Is It Harder to Manage Manufacturing Data than Design Data?
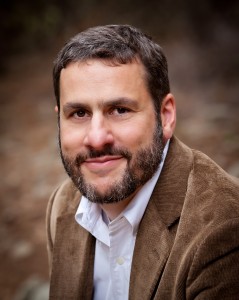
This blog post has been licensed for hosting by Siemens PLM. The concepts, ideas and positions of this post have been developed independently by Industry Analyst Chad Jackson of Lifecycle Insights. © LC Insights LLC
In the past few weeks, I’ve been lucky enough to attend a rash of conferences. This is one of the more enjoyable aspects of what I do because its a great way to be exposed to new approaches, ways of thinking and perspectives about technologies for product development. And I ran smack dab into one of this week, when I heard the following.
There is about 100 times the quantity of data that needs to be managed in manufacturing as there is in design.
Is It a Valid Point?
Well, I’ve publicly stated in the past that managing simulation data is far more complex than design data. But is the same true of managing manufacturing data? To start, I think there’s no argument that there certainly are more artifacts to manage. Consider this:
- The design model is used to create tooling, fixture and mold models, which can be highly complex assemblies themselves.
- Those tooling, fixture and mold models must have documentation, such as engineering drawings, to which they must be manufactured.
- Each of those items tend to composed of machined parts, so not only do you have design models of those tools, fixtures and molds, but then you have machining models where tool paths are defined.
- Then you have the outputs of those machining models which are raw NC tool paths.
- Those raw NC toolpaths, which are often composed of generic tool moves, must then be translated via a post-processor into machine specific tool paths.
- Some organizations use coordinate measuring machines (CMM) to numerically ensure that those told, fixtures and molds conform to the quality standards defined in their design.
There’s no doubt, there are a lot of representations and deliverables to manage. But actually, it’s not even that simple. The extra layer of complexity comes from a configuration management problem. You see, a machine specific tool path comes from a specific version of the generic tool path, which was generated off a specific version of the design model of the tool, fixture or mold which was also created from a specific version of the design model. A change anywhere along that path of traceability means everything downstream from it must be regenerated. Configuration management practices keep track of all of that.
My take? Yes. Managing this spiderweb of associated manufacturing artifacts and deliverables is more complex than managing design data.
Managing this Spiderweb
So how do most shops do this today? I’ve seen varying degrees of organization. Some don’t manage it at all. They just know that if anything changes, you need to redo everything. Other organizations attempt to track everything in a spreadsheet, but that commands disciplined participation from everyone involved. When there’s a breakdown in these scenarios, the implications are painful. Invariably, the wrong part gets machined. If that’s caught before the part is delivered, then the problem is just scrap and waste, no small loss given the expense of materials today. But if it is delivered, then a whole new set of problems arise because the customer is exposed to the mistake. It results in failed prototypes, shop floor errors, change orders and most likely very unhappy customers.
The alternative is fairly obvious. Product Data Management (PDM) and Product Lifecycle Management (PLM) systems are most closely associated with managing design data and product development processes. But many of them manage the spiderweb of manufacturing artifacts and deliverables as well. They often do it all in a very automated fashion, recognizing the relationships embedded in these data structures. And that’s no side note. For shops, its actually critically important.
Summary and Questions
Time to recap.
- The quote that started this post was: There is about 100 times the quantity of data that needs to be manages in manufacturing as there is in design.
- Above and beyond the design model, there are models for tooling, fixtures and molds, manufacturing models for each of them, drawings for the tools, generic NC tool paths, machine specific NC tool paths as well as CMM tool paths.
- The challenge isn’t just in the volume of artifacts that needs to be managed. A configuration management problem exists as well. Organizations need to know which models were used in succession to create the final deliverable. Changes to any associated artifact instigate the need for larger updates.
- Many organizations try to use memory or spreadsheets to manage this spiderweb of artifacts and deliverables, but there are dire consequences to the business if errors are shipped to the customer.
- PDM and PLM systems inherently know how to manage this spiderweb of artifacts and deliverables. It’s a consideration shops need to weigh seriously.
Your turn. What do you use to manage this network of things today? Are there other artifacts that I’ve missed? Are there other alternatives to managing them? Sound off and let us know what you think.
Take care. Talk soon. And thanks for reading.
About the Author
Chad Jackson is the President and Principal Analyst of Lifecycle Insights, a research and advisory firm that assesses the business impact of software applications and systems on engineering organizations. Chad has more than 15 years of experience with CAD, CAE, PDM, PLM and related technologies as part of the analyst community and software industry. Due to his industry knowledge and thought leadership, Chad is a sought-after expert, author and speaker that has advised, published and presented dozens of times domestically and internationally.