Design For Purpose: Virtual Simulation and Testing
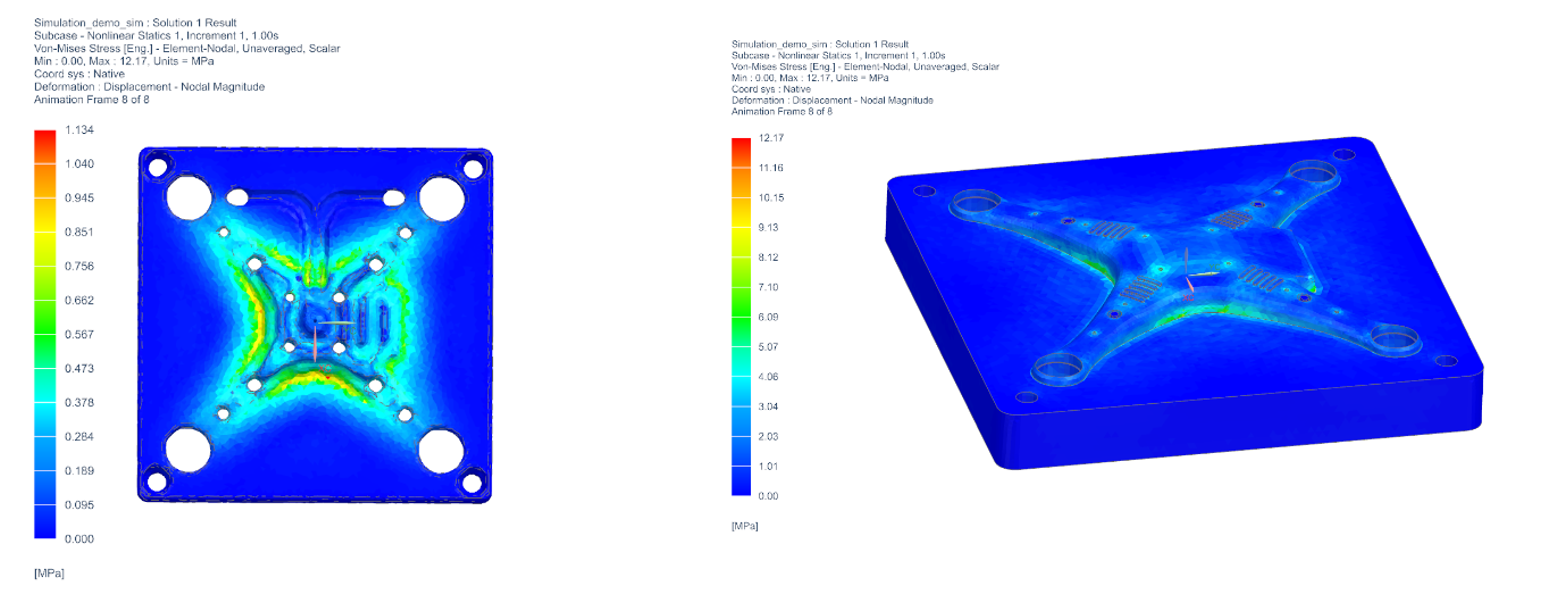
Welcome back! Thank you for your continued interest in how additive processes can radically decrease manufacturing’s sustainable footprint. In the first article, we covered NX lattice structure capabilities for enhanced designs. In the second article, we covered the incorporation of Multimech to accelerate the product development lifecycle by extending finite element analysis to the microstructural level to predict where and how failure will occur. If you’re new to this series, or are interested in reviewing these previous articles, click here and here.
Now I will answer the question you’ve all been asking yourself, “what’s next?”. The answer to this nail-biting question is simulation! The third step in this sustainable process is validating product design through integrated simulation. Let’s dive into it, shall we?
Understanding how a component or product assembly reacts under stress or vibration is critical in any industry, but as products and materials become increasingly complex, engineers need tools that go beyond linear statics analyses. Simcenter includes the structural solutions you need for a wide range of structural analysis problems within a single user environment. You no longer need one tool for linear statics, another to study fatigue, and yet another for nonlinear analysis. As a result, engineering departments can consolidate analysis tools, and you only need to know a single user interface.
Our structural simulation solutions can help you accurately simulate both linear and nonlinear analysis. Linear analysis is used to solve static problems, such as determining if a structure will fail under a prescribed load and can also be used to solve transient problems where loads change over time. Simcenter features a complete range of integrated linear analysis functionality, including analysis for linear statics, normal modes and buckling. You can use these capabilities to evaluate structural performance for applications in a variety of industries. If deformations are large, if linear material assumptions are invalid, or if contact is a factor, then nonlinear analysis is the appropriate simulation choice. Simcenter solves a wide range of nonlinear analysis problems. Nonlinear implicit and explicit analysis solvers enable engineers to address problems as simple as a plastic catch, or as complex as a car body roof crush analysis. Integrated explicit dynamic capabilities let you perform metal forming analysis or evaluate electronic hardware performance during a high impact drop test simulation.
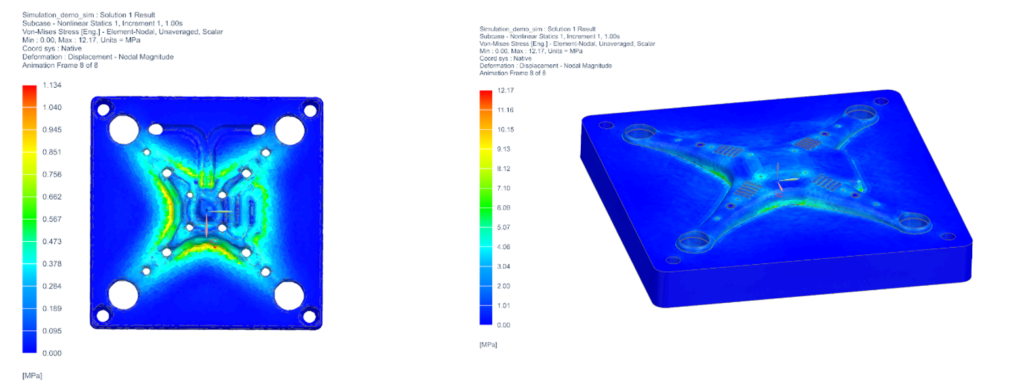
The other type of simulation supported by Simcenter is thermal simulation. Although this will not be demonstrated in this article, it is important to note that thermal management is a major consideration for a wide range of products, including industrial machinery, automobiles, and consumer electronics. The objective of any thermal management solution is to maintain a product’s temperature within a range that is optimal for performance. Accomplishing this may require the removal or addition of heat, either passively or in an actively managed fashion, and this can be evaluated using thermal simulation software. Simcenter includes comprehensive, best-in-class thermal simulation capabilities that can help you to understand the thermal characteristics of your product and subsequently tailor your thermal management solution for optimal performance.
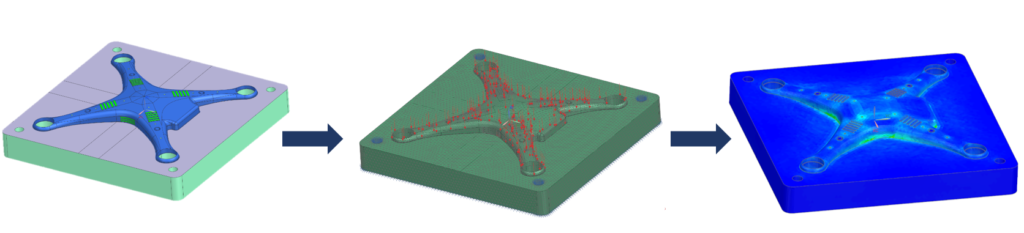
Computer aided engineering provides virtual simulations and allows for faster and more cost-efficient product development, manufacturing efficiency evaluation, simulation as concept demonstration, one step closer to single-prototype development stage, resource optimization and less energy consumption. In addition to its usefulness as a tool that provides the numerous commercial benefits, virtual simulations can have another dimension that is sustainable design of both the manufacturing system and the product/service. Virtual engineering and simulations empower users to support the growing importance of sustainable manufacturing by providing as a solution to the resource’s scarcity, the global willingness to reduce carbon emissions, and the customers attraction to environmentally friendly products.
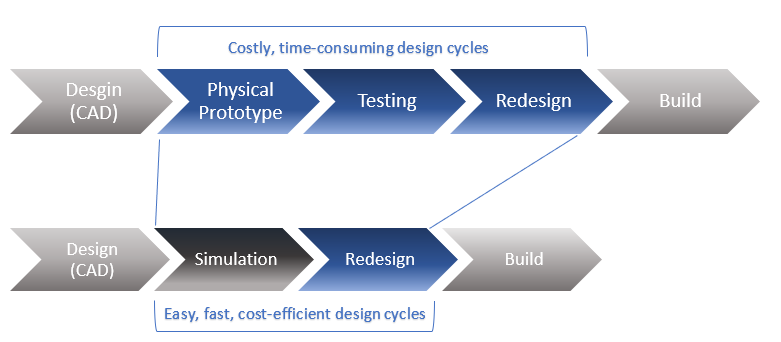
I know what you’re thinking, “This is all talk, there’s no way this is truly this simple and supportive”. I guess I’ll just have to prove it in a demonstration. Continuing with the injection die mold that I’ve redesigned for additive manufacturing, I will conduct a structural linear analysis to determine that the new lattice structure design is just as sturdy and design-efficient than the original one. To do this, I will create a FEM file in Simcenter to mesh the design to have an inner lattice structure portion and an outer solid shell. In this file, I will also apply the material properties to each section. Next, I will import the FEM file into a Simulation and apply fixed constraints to the bolt holes of the part and apply a force to the center of the design to simulate the real-life events. Once the loads and constraints have been applied, I will utilize the MultiMech multiscale solver within the Materials Engineering tab to run the simulation at the micromaterial level. Lastly, I will run the traditional mold design in the exact same simulation and examine the outcomes.
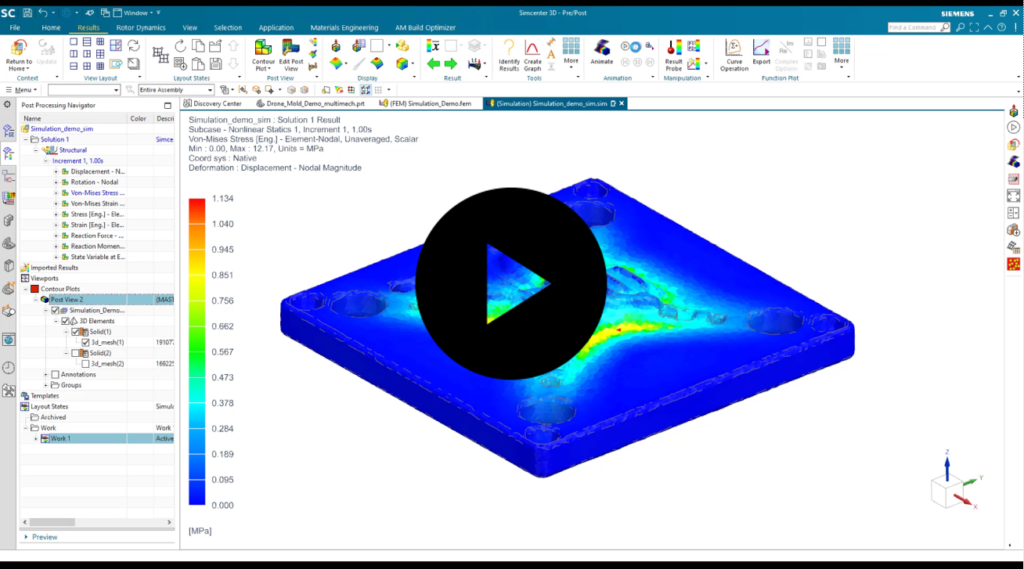
In that demonstration I did not show the set-up of the traditional mold tool. The process was the same as that shown with the innovated part design. The results do demonstrate that the additive manufactured part designs as well as, and even better than, the original design. Additive manufacturing is the solution of the future and the key to sustainable innovation. Integrated simulation and testing allow you to streamline the product development cycle, increase the durability and sustainability of designs, and get your parts to market faster. Reduce material usage, decrease energy spent on physical prototyping and machining, and allow yourself the ease of designing and testing all in the same work environment. Let the future start today with NX’s fully integrated product development workflow!
Tune in next time to learn about the last step of how to design for purpose and maximize sustainability. Want a hint? I’ll show you how to utilize a design space exploration and optimization software that allows you to run through numerous solutions in minimal time without the need for manual design alterations.
Comments