.
I was asked recently to give my perspectives on this topic at an industry conference, which was the point at which I had to crystalize my experience, organizing it in a way that could be helpful for A&D manufacturers and their suppliers in their quest for excellence, as well as guide them on their digital transformation journey (which all manufacturers are on, whether they realize it or not). I’ll share that information with you here.
First, what is Operational Excellence? At the most basic level, it is the combination of efficiency and effectiveness. With efficiency, manufacturers are producing things faster based on cost and resource constraints. With effectiveness, manufacturers are producing the right products with right processes and tools to achieve their long-term strategy. When manufacturers are performing well across those two vectors, they are achieving operational excellence.
For the A&D industry specifically, there are some unique metrics due to the complexity of the products they build, the first article inspections, and regulations.
- Adherence to the shop-floor processes defined by manufacturing engineering
- Requirement for full traceability, to ensure the product meets the intent of the design
- Overall cost efficiency, including downtime, human resources (properly skilled and certified), machines (properly maintained), and supply chain
- Cost of non-conformances and rework, which are extremely high due to engineering reviews and design authority for approval of changes
- On-time delivery and full compliance
For A&D manufacturers, there are some specific characteristics that pose unique challenges to operational excellence, and performing well against those metrics. First, the shop floor across many manufacturers still operates on a large number of home grown systems, spreadsheets, extensions of ERP, and even paper. Although A&D product designs are driving towards more sophistication with latest technologies and PLM usage, the shop floor is still quite manual, including drawings, processes, and this array of disparate tools disconnected from engineering. This creates a huge inefficiency, because engineering changes are constant, driven by customer requests for design and configuration modifications, and synchronization with shop floor systems is not automated. This inefficiency, and the lack of clear visibility of the status of any product built on the shop floor, often puts the quality, change management and thus delivery schedule for the end customer at risk.
It also drives risk for first article inspection, or the first time through test yield. If all this information flow is not synchronized in the right way, we see additional factory inefficiencies with less importance on effectiveness measures. Lastly – in this industry, one of the key requirements is that the product be shipped to the customer with the alignment of as-designed and as-built records, and the validation of the design intent. This includes the full traceability and process adherence, which becomes hugely burdensome and error-prone with disconnected systems.
Now that I’ve described the common challenges for A&D (in general, many discrete manufacturers) in achieving operational excellence, I’ll describe what I’m seeing as the best-of-the-best manufacturing approaches to overcoming the challenges and reaching true operational excellence. Stay tuned for my next blog on this topic.