How to reduce manufacturing costs? Start with the product
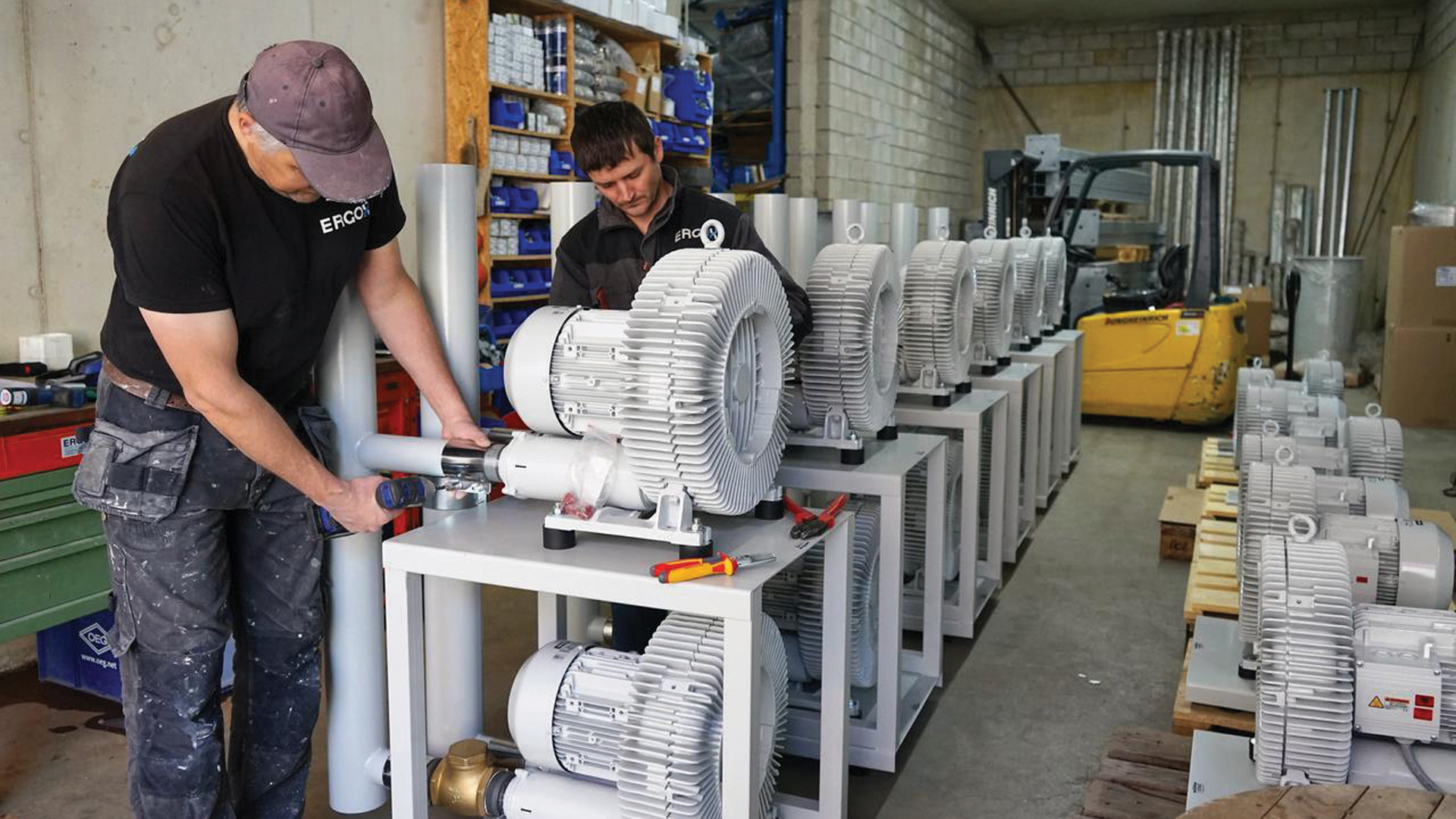
Industrial machines are only getting more connected, and demand for smart components rises. Supply chains have become more complex as they balance on a tightrope of uncertainty. These are just a handful of the challenges making it harder to reduce manufacturing costs, control product costs and grow a business.
How can component manufacturers navigate the product and process complexity labyrinth and come out on the other end with an innovative, carbon-compliant product that doesn’t break the bank?
Accelerated Product Introduction digital solutions helps component manufacturers keep costs and carbon footprint top-of-mind, so they can reduce manufacturing costs and build more profitable machine components their customers need.
Get a quick overview of how component manufacturers can build for profit in this infographic:
Adopt a new thought process for new product introduction (NPI)
It begins with reframing your NPI process. Eighty percent of the product cost and CO2e footprint are determined during the design stage. This means you need to answer questions like: “What material and what supplier can offer the best performance at the best price?” and “How will those different materials impact my sustainability goals?”
To answer these questions, component manufacturers need a software solution capable of exchanging cost and carbon information between departments and among suppliers.
Teamcenter Product Cost Management from Siemens does exactly this.
Teamcenter Product Cost Management as part of the Accelerated Product Introduction approach to NPI
Teamcenter Product Cost Management leverages the digital twin to support the ongoing evolution of the costing and carbon footprint calculations associated with product development and the processes that go with it.
This means designers, engineers and purchasers can quickly and easily swap different configurations in and out to identify factors affecting costs and emissions throughout its entire lifecycle.
Overall, Teamcenter Product Cost Management provides a centralized, enterprise-wide platform for creating and managing calculations. It captures internal costing expertise in a central location. Additionally, Teamcenter Product Cost Management holds BOMs and projects.
Teamcenter Product Cost Management wins in the details
How do these high-level benefits translate into reduced manufacturing costs? Component manufacturers know they need cost transparency early in the product lifecycle, but how?
A solution like Teamcenter Product Cost Management integrates market requirements and cost information all the way down to the labor and material levels. That way, component manufacturers can achieve an optimized request-for-quotation process.
Product-emissions data can be mapped to a minute level into the institutional GHG Protocol classifications of Scopes 1, 2 and 3. With this level of cost and carbon transparency so early in the product lifecycle, engineers now have time to explore new innovations.
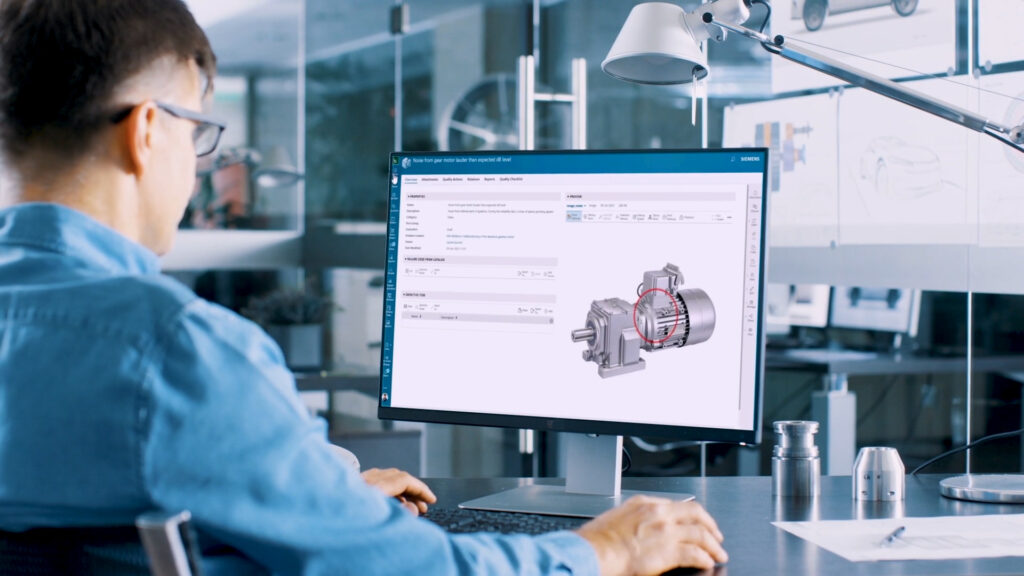
External communication and negotiation with suppliers is also possible with Teamcenter Product Cost Management. Cost and value engineering experts have the knowledge they need to bring evidence-based arguments to create transparent, trustful partnerships between the company and its suppliers.
When it comes to carbon footprint, manufacturers can’t rely solely on their suppliers to provide CO2e emission details. Thankfully, these digital tools allow users to generate the level of transparency necessary internally to find an accurate CO2e baseline. This transparency can also help to incentivize suppliers to seek more carbon-conscious production methods.
By the numbers: How Teamcenter Product Cost Management can reduce manufacturing cost
The optimized visibility, traceability and collaboration throughout the product lifecycle can create up to 16% savings in calculated parts. It can reduce up to 30% in preliminary carbon footprint calculations and up to 50% reduction in the time it takes to answer customers.
With the extra time and resources, engineers can focus on designing the next innovative, sustainable and profitable component their customers will need. Improve your product development process today.
Frequently asked questions about how to reduce manufacturing costs
Q: What specific software tools and technologies are recommended for integrating cost and carbon information between departments and suppliers?
A: For integrating cost and carbon information between departments and suppliers, specific software tools like Product Lifecycle Management (PLM) systems, Enterprise Resource Planning (ERP) systems, and specialized sustainability assessment tools are recommended. These tools enable seamless data sharing and analysis across the supply chain.
Q: How can small and medium-sized manufacturers effectively implement these cost-reduction strategies given their limited resources compared to larger companies?
A: Small and medium-sized manufacturers can implement these cost-reduction strategies by leveraging cloud-based solutions, focusing on incremental improvements, and seeking partnerships or government grants to offset initial costs.
Q: Are there any industry-specific considerations or adaptations needed when applying these cost and carbon reduction strategies in different manufacturing sectors, such as automotive or electronics?
A: Industry-specific considerations are essential when applying these strategies. For instance, the automotive sector may focus more on lightweight materials and fuel efficiency, while the electronics industry might prioritize energy-efficient components and waste reduction during manufacturing. Adapting these strategies to fit the unique requirements and regulatory standards of each sector ensures more effective implementation and greater cost savings.