Understanding Product Lifecyle Management with Cocktails
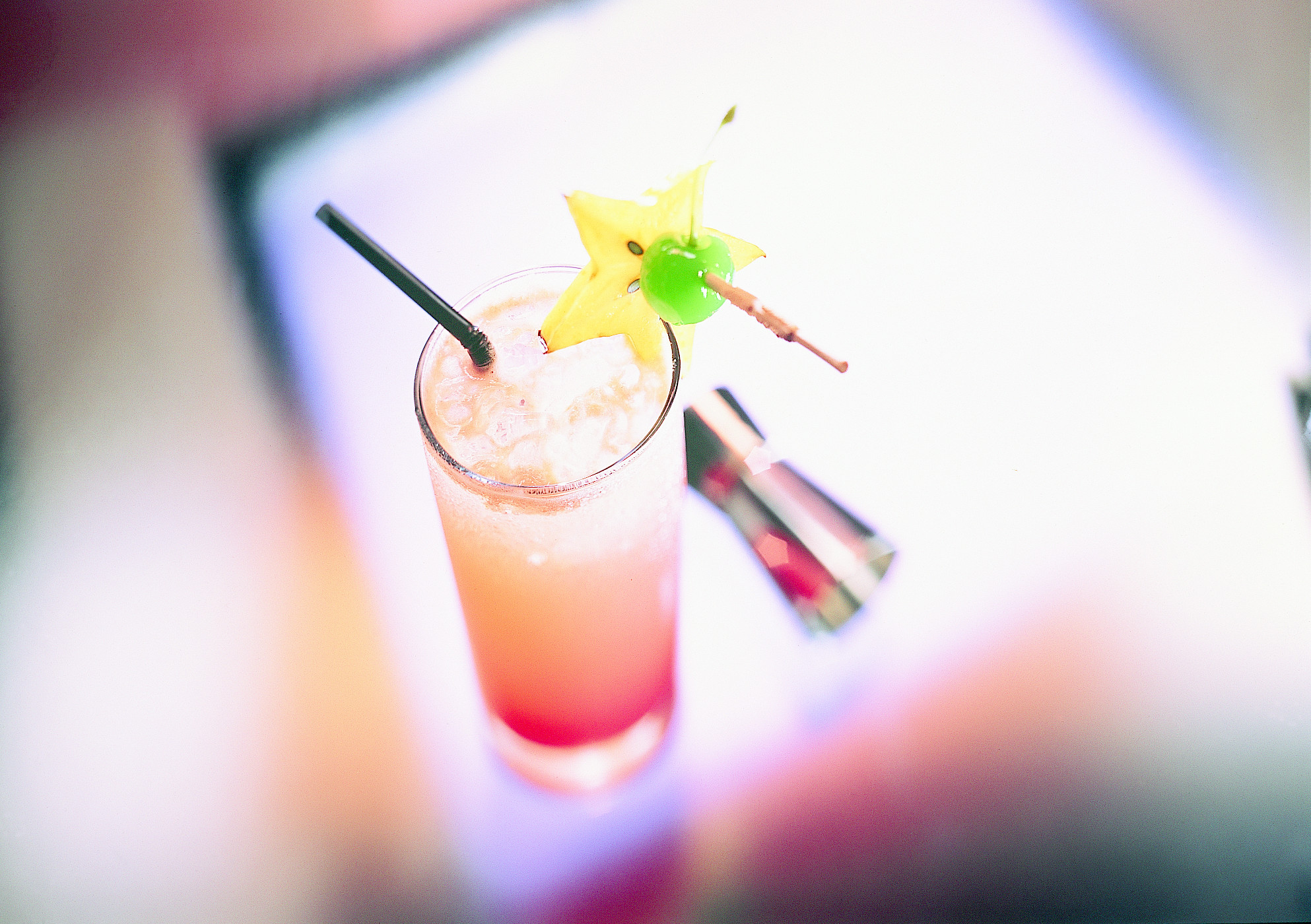
Learn the basics of Product Lifecycle Management, which comprises a set of methodologies and technologies used to manage the entire lifecycle of a product. This will be shown through the practical example by creating a cocktail!
Even cocktails require Product Lifecycle Management, and this helps to understand it:
Industrial products can be complex, and PLM (Product Lifecycle Management) helps to manage this complexity. However, a system for managing complexity must also be complex itself. This may seem difficult to understand, but it can be easily explained using a cocktail as an example. Let’s consider a cocktail as a product with a bill of materials (BOM) structure. This is a fundamental element of PLM, as it is for machines and devices.
The cocktail gets its name from its often colorful appearance, which suggests a certain complexity. By definition, a mixed drink consists of several ingredients, and in addition, the cocktail needs a suitable vessel, must be made using specific methods and tools. From ordering to production, to an empty glass that is put in the dishwasher (circular economy), the product lifecycle of a cocktail may be short, but it exists.
Starting with a Bill of Materials
As you can see, this article is not about the exact definition of PLM but aims to provide a basic understanding of PLM/BOM using an example that is easy to understand.
Therefore, let’s start with a specific product from the category of cocktails, the Planter’s Punch. The recipe is as follows:
- 2 cl lime juice
- 8 cl orange juice
- 5 cl brown rum
- 1 cl grenadine
If a host wants to serve the cocktail at a party, they must ask themselves whether the recipe is complete and includes everything needed to mix the cocktail. After all, they must take this into account when shopping for ingredients. If the party has already started, it’s too late.
If the host realizes that they are missing ice cubes and an orange slice for decoration, they would add these to the recipe. In industrial terms, this is called a bill of materials (BOM). The BOM for this cocktail would now consist of:
- 2 cl lime juice
- 8 cl orange juice
- 5 cl brown rum
- 1 cl grenadine
- 2 ice cubes
- 1 orange slice
Completeness is important.
Now we switch to the role or perspective of the cocktail mixer. This raises further questions:
- Do we have everything we need to mix the cocktail?
- Are all the recipe/bill of materials components present?
At first glance, everything seems correct, but where does the cocktail go or how do we drink it? We need to expand the bill of materials again:
- 2 cl lime juice
- 8 cl orange juice
- 5 cl brown rum
- 1 cl grenadine
- 2 ice cubes
- 1 slice of orange
- 1 glass
- 1 straw
At this point, we are talking about an eBOM or engineering bill of materials (note: this can be, for example, an assembly structure in a CAD solution). Our cocktail would already be very well described. However, before mixing the cocktail, the availability of the components must be checked, i.e., what is available in the kitchen and what needs to be purchased.
Bill of materials or BOM always serves a purpose: designers describe all the components used in it. Purchasing must be able to distinguish what they need to order as a standard part, what they need to order as a custom-made part, and what they need to commission as a self-manufactured part. From the purchasing perspective, the following questions arise:
- Is everything in stock?
- What needs to be purchased?
- What needs to be produced?
Thus, the list could look like this:
- In stock
- Glass
- Purchased
- Lime juice
- Orange juice
- Brown rum
- Oranges
- Self-manufactured
- Ice cubes
- Orange slices
PLM vs. ERP
Orderable components and assemblies are also called materials in an industrial context. These are managed in an ERP (Enterprise Resource Planning ) system (https://en.wikipedia.org/wiki/Enterprise_resource_planning). While PLM manages the technical description of a product over its lifecycle, ERP handles many logistical topics. To later determine quantities and costs, we refine our bill of materials by adding additional descriptive features and attributes, partly in the PLM system and partly in the ERP system.
Different bill of materials designations such as BOM, eBOM, mBOM, etc. always have a specific perspective and help to perform defined tasks from that perspective or role. By adding additional attributes, our bill of materials becomes a table, a purchasing bill of materials.
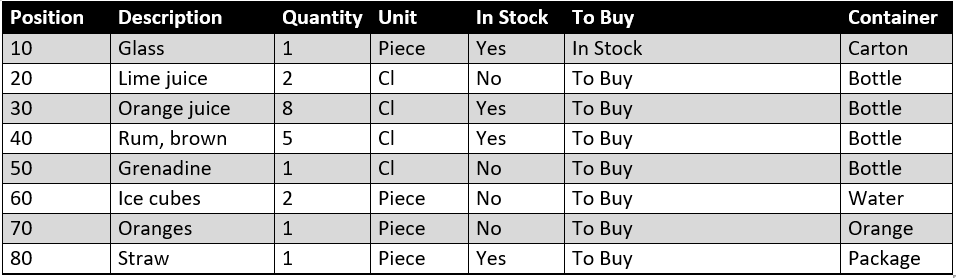
We view the table as a cocktail mixer from the perspective of the production planner. For this role, the location, timing, and sequence of processing steps, as well as material availability, are important. The list above is expanded by adding further additional information to the manufacturing bill of materials (mBOM). This describes the production processes, such as in the assembly of a product. https://en.wikipedia.org/wiki/Manufacturing_bill_of_materials
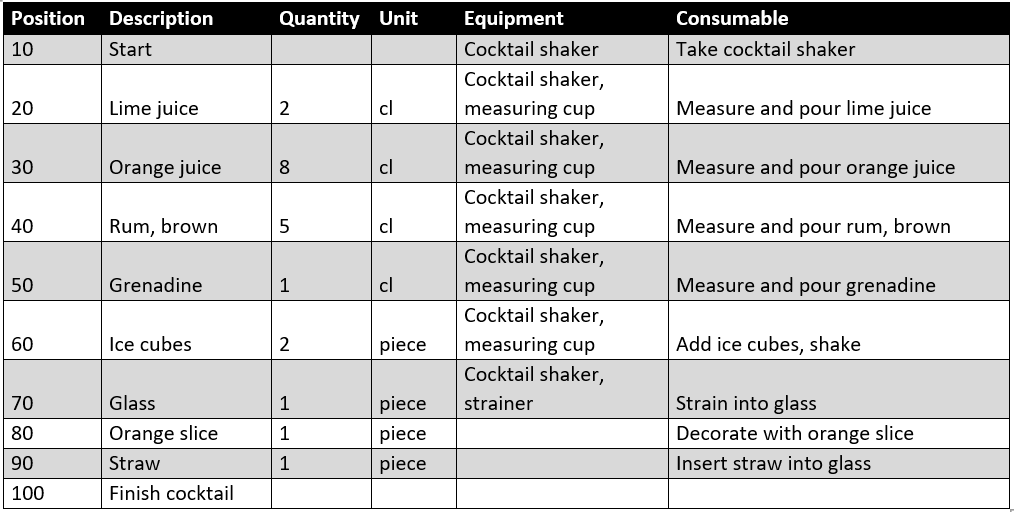
For ice cubes and oranges, which we want to produce ourselves, we would still have to create a production list. I assume that this has been done and I won’t go into the details. A list that describes the complete production process is also called a BOP (Bill of Process https://www.plm.automation.siemens.com/global/en/our-story/glossary/what-is-bill-of-process-bop/107901).
Challenge of Individualization
There is one more point we need to discuss: the variant bill of materials. What would change if we were to use different types of rum, for example?
This would not have any impact on the structure of the bill of materials, as only the material, i.e., the position, would be different. Here are two tables to illustrate:
Variance Caribbean RUM
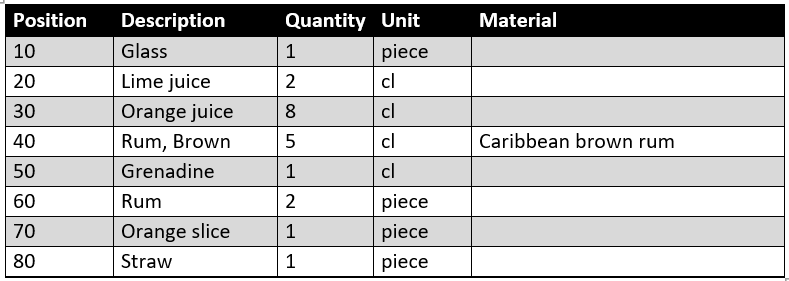
Variance Philippine Rum

If we consider all possible variants, not only materials can change, but also the quantity, for example. However, even with a changed material (e.g. Caribbean vs. Philippine brown rum), the structure of the bill of materials (BOM) does not change in an engineering context. For purchasing, this presents the challenge of managing additional materials, while logistics planners and production planners may have to consider additional requirements.
Conclusion and Example:
A BOM is a structure that can be defined differently based on characteristics, attributes, and ordering criteria, and can be perceived differently depending on the role of those involved. This is why departments often have extensive discussions about BOMs.
I have simplified many things to present the overall context, so I ask that you look up the exact definitions yourself on the internet. Good sources include Wikipedia or scientific articles on the topic of BOM, eBOM, mBOM, BOP.
Finally, as an example from the automotive industry, consider the BOM structure of the Volkswagen modular transverse matrix with ordering criteria and variable parameters. Vehicles are divided into zones.
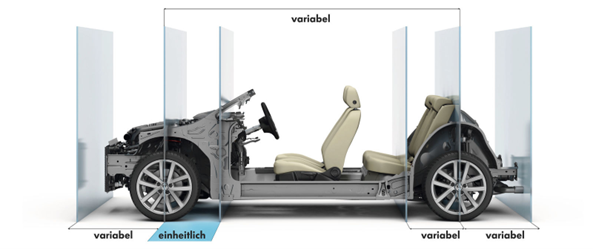
We will look at the instrument panel zone, where a BOM structure can contain variants, such as left-hand or right-hand drive. One level deeper, the components used may be manufactured by different suppliers in different locations. However, the structure does not change, and the components are manufactured based on their respective locations.
When a customer uses an online configurator from an automaker, they are doing nothing more than specifying their personal parameters within the variant BOM. This results in a unique configuration of materials, quantities, component numbers, and necessary assembly structures, allowing the customer’s personal vehicle to be manufactured.