Next-gen machining with NX CAM: accelerating production for high-performing parts [VIDEO]
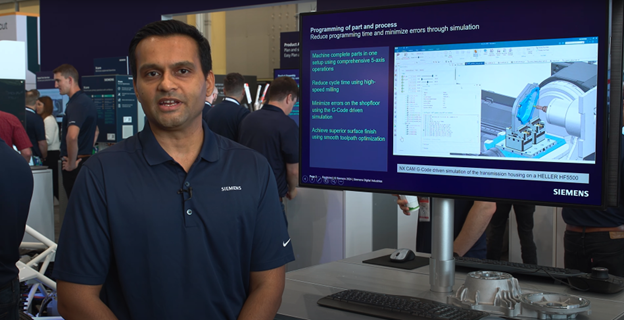
Siemens showcased the power of digital manufacturing with a fully integrated demonstration. A key highlight was the role of how NX X Manufacturing software like NX CAM helps optimize the CNC programming and machining processes. Using AI-driven automation and cloud-based solutions, we demonstrated how manufacturers can enhance efficiency, reduce errors, and achieve high precision in production.
Measuring and simulation powered by NX CAM
The advanced capabilities within NX CAM, including G-code simulation and Run MyVirtual Machine, provided an accurate digital twin of machining operations. This ensured seamless transitions from programming to execution, reducing setup times and improving quality control.
One of the standout benefits of this approach is the ability to simulate and validate machining operations before physical execution, minimizing costly errors and downtime. By leveraging AI and automation, manufacturers can optimize toolpaths, improve surface finishes, and extend tool life — all while maintaining flexibility in production workflows.
Additionally, cloud-based collaboration allows teams to access and refine CNC programs from anywhere, ensuring that best practices are shared across global operations. The combination of these technologies empowers manufacturers to adapt to changing demands, increase throughput, and drive innovation in their production processes.
Automate programming and accelerating machining for next-gen components
Building on this, the next stage of the demonstration highlighted how NX CAM and the digital twin of the Heller machine streamline programming and process validation. At our booth, we showcased the manufacturing of next-generation components, including the transfer case, installed on the E-Rod electric vehicle. With advanced machining strategies such as adaptive roughing, cavity milling, and mid-pass facing, NX CAM enabled highly efficient and precise part manufacturing. This seamless integration of CAD modeling, generative design, additive manufacturing, CAM programming, CNC machining, and quality inspection underscored the power of an end-to-end digital workflow.
By integrating AI, simulation, and automation, Siemens is redefining digital manufacturing — helping companies to accelerate production, lower costs, and maintain superior quality. In the next stage, we move to part quality inspection using CMM inspection programming to verify accuracy and improve workpiece quality, while reinforcing the value of a connected, data-driven manufacturing environment. Stay tuned!