7 key benefits heavy equipment manufacturers can gain from embracing model based systems engineering
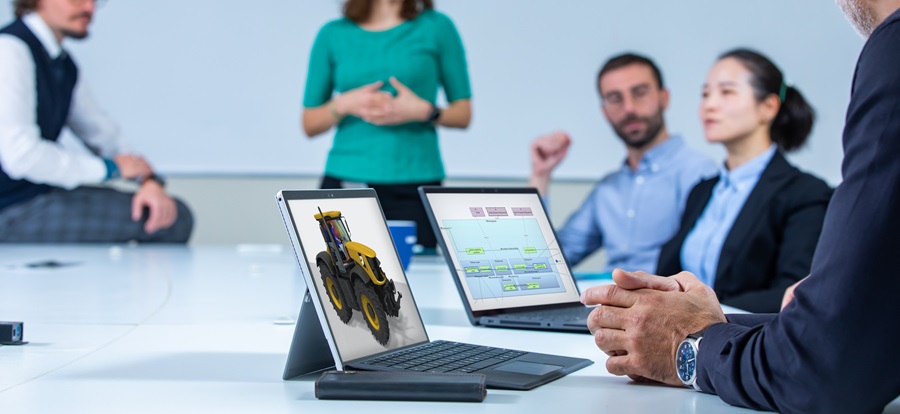
Most people think of heavy equipment as huge machines that operate in dark, foggy industrial areas, delivering gigantic power, driven by energy-grinding diesel engines. The industry’s image is anything but green and clean. Quite unfair. The efforts OEMs make every day in terms of efficiency and sustainability are enormous to reduce the environmental footprint of the machines that help produce our food, pave our roads, and mine the commodities that we use every day.
Evolutions in the global society, including changing customer demands and ever stricter regulations, are leading to an industry transformation. Digitization, electrification, connectivity, automation, and sustainable initiatives are no longer just buzzwords. Today’s OEMs make different products, and sell them differently, through a variety of business approaches. These changes are reshaping the industry landscape, leading to improved efficiency, sustainability, and customer value while driving innovation and new business opportunities.
The impact on heavy equipment product design and development is huge.
Almost every heavy equipment subsystem built today includes mechanical, electrical & electronics, and software components. Manufacturers must adapt their skills in new areas that are often far from their longtime legacy and core competences. And they must fit those new disciplines within established, often rigid, processes that have been around for decades. That is not a walk in the park. On average, OEMs currently spend about half of their development time and resources on fixing integration problems – combining input from different internal teams and their supply chain.
To prevent complex design problems from derailing, OEMs must integrate multiple disciplines earlier, preferably starting from the concept stage. Only by taking control from the beginning, considering all aspects simultaneously, systematically cascading down top-level requirements to domain targets and continuously verifying the overall impact of all decisions, manufacturers can remain successful delivering increasingly innovative products.
Embracing model-based systems engineering (MBSE) is the way forward
It’s the only methodology that will let them do all the above with the required efficiency and scale, both today and in the future. Implementing this methodology into current development processes is however not something companies can do overnight as it requires them to make changes at the core of their activities. But every step forward is a step they gain and will bring immediate benefits.
Here are some of the benefits that heavy equipment manufacturers can attain from an MBSE approach:
1. Enhanced system understanding: MBSE provides a holistic approach to system development by capturing and representing the complex interdependencies and interactions between all components. This enables a comprehensive understanding of the heavy equipment system in all its aspects, including mechanics, E/E systems, software, and controls. Increased system understanding leads to better-informed design decisions and ensures that all requirements are correctly captured and considered.
2. Faster multidisciplinary optimization: Complex systems often require numerous iterations during design and development. MBSE eliminates this iteration effort, as changes in one aspect of the system are automatically propagated across all disciplines. This allows manufacturers to quickly identify and resolve design conflicts and issues. It accelerates the design process, improves collaboration, and facilitates rapid system optimization.
3. Early detection of design issues: By using MBSE, OEMs can simulate and analyze multidisciplinary system behavior and functional safety virtually before physical prototyping. This capability enables early detection and mitigation of design issues, reducing the time and cost associated with fixing errors during later stages of the development cycle. MBSE helps identify potential problems, such as functional conflicts, interface issues, safety issues, and performance bottlenecks, which reduces the risk for quality issues and enables proactive design improvements.
4. Improved communication and collaboration: Successfully designing innovative heavy equipment relies on effective collaboration. MBSE provides a common platform and language for communication, allowing multidisciplinary teams, including those from suppliers, to collaborate more efficiently and effectively. By using standardized system models and notations, stakeholders across domains can understand each other’s perspectives, reducing misinterpretations and fostering better communication.
5. Continuous requirements management and traceability: MBSE enables requirements to be captured and directly linked to system models, providing comprehensive coverage and traceability throughout the product lifecycle. MBSE also ensures that the link between work-in-progress and released data is completely understood during all stages and that the correlation between the digital representation of the product and the real product is complete and meaningful. This improves regulatory compliance, enhances configuration management, and facilitates better analysis and smoother implementation of change requests.
6. Preparation for more reliability, availability, maintainability, and serviceability (RAMS): After the equipment is delivered, effective lifecycle management and maintenance become critical. MBSE provides a foundation for the creation of digital twins, which are virtual models representing the physical assets. Through the integration of real-time data and analytics, model based systems engineering enables predictive maintenance, continued performance optimization, and troubleshooting, reducing downtime and ultimately total cost of ownership.
7. Increased efficiency across programs. MBSE promotes standardization and knowledge and data sharing throughout the enterprise, which presents benefits that go beyond individual development programs. By making model-based descriptions of systems and subsystems available for all product groups, manufacturers will drive reuse across programs. This results in cost advantages when working with suppliers and improves overall efficiency. It will also help manufacturers better plan their resources and achieve the level of agility that is required to keep up with today’s rapid pace of innovation.
How and where to start MBSE with heavy equipment
The above-mentioned benefits OEMs can enjoy from an model based systems engineering approach are clear and well-known. Everyone in the industry realizes that there is no other choice than to jump on the bandwagon. The key question is how and where to start? It’s the question I’ve heard most over the past 25 years, working with many customers around the globe.
The answer to that question is very individual as all customers are unique in the way they define their business objectives and set their strategic priorities. The most successful cases I have witnessed always started with a maturity assessment in collaboration with a dedicated and experienced partner, followed by jointly defining and implementing their unique digital road map. This approach addresses their most pressing challenges and aligns their strategy for maximum benefits.
Additional heavy equipment model based systems engineering resources
Video: Integrated multi-domain systems engineering solution
Ebook: Cut development lead times by eliminating system integration challenges
To see how Siemens helps heavy equipment OEMs start and progress their own MSBE journey, check out this resource page Model-based Systems Engineering for Heavy Equipment.