Looking at Operational Excellence as a Value Stream
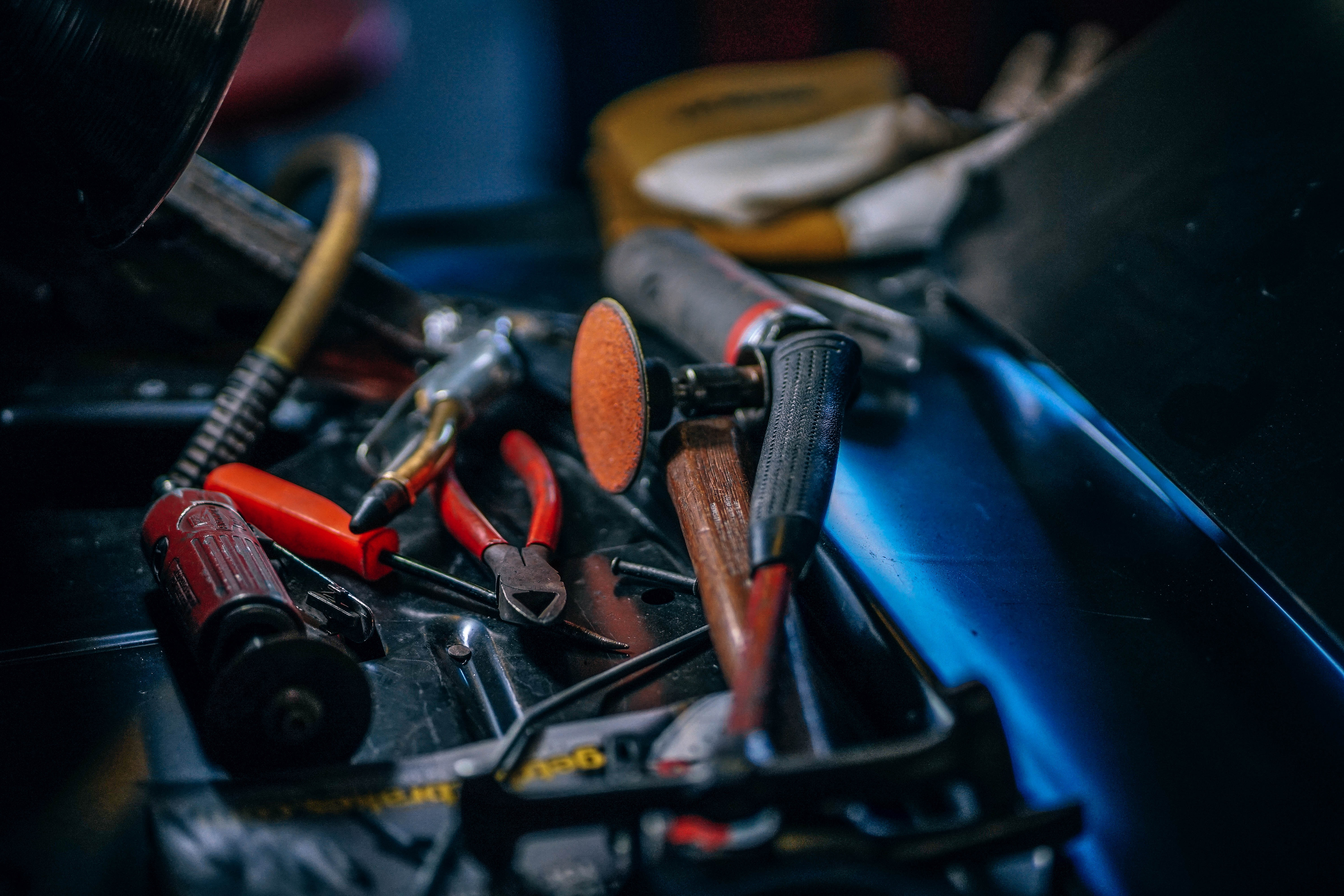
As we discussed in a previous blog, “From Point Solutions to Value Streams,” it’s time to look at the systems infrastructure of medical device manufacturers not as point solutions tackling particular areas of the product lifecycle, but rather as a connected value stream, supported with collaborative systems designed for closed-loop operations.
Some of the value streams that need to be considered include
-
- Design Excellence
-
- Reduced Time to Clearance
-
- Personalization
-
- Product Quality and Compliance Excellence
-
- Design & Make Anywhere
-
- Operational Excellence
In this blog, we take a deeper dive into the value stream of Operational Excellence.
First, what is Operational Excellence? Originally rooted in LEAN and Six Sigma principles, it has traditionally been a concept that relates, for manufacturing, to the continuous improvement in production efficiency. Key metrics, in that case, include cycle time, yield, throughput, and inventory turns. Much like LEAN, it has centered on plant floor operations. A more holistic, strategic view of operational excellence is by nature extending the value stream beyond the four walls of the plant, and into the ideation and consumption of the product. This concept of operational excellence can be thought of as the continuous improvement of the stream of value delivered to a customer. By nature, this concept extends the value stream beyond any single area of the product lifecycle, such as the shop floor.
Historically, the major system supporting the traditional approach of operational excellence has been the Manufacturing Execution System (MES), the heart of Manufacturing Operations Management (MOM). It has been relied on to digitalize manufacturing operations, enforcing efficient, compliant manufacturing processes and recording the production history of each product. The handoff to the MES occurs when a manufacturing order is delivered to the shop floor, either via the ERP system or the PLM system.
Information from the MES is used for regulatory and compliance functions, supplying the electronic Device History Record (eDHR) and electronic Batch Record (eBR). But the focus of the supporting systems has been a single discipline – ERP for Sales and Finance, PLM for product design, MES for production, Quality Management System (QMS) for quality, among others.
Now we take the more strategic approach of operational excellence as an end-to-end value stream, and something interesting happens to the supporting systems. They become collaborative and interconnected, anticipating what each other function will need to improve the value stream overall.
This is what is driving the approach of “closed-loop” manufacturing. MES is still at the heart of the infrastructure, orchestrating the execution of plans and designs, creating the physical reality of digital intentions. But the demands on that system become more profound as the center of an Operational Excellence Value Stream.
Let’s consider the characteristics of the connection of the MES with PLM. The connection becomes more than simply the handoff of a manufacturing order, which in the traditional approach would have been the transfer from one silo to the next. Now the connection becomes an efficient, accurate design transfer in support of new product introduction (NPI) for innovation, with many exchanges that impact overall efficiency, and ultimately time to market. The continuous stream of engineering orders completely transforms configuration and change management efficiency, and sustains engineering for smaller, incremental improvement. Feedback into design spans product lifecycles to drive manufacturability and quality.
MES and QMS become tightly coupled. Non-conformances trigger QMS work streams. Corrective actions are enforced in the MES, which verifies completion with the QMS. Prevention becomes a reality, with quality information flowing back into the PLM, change orders seamlessly executed in the MES, and effectiveness reported back to QMS.
Production Scheduling is collaborative with ERP and MES, optimizing day-to-day, hour-to-hour production at a level of detail beyond ERP. Feedback on production status from MES strengthens planning accuracy.
Product Data Analytics must support the concept of the Operational Excellence Value Stream, analyzing data across supply chain, manufacturing, and quality, including non-conformances and customer complaints. This big data intelligence looks across the value stream to identify trends and perform root cause analysis, now with a more comprehensive view of product performance.
We continue to see challenges in today’s medical device manufacturing enterprises with siloed functions, paper-based processes, huge caches of untapped data, quality as a compliance exercise. The systems infrastructure composed of disparate systems has contributed to siloes of excellence. Today’s systems are becoming more collaborative and connected, and fostering our ability to look at Operational Excellence as a Value Stream, an approach that promises huge advances in efficiency, quality, profitability, and innovation for the manufacturing enterprises that choose to adopt it.
To learn more about the Value Stream approach to Operational Excellence, and the results being achieved by leading manufacturers, download our materials.