Optimizing the supplier part approval process in automotive

Are you looking to enhance your implementation of the part approval process in the automotive industry?
To overcome challenges, a comprehensive smart manufacturing ecosystem mitigates risks with a closed-loop approach. In the upcoming webinar, we will explore how a closed-loop quality (CLQ) management approach can provide the necessary end-to-end visibility for automotive OEMs and suppliers.
The impact of sustainability, disruptive technologies, and supply chain volatility
In the rapidly evolving automotive industry, ensuring business continuity and delivering products of requisite quality have become paramount for automotive OEMs and tier-suppliers. The challenges have intensified due to the evolving supply chain trends.
The landscape of the automotive industry is being shaped by sustainability, disruptive technologies, and supply chain volatility, prompting OEMs and tier suppliers to make more frequent and impactful changes to their products and processes. Effective collaboration and visibility across the supply chain have become crucial for automakers to navigate these complexities successfully.
Navigating supplier quality management challenges
Fierce competition for the automotive customer continues to place downward pressure on vehicle pricing. As a result, automotive manufacturers of all kinds keep seeking ways to shorten development cycles, boost traceability and reduce costs.
As automotive manufacturers know, quality issues arising anywhere in the supply chain have the potential to determine the success or failure of a vehicle model and could even put the OEM’s reputation and business at risk. The desire of every automotive company that receives components from a supplier, no matter their tier, is to have confidence in the quality of that supplier’s goods.
As companies strive to enhance quality and reduce costs, they are increasingly relying on suppliers to provide specific product parts and components, making suppliers a crucial aspect of a manufacturer’s business continuity and new product development.
Adapting supplier quality management strategies to enhance collaboration
With increased product and process changes, automotive manufacturers must closely monitor supplier performance, quality metrics, and project milestones to enable proactive issue identification and timely decision-making. OEMs and tier-suppliers struggle to maintain visibility and control over the vast amount of supplier data, documentation, and quality records. Granting the right level of access and permissions for suppliers to collaborate on the part approval process is a delicate balance requiring robust onboarding and management systems.
These challenges around managing information, controlling access, and overseeing work underscore the need for automotive manufacturers to adopt a comprehensive, closed-loop approach to supplier quality management, which can enhance collaboration, improve quality assurance, and help navigate the dynamic industry landscape.
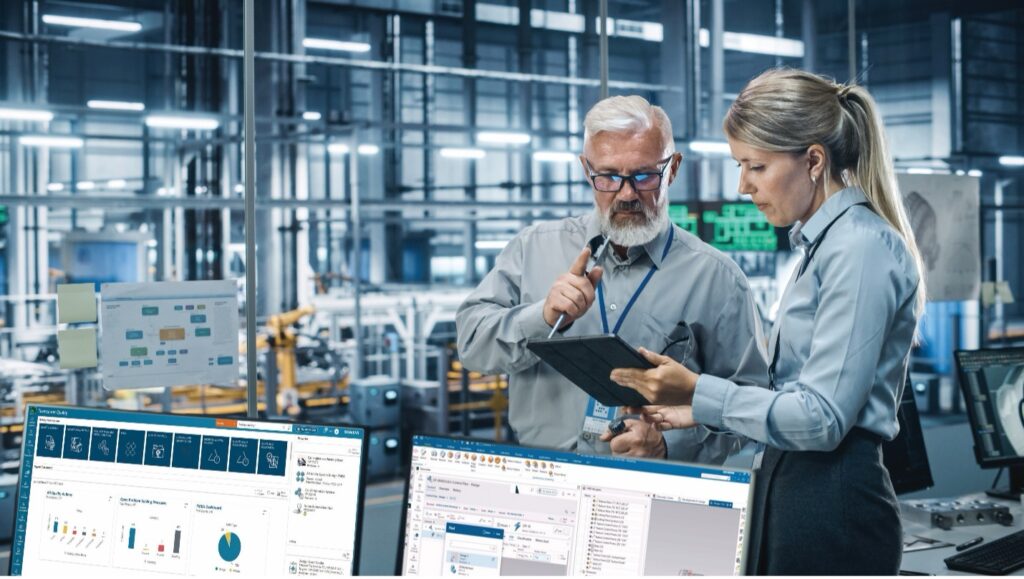
Navigating the requirements
As customer expectations for quality, reliability, and traceability continue to rise, manufacturers must adhere to standard requirements, such as the Production Part Approval Process (PPAP) by AIAG and Production Process and Product Approval (PPA) by VDA, to meet regulatory compliance. Implementing a comprehensive PPAP/PPA process can present challenges for manufacturers, including documentation management, supplier collaboration, and meeting strict submission deadlines. By understanding the key elements of the part approval process submission, manufacturers can streamline their part approval process and ensure that all requirements are met to guarantee product quality and compliance.
Enhancing quality and compliance through part approval process
By mastering the part approval process and leveraging best practices, manufacturers can enhance their quality control measures, minimize risks, and establish a solid foundation for continuous improvement. Effective part approval process implementation not only ensures that products meet design specifications and performance requirements but also fosters transparency, communication, and collaboration across the supply chain.
Leveraging smart manufacturing capabilities to stay ahead of part approval process
A closed-loop approach integrates product design, manufacturing design, quality and the supply chain to safeguard compliance and product integrity. Siemens’ Smart Manufacturing for automotive portfolio includes quality management solutions that enable OEMs and suppliers to break down barriers and adjust processes based on lessons learned.
Design, manufacturing, and quality teams can share the same views about the needed information to continuously improve product and process quality. With continuous improvement and seamless change management, issues are resolved faster, and costs are reduced.
When both OEMs and suppliers implement comprehensive and digital quality management solutions, they exceed the quality targets throughout production, and satisfy customers with reliable and high-quality products.
Having a deep dive into the quality solution
Join us on Wednesday, March 26, 2025 at 1PM CET. In this live webinar, we will explore how a closed-loop quality (CLQ) management approach facilitates a timely, efficient, and comprehensive production part approval process (PPAP/PPA), enabling successful supplier quality management.
We will explore:
- How to streamline the supplier PPAP/PPA process through digital collaboration and traceability
- How manufacturers can proactively identify and mitigate quality issues across the supply chain
- Best practices to drive continuous improvement in products, processes, and supplier relationships