End-to-End Quality in Automotive Manufacturing is Driving Business Forward
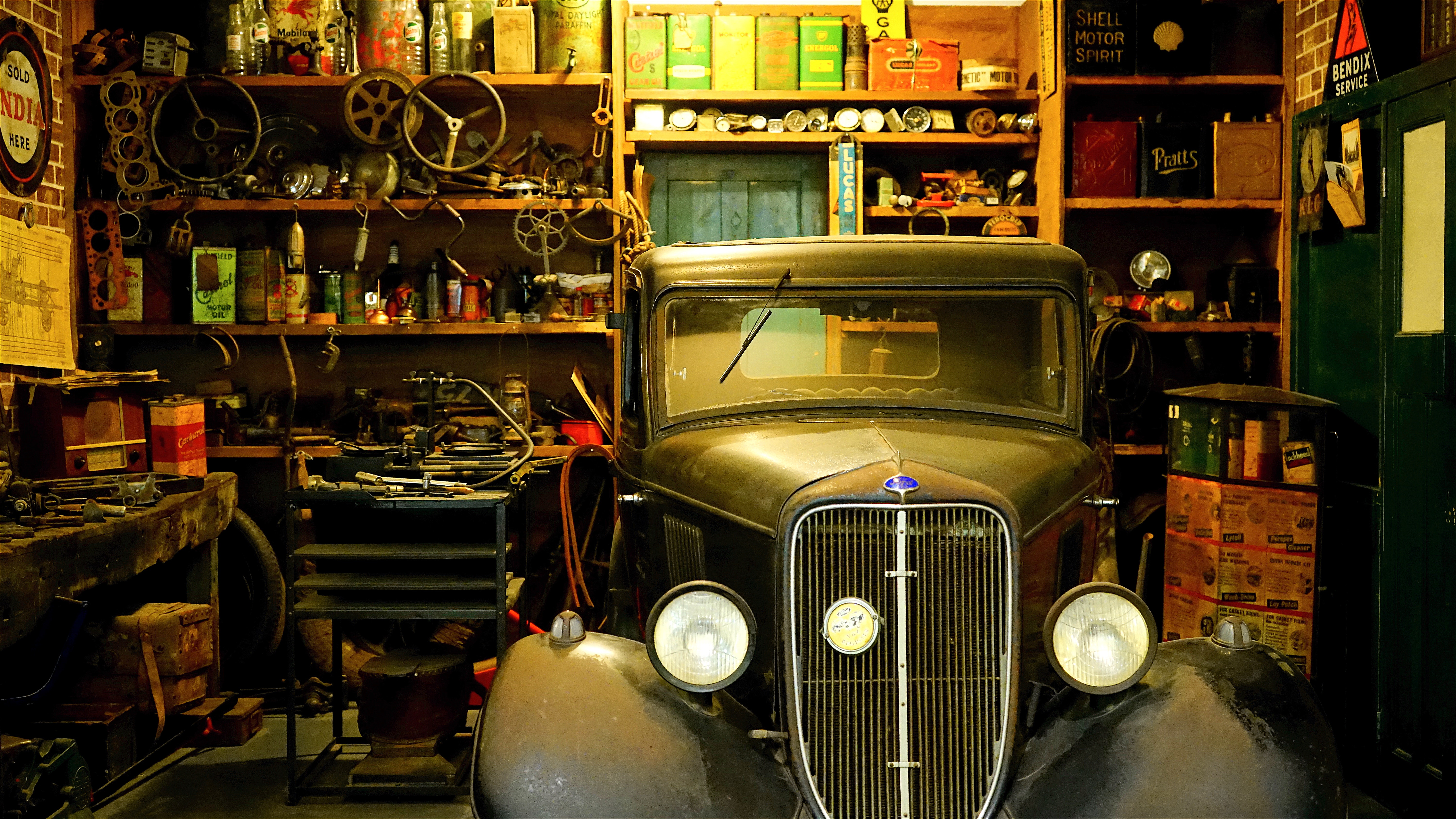
It’s a great time to be championing manufacturing quality. I’ve been working in the Automotive industry for over 15 years, and I’m excited to see the strides we are making in end-to-end quality. We are gaining access to new technologies, and connecting fundamental systems to leverage the intelligence these technologies offer. Let me tell you why you should be excited, too.
First, let’s define end-to-end quality in the context of Automotive tier suppliers. There are some trends that are worth noting that affect my definition. In recent years, there has been a shift in responsibility from OEMs to tier suppliers. Mass customization has required OEMs to push more of the engineering and configuration requirements of the end customer down to the tier suppliers. Tier suppliers are now not only executing the manufacturing of a product as required by the OEM, but they are also in charge of engineering the product.
That’s why we’re talking about end-to-end quality, which I define as the support of quality throughout the entire product lifecycle – from design (or ideation), to the execution of manufacturing of the product (realization), to performance in the field (utilization). End-to-end quality is a unified approach, what we call “closed-loop,” that captures data on the shop floor and in the field and feeds it back to design to create a lessons-learned environment.
This not only supports the small silos of quality like SPC and supplier assessment, but creates a holistic view from the first concept of the product, to managing the project of design requirements, planning and scheduling, engineering drawings and BOMs and BOPs, manufacturing BOMs, creation of the risk analyses (FMEA), and how everything gets executed by the operators to get that product made and shipped. Parts to be supplied, parts to be made in-house, parts to be assembled, and the product that needs to be shipped – all have to be executed by the operations. The inbound, in-process controls, outbound processes – data from deviation of tolerances, claims from customers, identification of supplier issues – all the data produced can be distilled into information that is used to modify and improve performance of the entire product quality cycle.
With this approach, we can expect an overall reduction in the cost of quality, from proactive intervention to prevent defects, to resource efficiencies gained from supplier quality information (e.g., reducing the inspection lot size based on high quality characteristics of a supplier), to reduction in scrap and rework – and ultimately from reduction of field failures, warrantees, and recalls.
The reality is that the approach is becoming a cost of doing business in the Automotive industry. Think about just a subset of what we have to manage:
-
- Projects
-
- FMEA objects
-
- Quality control plans
-
- Process flow charts
-
- Inspection plans
-
- Measurements
-
- Claims
-
- Supplier analysis
All of these domain functions can no longer be managed by siloed applications as they have in the past. I still see the attempt at integrating these domains through personal tools like Excel, private databases, Word, pdf files, even paper. This kind of approach is no longer manageable – the complexity is too great, and the competitive nature of time to market requires greater speed and agility. Any change in one of these domains will trigger a response in the others. This is simply not possible at the speed required today when these applications can’t talk to each other.
We have to consider that we are not only talking about the introduction of a new product to market, but the modification of an existing product. With mass customization, changes within the product lifecycle are increasing exponentially. Additional requirements are being created by the OEM around compliance, such as new in-process quality control checks to ensure process stability. New preventive quality requirements may arise from customer claims.
The entire product lifecycle is shortened with a holistic approach. Of course, the end product is also higher quality. Product innovation today must be accompanied by manufacturing system innovation as well. Our ability to support a holistic, end-to-end quality approach today is available, and the remarkable advancements being achieved with their use is returning huge payback for manufacturing leaders.
In the next part of this blog series, I’ll discuss in more depth some of the unique challenges I’m seeing in Automotive that are compelling more and more manufacturers to abandon their legacy, siloed applications, and adopt an end-to-end quality approach – and why they are getting excited about the results.
Comments
Leave a Reply
You must be logged in to post a comment.
Great Post ! Thanks Giulio.
I like the Quality Cycle that you describe, I mean:
FMEA Risk Analysis –> Definition of the Inspection Plan –> Quality Measurement Execution –> Statistical Analysis of executed Measureements –> Product Shipping –> Customer Claims –> Reaction to Claims including new version of FMEA –> Generation of new versions of Inspection Plans …. and so on and so forth….
And I also like the idea of positioning the respective subparts of such quality cycle inside the PLM MOM architectures. I mean “dismantling” the quality modules in the various repective subparts.
This allows to:
a) possibly expand the “PLM” planning / engineering part of such circle (FMEA, Inspection Plan, Customer Claims) to other PLM capabilities (e.g. Simulation, CAD, ..).
b) possibly expand the “MOM” execution part of such circle (Quality Measurement Execution, Data Collection from Machines, Historical Statistics, ..) to other MOM capabilities (e.g. Track&Trace, OEE and KPI calculations, …).
Waiting to read more from the Community!
Well writen – Thanks Giulio
Thk Oliver
Hope this series of articles might be beneficial for you all in order to better position our portfolio.
With best regards,
Giulio Folgarait
Siemens Industry Software
Digital Factory Division
MOM Business Enablement
Senior Director – MOM Industry Management Automotive
Via E. Melen, 83 Genova, Italy