Manufacturers meet at Purdue University to discuss data and PLM for better decisions
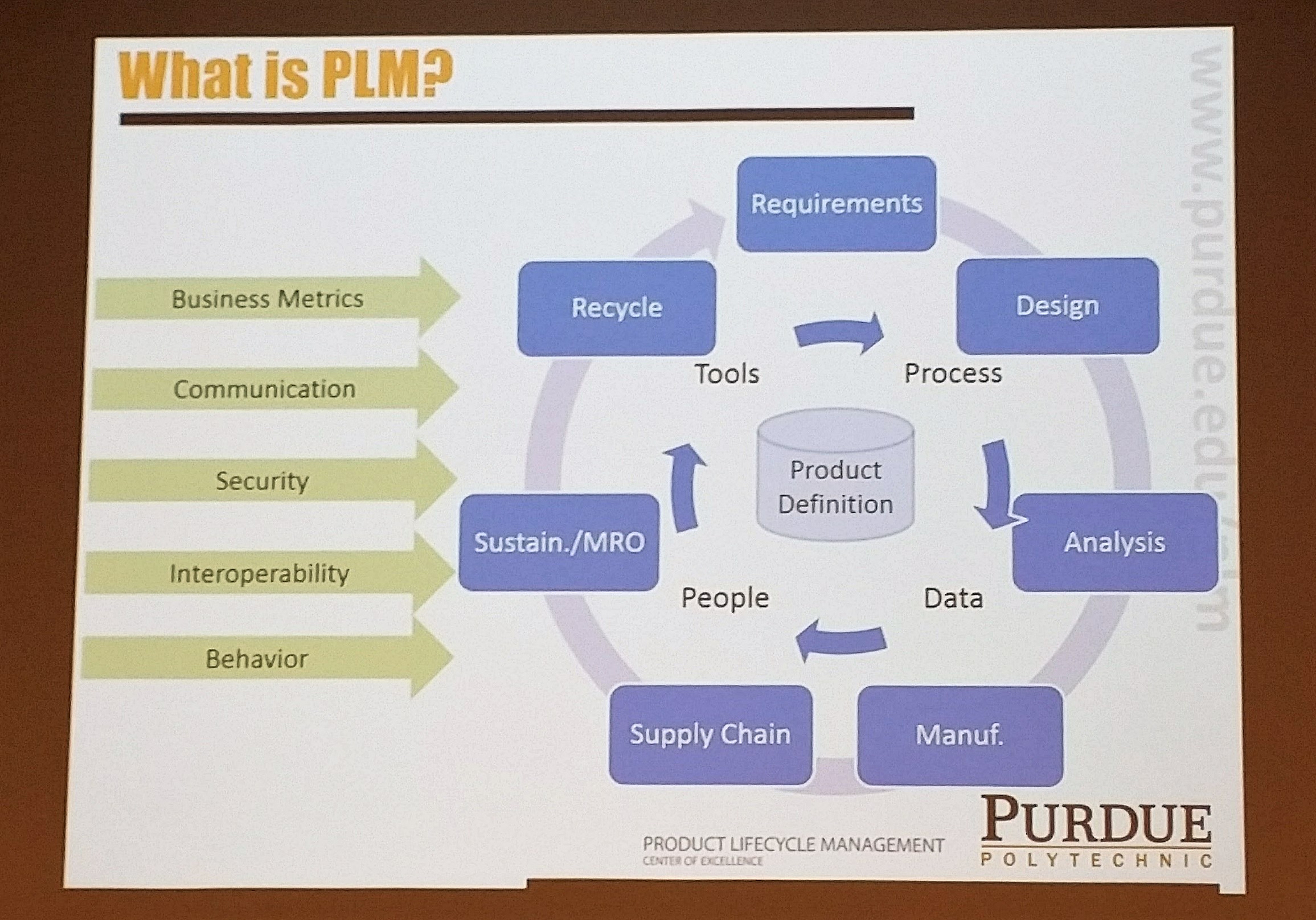
Purdue recently held its Fall PLM Center of Excellence meeting at the newly opened Indiana Manufacturing Institute. The state of the art facility houses Purdue’s PLM Center, an interdisciplinary research center, along with the university’s work for the Institute for Advanced Composites Manufacturing Innovation (IACMI), the Digital Manufacturing and Design Innovation Institute and the Indiana Next Generation Manufacturing Competitiveness Center (IN-MaC). It was clear that advanced manufacturing is alive and kicking in Indiana and industry is collaborating closely with academia to ensure a skilled future workforce.
This is a biannual meeting that brings together industry and academia to discuss the state of PLM from theoretical and applied technology viewpoints. Dr. Nate Hartman, director of Purdue’s PLM Center, is the mastermind behind this event.
Nate spoke the week prior to this event at one of our Regional User Group events. He shared the Education 1.0-4.0 story that much like Industry 4.0 transformed from apprenticeships to manual arts to industrial arts to where we need to be today with applied technology education. That was good background for the PLM Center of Excellence event that brought academia and industry together to collaborate on the digital and PLM topics that impact the current and future workforce.
The agenda for this event emphasized these topics:
- Customer-centric PLM
- PLM data in business decision making panel
- Digital Thread and Digital Twin
- IIoT and Big Data Analytics to Capture Value in PLM
- Digitalization Changes Everything. Everywhere.
- Manufacturing data in PLM for decision making
- Future state – next gen PLM
Siemens PLM Software’s president and CEO Tony Hemmelgarn shared how digitalization is changing everything and providing companies the opportunity to be the disruptors or be disrupted. He noted how digitalization is collapsing the innovation cycle and enabling continuous business transformation. He discussed how digital twins are at every step are connected through a digital thread that enables better decisions.He shared a use case from FMC –automating analysis to find optimal undersea pipe design that reduces pressure while minimizing erosion. Tony discussed advances in predictive engineering analytics with Simcenter, application lifecycle management to PLM integration with Polarian, new faceted design changes through convergent modeling as well as analytics in product and factory data with Omneo and Mindsphere.
Tony talked about with all this technology, the concept of a digital enterprise is difficult to grasp without seeing it in action. Together with Industry and Academic partners, we are transforming workforce development and education through Digital Enterprise labs. We have partnered with governments in several countries to establish labs to bring digitalization to life for industry, government and academia.
David Angelow, a lecturer at Texas State University & Management, talked about the need for a customer-centric business vs. product centric. He shared an example of 3M changing the design of a soap dispenser after comments posted on social ratings/reviews sites. He noted that there are three times the customer touchpoints after the sale. Since it is less expensive to retain existing customers than gain new ones, he argued we need to manage that lifecycle, that customer journey, carefully. He discussed capabilities to engage through PLM powered supply chain management SCM and customer price quote as well as product transformation tracking and innovation enablement through crowdsourcing.
A panel discussion on Leveraging PLM Data in Business Decision Making included input from Purdue, GE Aviation and Siemens PLM Software. Michael Witt, associate professor of Purdue, discussed different kinds of data and how different motivations play into making decisions on that data. Thomas Brush, senior associate dean at Purdue, noted challenges in risk management with IP protection in the supply chain. Mark Takacs, principle engineer at GE Aviation Supply Chain, noted that there is immense value when you can mix the terabytes of data with the results from the field to improve design. Tony emphasized the need for domain knowledge to filter through the data since it is often the unstructured data that most impacts how rapidly you can make a decision. He noted the work we’ve been doing around industry catalysts and argued if we get good at working with unstructured data, then why structure. Mark emphasized GE is not adding structure but focusing on the data science – how do you draw conclusions from the data.
The supply chain discussion was interesting. Tony talked about the mix of customer demands we get in terms of file formats. When we’ve provided options for just an abstraction of the CAD file through the JT format, some wanted more. When you strip out the design process and the knowhow, then the supplier may have to rebuild that. Yet when we’ve provided options to add more into the format, then customers worry about exposing too much IP. He said he believed the heart of the issue is a lot less about technology than the business relationship.
Another panel discussed Digital Thread – collecting and connecting data throughout the product lifecycle panel. The initial discussion was a NIST-funded project that the panelists collaborated on. Tom Hedberg of the Systems Engineering Group at NIST discussed some of the results of a survey asking OEMs how they provide data to suppliers. Phil Rosche, principal of ACCR, shared the value of moving model centric data downstream with the AP242 standard that included embedded PMI. They have seen some astounding results. Kevin Fischer, manager of Manufacturing Technology Pursuits at Rockwell Collins, talked about their need for more robustness in the model to suppliers. He noted there are some gaps to address before designs can directly assign PMI. Tom emphasized that we still need to change the way we think. He said there can be 75 percent cycle time savings if companies go all digital. There is still a lot of waste – creating the model, then the drawing, then verifying and sending to a supplier, then the supplier recreates and the original design requirements may not be met.
There was some discussion if additive manufacturing negates the need for richer data. Kevin noted that additive manufacturing puts an explanation mark on it. If we aren’t getting things dimensionally correct, then we can’t go through validation. Larry Maggiano, a senior systems analyst at Mitutoya shared that the AM model may go direct to manufacturing yet PMI and constraints exist and are misinterpreted. Other customers in the audience had similar experiences with “hidden PMI”. Nate spoke about sterile CAD models and looking at embedding vs. linking information for both behavioral and contextual input.
Matt Littlefield, president and principal analyst of LNS Research, presented on How the IIoT and Big Data Analytics Help Companies Capture Value in the PLM Environment. Matt emphasized the need to set strategic objectives on the role of PLM in connecting the virtual and real worlds. He noted the need for this both internally in a smart connected enterprise and externally with smart connected products. He pointed out the culture clash or data science divide between engineers and scientists. To cross this divide each has to be open to new tools and methodologies enabled by big data and machine learning. He noted that big data is not just about volume but variety and velocity.
Michael Grieves, executive director for the Florida Institute of Technology Center for Advanced Manufacturing and Innovative Design discussed the leverage of a digital twin on mitigating unpredictable, undesirable emergent behavior in complex systems. He argued the digital twin can ensure manufacturability, perform ability and supportability. He discussed DFAM – design for additive manufacturing.
Rolls-Royce’s digital manufacturing lead Dan Hartman moderated a panel discussion on – Leveraging manufacturing data in a PLM environment for decision making. There was some good discussion on how to ensure new designers and engineers understand what is possible on the shop floor. One individual in the audience from Lockheed spoke about when she was a new designer, a technician showed her how difficult it was to make what she designed. She spoke of the benefits of designing at a plant so you can see that impact first hand. Today we must find ways to capture that input for education and training. Dan DeLaurentis, professor of aeronautics and astronautics at Purdue, shared a brilliant idea. He recommended reverse sabbaticals. Similar to what can be learned in apprenticeships but with the opportunity to potentially impact many more students, send employees back into academia to mentor and guide students on concepts like DFM and PLM.
The final panel for the jam-packed event was on the future state – next gen PLM – where should we go and how do we get there. There was discussion on how PLM can transform current business practices. The panelists also shared a few ides of extending PLM into new areas. Dan noted that their focus is on getting information back into engineering to make better business decisions. There is a lot of legacy equipment and processes so it can be hard and costly to move data. Tom emphasized the need to think new without forgetting the past. He argued PLM is more than the technology. Michael talked about the supplier network and the need to help small and medium sized suppliers to participate in the digital perspective. He said we talk a lot about the people, process and technology but the practice is often forgotten.
There was some discussion on Google for PLM. Everyone wants to be able to do a quick search and get what they need. Someone recommended and XPrize for manufacturing to solve this. Some suggested better access through mobile apps. Others believed future systems will just know what you need to know and presented as needed where needed.
During breaks in the PLM event, a guided tour was offered through the Composites Manufacturing & Simulation Center (CMSC).The purpose of the center is to advance the design, analysis, certification, and manufacturability of composite materials.Guests got to see the material testing lab as well as a 3D printer that demonstrates additive manufacturing using composites.
I’ll come back to one of Nate’s What is PLM slides since this meeting touched on nearly every part of the lifecycle and challenged the audience of academia, industry and technology providers to collaborate for the strongest solution.
At Siemens, we believe we must bring industry and academia together to close the digitalization gap and develop the right set of skills in future designers, engineers and manufacturers. Our global academic program is committed to working with leading edge institutions like Purdue to close that gap through stronger industry collaboration and applied technology education.
Together we can empower a future workforce to be digital disruptors. Let us know how we can help you.