Machine design and simulation are merging: See how it’s done
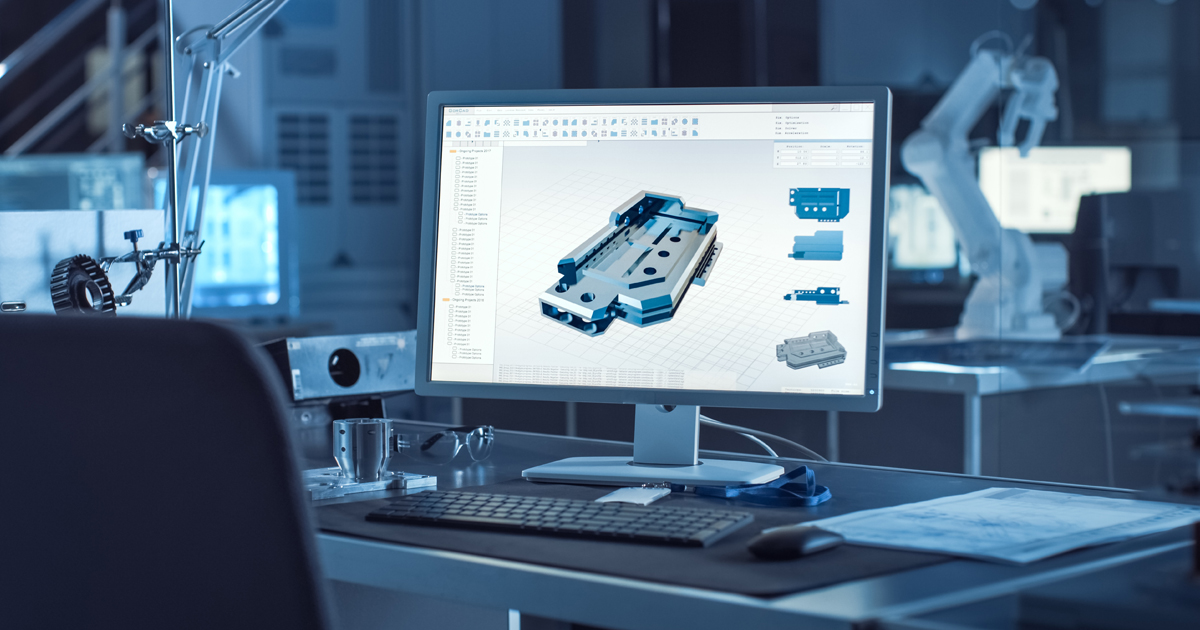
Manufacturers continuously push for more productive and efficient machines. Their customers want smarter, more flexible machines capable of meeting changing market demands.
To meet those needs, machine builders need to use the right digital tools to design, build and commission increasingly complex machines. These digital tools accelerate engineering processes, improve collaboration and optimize designs more quickly and efficiently.
Integrated design and simulation is one of these tools. It merges machine design and simulation software by managing analysis data and test data in a single simulation environment with design data.
This article features three short videos that highlight different features of integrated design and simulation. In these videos, you will see how to:
- Perform the setup of a machine assembly for dynamic modal analysis and turn those results into actionable design improvements.
- Use simulation to visualize the movements of an electromechanical actuator and ensure correct sizing.
- Complete an acoustics analysis of an industrial machine to identify the generated noise level and locate the critical noise level for the operator.
Watch the videos and learn how machine builders are using integrated design and simulation to innovate the next generation of industrial machinery.
Ensure machine performance, product quality with an integrated simulation environment
This first video shows a dynamic modal analysis for a milling machine. Using machine simulation software, a user determines the natural frequency of the machine at different operational points to rule out resonant changes.
This needs to be done because successful milling machines must avoid certain resonances throughout their operation. Resonances can negatively influence machine operation.
After verifying the quality of the simulation model, the user can easily make design changes to the machine because of a seamless connection between CAD and CAE environments.
This video shows how quickly and easily machine design engineers can compute and analyze different operational states for their machine and make necessary design changes to optimize operations for productivity, efficiency, reliability and more.
Reduce design cycles with system simulation
The goal of every design phase is to improve on the previous version. Whether design engineers are making a machine more productive, less expensive to build or a combination of this and other factors, it can be a lengthy process.
In this second video, a user wants to replace a pneumatic actuator with an electrical equivalent because eliminating a pneumatic supply system would mean significant cost savings. Watch how system simulation simplifies and accelerates the process by reducing the need for multiple design and prototype iterations.
The user begins by selecting the proper electrical and mechanical components from an extensive library to describe the actuator needed to open the tool changer door. The user then parameterizes the system model according to the requirements and visualizes how the new part will work.
This video highlights how validating early and verifying upfront in the product development process ensures selected components will meet operative performance and functional requirements.
Verify regulatory compliance using acoustic simulation
Every machine and component must meet customer, regulatory and safety requirements. This includes limits on noise. Simulation gives design engineers an idea of how much noise a single machine or component will produce.
The third video shows users how to create an acoustic simulation to determine the noise intensity of a milling machine and verify how effective a proposed encapsulation structure would be.
The user begins by determining the level of sound produced by the milling machine with and without proposed protection walls. The user then generates plots for acoustic pressure and verifies the performance of the acoustic shield.
Simulation reduces the need for expensive acoustic physical tests while still achieving safety standards. It also significantly lowers the overall product development costs. Engineers can identify problems faster and begin to troubleshoot any issues as soon as they have a better understanding of the acoustic behavior of the industrial machines they’re building.
Integrated design and simulation accelerates industrial machine design
Machine builders need a balanced multi-physics engineering solution to optimize the increasing complexity of industrial machines. Integrated simulation and testing solutions empower machine builders to deliver next-generation machine designs with higher throughputs and optimized controls logic to reduce vibrations and energy consumption.
By bringing design and simulation closer together, machine builders get shorter development times and lower their risk of poor design choices. Simulating complete machine operation early in the design process helps engineers increase machine productivity and improve reliability.
Learn more about integrated design and simulation and other advanced machine engineering solutions here.
To see how integrated design and simulation works and experience it for yourself, start a free 30-day trial.