Lightweighting by engineered composite materials, manufacturing and performance
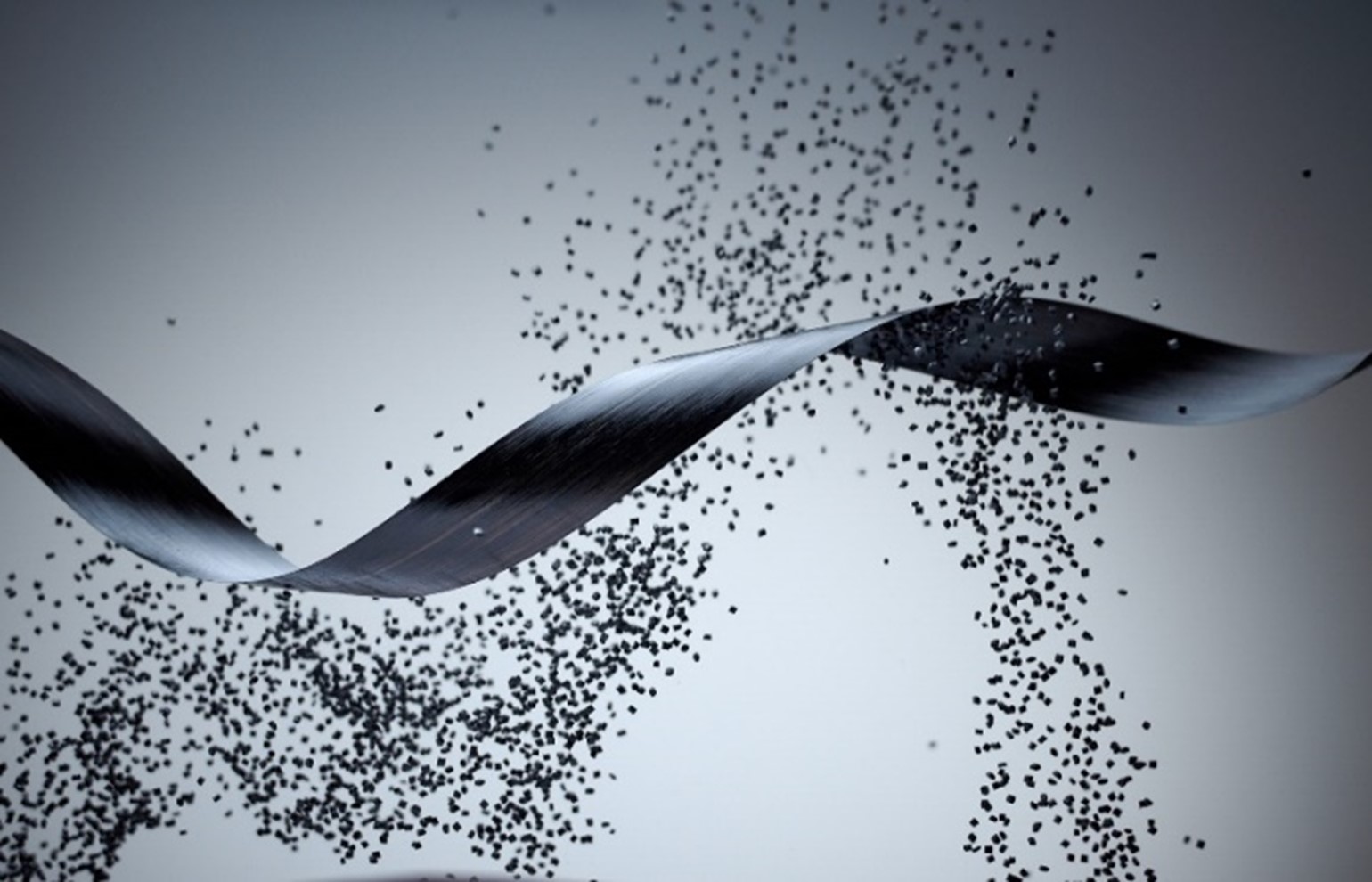
Building bridges with simulation
The development of new products increasingly demands the use of novel materials crafted through advanced manufacturing technologies. Conventional approaches often fail to fully exploit the potential of these innovative materials and processes, necessitating a more integrated strategy. Bridging the gaps between materials, manufacturing and performance through simulation is fundamental to harnessing their full capabilities.
- Materials: Key questions include which constituents to use and in what proportions. Understanding properties such as stiffness and strength is crucial for designing materials with specific performance characteristics.
- Manufacturing: The process significantly influences the material’s microstructure. Understanding how manufacturing conditions affect microstructure and optimizing these conditions is essential for producing high-performance materials.
- Performance: Effective design of products using these advanced materials involves optimizing formulations to maximize performance, ensuring the benefits of novel materials lead to measurable improvements in real-world applications.
Utilizing simulation to bridge these aspects is key to fully realizing the potential of new materials, driving innovation across various engineering sectors.
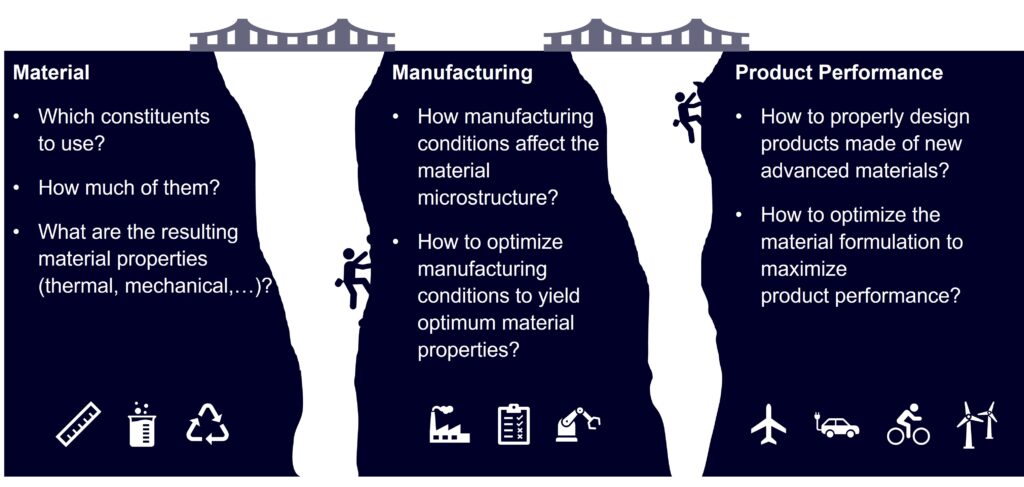
Composite materials: Challenges and opportunities
Composite materials, now prevalent in the aerospace industry and gaining traction in the automotive, energy and sports sectors, consist of two or more materials combined to achieve unique properties. Typically, these composites are made of a plastic resin matrix reinforced with fibers such as carbon or glass, in both long and short forms. They offer a high strength-to-weight ratio, making them particularly advantageous for sustainable technologies, especially in transportation and energy sectors.
Bridging the gaps Materials–Manufacturing–Performance (Figure 1) is particularly relevant but also challenging in the case of composite materials, primarily because the presence and orientation of the fibers can significantly impact both the manufacturing processes and the final product’s performance. In manufacturing processes, the directional alignment of fibers can lead to anisotropic cooling and residual stresses, which may result in warpage or geometric deformation, causing deviations from the intended shape of the part. Similarly, the performance of the final product is heavily influenced by fiber orientation: the anisotropic properties imparted by the fibers cause the material’s strength to vary with direction. In addition, the recent shift towards thermoplastic-based composite materials, which are more attractive in applications due to their easier processability and recyclability, has introduced additional challenges due to their sensitivity to environmental factors (temperature, humidity) and creep. This inherent complexity necessitates advanced simulation techniques to accurately predict and optimize material performance, ensuring the final product meets the desired specifications.
To address these specific challenges in thermoplastic composite materials, the research project ProPeL (Process and Performance Simulations of Lightweight Structures) aimed to research and develop an approach from the ground-up to better integrate material characterization, simulation of manufacturing processes, and performance evaluation of as-manufactured parts. Tackling this multi-physics and multi-scale challenge required a consortium of academic and industry partners, each bringing unique knowledge, experience, and expertise to the table.
- DOMO Chemicals, a global company specializing in the production of engineered materials, provided the materials used in this investigation and developed new advanced composite products that were characterized and improved during the project.
- KU Leuven and Universiteit Gent, serving as knowledge institutes, conducted innovative research on materials characterization techniques and the development of new materials modeling and research into homogenization methodologies.
- Siemens DI SW researched and developed an integrated methodology and simulation toolchain to link the simulation steps and incorporate the newly achieved material models and methodologies.
- MatchID, specializing in non-contact imaging systems for mechanical and kinematical data, providing its expertise and developing techniques for coupled thermal-DIC (Digital Image Correlation) to analyze in real-time mechanical tests using specialized cameras.
- Finally, REIN4CED, specializing in lightweight fiber-reinforced composite materials and active in high-end bike frames manufacturing, along with Honda, a leading automotive OEM, and Vitalo, specializing in thermoforming plastics and technical foams, provided industrial validation use-cases and extensive support to the research activities throughout the project, ensuring the accuracy and applicability of the developed approaches and methods. providing an industrial validation use-case for the research track on ABS vacuum forming.
What do we mean by integrated bottom-up approaches? What are the essential ingredients? Let’s explore this concept through two common manufacturing processes for composite materials addressed in ProPeL: thermoforming of long carbon fiber unidirectional tape and injection molding of short glass fiber reinforced plastics.
Thermoforming of unidirectional (UD) carbon fiber tape
Thermoforming a composite part typically involves two steps: first, a plate—often referred to as a blank—is created by stacking and pressing multiple layers (“plies”) of unidirectional tape (Figure 2(top)) at various angles; second, this blank is heated and pressed into a mold to form its final shape. Various challenges arise during manufacturing. For blank preparation, the consolidation of the different layers composing the blank must be optimal, which is influenced by the rheological properties of the resin and the tape, its surface roughness, and the pressing operation. During the thermoforming process, the final part’s geometry and properties are determined not only by thermoforming parameters such as temperature and pressure, but also significantly by the orientations of the plies.
For accurate mechanical performance simulations and to bridge the Manufacturing–Performance gap, it’s important to consider the fiber orientation from manufacturing, along with any potential residual stresses leading to warpage. Given the composite material’s complex microstructure, efficient simulations rely on homogenization techniques, where the individual fibers are replaced by a single anisotropic material that mimics the composite’s mechanical behavior. Within ProPeL, advanced polymer material models were first investigated and developed to describe the behavior of the thermoplastic resin, accounting for semi-crystallinity and self-heating effects. In the next step, inextensibility conditions were incorporated to induce anisotropy, mimicking the presence of fibers, thus building a physically-based homogenization methodology of the UD material from the ground up.
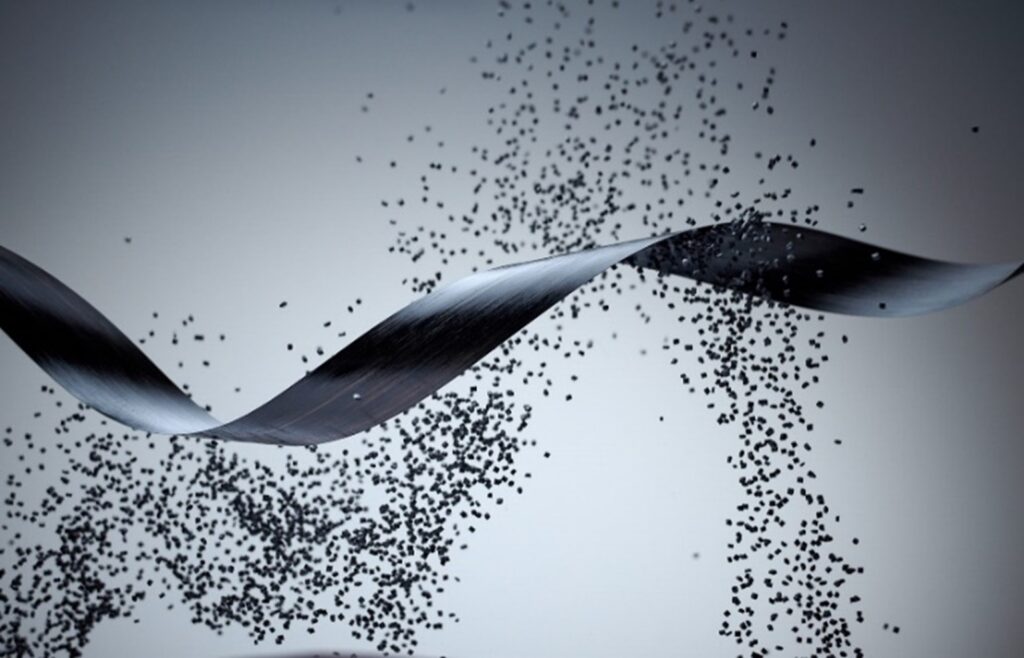
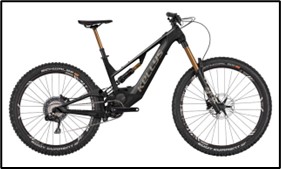
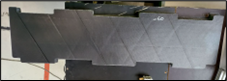
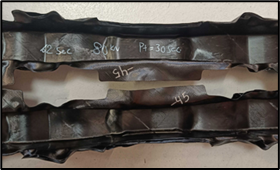
In addition, an innovative material characterization campaign, utilizing off-axis testing, was conducted to inform the modeling efforts and accurately characterize the UD material. Finally, REIN4CED provided an industrial validation use-case in the form of a bike frame component (Figure 2(bottom)). The manufacturing of this component focused on different ply orientation stacking configurations, and the mechanical performance of the various specimens was tested under different loading conditions, offering a valuable opportunity for validating the modeling and simulation methodologies researched and developed in the project.
Injection Molding of Short (Glass) Fiber Reinforced Polymers (SFRP)
In injection molding for short fiber reinforced polymers, pre-mixed pellets containing the polymer and short reinforcing fibers (Figure 3(top)) are typically heated until molten and then injected into a mold where they cool and solidify into the desired shape. The resulting fiber orientation is determined by the flow pattern during filling, which is influenced by the part’s geometry, the placement and design of the gate, and various injection parameters such as pressure and temperature.
As mentioned earlier, accounting for the resulting fiber orientation, as well as potential residual stresses and warpage from manufacturing, is crucial for accurate mechanical performance simulation and bridging the Materials-Manufacturing–Performance gap. Given the composite material’s intricate microstructure, effective simulations rely on homogenization techniques. Conventional homogenization methods for SFRP compounds, however, mostly rely on phenomenological observations of the global compound. Instead, in ProPeL, advanced homogenization methodologies were researched and developed starting from the material characterization of the resin alone and the composite material fully aligned in one direction. The proposed homogenization technique then combines those ingredients to create a macroscopic material model that mimics the local mechanical behavior of the microstructure, including elasto-plastic and visco-plastic behaviors. This bottom-up framework ensures that the proposed method remains grounded in physical principles.
To complement these modeling R&D achievements, an extensive material characterization campaign was conducted under a wide range of conditions, including varying strain rates, temperatures, and humidity levels. The latter is particularly important for certain thermoplastics, whose mechanical behavior is significantly influenced by environmental conditions. Honda also performed an experimental validation on an industrial use-case to not only assess the impact of injection molding parameters on the manufactured part, but also to test its resulting mechanical performance and validate the simulation toolchain (Figure 3(bottom)).
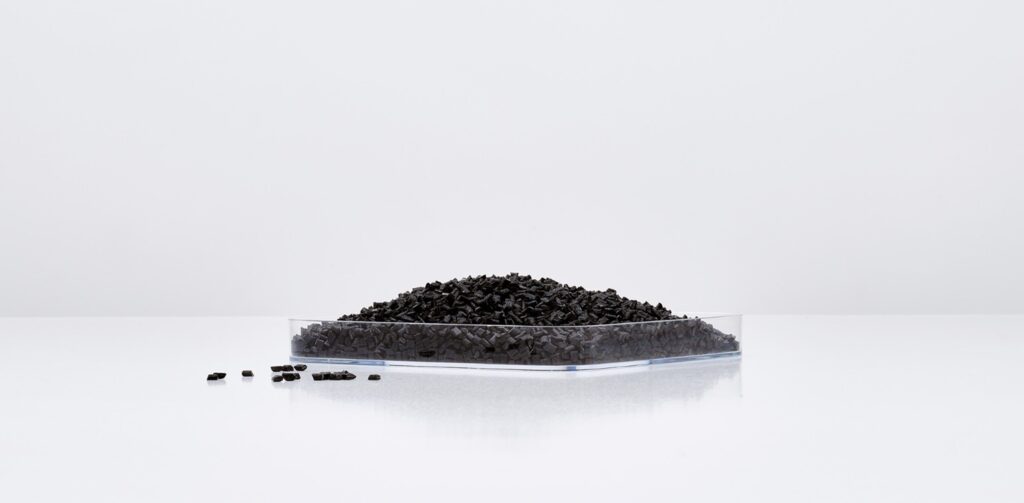
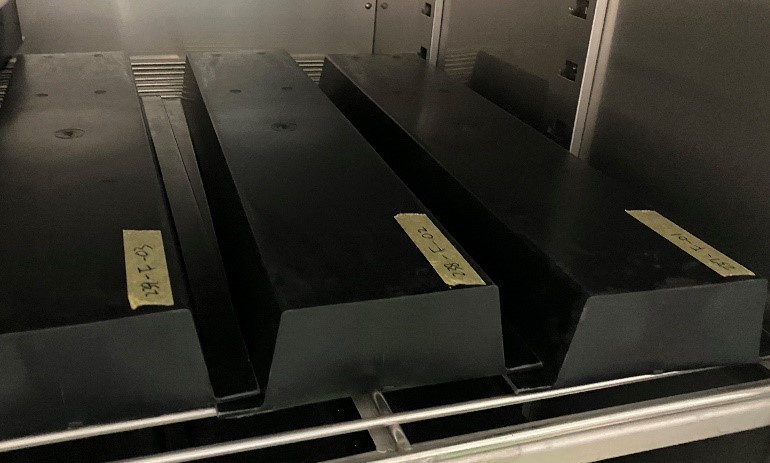
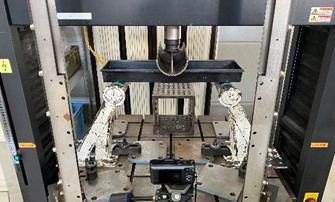
Conclusion
In conclusion, integrating materials, manufacturing processes, and performance evaluation through advanced simulation is essential for the development of high-performance composite materials. The ProPeL project exemplifies how R&D collaboration and innovative experimental and modeling methodologies can bridge these critical gaps, paving the way for future advancements in efficiently engineering lightweight composite structures.
Acknowledgements
The authors gratefully acknowledge SIM (Strategic Initiative Materials in Flanders) and VLAIO (Flemish government agency Flanders Innovation & Entrepreneurship) for their support of the ICON project ProPeL, which is part of the research program MacroModelMat (M3), coordinated by Siemens (Siemens Digital Industries Software, Belgium).