What’s New in Prismatic Part Machining?
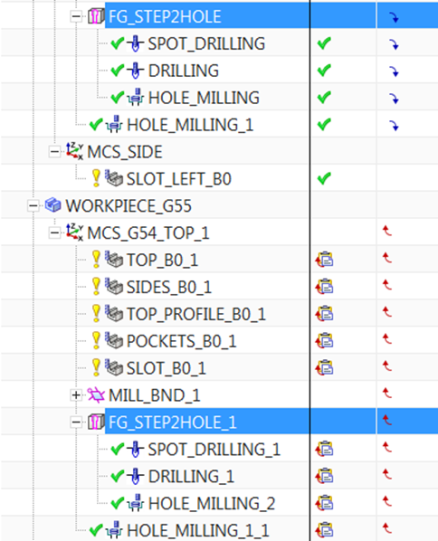
What’s New in Prismatic Part Machining? Oliver Sing, Siemens PLM Software, spoke to a capacity crowd on May 20 eager to learn about new functionality in the NX CAM prismatic part machining area since last year’s conference. This blog summarizes Oliver’s presentation and features all the cool new features released between NX 9.0 and NX 10.0.3. Please let us know if you have any questions about the new capabilities.
“NX for Manufacturing — Real solutions for manufacturing productivity” – by Oliver Sing
What is NX CAM?
NX CAM is our portfolio of digital manufacturing solutions for part manufacturing (as well as production line design) that help you to realize innovation by synchronizing product engineering, manufacturing engineering and shop floor production. NX CAM helps companies to eliminate inefficiencies, shorten ramp-up times and improve quality.
Aligned Feature Machining Concept & Roadmap
- NX 7.5 – NX 9.0
- New Drilling, Hole/Boss Milling, Thread Milling, Linear Groove Milling
- NX 9.0.1
- Hole Sequencing, New Feature Group Dialog, Tracking Points for Drilling
- NX 9.0.2
- Hole Chamfer Milling
- Enhanced Feature Grouping, Model Depth Control
- NX 9.0.3
- Sequential Drilling
- Radial Groove Milling
- Optimized Groups for new Drilling
- NX 10.0 & NX 10.0.1
- Rollover of NX 9 MR Deliverables
- Band Width for Hole Sequencing, Tracking Point per Diameter for Chamfer Tools
Upcoming NX CAM deliverables = NX 10.0.2
- Optimized Groups for Hole & Thread Milling
- Deep Hole Drilling (Gun-Drilling)
- Multi-Part Programming using Copy/Paste with Reference Enhancements
- NX 9 Hole Machining support
- Wave Link support
- NX 10.0.3
- Back-Countersinking
Dedicated Operations and Functionality to efficiently program Prismatic Parts
- Automatic Feature Recognition to collect the Geometry (prevent manual selection)
- Holes, Pockets, Grooves, Slots, etc.
- In-Process Feature Concept
- Visualize volumes to be cut
- Track what is already being machined and what still needs to be machined
- Manual or FBM based operation and tool selection
- Manual for programming prototype parts
- FBM based for reapplying established machining processes
Sequential Drilling (Web Drilling)
Capabilities
- Drilling or boring of coaxial holes that are intersected by air, avoid air cutting
- Motion Output à Interrupted Moves
- Geometry selection triggers infer of interrupted volume segments
- Operations in a sequence (i.e. drill, bore) utilize in-process feature volumes
- Model change updates in-process feature volumes
- Motions for Interrupted & Interrupted with Break Chip
- Is splitting motions in cut and step over sections to allow different feed rates
- Per cutting segment: Engage into material & break through material with lower feed rate
- First Cut distance = Shoulder depth
- Last Cut distance = Tip before break through
Radial Groove Milling
Capabilities
- Cutting of single or multiple circular grooves by using a t-cutter
- Mill a series of collinear grooves in a single operation
- Aligned with Hole Milling and Linear Grooving
- Half grooves supported but tool path will be fully circular
- Geometry selection triggers recognition of radial grooves and infers volume
- Operations in a sequence (i.e. rough, finish) utilize in-process feature volumes to prevent air cutting
- Model change updates in-process feature volumes
- Circular passes with axial & radial Stepover
- Level Sequencing
- Floor/Ceiling & Side Stock for Roughing & Finishing
- Avoid Re-cutting of Floor/Ceiling per Relief Clearance like in Linear Groove Milling
- Collision / Gouge Check like in Hole Milling
- Automatic switch of Tracking Data like in Linear Groove Milling
Hole Machining Sequence Optimization
Capabilities
- Automatic initial sequencing for features in a feature group (“Shortest Path”)
- Explicit sequencing now also available on feature groups created by Create Feature Process
- Explicit sequencing actions
- Closest, Shortest Path
- Primary Direction (Vector & Zig / Zig Zag)
- Reverse
- Drilling in one direction
- Tapping in the reverse direction
- Reload from Parent
Primary Direction & Band Width for Optimization
Capabilities
- Use for Primary Direction Optimization Method
- Includes locations that are slightly off the grid into a band to avoid unnecessary tool travel
- Preview Sequence before generating tool path
- Available in Feature Group, Hole/Boss group, Geometry dialog within operations and Optimized groups
- Use for Primary Direction Optimization Method
Optimized Groups for Hole Machining
Capabilities
- All Hole Machining Operation are now supported (Drilling, Hole Milling, Thread Milling, Radial Groove Milling and Chamfer Milling
- Combines tool path of multiple operations that are using the same tool
- Provides list of Machining Features and their In Process Features
- Reduce transition motions to save machining time
- Sequence is already optimized (shortest path) after creating the optimized group
- Quick Preview / Display of machining sequence
- Sequencing actions for further optimization
- Change NCM settings at Optimized Group level
- Standard Tool Path actions
- Select operations in the ONT à Object à Optimize à Create Optimized Group
Back Countersinking (Tool)
Capabilities
- New dedicated tool type for back-countersinking
- Parametric tool definition
- Off-center shaft
- Head Offset for required minimum shift (As per tool catalog/manufacturer)
- Control dimensions by Length, Diameter, Neck Diameter, Minimum Hole Diameter and Insert Size
- Supports 45 degree cutting edges
- Spinning and non-spinning representation
- Library Support (Import/Export)
- Export implemented under ENV
- UGII_CAM_BACK_COUNTERSINK_TOOL_LIB=1
Back Countersinking (Operation)
Capabilities
- New dedicated operation type for back-countersinking
- Countersink holes from the back-side by:
- Positioning the tool centerline over the hole in non-spinning mode
- Shift off-center by recommended offset
- Engage into hole
- Shift to centerline
- Switch to spinning mode
- Cut chamfer with a backwards motion
- Reverse procedure to retract out of the hole
Capabilities (Geometry)
- Same In-Process Feature geometry concept like other hole machining operations
- HOLE_BOSS_GEOM, Feature Group, In operation
- For modeled and unmodeled chamfers
- C-Sink Diameter controls chamfer size
Capabilities (Operation)
- Same look and feel like regular countersinking operation
- Use Cycle / Back-Drilling
- Shift (Head Offset) taken from tool
- Supports Tool Path Verify, Simulation, IPW update
Deep Hole Drilling (Gun Drilling)
Capabilities
- New Cycle Subtype in Single Moves Drilling
- Drilling of deep holes
- Pilot hole support
- Dedicated motion and event framework to control engage, cut and retract conditions. (Spindle, coolant, dwell, etc.)
- Same In-Process Feature geometry concept like other hole machining operations
- Cross holes & intersection handling
- Automatically detects cross holes and determines if they have been drilled or not
- Control feed rate at intersections
Multi-Part Programming Enhancements
Capabilities
- Copy/Paste with Reference now supports wave linked geometry
- In the CAM Setup, create wave linked body from part geometry in component
- Part geometry of all components must be wave linked
- Assign wave linked geometry to part geometry in WORKPIECE group
- Geometry is mapped properly from the wave linked body of the source component to the wave linked body of the target component
- Copy/Paste with Reference now supports NX 9 hole machining operations
- Only program source component by using feature recognition or manual selection and the new hole machining operations
- Use Copy/Paste with Reference to create feature groups and or operations for the target geometry
- Automatically creates machining features for target geometry
Capturing Machining Knowledge by using NX CAM UI
New “Operation Teaching” front end UI for MKE (Machining Knowledge Editor)
- First time users prefer to work exclusively in NX CAM
- Would like to avoid using the MKE as the rule definition environment to start with
- Shop Floor oriented; Ease of use; Define, Teach, Apply through a single application
- Capturing machining variants by using NX CAM UI (Operation Navigator)
- Teach customer specific feature type names and their operation sets per condition editor
- Define explicit operation sets (machining variants) and not re-use Machining Rules in multiple sets
- Easier to maintain and visualize (although Machining Rules are often duplicated)
Capabilities / Workflow
- Automatic mapping rules for customer specific feature types and their names
- For each feature type use a single part file to define the feature names and their processes (operation sets)
- MB3 action to launch Condition Editor
- Provides application conditions (which operation set is applied i.e. based on feature dimensions, color, etc.)
- Provides operation conditions (for tool selection and setting of operation parameters)
- Use Objects, their parameters and operators to construct conditions
- Copy/Paste conditions
- Teach conditions (Machining Rules) to MKE
- Edit Machining Rules in MKE or NX CAM
- Add Add-Ons and refine operation conditions in MKE
Read all of our prismatic part machining TECH TIPS!
To learn more about Siemens NX for Manufacturing solutions, please visit our website.