The Art of the Possible at PLM Connection
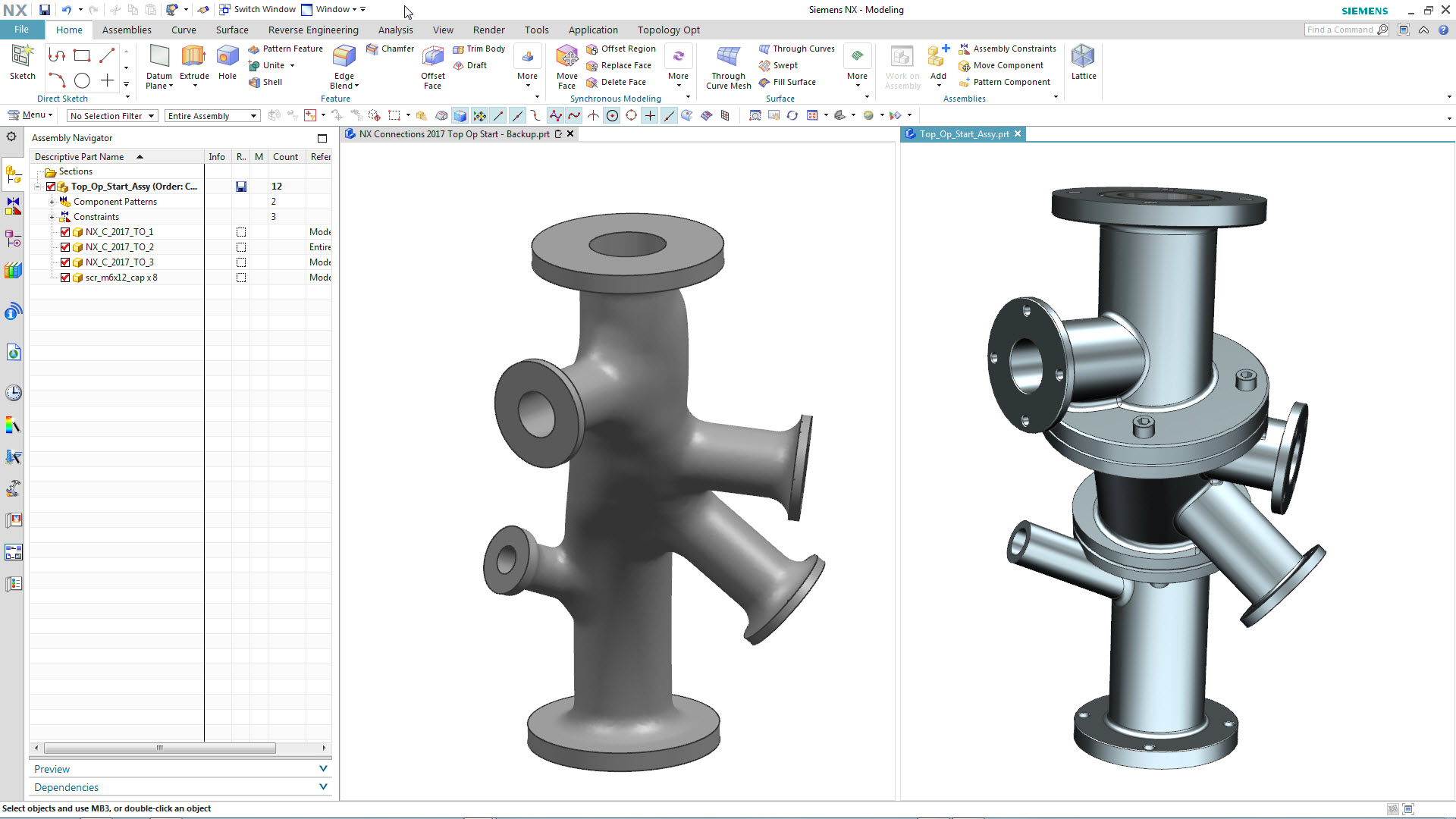
Siemens PLM Connection is the one time a year that users of our software, Siemens employees, and our partners come together under one building to discuss best practices and, as CEO Tony Hemmelgarn said during yesterday’s closing session, “next practices.” What will the future of PLM hold? How will computer-aided design evolve, and what can you expect to see?
That was the focus of this morning’s session Art of the Possible with Senior Vice President of Product Engineering Software (NX) Bob Haubrock. He connected the dots between what is new in NX today (or will be available within the year) to the long-term vision and overall direction not just of NX, but of computer-aided design in general. Because as technology evolves, we have the opportunity to leverage that technology to improve processes for design, simulation, manufacturing… all aspects of product development. All with the goal to help companies innovate and deliver the best products they can, both in terms of quality and safety.
There were three key areas Bob focused on, and the session was peppered with live demonstrations to show as well as tell the story he talked about:
- Generative design
- Convergent Modeling
- and MCAD / ECAD integration
Generative design uses the power of NX to suggest design alternatives, enabling designers to explore new shapes and solutions that would otherwise never be possible. It harnesses the power of a number of technologies including traditional feature modeling, advanced modeling tools like NX Realize Shape, and new technologies such as topology optimization and Convergent ModelingTM technology.
In the example shown onstage, the CAD user starts with a traditional feature-based model. He identifies a volume that the design must fill, selects any holes that must be retained, and then runs topology optimization to determine the best design alternative within those parameters to achieve a model that is lighter and uses less material. The end result? An organically shaped design that would be near impossible to model manually.
Of course, the output of topology optimization is faceted geometry. This is where Convergent Modeling comes in. Convergent Modeling, of course, allows designers to work directly with faceted data, combining both traditional feature-based modeling with facet-modeling in one. There are no additional tools required; Convergent Modeling technology simply works. This eliminates the hassle of data conversion in order to work with the results you get, allowing you to use topology optimization results as they are.
When it comes to manufacturing, again the irregular organic shapes generated by these design methods are virtually impossible to create using traditional techniques. Additive Manufacturing is required to bring these models to life in the real physical world. NX continues to expand capability in the area of Design for Additive Manufacture, as demonstrated by Bob and the NX team. There are a number of validation tools in NX today to check designs for 3D printing:
- Minimum wall thickness can be specified to ensure printability of the part
- Overhang angle lets you identify part regions that require support while printing
- Wholly enclosed volumes can be recognized to ensure efficient post-printing operations of these areas
- Printable volume quickly calculates if the part fits within the printer build volume
What I think you’ll find most exciting, though, is the new lattice design capability coming to NX soon. With this tool, you can automatically generate a lattice in a given space, including in topology optimized designs. This allows you to greatly reduce the weight of a part without compromising strength or integrity of the design. My colleague Paul demonstrated this capability in a design workflow during the presentation.
The enhancements discussed so far are exciting ways the NX team has leveraged existing or emerging technologies for use in design and manufacturing, opening the doors for further innovation down the road.
A bit more forward thinking in terms of where we are today with NX is Bob’s final key point: the integration of MCAD (mechanical) and ECAD (electrical). As Bob said, it is the combination of the two that is imperative for the future of design. How many products out there today are purely mechanical? None.
Think of a system like a car, for example, that combines the mechanical components of the engine and parts with the electrical components that control everything from the heating and cooling system, to automatic braking, even to tracking and regulating performance of the car. This is the situation faced by virtually every product industry. Electrical components are everywhere. Thus, the integration of electrical and mechanical design is a necessity. The acquisition of Mentor Graphics, a world-leading ECAD company, opens the door for us to expand on the integration of the two in design. Look for a post coming soon from Bob to explain what the Mentor acquisiton means for the future of design.
Ultimately, the Art of the Possible is about what you can achieve in NX today, tomorrow, and far into the future. As technology continues to evolve, so must your design tools. Imagine the possibilities in terms of what you can create and design five, ten, or even fifteen years from now. Where will the future take you?