From plant to bottle: redefining bottling with agile manufacturing engineering
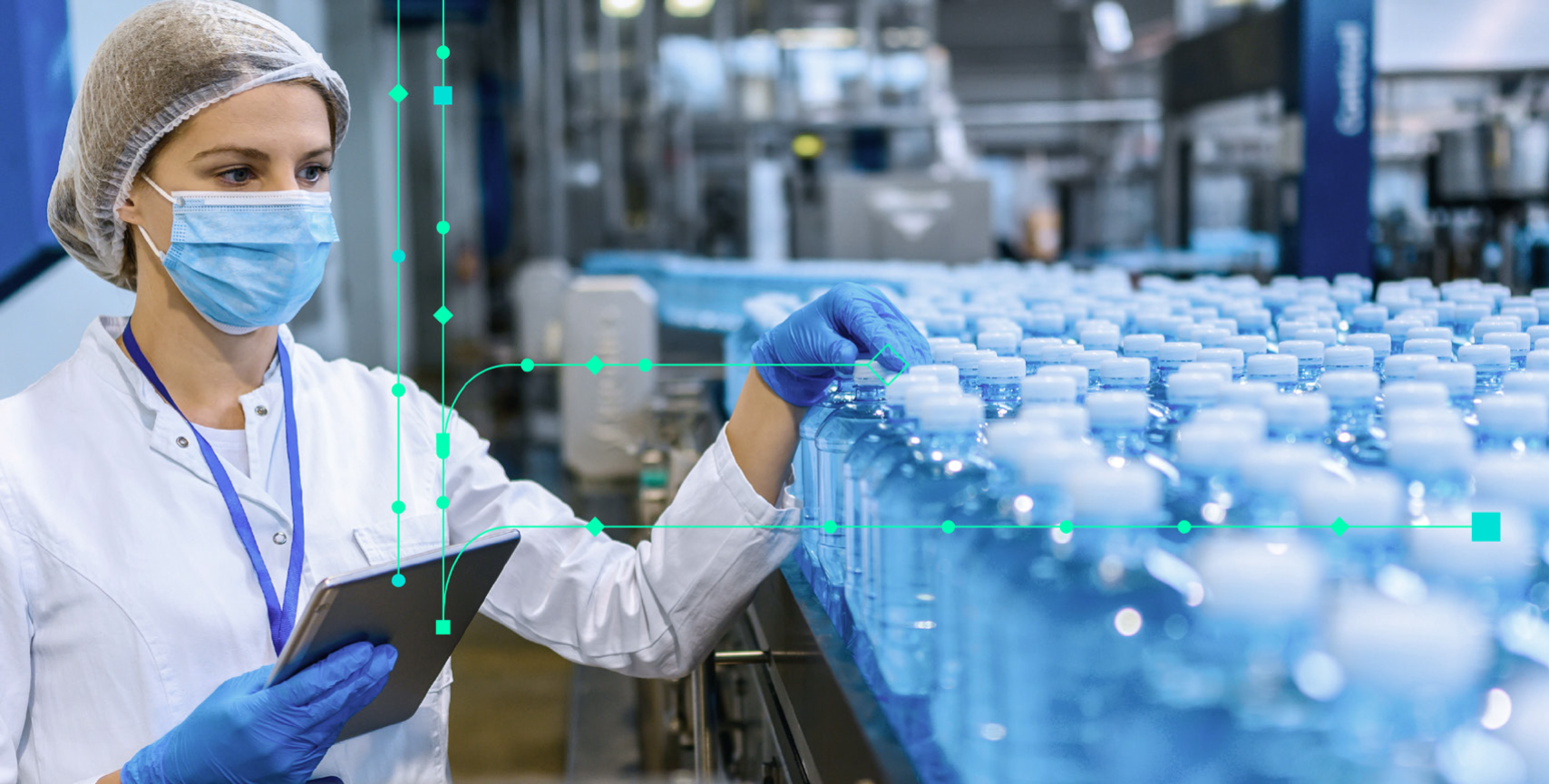
In the fast-paced world of bottling, where adaptability, speed, and quality are paramount, agile manufacturing in bottling is reshaping operations. By focusing on manufacturing process planning and line automation engineering, bottlers can streamline workflows, achieve standardization, and meet evolving market demands with confidence.
This blog explores how agile manufacturing engineering addresses the unique challenges faced by operations managers, plant managers, and other key stakeholders in the bottling industry.
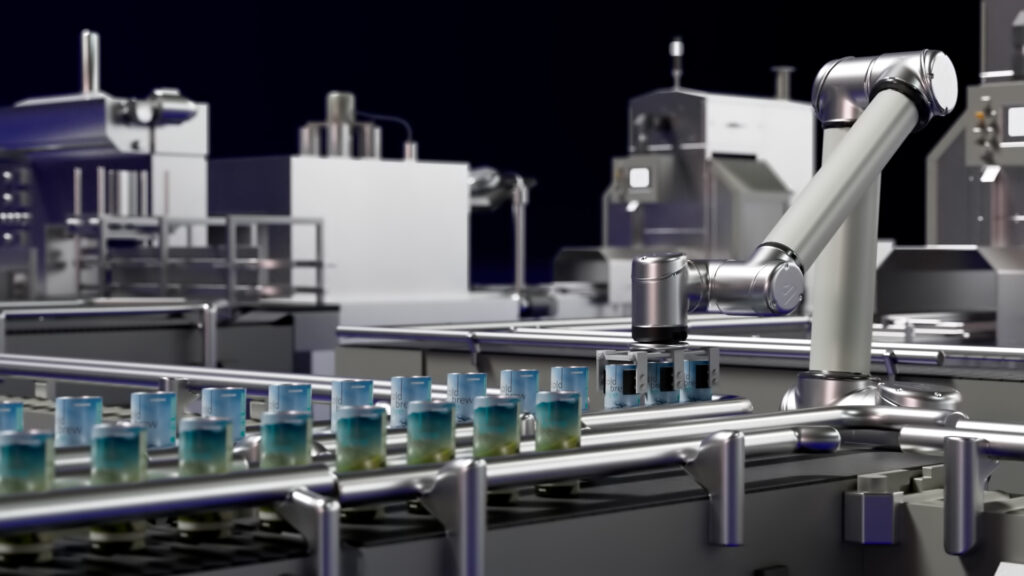
Building resilience with agile manufacturing in bottling
Bottling lines are the lifeline of production facilities. From material handling to final packaging, manufacturing process planning ensures every phase is optimized for efficiency and flexibility. Leveraging advanced tools and technologies, bottlers can design workflows that are both scalable and adaptable.
Key benefits of manufacturing process planning
- Streamlined product changeovers
Frequent product updates, such as seasonal beverages or new packaging formats, can challenge bottling workflows. Agile manufacturing engineering leverages digital tools to simulate and validate production changes before implementation. This approach minimizes disruption, reduces downtime, and ensures smooth transitions between product runs. - Optimized material flow
Production bottlenecks and waste are common challenges in bottling. Agile manufacturing allows bottlers to simulate production scenarios, helping them identify inefficiencies and refine processes for consistent throughput. - Enhanced scalability and adaptability
Demand fluctuations can put pressure on bottlers to adjust production rapidly. Agile manufacturing equips bottlers to scale operations up or down without compromising quality, enabling swift responses to market demands.
Discover more about how advanced robotic technology is transforming bottling with this comprehensive white paper.
Standardization in automation: Ensuring quality at scale
As bottling facilities expand globally, maintaining consistent quality becomes a critical challenge. Standardization in automation provides a foundation for reliable and efficient operations by unifying processes across all sites.
The value of standardized automation
- Uniform Quality Across Sites
Standardized automation ensures products meet identical quality standards globally, critical for protecting brand reputation. - Simplified Maintenance
With uniform automation systems, Maintenance Managers can streamline upkeep processes, minimizing downtime and focusing on long-term improvements. - Scalability for Growth
Modular automation systems enable bottlers to add new production lines or scale operations without major overhauls, ensuring seamless expansion.
Integrating agile manufacturing engineering for bottling excellence
Agile manufacturing engineering is about more than technology—it’s about fostering a culture of continuous improvement. By adopting agile practices, bottlers can future-proof their operations and meet evolving consumer demands with ease.
Best practices for agile bottling operations
- Leverage Digital Twins
Real-time virtual replicas of production lines enable predictive maintenance, workflow optimization, and faster decision-making. Discover the role of digital twins in revolutionizing food and beverage manufacturing. - Enable Data-Driven Decision Making
IoT sensors embedded in production lines deliver actionable insights, helping Continuous Improvement Managers pinpoint inefficiencies and refine operations for greater productivity. - Foster Cross-Team Collaboration
Agile frameworks align goals across teams—from production managers to logistics managers—ensuring streamlined processes and enhanced productivity.
Transforming the future of bottling with agile manufacturing
Agile manufacturing in bottling, powered by manufacturing process planning and standardized automation, is transforming the industry. By implementing these strategies, bottlers can adapt to market demands, improve production efficiency, and maintain consistent quality across all facilities.
Are you ready to future-proof your bottling operations? Explore Siemens’ innovative solutions to bring agility, efficiency, and excellence to your production lines.
FAQ: Agile manufacturing engineering in bottling
1. What is manufacturing process planning in bottling?
Manufacturing process planning involves designing, testing, and validating production workflows to ensure efficient material flow, optimized resources, and minimal downtime.
2. How does automation improve bottling operations?
Automation standardizes processes, enhances product consistency, and reduces errors, making it easier to scale operations and introduce new product lines efficiently.
3. Why is standardization important in bottling?
Standardization ensures uniform quality, simplifies maintenance, and allows for scalable, modular systems that support growth and operational efficiency.
4. How do digital twins support agile manufacturing?
Digital twins provide real-time visibility into production processes, enabling managers to predict maintenance needs, simulate process changes, and optimize workflows.
5. What are the key benefits of agile manufacturing for bottlers?
Agile manufacturing enhances flexibility, reduces downtime, accelerates product changeovers, improves supply chain resilience, and supports sustainability goals.