Re-use innovation assets: Unlocking speed and efficiency in consumer product development
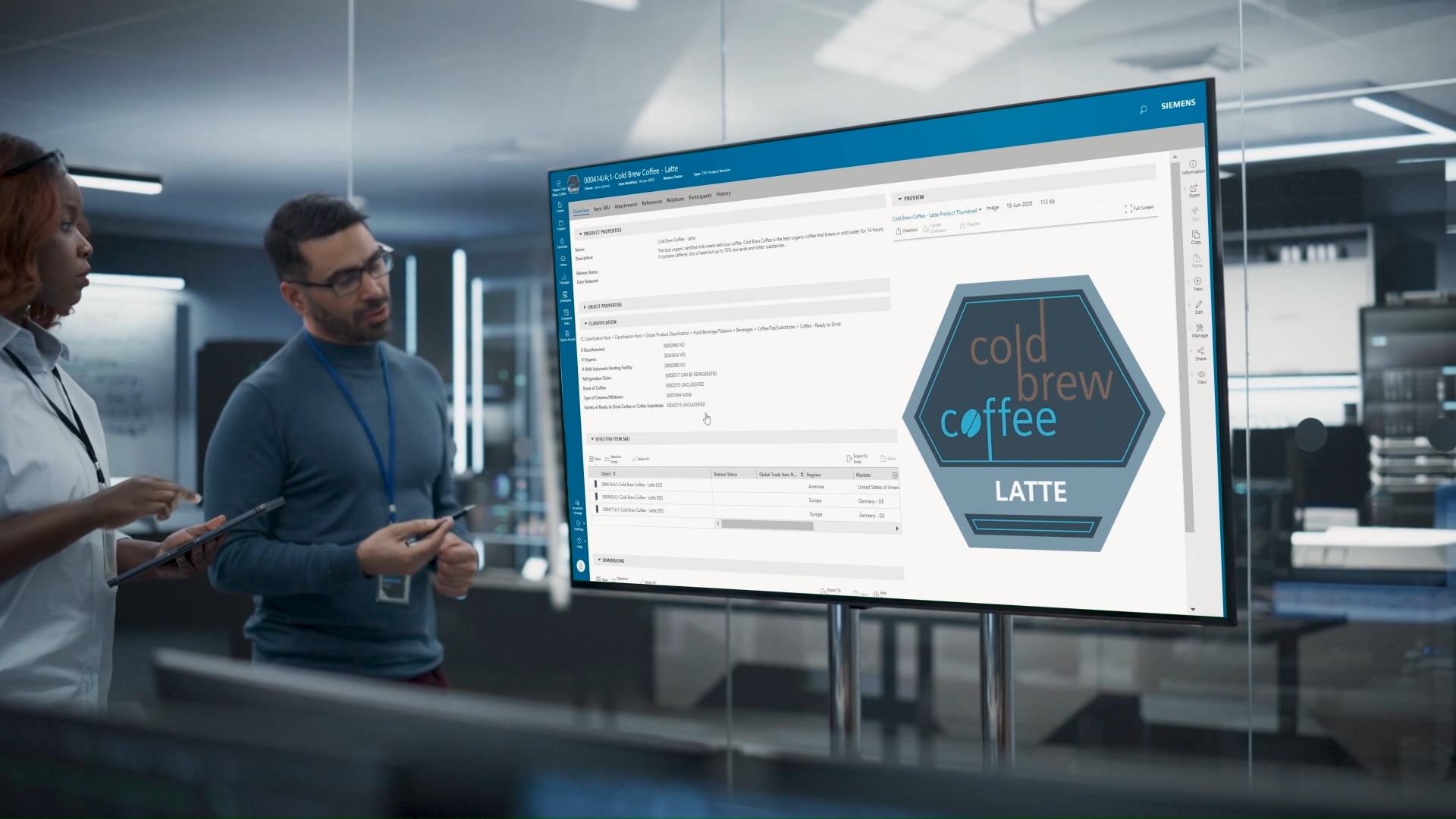
Maximize the potential of existing innovations to speed development, reduce costs, and drive sustainability
What if your next breakthrough product was already sitting in your archives? Many companies unknowingly waste time and resources recreating designs and processes instead of leveraging what already exists. Instead of starting from scratch, businesses can unlock speed, efficiency, and cost savings by reusing innovation assets.
Every year, 75,000 new consumer goods products hit the market, yet 95% of new product launches fail. Too often, companies spend unnecessary time developing what they already have in a new format rather than maximizing past innovations. A smarter approach is to reuse innovation assets—building on existing knowledge, designs, and processes to improve efficiency, reduce costs, and maintain consistency.
By streamlining consumer product development with proven intellectual property and process knowledge, businesses can accelerate market entry while keeping costs under control.
Why innovation assets go unused
Despite the clear advantages of reusing innovation assets, many organizations struggle to put this strategy into practice. Why? Because they encounter common roadblocks that prevent effective reuse.
Despite having extensive product development resources, many organizations struggle to take full advantage of them. Common challenges include:
- Lack of cross-functional visibility – Teams don’t always know what already exists, leading to duplicate efforts
- Inefficient access to previous designs – Engineers and designers may spend hours searching for relevant past work
- Disconnected systems – Without a digital thread, valuable knowledge remains isolated, making it difficult to integrate past learnings into new projects
A common scenario: an engineer spends hours recreating a component design, only to later discover that a near-identical version already existed in another department’s system. These inefficiencies lead to wasted resources, missed opportunities, and slower time-to-market.
Creating a more connected approach to asset reuse
To overcome these challenges, companies need a smarter approach—one that integrates past innovations into a connected, accessible system.
Cloud-based solutions provide the agility and resilience businesses need to efficiently manage product data and innovation assets. This is why many organizations turn to SaaS-based product lifecycle management to streamline workflows and enhance collaboration.
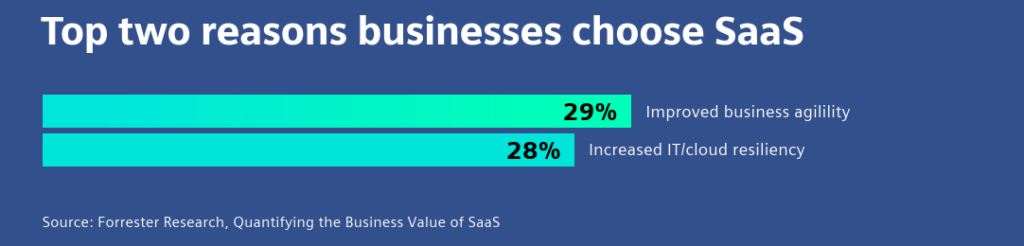
Successfully implementing asset reuse requires a structured approach:
- Auditing existing data assets to identify reusable intellectual property
- Standardizing formats to ensure consistency across teams
- Integrating a cloud-based repository for streamlined access
- Defining clear governance policies to drive company-wide adoption
With an integrated lifecycle management (ILM) strategy, supported by cloud-based PLM systems, organizations can break down silos between design, engineering, and manufacturing teams, ensuring they efficiently locate, adapt, and apply existing innovation assets.
How asset reuse impacts product development
A well-connected product development and manufacturing strategy amplifies the benefits of innovation reuse—helping companies eliminate rework, maintain data consistency, and accelerate time to market. By synchronizing the engineering BOM with the manufacturing BOM and bill of process (BOP), organizations can streamline workflows, improve production quality, and mitigate late-stage project risks.
Organizations that successfully adopt integrated lifecycle management (ILM) report key benefits, including:
- Accelerates project setup and execution
- Reduces redundant workflows and inefficiencies
- Expands product variation options
- Minimizes development risks
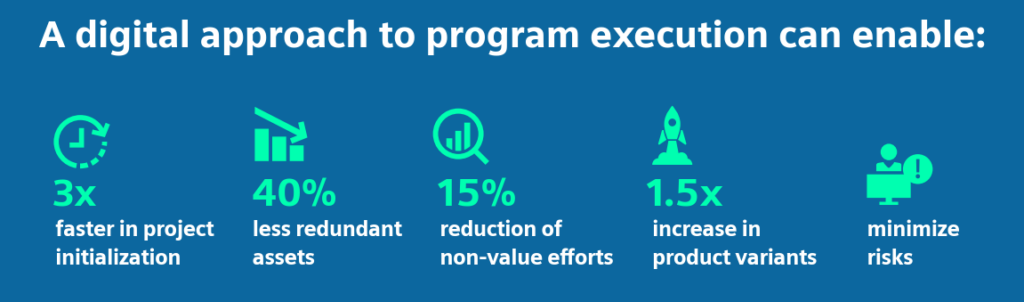
These benefits are not just conceptual—leading manufacturers have already achieved measurable results. Let’s look at how Electrolux and Joyoung successfully implemented these strategies to drive efficiency and innovation.
Practical examples of asset reuse in action
Industry leaders are already leveraging innovation asset reuse to speed up development, reduce inefficiencies, and improve collaboration. Two examples—Electrolux and Joyoung demonstrate how different approaches to reuse can drive measurable impact.
Electrolux: Reducing product development time by 20-30%
Electrolux, a global home appliance leader, streamlined product development by standardizing digital workflows and simulation processes. By reusing validated designs across projects, the company significantly improved efficiency and reduced costly iterations. Their results include:
- 20-30% faster product development cycles by avoiding redundant design work
- 15-20% cost savings from eliminating inefficiencies
- Improved issue detection, preventing costly late-stage production errors
Joyoung: Boosting product engineering efficiency by over 80%
Joyoung, a leading kitchen appliance manufacturer, took a data-driven approach to innovation reuse, improving accessibility and visibility across teams. By structuring product data in a centralized system, they achieved:
- 80% faster retrieval of past designs, cutting down unnecessary searches.
- 15% shorter product development timelines through streamlined collaboration.
- Greater cost control by minimizing data inconsistencies and duplicate work.
3 key strategies to maximize innovation reuse
The success of Electrolux and Joyoung shows that structured innovation reuse can drive efficiency, but how can organizations implement it at scale? Here are three proven strategies to make asset reuse a seamless part of your product development process.
1. Establish a centralized knowledge repository
Creating a structured, searchable database of past designs, specifications, and engineering documentation prevents teams from reinventing the wheel. With a cloud-based PLM system like Siemens’ Teamcenter X, engineers can quickly access validated designs, reducing wasted time on redundant efforts. This approach ensures that past innovations remain accessible, standardized, and reusable across projects.
2. Improve cross-departmental collaboration
Breaking down silos between engineering, manufacturing, and supply chain teams is critical for innovation reuse. When teams operate in isolation, valuable insights and assets often go unused. Siemens’ ILM solutions ensure that real-time updates are seamlessly shared, preventing misalignment and enabling faster, more informed decision-making.
3. Leverage digital twin technology for validation
Reusing past designs is only effective if those assets are validated for new applications. Digital twins allow teams to simulate real-world performance, ensuring that existing innovations meet new product requirements before production begins. Siemens’ Simcenter solutions integrate simulations across the entire product lifecycle, enhancing manufacturability, efficiency, and sustainability while reducing costly physical prototyping.
The future of consumer product development: Innovation reuse for efficiency
Successfully reusing innovation assets is more than just a best practice—it’s a competitive advantage. As product lifecycles shorten and consumer demands shift, companies that prioritize efficiency and standardization will be positioned to adapt faster, reduce costs, and accelerate time to market.
By leveraging integrated lifecycle management (ILM) solutions, companies can ensure they are making the most of their existing knowledge and capabilities, fostering innovation without unnecessary rework.
With Siemens’ Teamcenter X and Simcenter, manufacturers can standardize processes, enhance data accuracy, and improve collaboration across global teams, leading to more predictable, efficient, and scalable product development.
Stop reinventing the wheel. Start maximizing your existing innovations today. Learn how industry leaders are cutting costs and accelerating consumer product development with smart asset reuse strategies. Explore our resource page now.