Accenture and Siemens: Tackling industrial machinery challenges through Intelligent Service and Asset Lifecycle (ISAL)
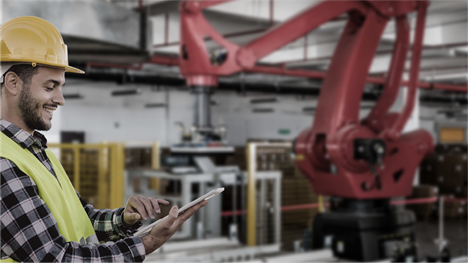
This blog article was co-written by Till Habel, Torsten Beste and Christopher Pennington.
The industrial machinery industry is being transformed by global supply chain disruptions, changes to equipment practices and a push for greater sustainability. Executives seeking to adapt to the shifting landscape need reliable partners and world-class solutions.
This trend is especially prevalent in fast-expanding areas, such as the production of battery manufacturing machines. Battery producers are building new gigafactories at an unprecedented rate – but often lack a skilled maintenance organization. This creates an opportunity for the machine builder to step in with a service to maintain the machinery that it provides, growing their business and fulfilling an essential role for the machine operator.
Accenture and Siemens can partner with industrial machinery manufacturers to help manage this period of transformation. This post discusses trends in the sector, the Intelligent Service and Asset Lifecycle (ISAL) solution and the role Accenture and Siemens play to support a new direction for industrial machinery companies.
Current industrial machinery trends
Supply chain disruptions resulting from global events (e.g., the COVID-19 pandemic and war in Ukraine) remain a challenge for the industrial machinery sector. These disruptions make it difficult to rely on material and component suppliers, causing issues ranging from forecasting and meeting production targets to hitting deadlines and sourcing equipment parts.
The industry is also seeing a shift toward an equipment-as-a-service (EaaS) model. For industrial machinery operators, keeping assets working efficiently and maintaining high output is more important than ever. More companies have adopted this approach, which transfers the burden of equipment upkeep and maintenance — and even factory output levels and other performance outcomes — to the service provider.
In light of the shift to EaaS, it’s increasingly important for industrial machinery companies to reduce failures and extend the lifespan of their machines. Minimizing failures not only allows these companies to lower materials and service costs, it also allows them to achieve the key sustainability goal of reducing their carbon footprint by lowering the frequency of field service calls. This point is especially critical, given the high priority the industry has placed on sustainability. Managing energy consumption and tracking sustainability data is vital as companies aim for improved efficiency throughout the entire product lifecycle and strive for a circular economy.
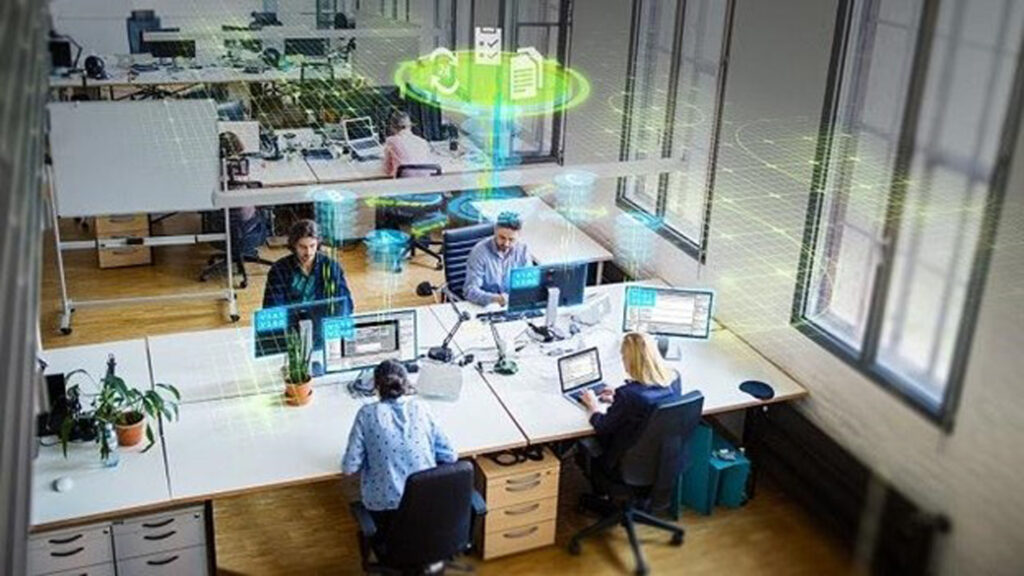
Intelligent Service and Asset Lifecycle (ISAL) for industrial machinery
Digital solutions from Siemens can help companies improve overall equipment effectiveness (OEE) and address these challenges. Siemens Xcelerator uses a closed-loop digital thread to connect every aspect of the product lifecycle. This provides the traceability and real-time, cross-domain data sharing vital to those efforts.
The visibility these solutions provide contrasts sharply with the siloed approach industrial machinery companies have traditionally operated within their functions along the lifecycle. Given the factors driving change in the sector, these companies need to transform their approaches to remain competitive. Siemens’ ISAL solution breaks down barriers between domains and provides a single source of truth for every stakeholder. Any product changes are propagated to downstream functions, such as service through a managed process, through Siemens’ Product Lifecycle Management (PLM) software, ensuring more effective coordination of work and reduction in overall lifetime costs.
With ISAL in place, companies striving for maximum machine uptime gain important advantages. Service technicians can better assess an asset’s health and maintain it more effectively because ISAL provides real-time insights into customers’ machines, including machine configurations and service history. In addition to making more efficient use of the technicians’ time, this approach reduces equipment downtime and increases output, critical steps to meeting the terms of increasingly common performance-based contracts. These insights also allow manufacturers to evaluate their needs for parts more accurately and source those parts more efficiently to overcome persistent supply chain problems.
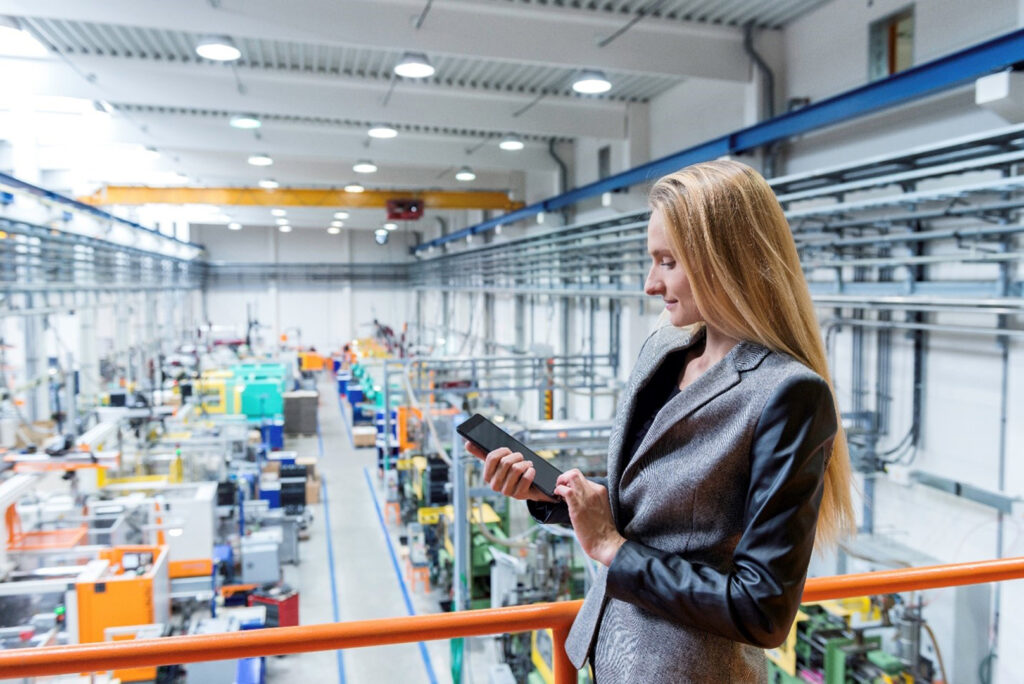
Benefits of Intelligent Service and Asset Lifecycle (ISAL)
ISAL enables industrial machinery manufacturers to keep their operational service costs low and fix equipment problems as efficiently as possible. But it also allows manufacturers to go a step further. With ISAL, companies can gather and analyze data on how the product is used, how and when it has failed in the past and more. This operational data was previously hidden, leaving companies to respond to failures after the fact. Now, they can use the data, along with artificial intelligence and machine learning, to predict failures, improve service planning and work proactively to address potential problems before they occur.
The predictive maintenance and service lifecycle management capabilities of Siemens Xcelerator and Mindsphere allow companies to reduce their risk of costly machine failures, extend equipment lifespans, and improve first-time fix rates. These improvements further minimize equipment downtime and increase productivity. ISAL allows manufacturers to more easily establish a closed-loop continuous improvement process to make their products better as time goes on.
Data related to machine maintenance is not the only actionable data Siemens’ solutions produce. They also provide key information on the sustainability of a company’s production efforts. Stakeholders can gather and analyze data on fuel consumption and the supply chain’s environmental impact, which gives the company a clear sense of how its operation helps or hinders its pursuit of sustainability goals.
What role do Accenture and Siemens play?
ISAL can provide significant advantages to industrial machinery companies, but only if it’s effectively implemented. Companies need a reliable partner in the transformation process – one that understands both the solutions in question and the industrial machinery sector itself. Accenture, an expert in digital transformation, can be that partner, and it has joined with Siemens to provide the solution integration companies will require to get the most out of their transformation.
Accenture can assess a company’s situation and existing digital maturity, and they can work with the company’s team to define a strategy tailored to their goals. Accenture leverages its expertise in data analytics and system integration to guide the transformation process in consultation with the companies it serves. And because of Accenture’s considerable experience in software implementation, it can also integrate new solutions with existing enterprise resource planning and customer relationship management solutions.
Siemens and Accenture work together throughout the transformation journey to deliver the advantages Siemens’ solutions provide. Siemens offers out-of-the-box solutions built on its profound knowledge of engineering and product development in the industrial machinery sector. Its partnership with a well-established solution integration expert like Accenture means industrial machinery companies can have confidence their digital transformations will yield meaningful results.
Conclusion
Disruptions to the global supply chain, the growing importance of sustainability, and the rise of EaaS models are leading industrial machinery companies to transform their approaches to managing the product lifecycle.
With ISAL, companies can effectively respond to each of these trends. They can start by improving their service processes with condition monitoring and remote services. Then, they can extend those services to include digital tools and connectivity support for field technicians who can more efficiently schedule maintenance jobs, manage spare parts planning and provide remote support to clients. Further, companies can enable field technicians to sell value-added services and products through integrated service and asset knowledge management.
ISAL allows executives to improve maintenance and operation forecasts and gain clear insight into key sustainability metrics by collecting reams of real-time data. The data collected through Siemens’ solutions is critical for companies who want to maximize the efficiency of their operations, but it also allows industrial machinery manufacturers to meet the performance outcomes stipulated by most EaaS contracts.
Through their partnership, Siemens and Accenture can provide and implement the solutions industrial machinery companies need to keep up as their sector undergoes significant change.
For more information, visit siemens.com/SLA
About the authors:
Till Habel is the Managing Director Supply Chain & Operations at Accenture Strategy.
Torsten Beste is the Global VP Intelligent Service & Asset Lifecycle Management at Siemens Digital Industries Software.
Christopher Pennington is the Marketing Manager Industrial Machinery at Siemens Digital Industries Software.