NX CAM 9: Providing industrial-strength CAM for complex part machining
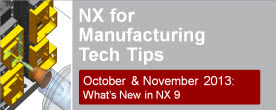
NXTM CAM 9 software (available now) delivers industrial-strength CAM for a wide range of industries. If you’re a manufacturer looking for the next level of control and faster computer numerical control (CNC) programming, then this release deserves a closer look.
In this introduction to NX CAM 9, I’ll look at complex part machining, particularly 5-axis milling capabilities that can help you to avoid reach problems for deep cores and the machining of turbines and blisks.
Cut faster, improve tool life and surface finish with shorter tools
It is always a good idea to use the shortest tool possible. Longer tools bend (and break!) more easily, and so suffer more chatter and vibration problems. Both speed and quality are impacted as feed rates are reduced and vibration shows up on the finished surfaces. Increasingly, die and mold shops are using 5 axis machines to avoid the need for long tool reaches in large, deep cavities. By tilting the tool away from adjacent walls, a short tool can reach beyond the depth where it would otherwise encounter holder interference – sometimes much deeper!
Figure 1: 3-axis tool paths can be adapted to include 5-axis tilting in order to reach deeper into cavities while avoiding holder interference. (Video: 3 to 5 Axis Toolpath Conversion – originally introduced in NX 8.5).
For parts with deep cavities and small vertical corners, our field tests indicate that 5-axis machines can improve machining productivity by up to 30 percent. The tilt tool axis function helps CNC programmers to take advantage of the efficiencies of 5-axis machining without the challenges of traditional 5-axis programming. The programmer creates 3-axis tool paths and then tilt tool axis looks for potential collisions. When a potential collision is anticipated, the tool axis is gradually tilted away from the collision area, resulting in a 5-axis tool path that takes advantage of the short tool.
Tilt tool axis was originally made available in NX 8.5 for only finishing operations. Support for roughing, undercut, and additional user control options have been added in NX CAM 9. (Hands-on demonstration: Precisely control tool tilt to avoid collisions).
Easily program complex turbines, impellers, and blisks
Turbomachinery components such as turbines, impellers, and blisks are challenging to manufacture. They are expensive to scrap, and hard to repair when programming mistakes are made. Moreover, their complex shape create reach and access obstacles. This is particularly true for radial impellers. If the blades are thin, they have additional sensitivities to cutting vibrations.
Figure 2: Blade roughing can be significantly more productive with bull nose tools.
NX CAM provides special operations that machine these components accurately and safely, with a minimum of programming inputs. In NX CAM 9, these turbomachinery milling operations are further enhanced to provide more process options, cutting even the most challenging of these components quickly and effectively. (Video: NX Turbomachinery Milling – originally introduced in NX 7.5).
Blade roughing now supports tools with non-ball nosed profiles. Using flat or bull-nosed tools for roughing improves the cutting action and may require fewer passes, significantly boosting efficiency over ball nosed tools.
Blade finishing is often done using many passes with the tool nose. But sometimes the blade surface is such that it can be cut with the side of the tool – mathematically called a, “Developable surface.” NX CAM 9 now provides an option to swarf cut (cut with the side of the tool) blades with this shape, resulting in the smoothest possible surface.
Very thin blades require special care during machining in order to avoid excessive vibration that can damage them. NX CAM 9 minimizes machining vibrations by stepping down thin blades in increments – roughing a shallow depth and then finishing to that depth, before too much of the blade protrudes from the rough stock. This incremental roughing and finishing continues until the entire blade has been finished. Programming this type of sequence in NX CAM 9 is accomplished by matching the finish region to the roughing region. This takes just a few more clicks than programming a single rough operation.
4-Axis Cylindrical Floor Finishing
Figure 3: The new 4-axis cylindrical milling operation avoids collisions by adjusting the lead / lag angle away from walls with undercut conditions.
A new specialized operation, 4-axis cylindrical milling, simplifies finishing of cylindrical floors.The new operation includes cylindrical floor and radial wall selections, and allows you to set a desired lead angle and then automatically adjusts it as needed to cut the entire floor including undercuts. Optimized sequencing and smart step-overs keep the tool engaged by minimizing lifts and traverses.
About the Author
Derek has been focused on PLM CAM software, in one way or another, since 1992, which sounds like a very long time. He’s written posts, done implementation and training, served as a product manager, and as a marketer. It has all been fun – he’s met a lot of interesting people and seen a lot of interesting machine shops. |
LIVE Tech Tip Webinars!
Watch NX experts demonstrate the latest capabilities in NX CAM 9. Stay online for Q&A. REGISTER NOW! (attendance is free)
Are you interested in receiving emails whenever we publish new posts to this blog?
(Frequency: Semiweekly) Click here to learn how to subscribe.