NEW WHITE PAPER: Closed-Loop Manufacturing in MedTech
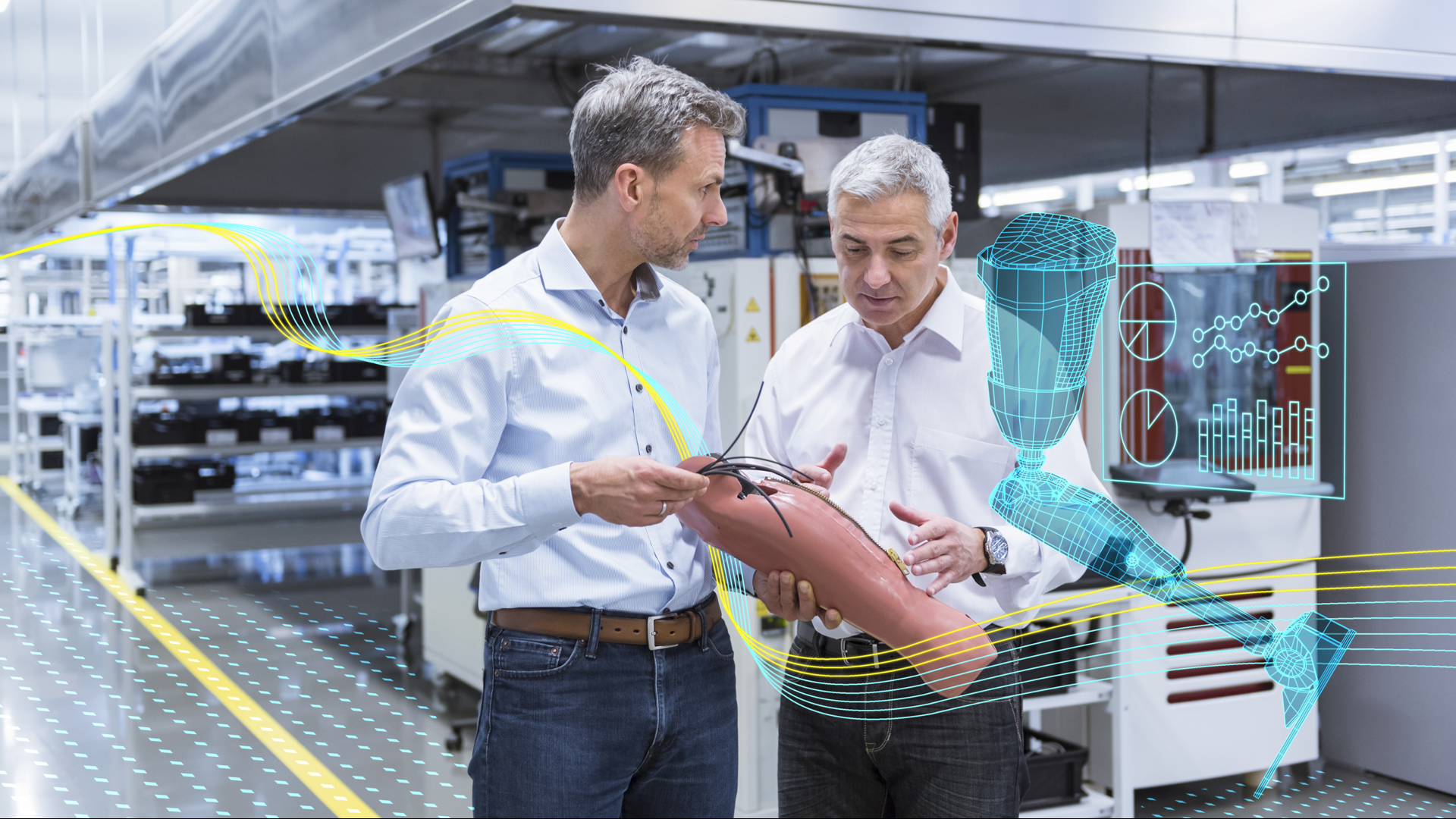
The changing healthcare landscape poses enormous pressure for medical device manufacturers. While they already operate in a complex, highly regulated industry, market dynamics such as global growth in the elderly population and the associated chronic diseases, as well as healthcare reimbursement models that are focusing on patient outcomes, are driving the need for innovation at consistently high quality and controlled cost levels. Globalization of manufacturing operations and the explosion in personalization and smart devices further complicates the process of innovation.
While the medical device industry continues to deliver innovative products to market, the historical focus on quality primarily as a regulatory compliance requirement versus a core business objective has been recognized by industry leaders, as well as regulators around the world. In response to this misplaced focus, the United States’ Food and Drug Administration (FDA) has established the Case for Quality program, while the European Union (EU) has completely revamped and modernized its regulatory framework to address quality and safety concerns more comprehensively across the entire device lifecycle.
In this environment, it is clear that the underlying internal development and manufacturing processes and systems also must innovate to enable manufacturers to accelerate product innovation while improving quality – a key metric that will dictate their success with patients and providers.
The innovation and digitalization of processes and systems is inevitable for medical device manufacturers.
The foundation must be anchored in intelligent, connected, collaborative systems that accelerate the exchange of information across the entire product lifecycle, driving quality, safety and reliability from idea inception through production and into service, and continuously feeding back relevant intelligence to optimize quality in real time at every step.
At the heart of digitalization is a closed-loop manufacturing (CLM) capability, which synchronizes and
optimizes production across product design, production planning, manufacturing execution, automation and intelligence. Creating a collaborative, connected information loop, CLM continuously improves the cost, time and quality of the manufacturing process to accelerate the delivery of new innovation.
The benefits of CLM directly address today’s medical device industry needs. Namely, the simultaneous achievement of:
- More rapid time-to-market
- Greater flexibility and agility with increasing change
- Improved product quality, safety and reliability
- Increased efficiency to lower costs globally
Siemens has recently released a white paper that details this step-by-step process to CLM and how a well-engineered infrastructure should operate for the digital manufacturing enterprise.
The time has come for manufacturing in the medical device industry to adopt the infrastructure that is essential for improving quality while making innovative, life-saving technology accessible for all patients.