What’s new in Opcenter Intra Plant Logistics 2410
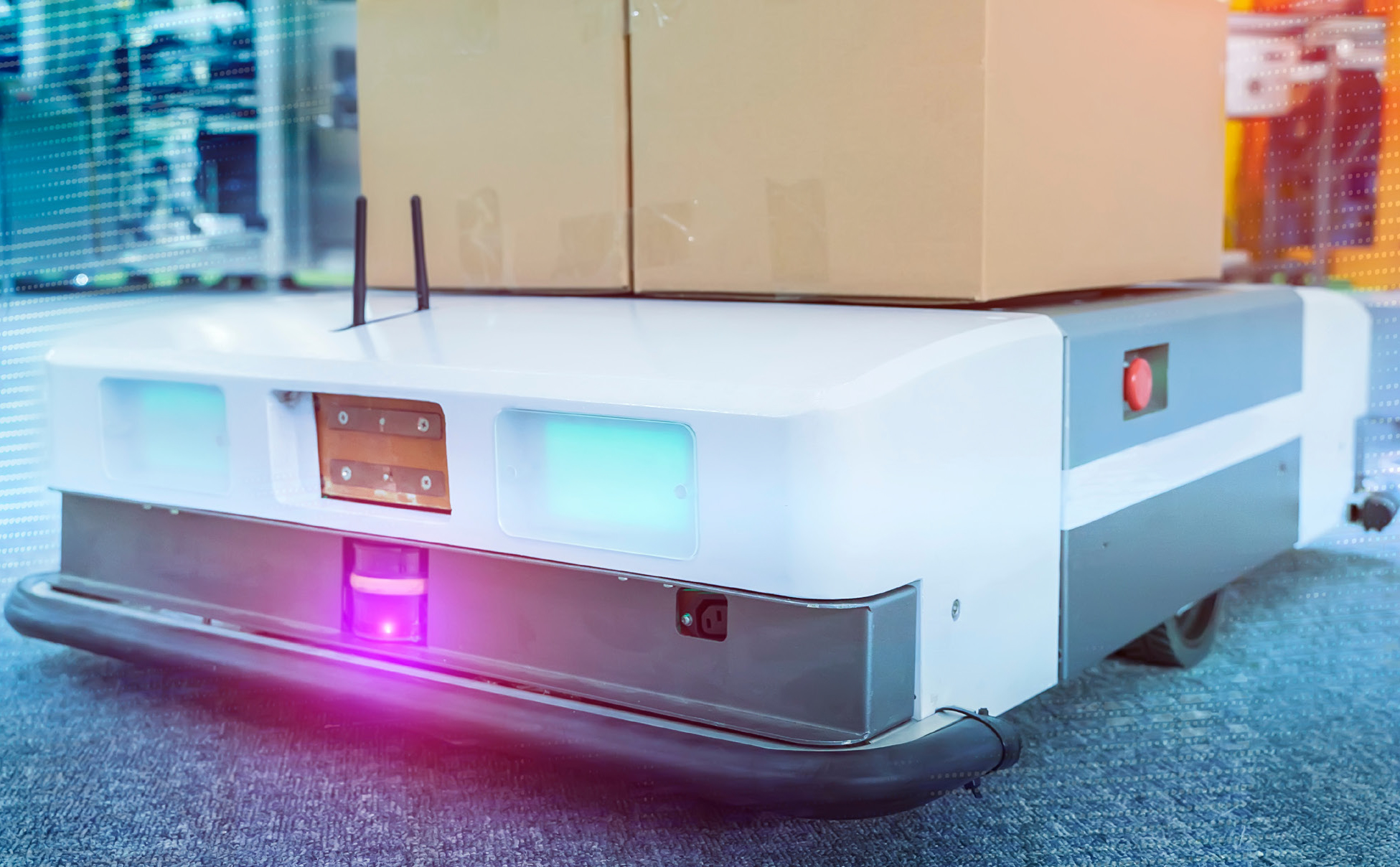
Streamlined transport and enhanced modeling for optimized intralogistics management
Managing logistics within factories and warehouses involves complex tasks like inventory control, storage optimization, and transport coordination. In the Opcenter IPL 2410 release, we introduce significant enhancements to streamline these operations, improve resource utilization, and enhance system security.
In Siemens Digital Industries Software’s ongoing efforts to enhance Opcenter™ Intra Plant Logistics (IPL) software, which is part of the Siemens Xcelerator business platform of software hardware and services, this release contains significant updates. This release features two new modeling applications for Warehouse and Manufacturing environments. The Layout Modeling tool enables users to create digital twins of facility layouts, including transport paths, nodes, and zones, providing a clear visualization of material flow. This tool helps optimize automated vehicle routes and improve transport efficiency. Complementing this, the Position Modeling tool allows users to define and manage individual storage positions, group them, and set specific attributes like capacity and restrictions. Together, these tools ensure efficient use of space and provide a precise digital map for improved planning and organization.
Benefits
- Enhanced facility modeling through digital twins for optimized layout and storage management.
- Streamlined transport execution with new tools for order, vehicle, and position management.
- Greater operational efficiency through vehicle reservation and task tracking features.
- Improved security and compliance with updated login management and data encryption standards.
- Simplified user experience with the retirement of redundant applications and refined documentation.
- Increased reliability and scalability with architectural enhancements like load balancing and database support.
Enhancements to the Transport Management suite include three new tools: Transport Order Management, Vehicle Reservation, and Position Occupancy. These tools provide users with the ability to monitor transport orders, allocate vehicles, and manage position occupancy in real time. Transport Order Management offers detailed status tracking for tasks, while Vehicle Reservation ensures vehicles are optimally assigned and managed. Position Occupancy allows operators to assess resource availability and track handling units by position, leading to streamlined workflows and reduced transport delays.
We’ve also introduced secure user access management within the IPL Portal, ensuring that only authorized personnel have access to specific applications, thereby reducing security risks and maintaining data integrity. The new login management system supports industry compliance standards and integrates with external user management systems like Keycloak and Active Directory.
The retirement of legacy applications has simplified the suite, enhancing deployment and management, while our updated documentation provides clearer, more concise user guidance. Architectural improvements, such as load balancing for the IPL API Gateway and support for Oracle databases, enhance the system’s scalability and reliability. Furthermore, an upgrade to .NET 8, along with encryption for Microsoft SQL Server and Oracle data, strengthens our overall security posture, aligning with the latest compliance standards.
In summary, Opcenter IPL 2410 brings enhanced modeling, optimized transport execution, improved user access control, and robust backend architecture. These updates underscore our commitment to providing a secure, efficient, and adaptable solution that meets the evolving demands of intralogistics management.
Capabilities
Warehouse and manufacturing layout modelling
New advanced layout modeling capabilities for warehouse and manufacturing environments.
IPL now enables users to create a digital twin of their physical spaces, capturing essential details and infrastructure within the facility.
Users can import their drawings of the plant, map out transport paths, storage zones, and key nodes in their layout.
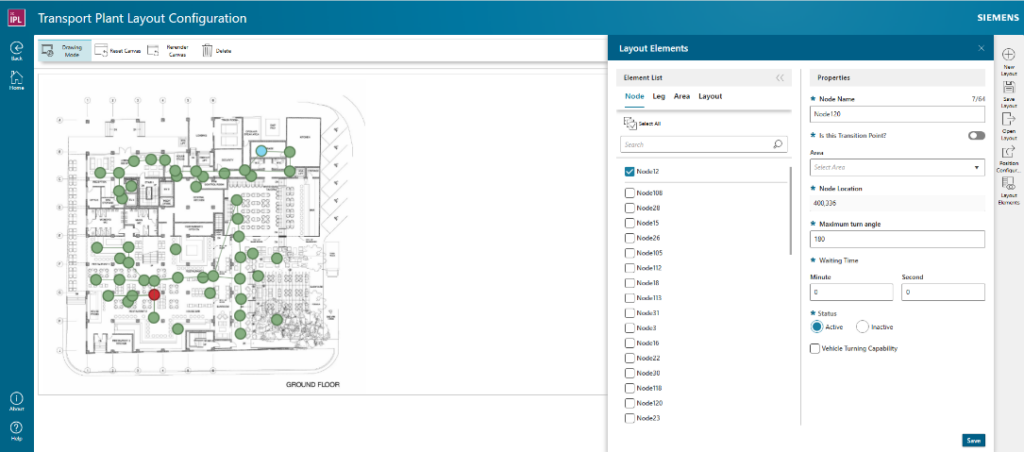
Introducing our new configuration tool, designed to revolutionize the management of storage positions within warehouse and manufacturing environments. This innovative functionality adds another layer of sophistication to your digital twin model, empowering you to define and manage every individual storage position with precision.
Create and customize detailed profiles for different types of storage positions, considering factors like weight capacity, size dimensions, and storage restrictions. Organize positions into logical groups (e.g., racks, rows) for streamlined management and tracking. Define specific attributes for each position, link them to corresponding types and nodes, and ensure accurate data across the warehouse.
By optimizing warehouse space and implementing a well-organized storage layout, you can reduce the need for frequent adjustments and improve overall efficiency. The detailed digital twin model provides a comprehensive overview of your facility, enabling data-driven analysis and optimization of storage strategies. Ultimately, this leads to cost savings and improved operational efficiency.
With this powerful tool, you can unlock the full potential of your warehouse or manufacturing facility, driving productivity and profitability.
Warehouse and manufacturing positions modelling
This new configuration tool empowers users to define and manage every individual storage position, enhancing the digital twin model of the facility. By enabling comprehensive management of:
- Position Types: Defining attributes like weight capacity, storage restrictions, and size dimensions.
- Position Groups: Organizing positions into groups (e.g., racks, rows) for efficient tracking and configuration.
- Individual Positions: Detailing specifications and linking them to relevant types and nodes for accurate data management.
This structured approach maximizes warehouse space utilization, ensuring each position meets specific requirements. It also supports optimized storage strategies, reducing the need for frequent adjustments.
As part of the digital twin concept, this level of modeling provides a precise digital map of the facility, facilitating analysis, layout adjustments, and the identification of underutilized areas. Ultimately, this tool contributes to cost savings and efficiency improvements by ensuring that every inch of warehouse space is utilized effectively.
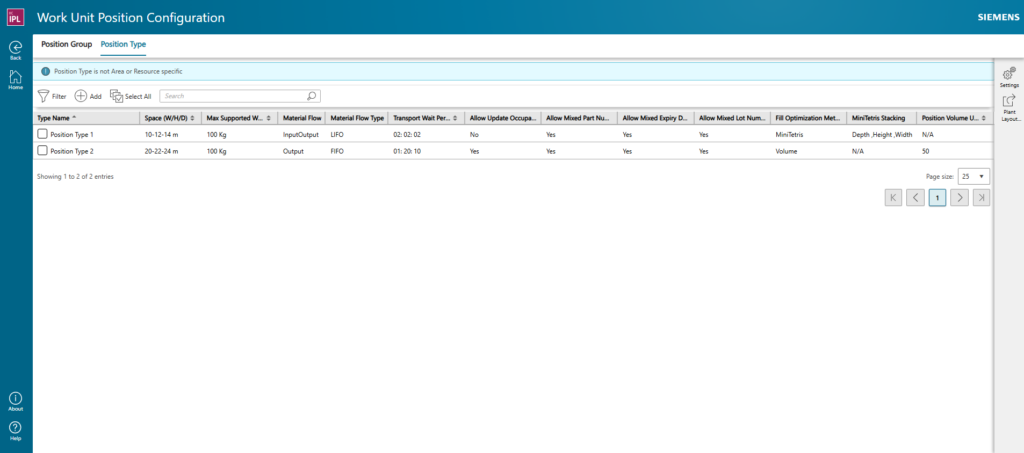
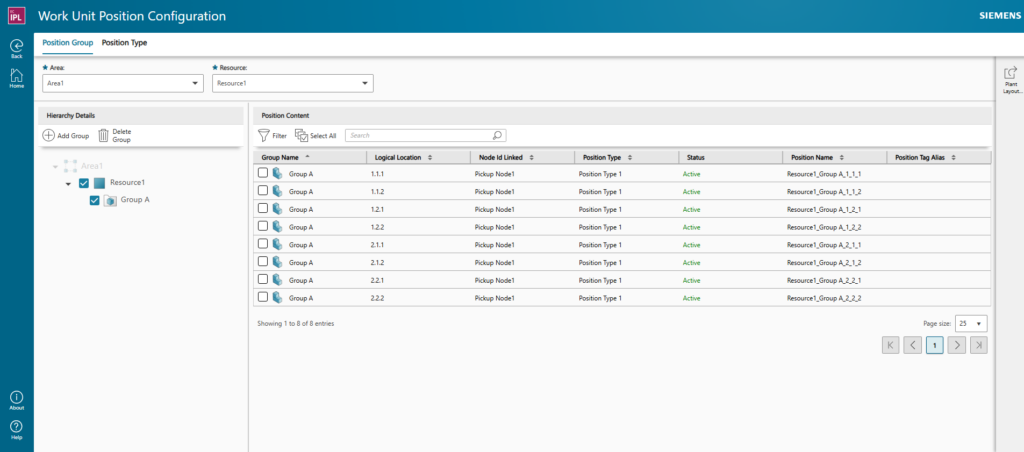
Streamlining transport operations with IPL transport order management
IPL’s Transport Order Management provides a comprehensive overview of transport orders, enabling users to easily monitor and manage the entire workflow. The user-friendly interface displays key information such as order status (New, In Process, Completed, Pending, Failed, Canceled), priority, and timestamps. This level of organization ensures timely action on high-priority orders and efficient task management.
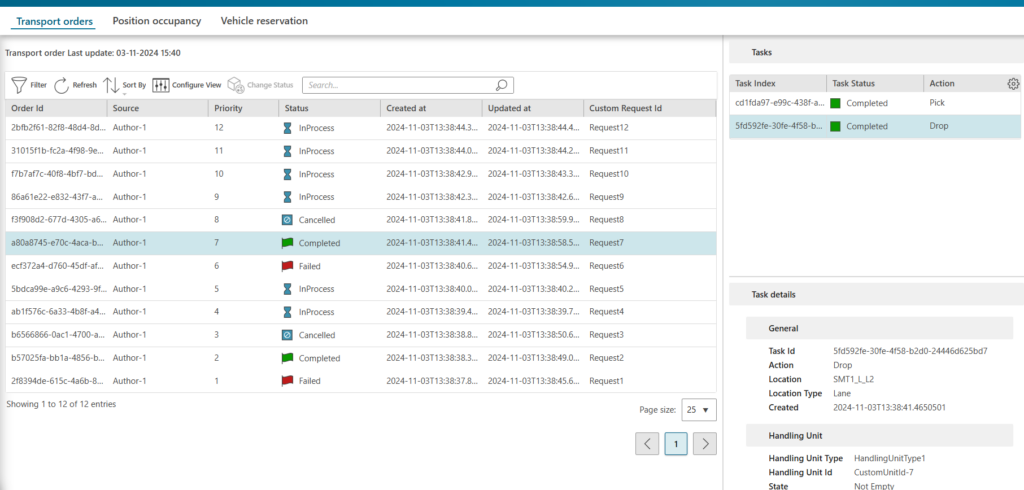
Zooming into individual transport tasks, users can track the progress of picking, dropping, and other relevant activities in real-time. Essential details like location, handling unit ID, and task action type are readily accessible, providing clarity and guidance to transport managers and operators.
The “Task Details” panel offers even more granular insights, including handling units, locations, and timing information. This level of detail empowers users to make informed decisions and take proactive measures to optimize transport operations.
By offering visibility at every step of the transport process, IPL’s Transport Order Management empowers users to:
- Improve delivery reliability: Ensure timely and accurate deliveries.
- Optimize vehicle utilization: Efficiently allocate resources and minimize idle time.
- Reduce operational costs: Streamline processes and eliminate unnecessary tasks.
With this powerful function, you can proactively manage and fine-tune your logistics operations, driving efficiency and customer satisfaction.
Enhanced position occupancy view and management
The Position Occupancy tab within IPL Transport Management provides a clear overview of current position statuses and resource availability. Transport Managers and operators can easily see which positions are active or inactive, along with their associated Work Unit status. This real-time visibility enables efficient resource allocation and ensures that positions are used effectively.
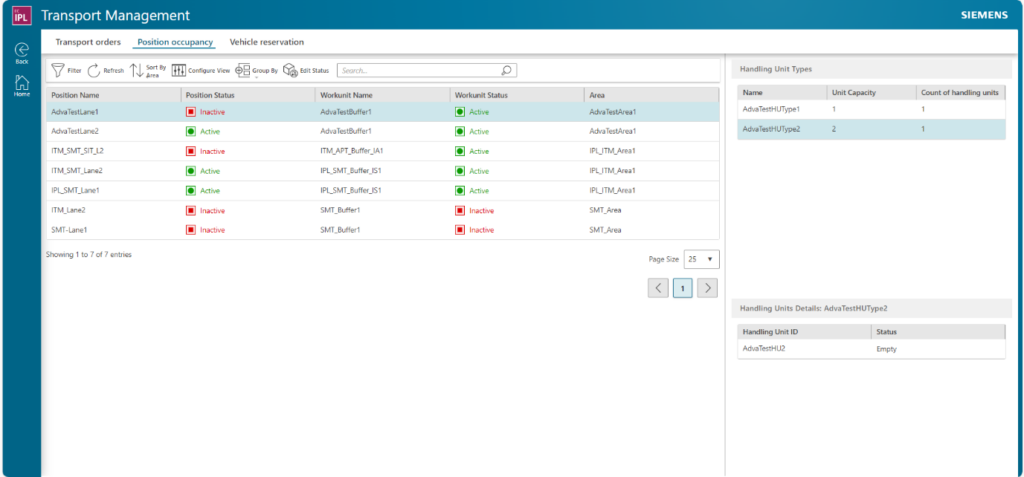
The Position Table displays:
- Position Name: Identifies specific storage or buffer locations.
- Position Status: Color-coded indicators (green for active, red for inactive) for quick assessment.
- Work Unit Name and Status: Shows the related position parent and its status, ensuring all resources are accounted for.
The Handling Unit view provides detailed information on Handling Unit Types, including:
- Unit Name, Capacity, and Count: Helps operators verify the availability of correct unit types and quantities.
- Individual Handling Unit IDs and Quantities: Provides granular information for precise transport operations.
By manually changing position or Work Unit status, users can block positions for various reasons, ensuring they are not used for picking or put-away activities. This feature promotes efficient resource utilization, reduces bottlenecks, and optimizes facility layout.
Vehicle reservation view and management
The Vehicle Reservation module within IPL Transport Management provides a clear overview of all vehicle requests and their statuses. This enables users to easily track:
- Reservation Details: Each reservation is uniquely identified, with information on creation date, status (Confirmed, Requested, Return Requested), and linked transport order.
- Vehicle Information: Vehicle ID, type (e.g., trolley, forklift), and fleet manager are displayed, ensuring clarity and accountability.
By providing a centralized view of vehicle reservations, logistics managers can:
- Optimize Resource Allocation: Efficiently assign vehicles to transport tasks, minimizing downtime and maximizing utilization.
- Proactive Management: Identify potential conflicts or delays and take corrective actions.
- Streamlined Operations: Reduce administrative overhead and improve overall efficiency.
The ability to release vehicles from assigned orders provides flexibility in managing dynamic situations, such as equipment failures or unexpected changes in demand and provides a streamlined approach to fleet management.
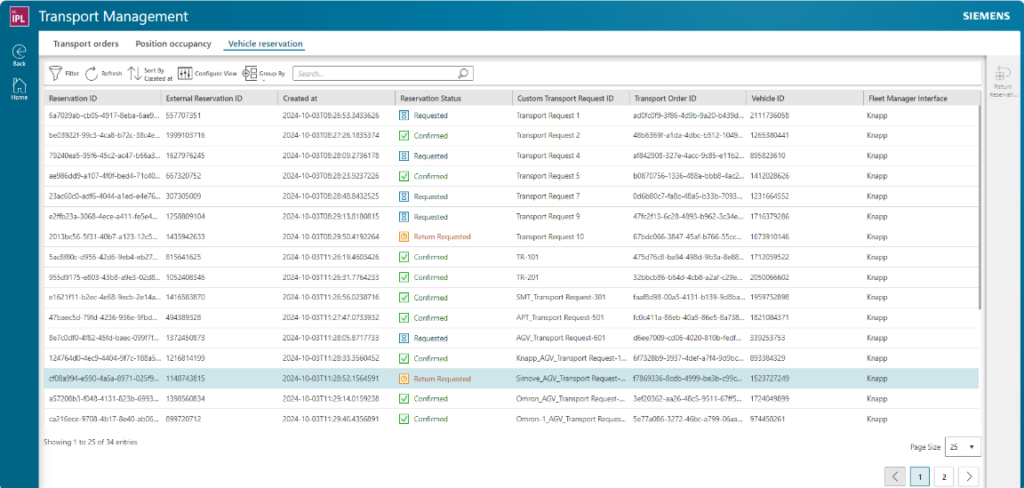
IPL portal: Enhanced user login management for enhanced security
The IPL Portal’s new user login management feature ensures that only authorized personnel can access the system, safeguarding sensitive data and maintaining security.
The user-friendly login screen guides users through a secure authentication process, while the profile panel allows for personalized settings and secure logout. Opcenter IPL supports external user privilege management, seamlessly integrating with platforms like Keycloak or Active Directory.
By adhering to industry security standards, the IPL Portal protects against unauthorized access, reduces the risk of security breaches, and maintains data integrity. This robust login management system aligns with regulatory requirements and internal security policies, providing peace of mind for organizations.
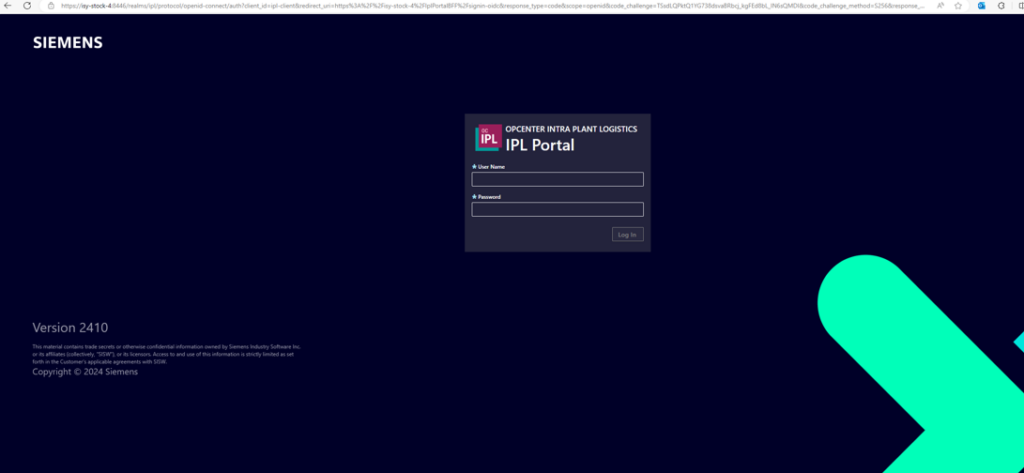
Improved security
We are committed to providing a secure and reliable intralogistics solution. As digital threats evolve, we continue to strengthen our security measures to meet the latest IT standards.
Key security enhancements:
- Modernized Technology Stack: We’ve upgraded the IPL development stack to .NET 8, ensuring compatibility with the latest security practices.
- Data Encryption: Building on our previous enhancement of encrypting data at rest for Microsoft SQL Server, we’ve now extended this protection to Oracle databases.
- Robust Security Architecture: Our system is designed to align with industry security standards, reducing the risk of data breaches and cyberattacks.
By implementing these security measures, we safeguard your sensitive data and ensure the continuity of your intralogistics operations.
Application retirement & Documentation improvements
We are consolidating and simplifying the application landscape within the IPL suite by retiring certain applications.
This effort aims to streamline our toolset, making deployment and ongoing management easier for our users.
Application | Retirement Reason |
Kitting Optimization | End of life |
Machine Waste Reporter Service | End of life |
Line Status Selector | End of life |
Enhanced platform and product features
We’re continually working to refine the platform and deliver a seamless user experience. Key architectural improvements include:
- Windows Authentication Support: Expanded database connectivity options to include Windows authentication.
- Oracle Database Support: Enhanced compatibility with Oracle databases through the IPL MES Gateway.
- Load Balancing: Improved system performance and reliability by enabling load balancing for the IPL API Gateway.
On the product side, we’ve enhanced the Commissioning Client to enforce the use of suggested containers for picklist entries, streamlining workflows and reducing errors.
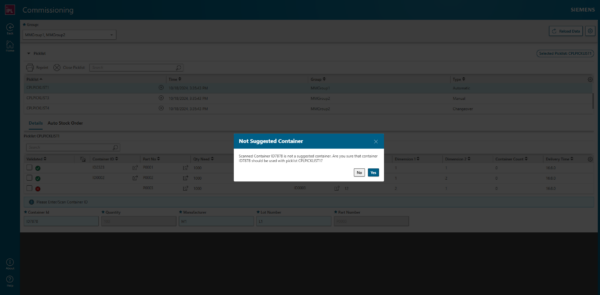
These enhancements work together to create a more robust and user-friendly experience, minimizing disruptions and maximizing efficiency.
Learn more about Opcenter IPL
Discover the power of Opcenter Intraplant Logistics to optimize your material flow from warehouse to factory floor. With real-time inventory management, smart JIT material replenishment, and special material management, you can increase line performance, maintain inventory accuracy, and ensure smooth material flow. Learn more about how this solution can revolutionize your intralogistics capabilities.
Learn more about supply chain management and logistics
A successful supply chain is not only relevant for intralogistics – Siemens has also solutions to support you with your intelligent and digital supply chain management:
- Siemens Digital Logistics
- Supply Chain Suite – PLANNING AND SIMULATION
- AX4 – COLLABORATION AND EXECUTION
- Supply chain consulting – Empowering excellence in logistics