Manufacturing trends for hybrid skills and machining
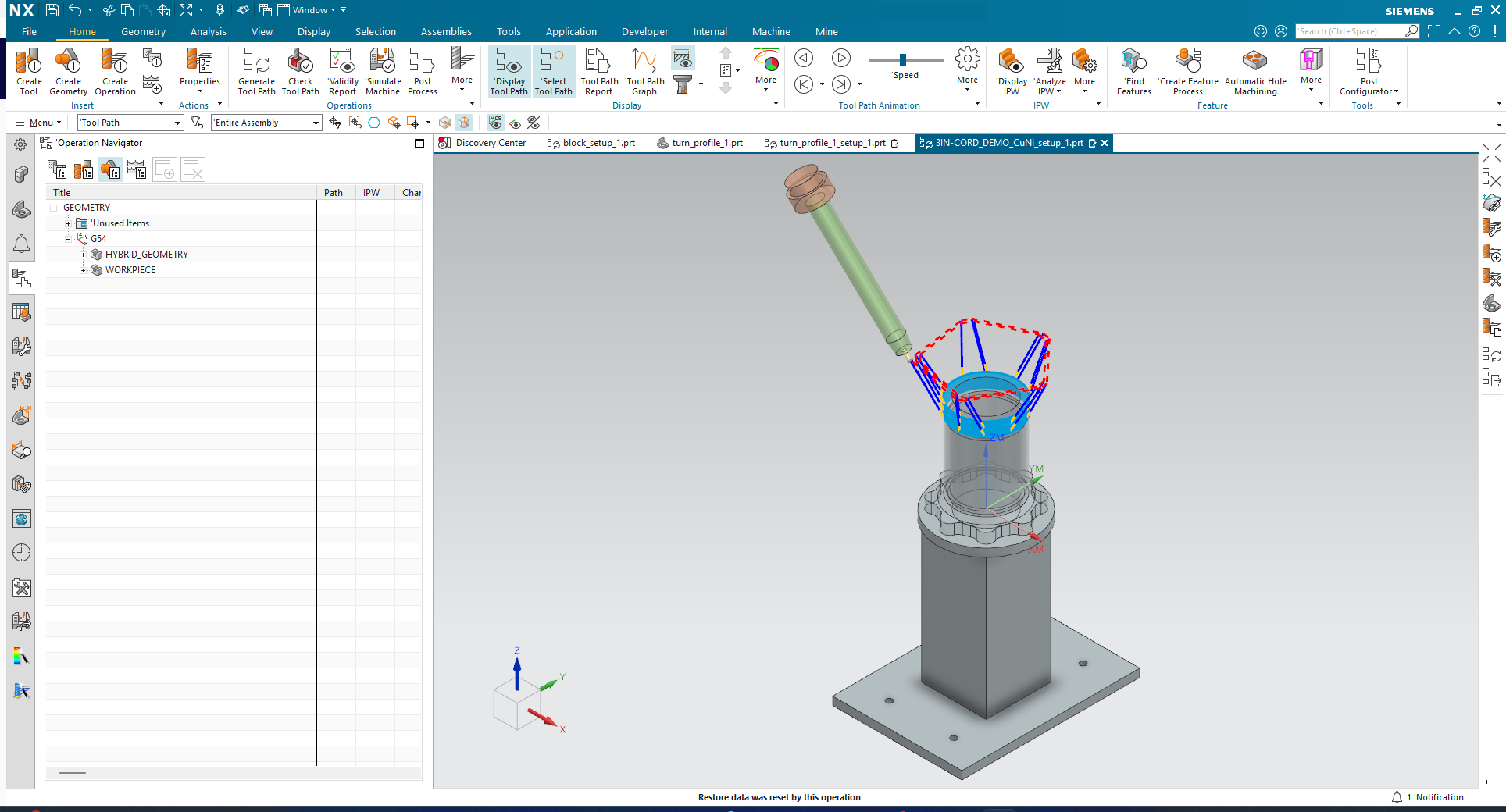
This blog series explores key lessons from my visit to Big Metal Additive (BMA), an advanced manufacturing shop in Denver, Colorado, that integrates Siemens NX for Manufacturing software and hardware for hybrid machining. Hybrid machining — combining additive and subtractive processes —enables the production of parts once thought impossible. However, mastering this workflow requires a hybrid skill set, where employees operate diverse machinery and software. In this blog, I explore the unique skillsets and common machining trends in the industry.
For example. I recently had a visit with a major industrial additive manufacturing customer, Big Metal Additive (BMA) who uses Siemens Additive Manufacturing software. BMA is an additive manufacturing machine shop in Denver, Colorado, specializing in metal 3D printing and integrating welders with 5-axis CNC mills to explore new frontiers in manufacturing. Their work is often pushing new boundaries, serving both private companies and government agencies to replace traditional processes, build intricate geometries and conduct material testing.
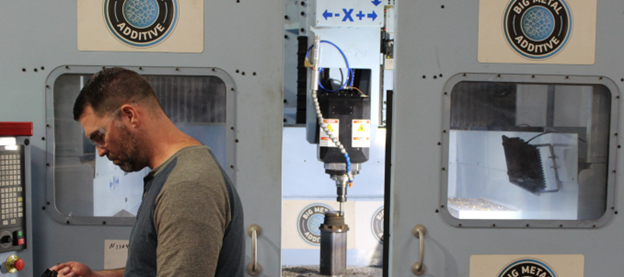
The Growing Need for Hybrid Skills
A few months prior to visting BMA, I had spoken at a technical education conference, urging schools to adapt to modern manufacturing training. I reinforced that companies should break down silos and train employees across multiple disciplines — machining, welding, and toolmaking — especially as technologies like additive manufacturing, robotics, and automation become more prevalent.
BMA exemplifies this shift. It isn’t just a machine shop—it’s a hybrid machining powerhouse that embraces cross-functional expertise.
The Power of Hybrid Machining
Hybrid machining integrates additive and subtractive processes, allowing manufacturers to reinvent production workflows. While 3D printing has advanced significantly, it still can’t replace all traditional methods. Combining it with milling or turning enhances efficiency and expands design possibilities.
From a workforce perspective, this requires more than just welders, machinists, and programmers — it demands multi-skilled employees who can adapt to different tools and equipment. The future belongs to versatile engineers who can operate across domains.
CNC Meets Robotics
BMA’s shop floor is a fusion of technology — with both 5-axis CNC machines and articulated robots capable of welding and machining. Engineers must navigate G-code-driven CNC machines alongside six-axis robotic systems with SINUMERIK controls — each with vastly different programming languages and degrees of freedom.
One engineer at BMA hired with a CNC background but was tasked with learning robotics from day one. He embraced the challenge and is now an expert in both fields — a testament to the adaptability required in modern manufacturing.
Software as the Driving Force
BMA’s hybrid operations depend on multi-functional CAM software. Siemens NX Multi-Axis Deposition enables programmers to create both additive and subtractive toolpaths within a single environment. This means engineers must understand both processes and synchronize them for successful builds — a critical step in creating a digital twin for hybrid machining.
At BMA, welding expertise isn’t limited to hands-on operations — it starts in the software. Engineers like Jordan factor in heat dynamics while programming additive toolpaths. Miscalculations in layer height can disrupt a build, but experienced engineers adjust settings in NX for Manufacturing to ensure success.
BMA doesn’t rely on intuition alone. Engineers meticulously record process data, tracking voltage, amperage, and temperature during builds. This data is stored in a database, allowing for process optimization and repeatability. Many BMA customers seek to explore additive manufacturing’s potential—whether to create complex geometries, reduce lead times, or supplement production. Each project involves extensive testing, often requiring destructive analysis like tensile strength testing. Even tasks like wire EDM cutting—traditionally handled by specialists—are now done by multi-skilled engineers.
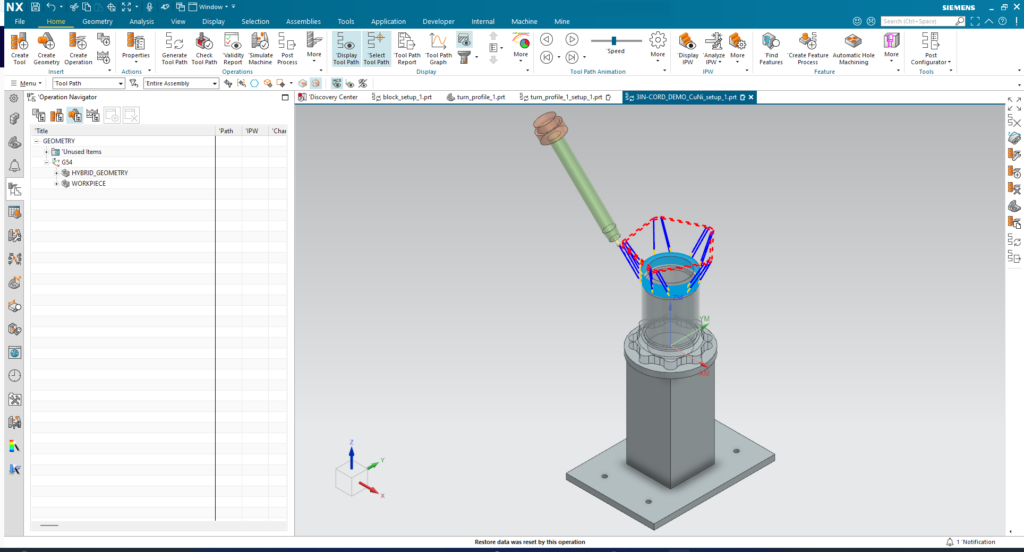
The rise of hybrid machining raises questions about workforce training. Should technical schools pivot toward certificate-based programs that teach a wider array of skills? Should degree programs become more flexible, allowing students to mix and match courses? Educators must adapt sooner rather than later.
The Future of Hybrid Manufacturing
BMA’s engineers embody the versatile workforce of the future. Their ability to blend skills across machining, robotics, and data analysis creates a dynamic, resilient manufacturing environment.
As additive manufacturing continues to evolve, shops like BMA will shape the next era of production. I can’t wait to see what they achieve next. Stay tuned for my next blog discussing the future of hybrid manufacturing and industry insights.