Novak M responds to production changes 50 percent faster by streamlining production processes and scheduling
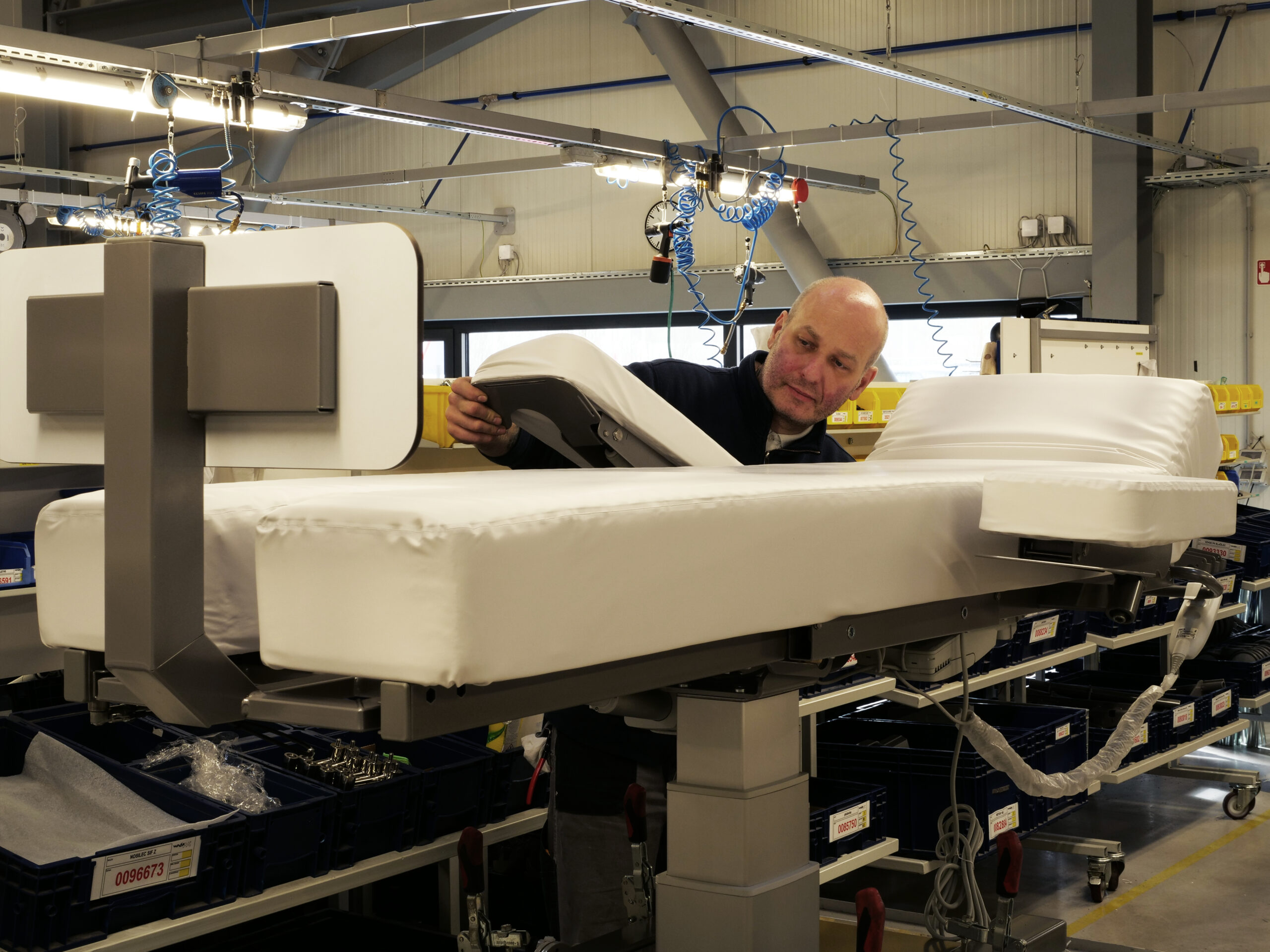
Novak M uses Opcenter to increase production response time, material preparation and ordering speeds
Supporting medical professionals and patient experiences
Novak M is a Slovenian, family-owned and globally oriented medical equipment manufacturer, developing high-quality medical equipment ranging from examination and treatment tables to therapy chairs and hospital stretchers. Since 1979, they have been combining industry expertise with innovative technology and staying in close contact with end users through distribution networks.
With the increase in production quantities, Novak M engineers were experiencing frequent changes in production schedules, making work difficult for their production scheduling department. Due to the large amount of data that engineers need to manage over the supply chain, the company realized that using spreadsheets was not powerful enough to handle their production scheduling any longer.
Benefiting from streamlined scheduling
Using Opcenter Scheduling, the company could create a schedule and assign every production operation to a qualified worker on the correct resource depending on their skills and availability. This provides an activity list to every worker in advance so they can prepare accordingly. As a result, workers can prepare the material for their scheduled operations on time, and they can add new orders to the plan 30 percent faster.
By leveraging Opcenter Scheduling, Novak M could respond to changes 50 percent faster. “Production scheduling with Opcenter is resilient to market changes, unexpected events in production and production planner absence,” says Tanja Jereb, the chief procurement officer at Novak M. “Using Opcenter Scheduling, the planner can quicky adjust the production plan when there is a change in a customer’s order, a worker’s availability, or a lack of materials.”
In addition, with help from Inea expert partner, the planner and management team were able to easily get custom reports based on the specific data they need. A final benefit of using Opcenter is that it also helps workers order from subcontractors 40 percent faster and without errors since the company could now schedule work operations and know precisely when they would complete certain tasks.
“Thanks to Novak M’s forward thinking, the company realized it needed a solution and initiated talks about supporting their production scheduling with a specialized solution,” says Tomaž Grabnar, the head of Opcenter APS program at Inea. “Their vision and dedication to constant improvement help them grow as a company and gain a better market position. I’m glad our team got a chance to be a part of their success story.”