NX CAM 9: Providing powerful CAM for prismatic parts machining
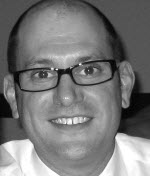
NX TM CAM 9 software (available now) delivers many new capabilities and enhancements that can improve computer numerical control (CNC) programming and machining productivity for wide range of industry applications. In this introduction to NX CAM 9, I’ll look at the new and upgraded CAM capabilities for prismatic part machining.
Prismatic-shaped parts are often machined for use in the machinery, automotive, and aerospace industries. 2.5 axis milling and drilling operations are commonly used to machine the prismatic shapes (planar and perpendicular faces) and simple features positioned at points (holes, threads, etc.) For cylindrical-shaped parts, turning operations are utilized.
While prismatic part geometry is simple, these parts tend to have large quantities of faces and features which require the ability to quickly program accurate and error-free tool paths. For higher volume orders, prismatic parts can be manufactured on setups that mount multiple parts, for example a tombstone setup. These setups usually have extensive clamping and fixturing to consider.
Faster turn-around for high volume jobs
Significant productivity benefits can result from reusing programming work, especially for setups with multiple identical or even similar parts. High-volume machining jobs can be delivered more efficiently by putting you right in the context of the production machining setup. Integrated computer-aided design (CAD) with assembly modeling tools in the CAM system give programmers the ability to position fixtures and work pieces onto a tombstone or other type of fixture.
Watch a video (10 minutes) on how to program setups with multiple parts in NX CAM.
The new multiple-part programming capability assists you with reusing complete machining sequences. Machining sequences can be copied from the parent workpiece and distributed to other parts in the setup. The tool paths are kept associative, so changes are kept up-to-date on the dependent work pieces. Complete jobs with multiple similar or identical parts can be programmed in almost the same time it takes to program a single part.
For a setup with six identical parts, our studies conservatively estimate a 4X productivity improvement in programming time. Tweaking of reused machining sequences due to accessibility and clearance issues (easily visible in the context of the complete setup) is done on an as-needed basis. (Hands-on demonstration: Faster CNC programming for setups with multiple parts).
A new way to program holes
Drilling and hole-making is often a major part of 2.5 axis machining jobs. In order to help save programming time and avoid mistakes, like accidentally missing a hole, NX CAM 9 provides a new level of programming automation for holes based on feature recognition.
Hands-on demonstraton: Learn how to use feature recognition for more efficient hole drilling
With NX CAM 9, the complete process for finding holes is automated, from recognition to filtering and grouping by dimensions and accessibility. Simply select a group of holes and drill. No holes remain uncut, and holes sharing the same attributes values are cut together. You can also save machining time by having NX CAM optimize the drill sequence and calculate efficient traverses to minimize lifts while accounting for all part and fixture geometry.
Whether you’re working with imported part geometry or a part with features, holes are automatically recognized and organized into feature groups. You decide how to machine them. You can manually specify the process, i.e. spot drill, drill, tap, or use other canned cycle methods; or, NX CAM can automatically apply your predefined machining sequence (requires a Feature Based Machining license). NX CAM supports a wide variety of drilling cycles across most industry machine tool controls.
Enhanced controls for turning
Several turning upgrades provide more control for typical workflows with NX CAM 9. A new part-off operation has been added with options for cleaning walls, depth control, pre-plunging and chamfering. For certain tapered threads, obstructions can be easily avoided with new parameters for controlling infeed and angle when engaging, as well as local return moves for roughing and finishing. The new centerline drilling depth control simplifies the depth specification for full diameter drilling and new non-cutting move capabilities help to avoid collisions (Hands-on demonstration: Enhanced centerline drilling and collision avoidance).
On-machine probing is useful for automating setups and maintaining process control. It can be used to perform pre-machining alignment checks and to measure tools to determine offsets. With a bit of creative programming logic, it can also be used to automatically adjust NC code based on measurements of the workpiece. For example, a precision turning job can use on-machine probing measurements to determine whether or not to perform an additional spring pass.
With NX CAM 9, on-machine probing operations have been added to turning setups. Multi-point probe types are supported. The new sub-operations provide several turning probe motions and support for simultaneous tracking of multiple probe points. With NX CAM 9, on-machine probing for measuring cutting tools has also been added.
New controls for cutting grooves with a T-slot cutter
New groove cutting operations in NX CAM 9 provide more control for slot milling. Cutting side grooves is simplified with a new T-cutter groove milling operation. The new operation gives controls to efficiently cut grooves by using various cut level sequencing, step-over, and cut order options. With a single programming step, the T-cutter can be directed to rough the center of the groove and finish both top and bottom using the T-cutter’s separate top and bottom contact points. Predefined T-cutter tracking points have been added to the tool definition for programming convenience.
I’ll also discuss these capabilities and others in the upcoming months, so stay tuned… Be sure to watch for announcements about upcoming Tech Tip webinars, videos, hands-on demonstrations, and more.
Next up…NX CAM 9: Complex parts machining.
LIVE Tech Tip Webinars!
Watch NX experts demonstrate the latest capabilities in NX CAM 9. Stay online for Q&A. REGISTER NOW! (attendance is free)
Are you interested in receiving emails whenever we publish new posts to this blog?
(Frequency: Semiweekly) Click here to learn how to subscribe.
About the Author
Aaron Frankel is a member of the marketing team at Siemens PLM Software and focuses on part manufacturing solutions. He has been in the PLM industry for over 15 years and enjoys helping companies apply innovative technology solutions to design and manufacturing challenges. Aaron resides in Southern California with his family. |