What’s new in Opcenter X 2410
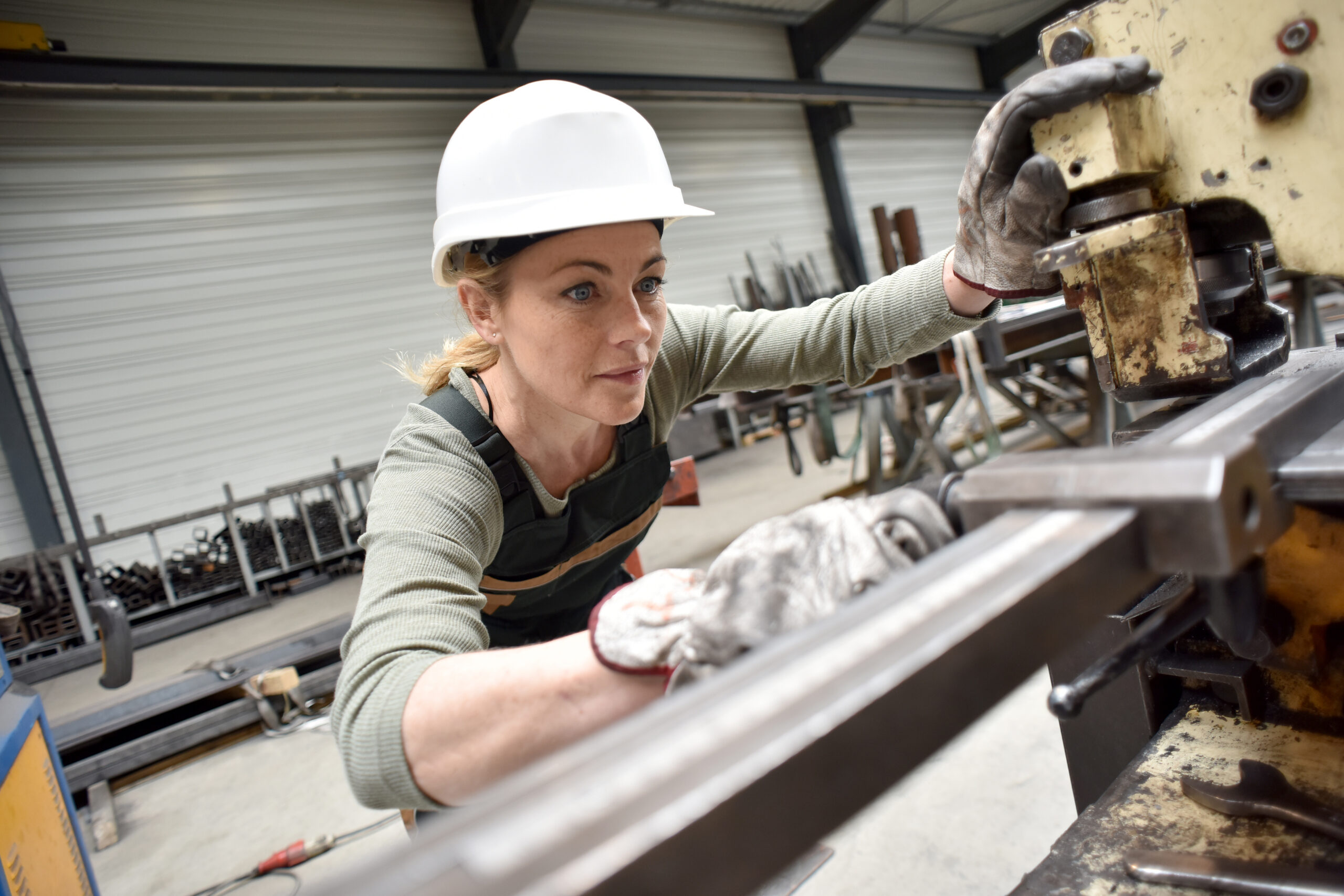
Boosting Operational Success: Empowering Operators with Essential Manufacturing Resources
Summary
Siemens Digital Industries Software is pioneering modular MOM, enabling more manufacturers to take a stepwise approach to digital transformation. Built with cloud technologies and offered as software as a service (SaaS), using Opcenter™ X software, which is part of the Siemens Xcelerator business platform of software hardware and services, lowers the time and cost barriers for SMBs, enabling you to realize rapid return-on-investment (ROI) with modules that connect and adapt as your enterprise matures.
With Siemens as your MOM solution partner, you can be sure Opcenter X is built on a rich and deep knowledge base and the extensive capabilities of a leading software company. We listen to and learn from our customers, then innovate and capture best practices for every digital task. Then we apply best practices to accelerate time-to-value of our software. With Siemens as your software partner, implementing modular MOM capabilities by using Opcenter X will bring about the manufacturing agility you need to thrive in your manufacturing space, both today and into the future.
Benefits
- By adding Manufacturing Resources like tools to your operations, user can enhance efficiency and productivity. These resources can be easily provided to operators during execution, ensuring that they have everything they need to excel in their tasks.
- Easy adding and access to manufacturing important documents and work instructions
- Configurable gantt chart for easier handling e.g. display range or filtering
- SPC evaluation considers visual inspections
- Effortless quality control integration: Seamlessly insert quality tasks and collect data without any disruptions
- Better shopfloor connectivity through OPC UA and HTTP
Features
- Document and resources management optimization
- Enhanced gantt interactivity
- User defined custom views for scheduling
- Many to many relationships support for scheduling
- Non-conformance management – Optimized support of defect collection cards
- SPC enhancements – Localization for number separator supported
- File connector
- OPC UA connector (with limitations)
- Http connector (Opcenter X call of APIs of external system)
Capabilities
Audit Trail
- Audit Trail: captures and records all relevant data and activities within the manufacturing process. It enables a review of who has changed what in the system, and when.
- Shopfloor Audit Trail: search for all the records related to the production execution. The transactions performed by tracked objects (e.g. the start of a work order operation) are automatically collected and available in the Shopfloor Audit Trail page.
- Modeling Audit Trail: search for all the records related to production engineering. The actions performed on modeling objects (e.g. creation of a new Material) are automatically collected and available in the Modeling Audit Trail page
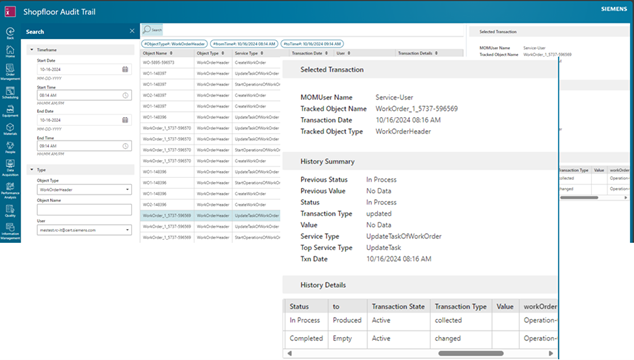
Resource management enhancements
Support the concept of mounting, assembling physical resources and de-assembly. This assembly will be managed as “one” equipment to support production.
- Ad-hoc assembly of resource via the resource administration page
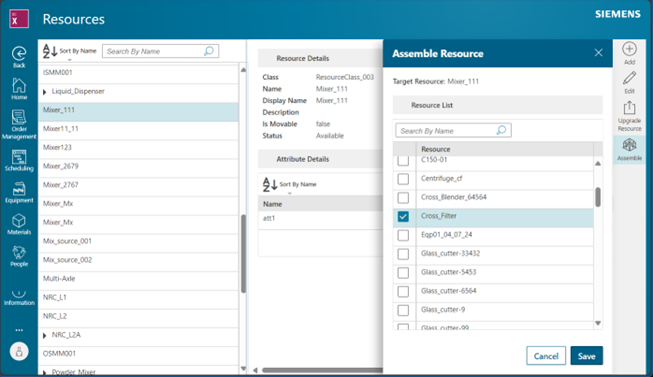
- Guide and control assembly via Operator Terminal
- Guide the operator in Operator Terminal to perform resource assembly.
- Operator identify and confirm the assembly resources on the work unit assigned to the operation.
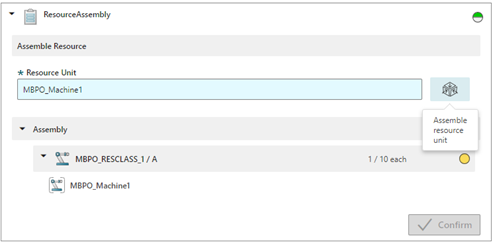
- Operator terminal enhancements
- Count down timer allows to monitor time left for operation execution

- Possibility to select a Work Unit when operation is started
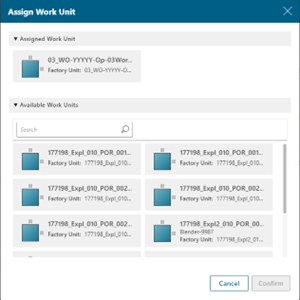
CNC part program management
- Define part programs and associate with compatible resources (work units and resource groups)
- Assign one or more part programs to process operations considering current equipment association
- Access the assigned part program during operation execution
- Send part program to the machine network folder utilizing capabilities of interoperability application
- Select and download assigned part program to local folder as a file
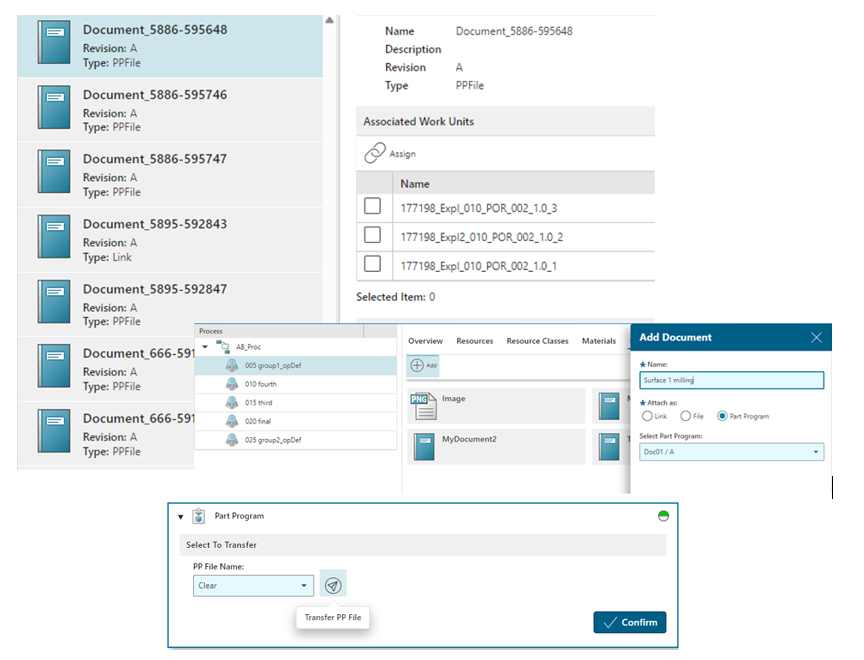
Activate task from external system events
- The definition of the event that will interact with the task is configured via the process designer.
- The event could come from external system via Interop App or any other Opcenter X application publishing NATS message. The information carried by the event will be stored as parameter of the operation and can be used for the other business logic tasks of the operation.

Intelligence
CSV Export
- Possibility to export the filtered data table as an csv export for importing in a secondary system for further creation of reports or data exploration.
Quality
- SPC
- Inspection order state
We support an Inspection Order state, that inspection orders can be closed and are not available in the SPC acquisition any more.
- Support acquisition of defects/defective parts for att./vis. characteristics
For attributive/visual Characteristics we can divide between “Number of defects” and “Number of defective Parts” and the user is aware of this. - Change RuleSet in Inspection Order Management
If the RuleSet is not provided by TeamCenter, it is possible to add/change it in Inspection Order Management. - Next inspection per characteristic or per inspection order
Some Customers want to have the inspection interval for all characteristics to be synchronized.
It is now possible to configure the required behavior. - Fast Non-Conformance generation
- When a process violation occurs, a panel appears in which all the relevant information for generating a non-conformance can be compiled. This is then fully generated in the background when the ‘Create Non-Conformance’ button is pressed. In this mode, you do not have to go through the NC workflow.
- Inspection order state
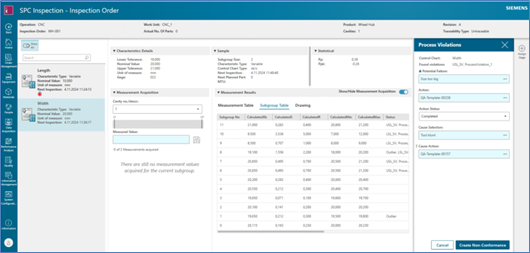
- IES-related Non-Conformances
- Creating multiple Non-Conformances out of IES, fully automated or using the wizard
- Grouping of IES-related Non-Conformances and show this in own Office Page tab
- Copy Cause from one related Non-Conformance to others
- Non-Conformance Management
- Add Closing Functionality to Shopfloor Page
- Improved Workorder Selection Dialog by adding additional parameter (Operation Description and Work Unit)
- Sorting of Non-Conformance Overview
- Save and reuse last sorting per user
- Introducing Rework Time “Actual Duration” of Actions into Non-Conformance
- In Wizard in add Action step
- In Shopfloor Page when working on an Action
- Pattern search: Correlations defined in Failure Catalog between different Failure Term Types are taken in consideration, if wanted
- Setting the focus in first editable field in multiple views and dialogs for a better workflow support
- Make the Failure Description tab of Failure Pattern visible in case of creating an Non-Conformance out of Data Acquisition
- Action Management
- Adopt Documents from Action Template to concrete Action
- Reuse existing Action Templates as linked Actions
- Display Linked Action navigation over Breadcrumbs
- Introducing Rework Time “Actual Duration” of Actions
- Possibility to add Actual Duration in Action during creation
- Edit Actual Duration in not Closed Actions
- Enter Actual Duration in Change Status Dialog of Action Management
Scheduling
The following updates are made within the Schedules feature:
- The shop floor status of an operation is displayed in the Orders table (column) and Gantt Chart (tooltip). This information is displayed after updating the default schedule. The Actual values of an operation are also updated. The information is updated as per changes done in the Data Acquisition app. If an operation has not started, then the shop floor status is displayed as ‘Pending‘ in the Scheduling app.

- Scheduled operations can be locked from the Gantt Chart and the Orders table after user confirmation.
However, unscheduled operations displayed in the Orders table cannot be locked.
The ‘Lock Operation’ option is displayed at three locations, by right-clicking a bar on the Gantt Chart, right-clicking an operation in the Orders table or selecting an operation in the Orders table, which displays the Lock Operation button on the command bar at the top of the table.
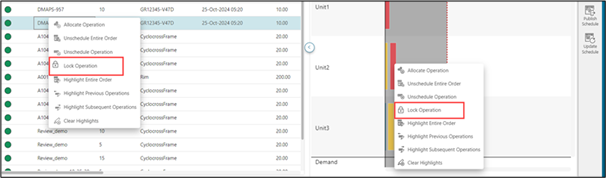
- Operations can be highlighted and unallocated from the Orders table as well. This can be done by either right-clicking an operation or selecting it and clicking a button from the command bar above the table.
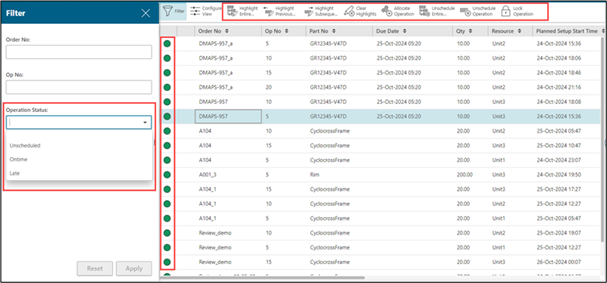
- Operations can be filtered in the Orders table based on their status also. The operation status is displayed as icons in the first column of the Orders table.
- Historical scheduled operations (displayed to the left of the terminator line on the Gantt Chart) cannot be unscheduled. If a user tries to unallocated such an operation, a message will be displayed informing them that the action cannot be performed.
The following updates are made within the Calendar Management feature:
- Custom resource calendar templates can be created, modified, deleted, and assigned/unassigned to multiple work units (resources).
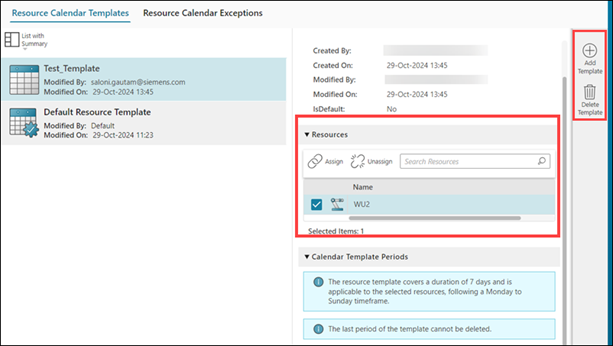
- Multiple resources can be assigned to an existing resource calendar exception record.
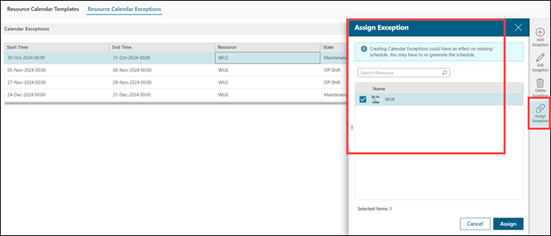
- New set of Administrator permissions can be applied to users to manage Calendar Exception records. These permissions allow managing of historical, ongoing, and future records, whereas non-administrator permissions allow managing only future records.
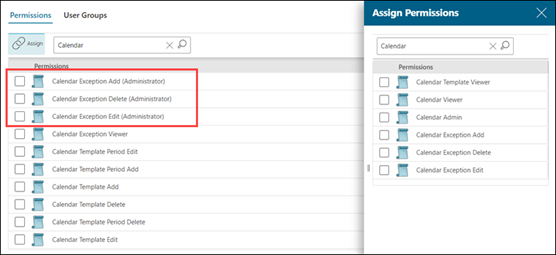
Configurator, Extendibility
Extendibility with the configurator is new for 2410. This means that Metadata models can now be extended with custom properties and deployed from the Configurator.
Configurable Objects
The Configurator has the ability to extend metadata models, which includes Adding, Editing and Deleting Fields of Configurable Objects.

UI Components
The Configurator supports adding SDC Dynamic UI component script files in JSON format. This facilitates dynamically rendering fields on the SDC pages without traditional UI page editing.
Deploying Changes
The Configurator facilitates releasing new versions of models and re-deploying Apps.

Interoperability
Usability Improvements
Indication of the Trace Records with Message Payload Details
- The “paper clip” icon quickly indicates that a trace record that includes the message payload contents
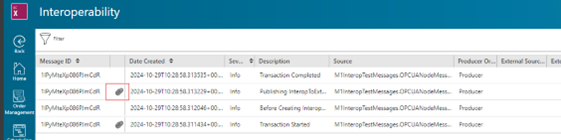
- The contents of the message payload can then easily be explored when opening the details tab
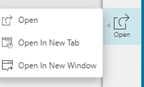
- The payload contents

Refresh Button and Sortable Columns
- The new refresh button can be used to show latest records in the table
- The columns in the table are now sortable
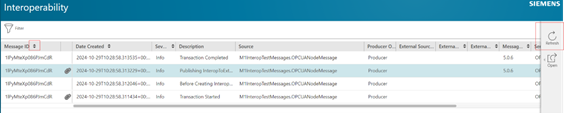
File Connector
Read Files
- The File Connecter can read files from local or network file systems and transfer the contents to the Opcenter X Interop App as shown below.
- The files are read sequentially by the File Connector based on the creation date of each file. When a file has been read and the contents successfully delivered to Opcenter X the file is either deleted or moved (depending in configuration).
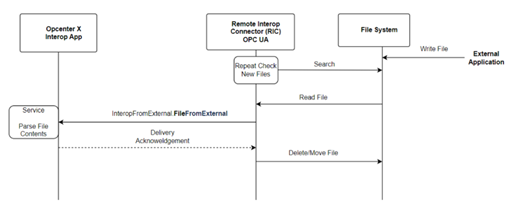
Network Folders
- The File Connector now supports the use of network-based file paths and mapped drives.
OPC UA Connector
Read Nodes
- The OPC UA Connector can read single values or an array of values from OPC UA Server Nodes as shown below.
Methods
- The OPC UA Connector can call methods exposed by an OPC UA Server as shown below.
If you are a decision-maker in an SMB in discrete industries and resonate with the challenges discussed, consider exploring Siemens’ new solution Opcenter X. It might just be the catalyst your company needs to leap into the future with confidence.
Try our product through our Trial page, or by requesting a demo.