BOM and configuration for machine builders 101
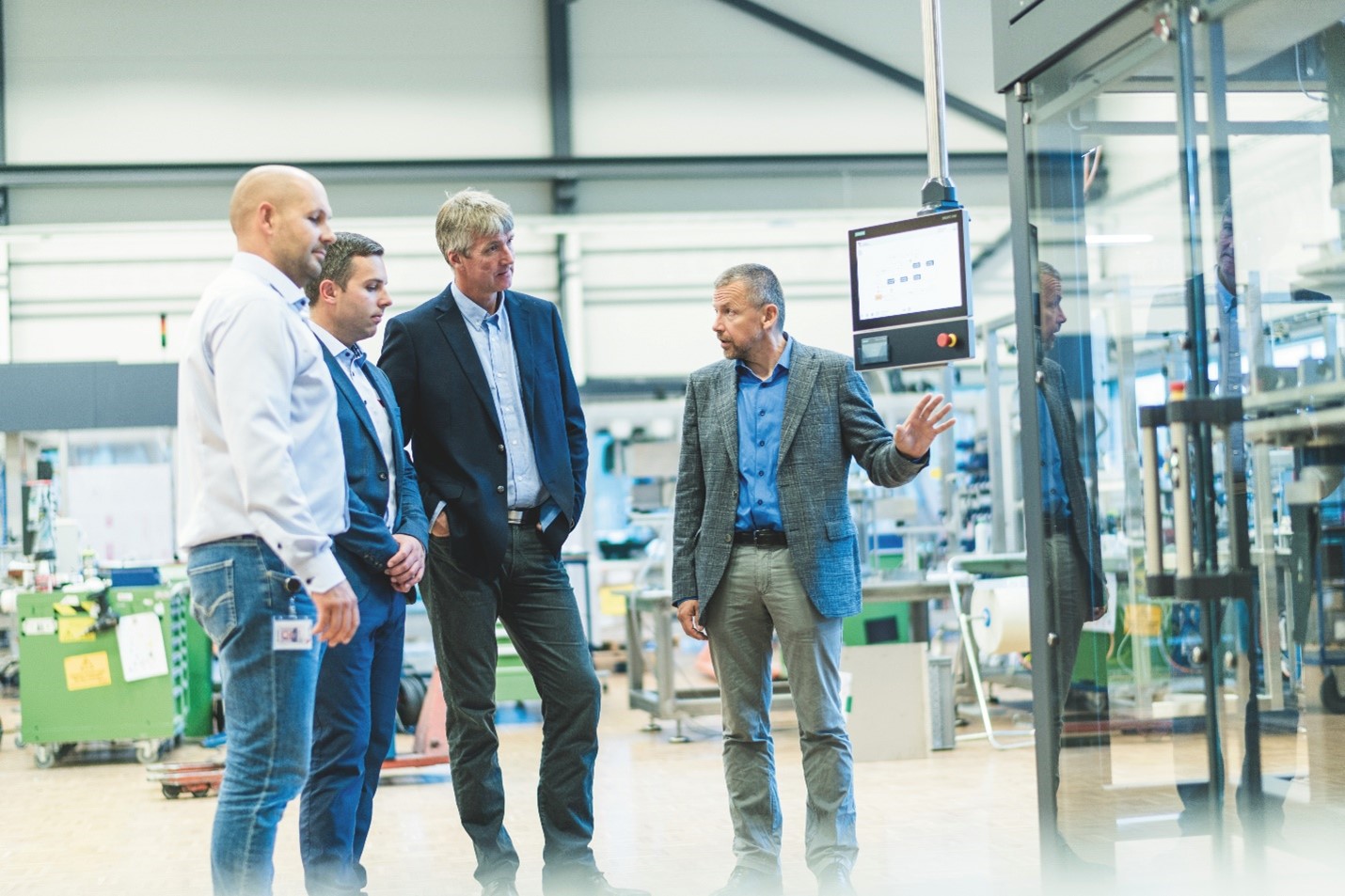
This article is a conversation with Tim Yerby, Director of Industrial Machinery Solutions at Siemens, and Will Haines, Market Management Senior Representative at Siemens
What is a bill of materials and why is it crucial to machine builders?
A BOM is a structured list of all the components, assemblies, and parts needed to manufacture a product. In machine building, it serves as the foundation for managing parts, assemblies, and their relationships, ensuring accurate manufacturing, assembly, and maintenance of your machines. Beneath the BOM umbrella, there are a few specific types of BOMs to consider:
- The Design Bill of Materials (DBOM): Also referred to as the CAD BOM, this represents the geometrical definition of a product and helps manage the design data that comprises design components and their instances.
- The Engineering Bill of Materials (EBOM): The EBOM manages all the parts and configurations needed to define the finished product. It includes information about product specifications, tolerances, quantities, units of measure, and related engineering standards.
- The Manufacturing Bill of Materials (MBOM): The MBOM defines all the parts and assemblies required for production, typically pulled from the EBOM. The MBOM also includes material requirements, supplier sourcing and part procurement lead time, manufacturing tolerances and quality standards, testing and validation procedures, and regulatory and compliance information.
These types of BOMs are fundamental in optimizing manufacturing operations, as we’ll touch upon in a moment.
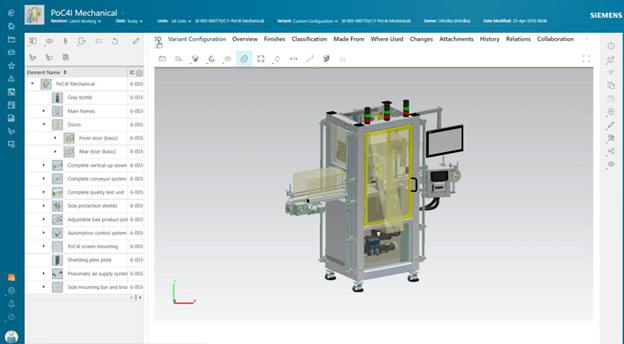
How do machine builders use BOM data?
It all starts with the EBOM. The EBOM defines specific criteria, and then the MBOM absorbs and utilizes this information, specifically part numbers and descriptions, part quantities, part specifications (dimensions, materials, and performance characteristics), and the hierarchical relationship between assemblies, sub-assemblies, and individual components of the machine.
In the MBOM, you will see manufacturing consumables, like cutting and machining fluids, welding and soldering supplies, abrasives, marking and measuring tools, and even protective equipment employees need in the production process. It also manages part surface treatments like paints, primers, and coatings.
A derivative of the MBOM is the Bill of Process (BOP), which outlines the sequence of operations, instructions, and resources needed to manufacture a product, detailing how each component is processed.
If your machine is manufactured across multiple plants and geographies, a Plant BOM will list all materials, components, and sub-assemblies required to manufacture a product at a specific manufacturing plant, often customized to the plant’s capabilities and processes.
Some machine builders handle part and component assembly separately from manufacturing operations. A dedicated assembly group would maintain an Assembly BOM to manage the parts to be assembled along with specific assembly instructions.
An Assembly BOM also includes consumables such as fasteners, adhesives and sealants, lubricants, electric consumables like wire connectors, cable ties, heat shrink tubing, and solvents and degreasers needed for cleaning the assembled components.
The Shipping BOM documents everything needed to ship the product to the customer, including detailed instructions on what to pack and how to pack it. The packaging material, be it cardboard boxes, crates, bubble wrap, or foam inserts, needs to be itemized and managed.
Machines are often shipped with protective wrap, cushioning materials, and straps to secure the package in transit. Some companies manufacture their own pallets and boxes while others procure these materials from suppliers, so it’s important for this BOM to communicate with manufacturing and supply chain BOMs.
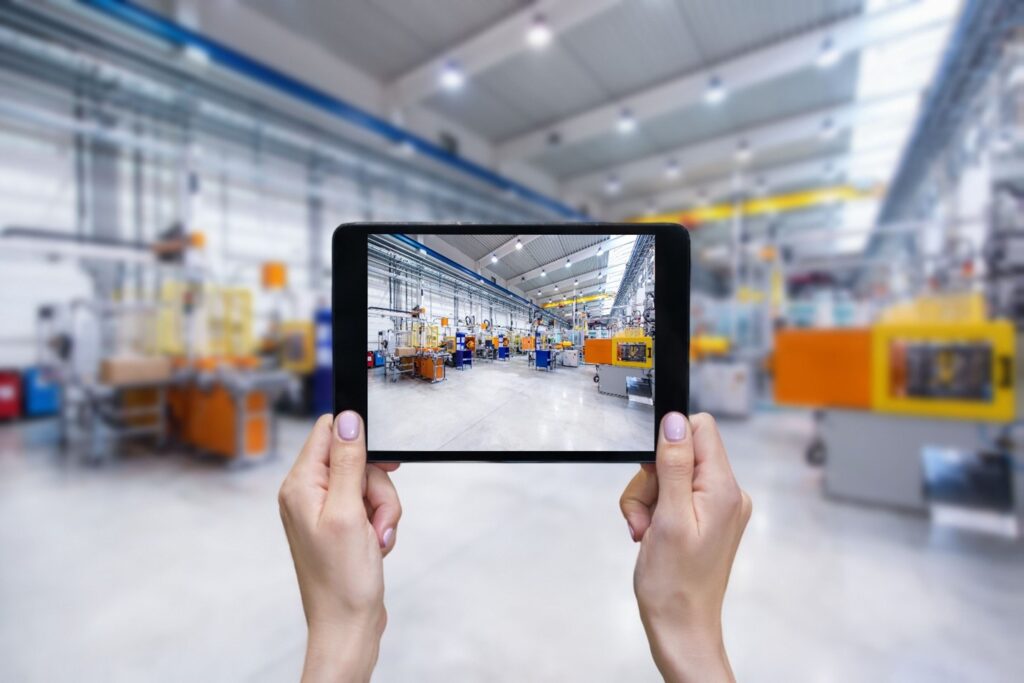
What is the advantage of using multiple BOMs?
Managing a single BOM has the advantage of creating one common data structure used across engineering and manufacturing, but this approach can also lead to compromises in data management.
Data is not optimized for the individual needs of various groups, which can slow down design, release, and change processes.
Companies producing standard, low-complexity machinery with minimal customization often use a single BOM approach due to its simplicity and efficiency.
A multiple BOM approach allows for optimized BOMs tailored to each department’s needs, enabling timely and efficient manufacturing changes.
Companies building complex, highly customized machines typically separate their engineering and manufacturing BOMs to accommodate the distinct needs of each discipline.
In this approach, data integration between the two BOM systems is critical and can be further supported through an integrated product lifecycle management (PLM) system.
What are examples of other useful BOMs that machine builders might employ?
There are many other BOM types, such as Concept BOM, As-planned, As-ordered, As-built / As-delivered, Service BOM, and As-maintained BOM to help companies with complex development and manufacturing processes manage the various stages of the product lifecycle.
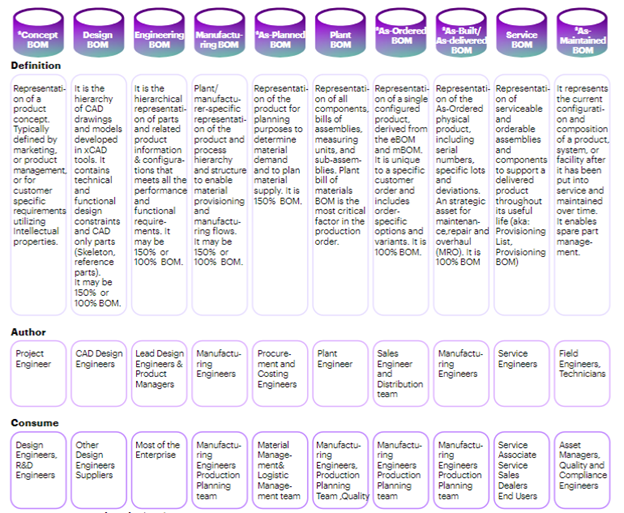
How do machine builders manage different product configurations within the BOM?
Buildable product configurations are typically managed by the EBOM system. The rules and constraints that define these configurations are mainly set in the product planning stages but also require input from design, manufacturing, supply chain, marketing, and sales.
This is why a common configuration management platform that spans the entire product lifecycle is key to succeeding: a digital thread backbone allows you to configure any artifact, including features, families and product lines, parts and modules, and system requirements and constraints to produce and validate buildable product combinations.
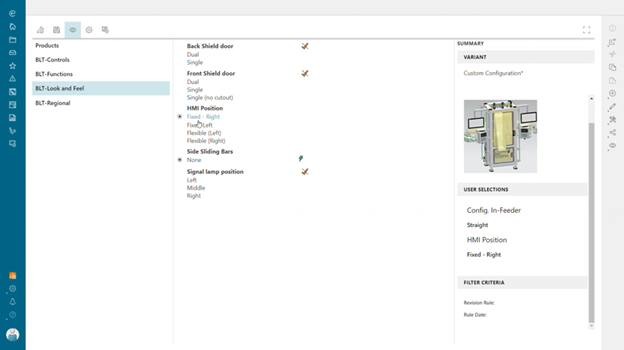
What are some ways you can improve process efficiency if you produce highly customized machines?
Engineering automation can be highly beneficial for companies that produce customizable machines. Creating a custom machine configuration requires significant manual effort.
Engineering automation tools can significantly reduce this effort through rule-based design automation and configuration management.
The key to accelerating design time is reuse. You can drive reuse by creating reusable libraries of standard components and by capturing organizational knowledge in engineering automation tools for consistency and efficiency.
With these reusable libraries established, you can automate quoting and proposal generation processes, which help you both quote more business and fulfill orders more effectively.
What are some common characteristics of companies that are most successful in deploying engineer-to-order (ETO) processes?
When evaluating companies that excel in ETO, two key attributes stand out.
First, a structured approach is essential to capture and analyze customer requirements early in the design phase. A PLM-based approach allows you to link your requirements, design variations, product BOM, documentation, and processes in an integrated data backbone.
This ensures that design variations are managed systematically while maintaining high standards of quality and meeting deadlines.
Second, successful machine builders optimize their manufacturing operations, including their supply chain, to accommodate variability. Again, a digital thread backbone helps you connect your BOM-driven configurations to the suppliers you rely on for part sourcing.
Maintaining flexible production capabilities helps you efficiently adapt to diverse configurations and specifications. Emphasizing modular designs and standardized components enhances reusability and reduces lead times for custom orders.
Integrating advanced planning and scheduling systems, aligned with PLM, plays a crucial role in optimizing resource allocation and sequencing production.
This comprehensive approach not only ensures timely deliveries but also minimizes costs associated with managing variability, thereby boosting customer satisfaction and market competitiveness.
What are some of the biggest challenges machine builders face when it comes to managing their BOM, and what are some potential solutions?
One of most common issues is simply maintaining an accurate record as data moves through the product lifecycle.
Data is coming in from all parts of the organization, from product planners assigning requirements, to mechanical, E/E, and software teams designing and engineering the machine components.
Data needs to be accessible and up-to-date for all stakeholders, including downstream manufacturing and maintenance operations.
Especially when BOMs are authored in Excel or within separate, siloed systems, manual efforts are required to translate and maintain data consistency between teams. Release processes can be time-consuming and costly, as can managing change. Traceability is challenging, and it’s easy to see human error creep in.
Another big issue is the difficulty for engineering to assess the impact of changes on manufacturing. The handoff and release of parts from engineering to manufacturing often require extensive manual coordination.
Usually, we see teams pulling together information from multiple different systems to determine the impact of releasing a part. Without integrated systems, it’s difficult to determine the impact the release of a part will have on products in production, the impact on cost, or the effect on inventory you might have in your production plants.
One of the most common solutions to overcoming these challenges is to establish a digital thread backbone in a PLM system like Teamcenter, which enables you to drive information from the EBOM and MBOM.
We’ve built powerful automation tools that allow customers to automatically align the DBOM to the EBOM and MBOM, eliminate the manual coordination between these disciplines and allow you to understand exactly how a released part will impact your downstream processes.
As a final takeaway, what’s your advice to companies that want to improve their overall development processes and bring their machines to market faster?
The leaders in machine building have already made strong investments in digitalization technology and systems.
They see the value in digital twins. But the challenge often seems to be in the coordination between these different systems. That’s where you see a lot of manual effort and redundant synchronization work that slows down the overall development process.
I see an opportunity to maximize your technology investments by bringing together these siloed systems. An enterprise BOM can integrate all the pieces of the product lifecycle, connecting users to a unified product definition across domains.
Establishing an enterprise BOM gives you more control over configuration and change processes, enhances multi-domain collaboration, and provides the traceability needed to empower better decision-making.
Siemens has extensive expertise and leading technology to support your enterprise BOM vision. Siemens Xcelerator open digital platform helps machine builders realize comprehensive digital twins, supported by Teamcenter’s enterprise BOM solutions.
To explore enterprise BOM management with Siemens, click here: https://www.sw.siemens.com/en-US/solutions/bom-management/
Tim Yerby currently serves as the Director of Industrial Machinery Solutions at Siemens Digital Industries Software. With over 20 years of experience in engineering, product, and marketing management and a background spanning multiple industries and disciplines, Tim specializes in core-to-value creation through innovation, particularly in areas of new products and services to fill as yet undefined and unmet customer or consumer needs. Tim holds a BS in Mechanical Engineering from Louisiana Tech University and an MBA from DePaul University with a concentration in Marketing. He is also certified as a Lean Six Sigma Black Belt.