Manufacturing Product Quality Excellence
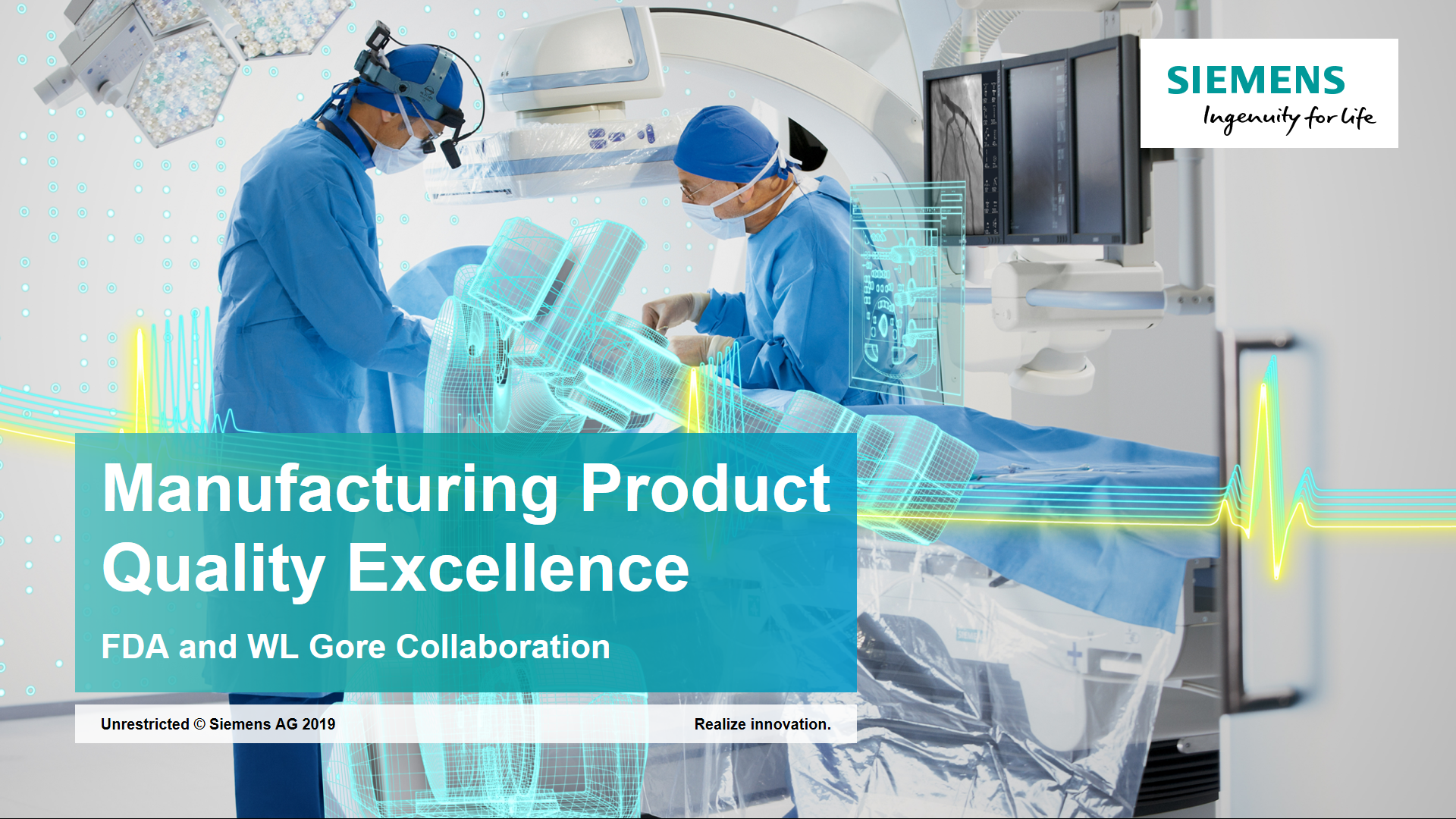
Medical Device and Diagnostic (MD&D) manufacturers have an opportunity to transform their relationship with the U.S. Food and Drug Administration (FDA), and in the process to improve their manufacturing performance and bottom line. The keys to this transformation? A new paradigm at the FDA, and the digitalization needed to make this paradigm work successfully.
For both the FDA and the MD&D industry, the core value driving collaborative efforts is an improved patient experience. This means that both the manufacturer and the regulator want innovations to reach patients and improve their quality of life as quickly as possible. Of course, no one wants a reduced time to market or higher level of productivity to be achieved at the expense of product quality; in fact, improved product quality is in the interest of patients, regulators and manufacturers alike. So what can be done to simultaneously improve time to market and product quality?
For its part, the FDA’s Center for Devices and Radiological Health (CDRH) has been finding ways to streamline regulatory processes as part of its paradigm shift from one focused on enforcing compliance to one that encourages operational excellence. The agency is moving away from inspect and control processes and is looking to drive connections within quality systems and organizations, enabling simplification and error-proofing. The FDA hopes to cultivate a culture of rapid learning and continuous improvement, both at the agency and throughout the MD&D ecosystem.
Practically speaking, the CDRH has begun making this paradigm shift through its two-year Voluntary Manufacturing and Product Quality pilot program, which wraps up in December 2019. Through this program, the agency adopted third-party maturity appraisal system that leverages the Capability Maturity Model Integration (CMMI) framework to assess a medical device organization’s ability to produce high-quality devices and increase patient safety. Results of this program are impressive:
- Manufacturers participating in the pilot program have received approval to implement changes in a review process that averages three days, compared to the average 24 days for a traditional review process.
- One change resulted in $286,000 additional cost savings.
- Another improvement change eliminated a manufacturing error that previously required visual inspection, and allowed 10 FTEs to be reallocated to higher value operations.
- One change increased production capacity at the manufacturer by 11%. The 21 extra production days resulted in 882 additional high-risk patients receiving products and treatment.
These results arise out of a transparent, data-driven regulatory model — one which relies on digitalization being implemented both at the agency and at MD&D facilities. Digital tools will enable regulators and manufacturers to work collaboratively to:
- Demonstrate design and development control through logically linked risk elements, design requirements and evidence
- Implement high traceability and granular revision control of those linkages
- Engage in active performance monitoring and responsiveness to issues
- Integrate closed-loop, real-world feedback
- Promote rapid learning cycles and continuous improvement in design
- Evolve from a reactive framework to a responsive and proactive one
Digitalization improves a manufacturer’s analytics and error-proofing and drives quality and responsiveness to issues, enabling a true total product lifecycle approach — all of which improves the effectiveness and efficiency of FDA reviews. For this reason, the FDA supports and encourages the use of automation, information technology, and data solutions throughout the product lifecycle in the design, manufacturing, service, and support of medical devices.
Learn more about collaborative efforts between the FDA and MD&D manufacturers, and how these efforts are simultaneously improving quality and time to market, in this on-demand webinar.