Powering software-defined vehicle insights through verification and validation

As automotive manufacturers shift to developing more complex software-defined vehicles
(SDVs), the verification and validation process becomes more challenging and crucial thanks to
the number of complex interactions between software systems and hardware variations.
Fixing the software-defined vehicle design cycle
One of the most imposing issues related to verification and validation is that, historically, it’s been done
using the engineering V model. This model has engineering teams work on systems definitions,
then modules and assemblies, and finally, the components within those modules or assemblies.
When it comes time to do verification and validation, however, engineers must work from the
bottom up in reverse order.
According to this model, they only get to the systems level after examining components and then modules and assemblies. This means that engineering teams can only gain insight into systems-level verification and validation problems at the very end of development.
For example, the engineers responsible for electrical and electronics (E/E) systems might perform their calculations for verification and validation based on an initial configuration.
If the battery management systems team is pushing its own changes separately, no one on the design team may realize there is a conflict until late in the design cycle, when it runs integration and feature-level tests. Consequently, the engineering teams may only then detect issues that get in the way of verification of the whole vehicle.
Verification and validation for Software-defined vehicles
The traditional engineering V places verification and validation in the later stages of product
development. This approach is inherently flawed because of the large gaps in time between
design and validation.
Engineers do their testing on physical prototypes, which often do not allow them to investigate product features under a wide range of real-world driving conditions and safety scenarios. This also means engineers are working with a more limited design space, which makes it harder to explore, iterate, and innovate.
Verification and validation are a challenge, and engineers can struggle to effectively deal with any issues at the systems level because they are found so late in the development process.
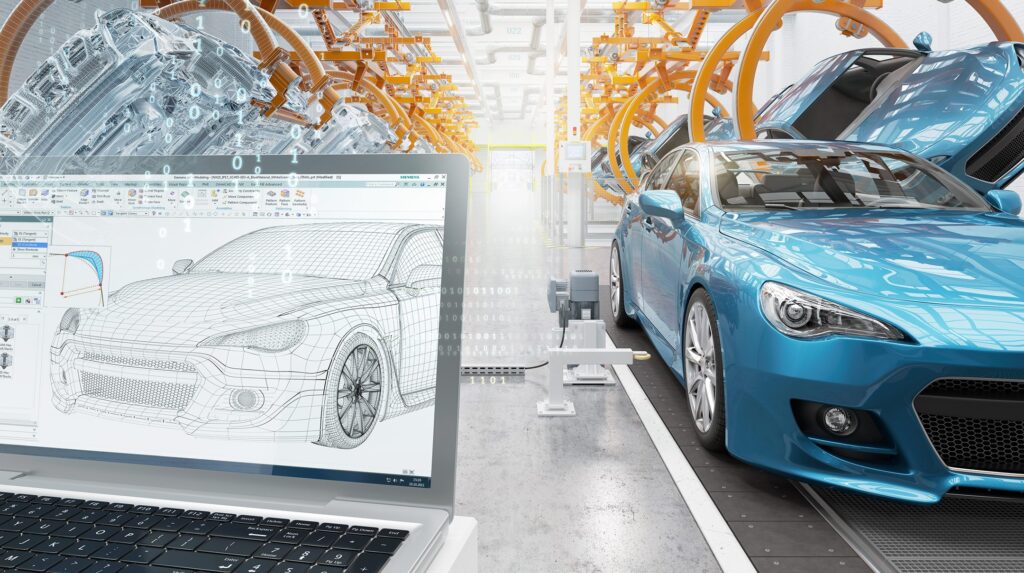
Software-defined vehicles and digital twins
When engineers take a more advanced approach, embracing digital technologies, they gain the
ability to progressively and continuously validate systems—and can fill in the gaps inherent in
the engineering V. Engineers can conduct their own domain-specific simulations to verify
functions and features.
They can identify potential problems early in the design process and resolve them. Once those issues are resolved, engineering teams can go on to build prototypes and do physical tests—and use that data to create accurate response models.
Engineering teams no longer have to rely solely on physical prototypes for verification and validation. They can use a mix of digital and physical models to make sure all product requirements are satisfied and to understand the vehicle’s behaviors and functional performance.
Streamlining software-defined vehicle product development cycles
Another advantage of these solutions is the ability to perform realistic testing on the models
across a wide range of different scenarios. Engineering organizations can conduct comprehensive simulations at each progressive stage of development.
Then they can ensure that all components and systems meet necessary requirements for performance and safety before moving on to the next stage. The ability to do this kind of virtual testing streamlines the product development cycle.
It improves the overall efficiency of verification and validation and yields results that are most likely to replicate real-world conditions. It also allows engineering teams to identify potential issues in design much earlier in the development process, avoiding schedule delays or costly rework.
Leveraging data for strong software-defined vehicle design
Verification and validation are an essential part of supporting the more complex features and
functions inherent to software-defined vehicles. As automotive manufacturers look to the future of vehicle design and development, they can see significant benefits when they adopt digital technologies and simulation tools.
These tools allow engineering teams to enhance the efficiency and effectiveness of the verification and validation process, filling in the gaps left by the traditional engineering V. As a result, engineers gain a better understanding of the complex interactions between software and hardware early in the development process.
They can leverage continuous data-driven insights from both digital and physical models to come up with the strongest possible designs.