Assurer la sécurité de la mobilité hydrogène
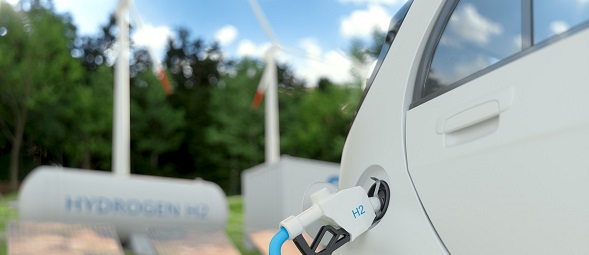
Batterie ou pile à hydrogène ?
L'électrification de la mobilité n'est pas une tendance. C'est un fait. La plupart des équipementiers planifient déjà le retrait de leurs flottes de moteurs à combustion. Mais à l'électrification, nous associons généralement les batteries Li-ion et de nombreux défis inhérents. Les matériaux rares, l'anxiété liée à l'autonomie, le manque de stations de recharge, la sécurité des batteries et les faibles possibilités de recyclage en sont quelques-uns. Bien que des recherches approfondies soient menées pour résoudre ces problèmes, une alternative est envisagée : les véhicules à pile à hydrogène. Dans cet article, nous expliquons comment la simulation peut aider les équipementiers & fournisseurs à concevoir virtuellement et à certifier l'enceinte sous pression en matériau composite utilisée pour le stockage de l'hydrogène.
L'hydrogène : la source d'énergie miracle pour l'avenir de la mobilité ?
L'hydrogène est l'un des atomes les plus courants sur terre et constitue une ressource illimitée ; l'autonomie d'un véhicule à hydrogène est souvent supérieure à celle des véhicules électriques à batterie ; une pile à combustible à hydrogène n'émet que de la vapeur d'eau ; et un réservoir d'hydrogène peut être rempli en quelques minutes. Nous considérons donc les piles à combustible comme une alternative de plus en plus sérieuse aux batteries.
Dans l'industrie automobile, la Toyota Mirai et la Hyundai Nexo ont été des précurseurs. BMW est sur le point de lancer son iHydrogen NEXT, tandis que Daimler Truck AG et Volvo ont créé une coentreprise en 2021 "pour accélérer l'utilisation des piles à combustible à base d'hydrogène". Un nombre croissant de start-up spécialisées dans la mobilité misent également sur l'hydrogène. Dans l'aéronautique, Airbus a lancé en 2020 un programme ZEROe visant à développer des avions commerciaux à hydrogène d'ici 2035. Des leaders de l'industrie ferroviaire comme Siemens développent également des trains à hydrogène.
Cette tendance a conduit de nombreux gouvernements à financer la recherche pour développer la mobilité par l'hydrogène. Un exemple récent est celui de la France, qui a annoncé en 2020 que "7 milliards d'euros seront utilisés comme financement pour faire de la France un fer de lance de l'hydrogène vert d'ici 2030".
Cela semble prometteur... alors pourquoi seulement "27.500 véhicules à pile à hydrogène avaient été vendus à la fin de l'année 2020 depuis le début de leurs ventes ?
Quelques défis technologiques à relever...
Malheureusement, il n'y a pas encore de miracle. Nous avons besoin d'une grande quantité d'hydrogène pour produire chaque kilowattheure, ce qui entraîne deux défis technologiques limitant l'expansion de l'hydrogène.
- La production d'hydrogène se faisait généralement par le biais d'une réaction chimique (SMR) à partir de méthane et d'eau pour produire de l'hydrogène... et beaucoup de CO2 ! L'hydrogène est désormais produit de manière plus propre grâce à l'électrolyse, qui consiste à séparer l'eau en hydrogène et en oxygène... mais en utilisant de l'électricité !
- Le stockage de l'hydrogène doit se faire dans un petit volume pour être intégré dans le véhicule, dans un espace disponible restreint. Cela implique une pression très élevée, et les systèmes de stockage doivent évidemment être totalement sûrs en toutes circonstances.
Cela nécessiterait d'importants investissements dans les stations de recharge, et le coût d'une voiture à hydrogène est encore élevé. Pour toutes ces raisons, les piles à hydrogène sont encore en phase d'incubation en tant que technologie pour l'e-mobilité. Mais ce ne sont pas des obstacles insurmontables.
Stocker une grande quantité d'hydrogène dans les véhicules
Des technologies de réservoir compactes, sûres en toutes circonstances
Concentrons-nous ici sur le deuxième défi technique mentionné ci-dessus : le stockage en toute sécurité d'une grande quantité d'hydrogène, dans un petit volume, à bord d'un véhicule en mouvement. Les technologies de pointe pour relever ce défi sont des réservoirs d'hydrogène pressurisés à 700 bars ! De véritables bombes intégrées...

Un seul accident serait probablement fatal pour les passagers et les personnes environnantes. Et cela détruirait évidemment l'image de marque de l'hydrogène en tant que solution de mobilité future. Un tel accident s'est produit en 2019, non pas sur un véhicule mais dans une station de recharge, tuant deux personnes et détruisant tout autour. Si l'on considère ce qu'un véhicule en mouvement peut typiquement subir pendant sa durée de vie par rapport à une station de recharge stationnaire (accident, mauvaise utilisation, dizaines de milliers de charges et de décharges, températures extrêmes, sécheresse, humidité...), la sécurité est sans aucun doute un défi pour la conception de ces réservoirs.
les réservoirs 700 bars développés aujourd'hui se composent d'une membrane en polymère assurant l'étanchéité, entouré d'une grande épaisseur de composites en fibres de carbone continues à haute résistance permettant une performance mécanique très élevée du réservoir, et d'un bossage métallique avec une valve pour fermer le système et assurer son intégration dans le véhicule. Nous appelons cette technologie "Type IV", c'est-à-dire la quatrième génération de réservoirs pressurisés, ou "Composite Pressure Vessels".

Combien d'années et d'argent pour certifier un appareil à pression en matériaux composites ?
La nécessité absolue de garantir la sécurité des véhicules à hydrogène conduit à des marges de sécurité très élevées imposées par les normes mondiales. Le règlement technique mondial n° 13, l'une des principales références mondiales, impose par exemple une marge de sécurité de 225 % pour l'éclatement à température ambiante, ce qui signifie qu'un réservoir de 700 bars ne devrait jamais exploser avant 1575 bars. La variabilité conduit les fabricants à ajouter leur propre marge supplémentaire, jusqu'à 1700 ou 1800 bars. Cela permet de garantir la réussite des tests de certification et de vérifier, par des centaines de tests physiques coûteux et compliqués, l'intégrité de leur réservoir.
L'éclatement à température ambiante, le cyclage à des températures extrêmes, l'effet des dommages de surface, la résistance aux produits chimiques, les chutes sous différents angles et de différentes hauteurs, le fluage, le tir de balles et le feu ne sont que quelques-uns des tests imposés par les normes de sécurité. De nombreux fabricants de réservoirs effectuent certains de ces tests en interne de manière très itérative et supposent (ou espèrent...) que les autres tests seront tout à fait satisfaisants. Dans un marché concurrentiel et en pleine expansion, cette situation n'est plus acceptable. C'est là que la digitalisation entre en jeu.
Conception virtuelle et certification d'un appareil à pression composite
La complexité de la technologie de navire et la variété des tests de certification imposent de nouvelles méthodes que nous pouvons intégrer dans les solutions IAO, en visant une précision totale du jumeau numérique. Les solutions Simcenter intègrent les processus et les technologies pour découvrir la meilleure conception possible, qui sera aussi compacte, légère et bon marché que possible, qui sera capable de transporter la quantité d'hydrogène attendue tout en respectant toutes les réglementations, et qui permettra une certification virtuelle de la conception telle qu'elle est fabriquée, avant le prototypage.
Évolutivité des méthodes IAO
Ces méthodes d'IAO innovantes ne font pas partie des méthodes dites "standard". Ils doivent intégrer un grand nombre de principes physiques différents et ne sont parfois pas tout à fait au point dans l'industrie. Cependant, le nombre d'analystes IAO travaillant sur les certifications de réservoirs est, en général, assez faible, et les entreprises ne disposent pas d'une expertise dans tous les domaines. Les solutions Simcenter vont des méthodes simplifiées et automatisées permettant aux non-experts de déterminer plus rapidement les premiers concepts, aux méthodes avancées haut de gamme développées et évaluées dans le cadre de projets de recherche avec des clients industriels pour modéliser la complexité.
Conception préliminaire d'un réservoir d'hydrogène avec simulation : Évaluez des milliers de modèles en quelques heures
Avec Simcenter, un concepteur de réservoir commence généralement par une étude d'exploration de l'espace de conception très large qui aboutit à une ou plusieurs conceptions préliminaires. Au lieu des méthodes analytiques approximatives généralement utilisées, nous incorporons des flux de travail FEM automatisés dans un problème Simcenter Heeds. Un non-expert sera en mesure d'évaluer en quelques heures les performances de milliers de conceptions (avec différentes géométries de mandrin de gaine, géométries de bossage, matériaux, couches composites, stratégies d'enroulement filamentaire...) par rapport aux exigences de certification et de conception. Il peut ensuite déterminer les meilleurs candidats à l'adoption définitive. À ce stade, les simulations restent linéaires ou incluent une non-linéarité géométrique simple et il/elle peut utiliser des modèles simplifiés efficaces avec des lois de matériaux de base pour tous les composants. Le placement des fibres est pris en compte par l'automatisation de l'exécution de l'outiltiersintégré, comme décrit plus loin. Cela permet d'obtenir une précision bien supérieure à celle des méthodes analytiques, tout en conservant une efficacité très raisonnable.

L'équipe d'ingénierie de Simcenter (anciennement LMS Samtech) a travaillé sur le projet de recherche OSIRHYS IV. Ce projet visait à développer et à valider ces méthodes, qui ont permis de réduire la masse de 30 % par rapport aux navires conçus avec des méthodes analytiques, sans compromis sur les performances et la capacité.
L'importance de la simulation du processus de fabrication de bout en bout des appareils à pression en matériaux composites pour une certification virtuelle précise
Le processus de fabrication d'un appareil à pression composite aura un impact très important sur ses performances finales et sur la variabilité de ces performances. Lorsqu'ils sont négligés, les réservoirs peuvent même tomber en panne avant même que nous les utilisions pour la première fois. Les solutions Simcenter simulent avec précision le processus de fabrication de bout en bout afin d'évaluer a posteriori les performances du navire tel qu'il a été fabriqué.
À partir du rotomoulage...
La première étape est la production du revêtement en polymère, par un procédé de moulage par rotation. La géométrie finale et les propriétés mécaniques du revêtement dépendent fortement de ce processus. Un revêtement trop fin ou mal conçu se fissurera et créera des fuites dans le réservoir. En revanche, un revêtement surdimensionné réduirait la capacité du réservoir et augmenterait sa masse. Nous utilisons Simcenter STAR-CCM+ pour simuler le processus de moulage par rotation. Cela inclut le contrôle de la température, afin d'obtenir la géométrie et les propriétés mécaniques attendues du revêtement.
... à l'enroulement filamentaire...
Les fibres de carbone sont ensuite appliquées autour de la membrane dans une séquence prédéfinie d'orientations par enroulement filamentaire. Ce procédé fait appel à de grandes machines qui enroulent les fibres autour du revêtement. De nombreuses variables liées au contrôle du processus doivent être gérées et auront un impact très fort sur l'orientation locale et l'épaisseur de la coque composite [schéma 6], et donc sur les performances globales du réservoir. Simcenter 3D permet l'intégration de solutions verticales spécialisées de tiers pour simuler avec précision le processus d'enroulement filamentaire. Tous les paramètres de fabrication nécessaires sont alors disponibles via une interface graphique spécifique.

... et le durcissement
Le réservoir est ensuite durci, ce qui permet la polymérisation de l'enveloppe composite, mais peut affecter les performances du revêtement et induire des contraintes résiduelles dans l'assemblage. Pendant le durcissement, les différents matériaux qui composent le réservoir réagissent de manière très différente aux changements de température. Simcenter 3D intègre des solveurs thermiques et mécaniques et des méthodes qui prennent en compte l'historique du matériau pendant le processus de durcissement, déterminent les déformations induites par le processus et évaluent les effets des contraintes résiduelles sur les performances du produit.

Certification virtuelle des appareils à pression en matériaux composites : Modéliser la complexité, avec une précision totale
Vous pouvez utiliser Simcenter 3D, la plateforme Simcenter Mechanical, pour modéliser toute la complexité des tests de certification.
Les modèles d'endommagement des matériaux composites sont intégrés de manière native dans Simcenter 3D. Il permet de prévoir la réduction de la rigidité qui se produisent pendant la pressurisation et la dépressurisation. Il s'agit notamment de méthodes statiques et de fatigue innovantes pour les composites, développées et validées dans le cadre de projets industriels et applicables aux appareils à pression en matériaux composites.
Des modèles thermomécaniques sont disponibles pour évaluer l'effet de la température combinée à différents cas de charge mécanique. Des solveurs dynamiques transitoires sont utilisés pour calculer la résistance du réservoir soumis à des essais de chute standard. La résistance au feu a également été étudiée dans le cadre du projet de recherche FireComp. Enfin, Simcenter intègre la simulation multi-échelle pour tenir compte du comportement microscopique du matériau dans la simulation macroscopique. Cela permet d'accéder au niveau maximal de fidélité des modèles.
Cette liste n'est pas exhaustive. L'avantage d'une plateforme intégrée est que nous pouvons réaliser tous les cas de charge dans une seule plateforme. Un seul utilisateur peut avoir accès à tous les ICP dans le même environnement.

Les voies de la mobilité par l'hydrogène
Si la plupart des analystes prévoient que les véhicules électriques à batterie resteront en tête pour les petites voitures particulières, nous nous attendons à ce que la solution de l'hydrogène soit de plus en plus utilisée dans des véhicules plus grands comme les bus, les camions, les trains, les navires ou les chariots élévateurs à fourche. La raison en est qu'ils ne disposent pas de l'espace nécessaire pour les cuves sous pression et que les batteries Li-ion requises pour les alimenter seraient trop lourdes.
Les entreprises impliquées dans la production d'appareils à pression en matériaux composites pour le stockage de l'hydrogène doivent anticiper cette expansion. La concurrence sera rude. Les entreprises qui réussiront seront des précurseurs et non des suiveurs. Avec Simcenter, ils peuvent intégrer en toute confiance le jumeau numérique de leurs appareils à pression. L'équipe de Simcenter investit beaucoup dans la recherche. Nous travaillons avec des clients industriels comme Honda R&D Co, Ltd pour minimiser l'incertitude des prévisions et créer un véritable jumeau numérique. Cette collaboration permet de réduire et, espérons-le, d'éliminer un jour tous les essais physiques réalisés avant la certification, en les remplaçant par des simulations et des optimisations fiables, peu coûteuses et immédiates, toutes intégrées dans une plateforme de simulation.
Il est évident que la sécurité dépend également de la manière dont le bateau est intégré dans le véhicule et de l'endroit où il l'est. Il doit être protégé contre les scénarios d'accident typiques, sans influencer le poids du véhicule, les NVH ou le comportement dynamique. Pour vous aider à relever les défis propres au secteur de l'automobile, nous vous proposons un jumeau numérique intégré et précis pour les véhicules électriques. Mais c'est une autre histoire !