Improve machine and component durability with strength and fatigue simulation analysis
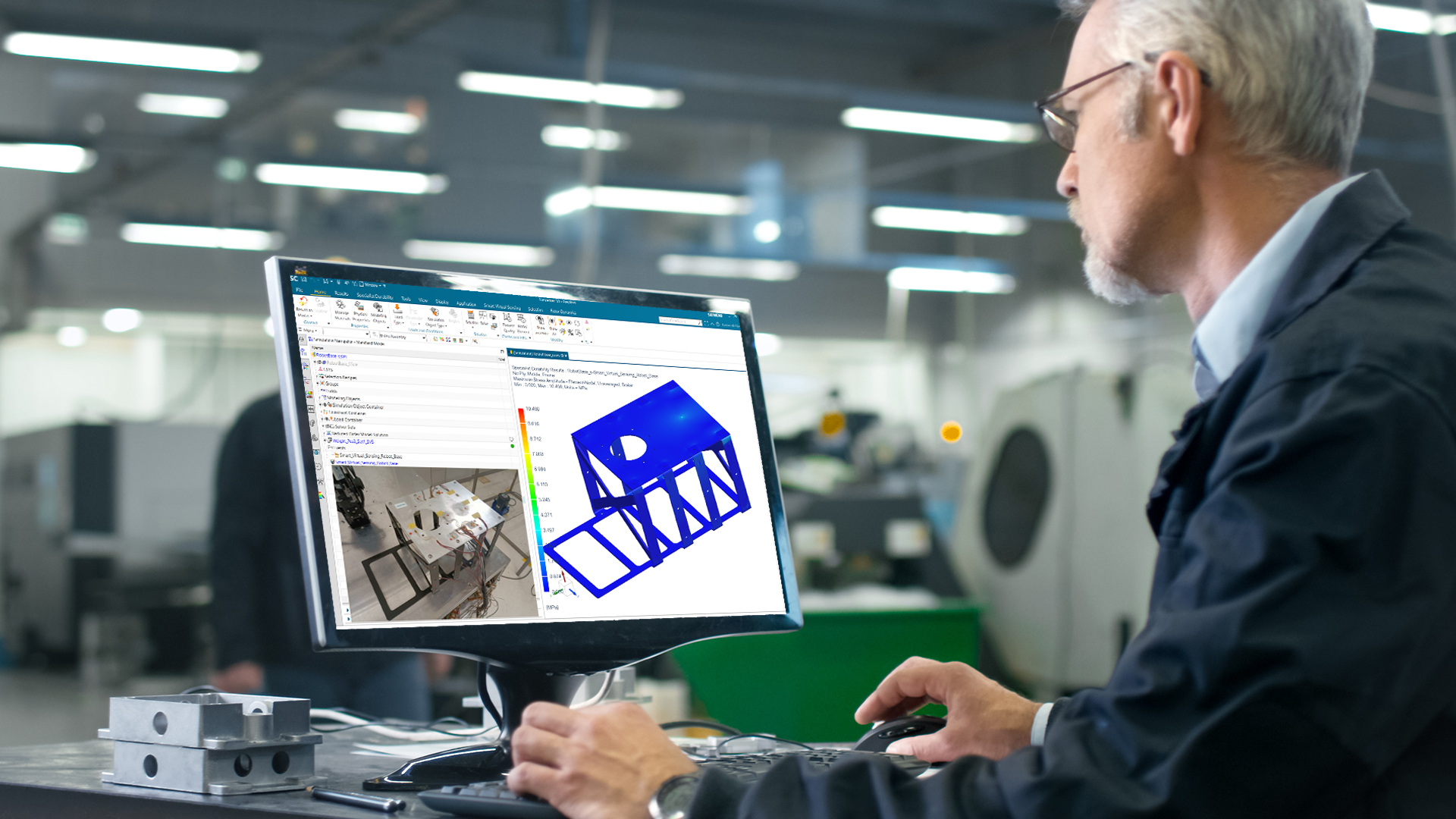
Machine builders, OEMs and component manufacturers want to prevent fatigue failure, or at least guarantee a certain lifetime for their products.
Fatigue assessments aim to inform engineers of the durability and strength of their products.
A recent webinar presentation from ASML and Siemens Digital Industries Software took a closer look at the importance of these tests and examined how engineers can integrate fatigue assessment directly into their design process.
Watch the webinar trailer:
The value of fatigue simulation analysis for industrial machines
Industrial machines and their components must withstand high accelerations over numerous cycles. This causes a natural wear and tear on valuable manufacturing equipment.
Fatigue assessments during the design process lead to more durable machines and components, and they can provide valuable insight for preventative maintenance during the product lifecycle.
Eva Eggels of ASML opened up this webinar with an example of a lithography machine, an essential component in computer chip manufacturing.
Fatigue assessments traditionally involved complex processes with significant manual intervention, leading to inefficiencies and a high possibility for errors.
Simulation software like Simcenter 3D Durability offers a more streamlined solution by integrating fatigue assessment into the design process.
This reduces the risk for errors and improves workflow efficiency by providing engineers with real-time insights into structural stresses.
Streamline fatigue simulation analysis with comprehensive workflows
Simcenter 3D provides a comprehensive workflow that integrates finite element analysis with durability assessments, eliminating the need for manual data transfer between separate tools.
This integration supports a more seamless analysis process where fatigue assessments are performed directly on stress data derived from FEM models.
Engineers can visualize regions where stress loads are highest through intuitive color-coded outputs, making it easier to understand the stress impacts on designs.
In this webinar clip, Eva Eggels compares the fatigue simulation analysis with and without Simcenter 3D.
The video above highlights the real-world benefits of integrating advanced simulation technologies into fatigue assessment.
With a single tool, Simcenter 3D Durability, users can streamline processes and reduce the risk of errors.
Improve designs of you machines and components with fatigue simulation analysis
The ability to perform direct fatigue assessments with the digital twin allows for a more streamlined process where critical regions can be easily identified and analyzed.
This provides valuable insights into potential design improvements, ultimately contributing to more reliable and robust machines and components.
In the next webinar clip, Dr. Michael Hack of Siemens Digital Industries Software shows users how to simulate and analyze multiple different scenarios.
Additionally, template-based solver intelligence within Simcenter 3D further enhances this process by allowing expert-defined templates that ensure robustness and repeatability in analyses across different projects.
This capability not only improves the quality of fatigue assessments but also empowers engineers to make informed design adjustments early in the process.
The role of virtual sensors and their placement in fatigue simulation analysis
An integral part of enhancing fatigue analysis is the use of smart virtual sensors.
This approach allows engineers to predict and analyze operational loads more accurately by strategically placing virtual sensors.
These sensors simulate real-world conditions and provide critical data that informs the fatigue assessment process.
In this webinar clip, Dr. Michael Hack shows users how Simcenter 3D strategically places these sensors.
Optimal sensor placement ensures data collection is both efficient and comprehensive, covering all potential stress points in a design.
This methodology not only improves the accuracy of fatigue predictions but also supports predictive maintenance strategies by providing insights into when and where potential failures might occur.
Conclusion: More durable machines and components with fatigue simulation analysis
Integrating fatigue assessment into the design workflow represents a significant advancement in machine and component engineering.
By providing a comprehensive and streamlined approach to fatigue simulation analysis, this tool empowers engineers to make informed decisions that enhance the safety and reliability of their designs.
As machine engineering continues to evolve, embracing these technologies will be crucial for maintaining competitive advantages and ensuring the longevity of products.
Watch the full webinar and go in-depth with into how these tools can transform your engineering processes.
Comments
Leave a Reply
You must be logged in to post a comment.
Improving machine durability is essential for sustained effectiveness and performance. High-quality equipment solutions designed for reliable operations are offered by Hydro-Mechanical Systems. Even in the most challenging circumstances, their proficiency in providing precisely built components guarantees dependability. Businesses can use tools made to endure wear and tear by selecting Hydro-Mechanical Systems, which will increase productivity and decrease downtime.
Visit Hydro-Mechanical Systems Website to get more information! https://hydromechanical.com/