Simulation-driven design: A closer look at how engineers can save time, resources and manpower by frontloading simulation
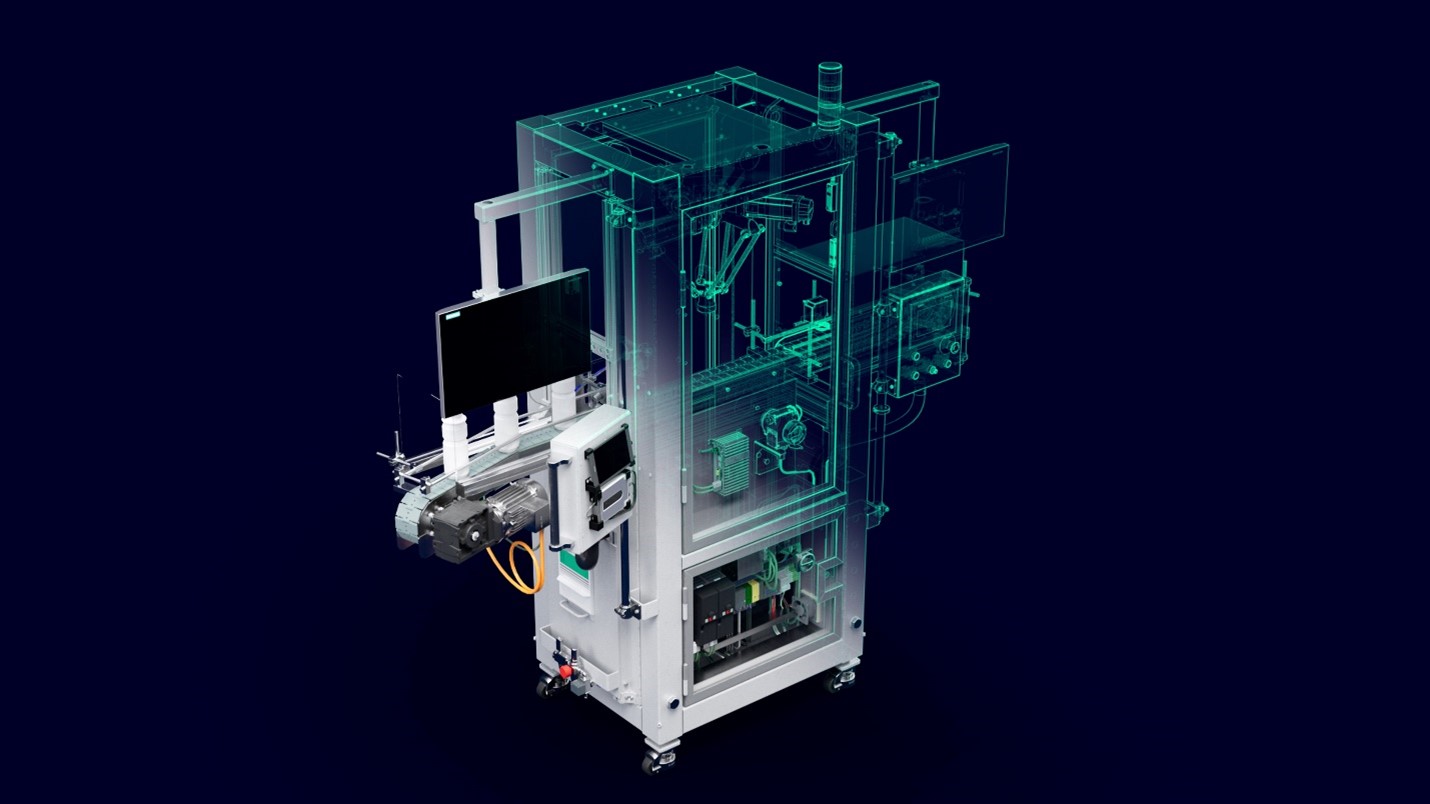
This blog article is co-authored by Rajesh Selvaraj Ramaya and Tim Yerby
An introduction to simulation and the digital twin
The industrial machinery landscape is changing. To meet consumer demands, machines must be faster, more reliable and more agile. Machine builders and OEMs need to find new ways to improve operational efficiency, adapt to changing requirements and harness product development complexity into a key competitive advantage.
To make the machines of tomorrow, businesses can no longer rely on traditional serial design processes, which require large amounts of “worst case” design calculations, copious amounts of trial-and-error testing, long feedback loops from product evaluations, and long development timelines with high levels of design risk. The machines of tomorrow require a holistic digital approach. They require a digital twin, a virtual 3D mockup of a machine displaying various attributes from speed and output to vibrations and heat.
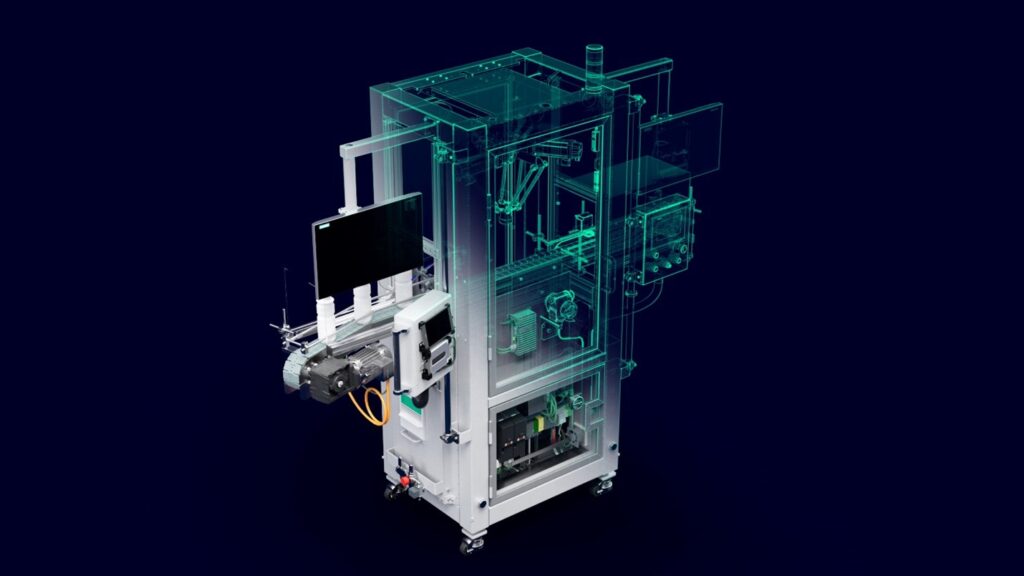
Armed with the digital twin, engineers can evaluate their designs early and often using fully integrated simulation software. Simulation and testing are the beating heart of the digital twin, as they provide manufacturers with a predictive capability, providing feedback on every aspect of product performance.
The power of machine simulation
Simulation is an industry game-changer. Why? Because manufacturers across industries accept two common truths:
- Decisions made during the early concept stages lock nearly 70 to 80% of the development costs
- The cost to fix defects rises as you proceed from concept to production
So, with simulation, these two truths can change: machine builders can virtually build, prototype and commission their machines all before physical production or hardware enters the development cycle. In turn, machine builders can accelerate machine design calculations and reduce the risk of failure. Better design calculations also mean machine builders can rapidly design systems and improvements while optimizing their costs through strategic material and hardware choices.
Simulation empowers innovation against challenges, whether a business seeks to optimize multiphysics behavior, adopt new technologies like additive manufacturing, or lightweight machine materials like composites. Simulating early and simulating often is essential to avoid product failures or cost overruns.
Simulation-driven design
What sets simulation-driven design apart from traditional simulation is its integration within the design process. Embedding multi-physics prediction capabilities directly into the native CAD tools allows design engineers to gain performance insights earlier in the design phase, streamlining the development process, enhancing design excellence and improving product quality. This integration enables the creation of more advanced machines and accelerates time-to-market compared to non-integrated approaches.
But don’t take my word for it: In a report published by Aberdeen Research Group, it was found that “workflows that isolate a simulation specialist group can lead to bottlenecks in the design process.” In other words, when design and simulation disciplines are kept apart, the chance of miscommunication, data duplication, translation errors and other issues substantially increase.
The value of integrating simulation with design grows more apparent when we consider the growing complexity of today’s machines. Many of today’s machines require mechanics, electronics and software to cooperate as one system, but often, these domains work in silos. A siloed work environment significantly slows down the development process and can frequently cause bottlenecks. Simulation-driven design disempowers these risks because it accounts for each domain’s functionality and performance limits simultaneously rather than consecutively, thus expediting machine development.
One of the key advantages of simulation-driven design is its ability to identify potential design flaws early in the design cycle, leading to significant time savings. By frontloading simulation, testing and validation take place earlier in the development process. With simulation-driven design catching most of the potential errors upfront, engineers can cut time off the backend of machine development, as they reduce the need for physical prototyping, physical commissioning and hardware-in-the-loop testing. In turn, machines can enter the competitive landscape sooner, and businesses that frontload simulation gain an advantage in the market.
Deploying simulation-driven design
Businesses can take several routes to actualizing simulation-driven design. The typical route for implementation is an out-of-the-box CAD environment. In this scenario, businesses license or own CAD software that comes with native features integrating design and simulation; simulation is embedded directly into their design tools and offers basic structural, motion and flow simulation.
After establishing basic environmental compatibility between design and simulation, designers can use this common platform to model and understand their design’s complexity: multiple physics solvers can be examined at the same time, real-world conditions can be simulated more accurately, and data transfers and multiphysics workflows can happen seamlessly.
Designers can even go a step further by automating routine simulation processes during design development. Namely, they can set up workflows to capture and deploy advanced simulation testing, deriving benchmarks into a dashboard and making it possible to scale their technology from simple design into analysis. This analysis includes single-part analysis, assembly-level analysis, and high-end multiphysics. Engineers gain a clear path to upgrading their physics, implementing bigger models that can do more or even improving basic performance areas on a machine. It also often means easier collaboration with third parties, as this data analysis can be shared across the cloud.
For the truly savvy business owner, CAD and simulation don’t just integrate – they come from the same tool. While integrated tools offer basic simulation and modeling, CAD-simulation coming from the same tool provides high-end 3D simulation, making it easier and faster to mesh design with simulation for greater accuracy and lowered costs. It also means it’s easier than ever to access multiple simulation tools at a time – a high-end CAD-simulation solution often comes with value-based licensing, a methodology where users can pick and choose which functionalities they need through the use of tokens. It’s an effective way to control costs and gain the most value from a variety of products.
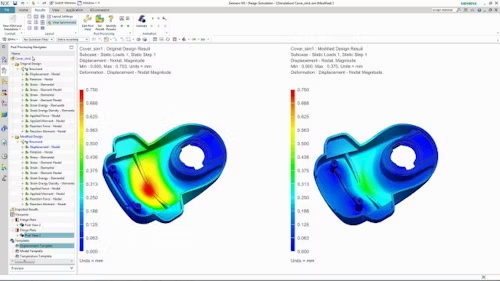
A visionary business owner takes it one step further by using multidisciplinary design analysis and optimization (MDAO) methodology, i.e., automating repetitive tasks in the design and optimization process, streamlining workflows and enhancing efficiency. Such automation can lead to faster decision-making and more comprehensive exploration of design spaces. Now, let’s take a closer look at how a certain company used simulation-driven design to improve their products and extend their lifetime.
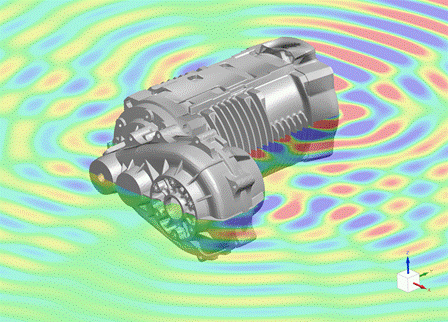
What simulation-driven design success looks like
Mitsubishi Materials Corporation, a metalworking solutions business, delivers a wide range of machine-cutting tools across several industries. Due to the thermomechanical effects on their tools, one of the biggest challenges Mitsubishi faced was expanding their tools’ lifespans.
After partnering with several third parties to develop a new cooling methodology and apparatus for their machine cutting tools, Mitsubishi needed a means for simulating how these items would perform.
Partnering with Simcenter, Mitsubishi engineers were able to incorporate simulation-driven design into their development process, making it possible to test their new cooling methodology and apparatus with their machine-cutting tools.
Mitsubishi successfully extended their tools’ lifecycles by 40 percent with the new cooling system when compared against the old cooling system. Furthermore, simulation-driven design helped them improve their tools’ cutting length by 70 percent, in addition to improving their tools’ mass flow and velocity while decreasing pressure. As Mitsubishi’s story demonstrates, simulation is more than just a trend; it’s an actual means to creating and optimizing highly productive machines and tools that can transform our world from the micro level to the macro level.
Simulation-driven design enables businesses to make what once seemed improbable finally possible, with as little as a keyboard and a few clicks of the mouse. So, what are you waiting for?