Three World-Class Student Competition Teams Share Their Success Principles
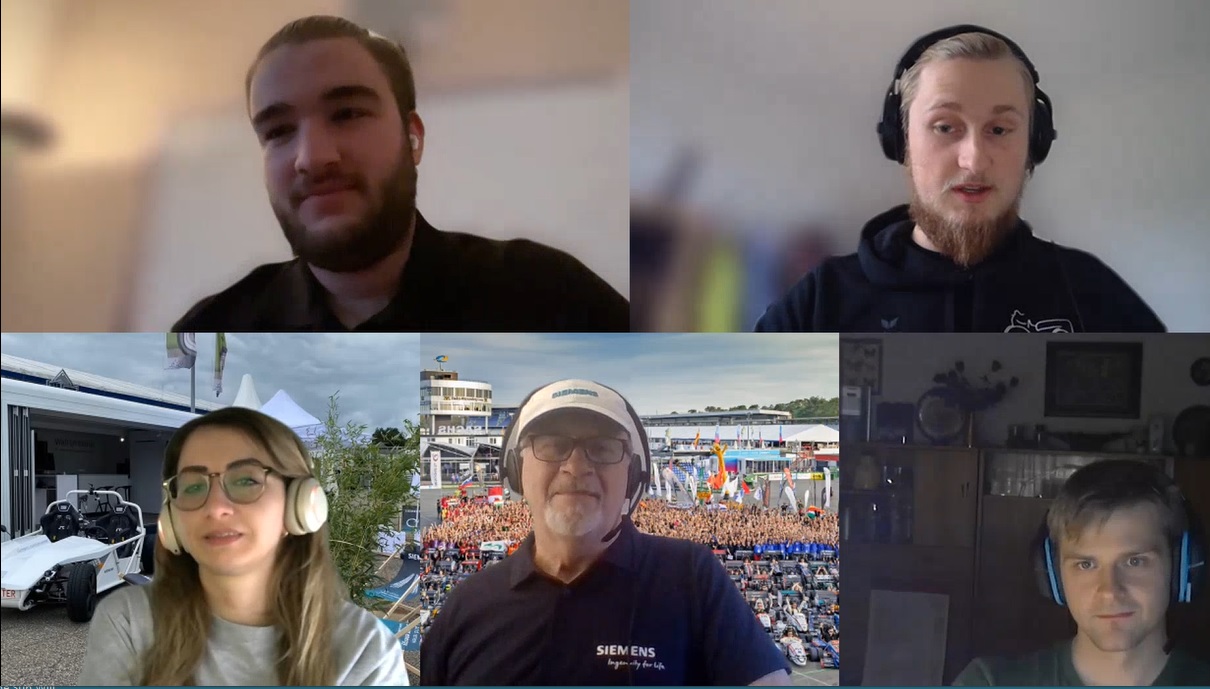
Due to the pandemic, it’s been very difficult for teams around the world to retain knowledge and to pass on knowledge to new members. With two whole seasons under Covid constraints, the negative effects on team knowledge and communications were magnified – so we decided to interview a few top teams that have what we call ‘learning organizations’ or ‘knowledge-retention organizations’ – teams who are very intentional about their process and organization and have many podium successes as a result. Such as the #1 and #6 world-ranked Formula Electric teams. All three outstanding teams were eager to share with other teams around the world. These insights are valuable for student teams of all kinds such as other Formula Student teams, rocket teams, airplane teams, solar car teams… long after Covid constraints are lifted.
Siemens Software has a global student competitions program which includes financial support to competitions as well as no-cost software grants, training and tech support to student teams. Teams can apply for grants at www.siemens.com/plm/gaf.
Read on, with apologies for the lengthy interview transcripts in the Appendix – it’s quite difficult to make an interview transcript short without losing concepts and subtle but important details. Below are the key points from the interviews.
- Alumni of the team can be a huge factor for technical advice and for team spirit. Put serious effort into communications and motivating alumni to keep helping after graduation. Their advice can help enormously!
- Simulation-centric or ‘digital ‘twin’ engineering methodology is a core process for every top team’s success.
- Recruiting & on-boarding – effort, persistence and discipline pays off. Write tutorials. Consider a probation period and/or ‘CAD boot camp’ to ‘filter in’ good members as well as help them figure out the best sub-team for their interests and skills.
- Recruit for balance in engineering disciplines; strive for electrical and computer science recruits to balance out the mechanical majors.
- Recruit and screen for high-motivation and reliable members – with little weight on high grades.
- Even marketing/business members should learn enough to make attractive images from CAD and better relate to engineering members.
- Spend enough time on the high-level car architecture/concept and requirements – that will drive the rest of the year’s effort.
- Be diligent about documentation, wikis – take the time and discipline to be knowledge-organizations. Preserve the why not just the what for future generations.
- Product data management pays off with fewer mistakes and improved efficiency.
- Use engineering software packages that are already integrated and have good training materials – saves a lot of time.
- Do distribute decision making to sub-teams but verify against requirements and system-integration. Helps motivation and creativity. Avoid a top-down culture that can de-motive members.
- Do have a member or two specializing in the engineering infrastructure: software licenses, servers, product data management, wiki admin, etc.
- A manufacturing sub-team can be consultants to designer members for ease-of-manufacturing advice and experts in machine tooling to help other members fabricate parts.
- Be creative with virtual team-building and comms using virtual tools. It’s harder than in-person, but keep it up.
- Sponsors can be a great success factor and save costs, not only software providers like Siemens, but also shops that may donate fabrication machine time. Actively seek out sponsors – make it someone’s priority.
- Be very careful about self-developed vs off-the-shelf parts decisions. The highest performance can come from custom parts,but consider carefully a reasonable ROI for competition points gain (using simulation), vs the cost/time/focus required.
————————– Appendices – Interviews with 3 Top German Teams ————–
In the Formula Student community, it is widely acknowledged that the top teams from Germany (plus select teams of Switzerland, Austria, Netherlands) are the best organized teams making the highest performance Formula Student racecars in the world. The first one is the #1 ranked Formula Electric team:
GreenTeam Uni Stuttgart Team Interview
Team Organization Best Practices (& with Covid)
www.greenteam-stuttgart.de
info@greenteam-stuttgart.de
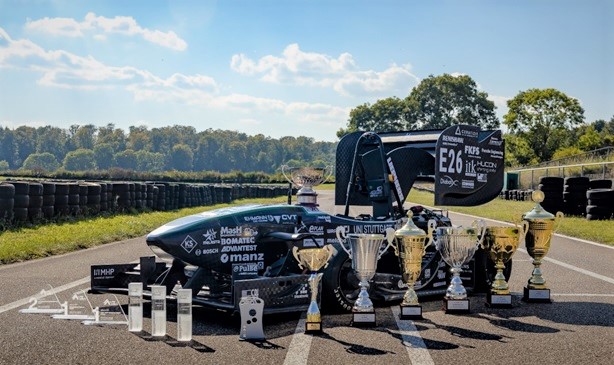
2021 FS Austria: Formula Electric 14th Place overall
2021 FS East/Hungary: Formula Electric 2nd Place overall, Driverless 7th Place overall
2021 FS Germany: Formula Electric 1st Place overall, Driverless 8th Place overall
2021 FS Alpe/Croatia: Formula Electric 1st Place overall
RANKED #1 in the world for Formula Electric
out of 203 teams worldwide, as of 3/22
Intro: I’m Daniel. Martin was team leader last year with the e0711 evo car. I’m Oliver I’m the new leader of the new team leaders for the coming season we are from the GreenTeam at the University of Stuttgart building electric racecars since 2010. We’ll start with the topic of how we achieved to reach this high level of race car technology and the success we had in the last year. First of all our main goal always is to win at student competitions, nothing less, that requires strong dynamics and aesthetics therefore we need to build a big team and develop the team over the years.
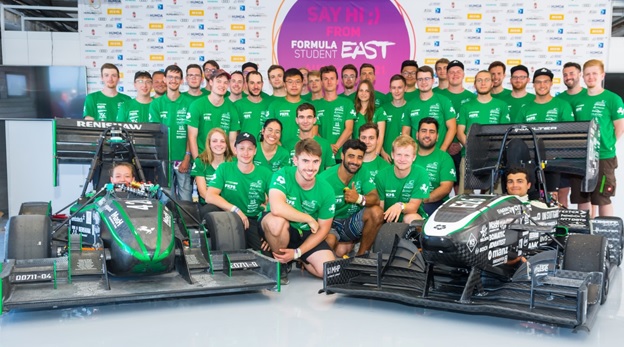
Self-developed: One foundation is that we have strongly focused on building self-developed parts instead of just buying them because there’s almost every time a way bigger potential in self-developed parts than just in just buying. With the e11 evo we had our top goal to develop the first fully self-developed car at the university in Stuttgart and so we made a fully self-developed powertrain and almost self-developed every important part on the vehicle.The main parts we still buy are tires and screws like that – we also plan to integrate the self-developed inverter into the car sadly we couldn’t make it we weren’t sure enough about the reliability and the performance this year so for the next car we are definitely aiming for integrating a custom inverter into the car. We’re investigating every part of the vehicle – we are comparing where we have a basic decision make-or-buy. Another example to buy is switches. That would be a big effort to build them or design them on your own and build them and test them and the gain you can get is really low – but for example developing our own electric motors gave us a lot higher performance.
Car-Architecture: The most important thing for us always is the Car Concept: at the beginning at the concept phase for the evo it was to maximize the downforce aerodynamic system – we have made lap time simulations – based on the data we have from the last years on those tracks and it showed that a big down force is giving the best performance impact so we decided to build a completely new monocoque in a very narrow design to give as much space as possible for the aerodynamic devices around the car.
The next big thing is the electric powertrain with our self-developed motors (4WD) and the battery accumulator. Another big new thing on the car was we redesigned the rear to integrate the motors into the wheel hubs to give space between the monocoque and the wheel package for the air to flow through to reduce the drag and increase the potential for downforce. In the end we were able to use all this development to achieve a good success at Formula Student Germany for the third time now in our history.
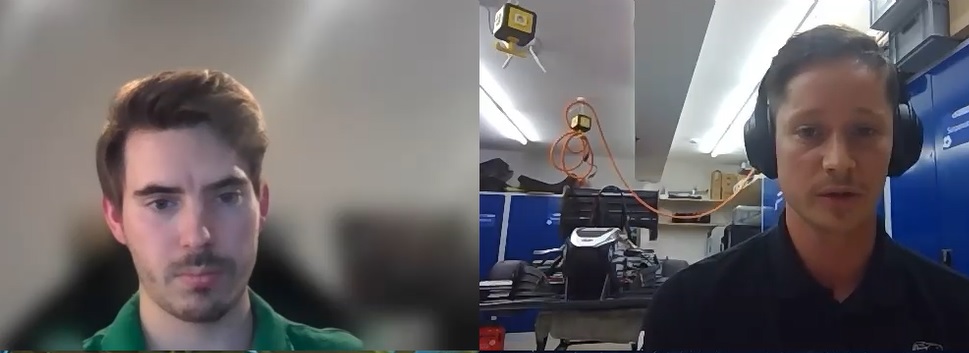
Simulation: I mentioned the lap time simulation before in developing the vehicle concept that is one main thing we do in the concept phase – we are analyzing the data from the last years especially the year before in our lap time simulation as well as from the event data itself like the points we were able to score – we always have a very close look on where we lost points and why we lost points – also compared to other teams. For example how many points did we lose because of missing reliability of the car compared to other cars so we can see for example if we focus on making our car more reliable we can win more points and maybe add a little bit of weight to the car but the performance we lose from the bit of weight reduction is worth adding to the reliability of the car. We are building up a different tool chains to feed our lap time analysis -for example we have a logging system during our testing phase where we log all the data we get from our and so we can analyze it and we can get knowledge from the testing phase or testing phases accumulated over the years.
Recruiting: In the formula student events, to be at the top – it is more important to have a strong team that works together well. Often the problem is how do you even recruit students at your university. For students, it’s a lot of work just to be in engineering classes and some students want to hold their work at a minimum level so they are not ready to risk joining the team. We first start by recruiting through various channels such as Instagram or in online lectures or at the in-person classes at the university. We do some info events, we go to the cafeteria to just be visible for students that they see okay we are here and maybe an interesting project to join. The most important thing for us is that they see that they have a lot of opportunities within the team to fit them. It’s racing, that’s something some people dream of their whole life but just see it on the TV only such as Formula-1. By joining our team you really can get in touch with that interest to see how a car is developed from zero to 100. That holistic view of a vehicle development is something industry you won’t get to experience normally in school or even in industry, you just get a narrow assignment usually in a big company. You can make this whole vehicle with friends you can develop yourself to be a complete real-world engineer, such as learning project management and team communication so we emphasize that to candidates. We benefit from a broad diversity of students and that for us it doesn’t really matter what kind of major they study or where they come from – the much more important thing is their spirit – we want them to have commitment – we want them to take responsibility and we want them to be willing to learn and work hard with the team – because this is something that can make a huge difference and keep the team together even if it’s a really hard time just like in Covid. When there’s a candidate to get to know him or her and just not just like okay come here’s your work – so we want to know what kind of person they are, and we think that everybody can be an effective engineer even if they don’t have much experience when they’re willing to work and willing to learn We show them the opportunities they have within our team and how and the next step would be how to train them.
Onboarding-Members: A big question for every student team is how to handle new team members and how to train them – because that’s the main problem you always have new students in your team almost every year. For example we create and record workshops we can reuse every year because they don’t really change a lot of the time for example a CFD workshop to get the people work with CFD aero simulations as fast as possible (Siemens STAR-CCM+). And in the way we use our CAD system (Siemens NX). Alumni are a big help here.
Alumni: Alumni are a huge success factor. We try to keep them close to the current team so that they are helping teach the new people how to do this and that – how to work – what is most important – what they have to look for – or how they can get started with all the other problems. This training is mostly organized by alumni so they can teach the new members. Also from sponsors, and institutes from the university. To keep a close exchange with alumni for example is the ‘alumni night’ – that’s a special event every week so we are inviting all the alumni from previous years to come by they have a defined date and place to come to greet each other as well but also to help the new team members and design reviews with senior members.
Sponsors: We have long-time sponsors that are supporting us with knowledge and with technology – they help us to get the people started to help them with the development process we also use the institutes at the university – we have a big university behind us and almost every institute of the university is happy to support us with knowledge – with machine tools or whatever needed.
R&D-Process: We have a very defined development process we repeat every year. This starts with the pre-concept architecture stage, during the last events or just after the last events of the summer. This is mainly data analysis from the recent season – building up a new concept for the next car and this is mainly done along with the alumni so they can give early input to the main problems or a checklist for the next car concept.
After that we start with the concept phase, where the alumni and team members start to develop a more detailed overall vehicle concept. Then we split it up into sub-tasks for the sub-teams so they know what to do to reach the overall vehicle goal and to work together with their charges to prevent every sub team from working just for their own goals and not working together for an overall goal.
So we have a pre-design phase and ending with the pre-design presentation where every team member shows what they have done so far and are planning to do until a defined deadline. Then the alumni can have a look on the whole car over two days and get an overview and then give comments and advice on what would work and what would not work – how good they are getting along with the timeline – the process ends with the design presentation with all the alumni from previous teams – where the team shows the alumni what they have developed – how they want to build their parts – how they want to assemble their parts. They give an overview over their project timeline they’ve built for the coming weeks to build and assemble the car.
We also have a well-developed network to university and sponsors as well so for example presenting our development steps or development to the sponsors that are supporting us with the fabrication – so they can give input on what would work – what would not.
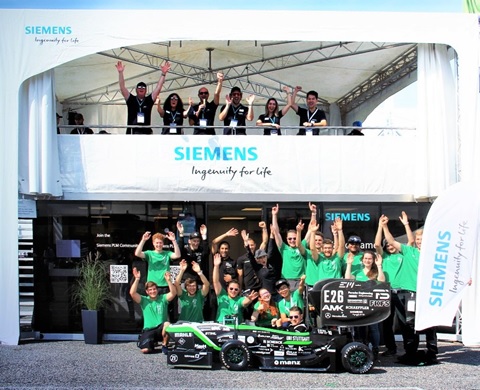
Infrastructure: A very important thing is a well-developed IT infrastructure – so we have on our own server system in-house where we host our own cloud we can put all the data we have in our own cloud – so we are sure we everyone can reach the data. We have our own wikipedia system so where everything is documented over the years what was developed. What didn’t work, what did work, what were nice ideas but couldn’t be developed in time. We have Slack as the main communication system so everything we are communicating between the team members and sub teams we do over Slack. We have some project management tools we are using for example to-do lists, gantt charts – all that where we can organize the whole team have an overview on what all the people are doing in their work package in their sub teams.
Engineering-Tools: We’re using Siemens software for example the CFD package STAR-CCM+, and NX for the CAD system. Also the CAM tools in NX, as well as the FEA strength simulation tools in Siemens Simcenter. We also use Github. We also use Siemens Fibersim for the carbon composite design of the monocoque chassis and wings. We use Star-CCM+ for the simulation of our cooling system (water and air) – as well as for aerodynamics to optimize for downforce versus drag. We plan to switch to Siemens Capital/VeSys software for electrical system and wire-harness design in the coming season. We are using the Reverse Engineering add-on in NX to reverse engineer a 3D scan of our driver’s seat.
Organizing-Tasks: How do we assign tasks to team members or how do we define goals for the team members for the sub teams? We start with a “leaderboard” meeting of the team – we get together every week – talking through what happened last week – problems they figured out that came up. Talking that through as a group that often takes about three four five hours discussing different problems – then we go into the sub-teams where the sub team leader reports what has happened or what we have been talking to his sub team – getting feedback from his sub team members – what they see as a problem or where they are struggling with – then we are talking to every separate team member – what they don’t know – which maybe they don’t want to say in a bigger group – so we can talk to them personally and then it goes all the way back to the sub team leader – and he’s giving the information back to the leaderboard – so we have an overview of what happens in the team and what are maybe problems technical and also personally.
Covid: We’ve talked a lot about general processes which are used every year every season and refine further to make them from season to season better and better – but I think also the Covid pandemic shows a lot about how we are working and how it is also kind of inspirational hopefully for other teams – because for us it was it was a really fantastic story. Let’s take the story from the end of 2019 – at that time we were a completely new team and a lot of alumni from the previous years had a job and it was a problem was actually that we had a lack of knowledge and a lack of experience in the whole team because almost everybody was new and to the time that pandemic hit our team just as we started to manufacture our new car and shortly after we had to go into home office only.
So everyone had to re-think how can we keep this whole project alive because you can’t manufacture from home – and because the whole competition said the in-person FS events were canceled for 2020 we decided to stop the manufacturing process and instead start a huge re-design process because we had a lot of long-term projects and a lot of knowledge of past seasons documented, that we wanted to revise and a lot of things we wanted to test in the old cars and on test benches – to get the best possible overall new vehicle concept for 2021 or 2022.
Okay we have now the chance to get the best potential out of the car across two years, and we also had a chance to get new team members into the team and get them trained so that they can learn new things without having to manufacture a car in ‘20, so that was pretty good for us because the team really built up expertise – at one time we had about 70 members and that was the best decision we could make into the time – because design was possible from home and manufacturing not. We kept contact to our university together to create a new covid hygiene concept – which enabled us to make the tangible work at the workshop and other tasks from home – so that the engineers who have to get some devices from the workshop for example can go to the workshop – and the others could work from home. We set up a lot of new communication channels using Discord, Slack and Zoom.
We searched for everything we could find to communicate online and to keep the spirit of the team alive. We had the potential for the new car to be really great – but on the other hand we had a lot of risk because we knew we developed a lot of new, self-designed parts where we can get some parts from the old car into the new car if it’s not working in the years before we often use some parts again to be reliable This was one risk mitigation. We also we used test benches, but we knew we will have just a limited time for testing – because due to Covid everything takes longer and at the end it turned out more or less just like we planned – we had a car together more or less at the end of May ’21 and just one week before Formula Student Austria, we had for the first time aerodynamic parts on the car. At FSA we had the fastest car in the Endurance even but sadly we had a failure of the suspension – but it showed us how much potential the car had, but on the other hand we knew the car might not be that reliable – but we kept fighting and fighting and trying to understand the car even more in the few weeks before the big event – Formula Student Germany. At FSG the car was reliable enough to make it through the whole competition. We had even a lot more potential, which now can be used for the next version of the car. During this season it was always necessary for the team to be well structured and solution-oriented, and hard work pays off. There were team members working two years on and on and on and on and now they are super happy since they won at FSG, because the whole team benefit from their experience and hard work.
Siemens – One comment and a couple of questions. Formula Student Germany is I think the most competitive, most sophisticated student competition in the world. Siemens Software sponsors dozens of different student competitions around the world in various domains not just automotive, so we have a good idea of just world-class is the level of competition at FSG.
The Uni Stuttgart GreenTeam has won the Siemens Digital Twin Engineering Excellence Award every time they’ve entered at FSG – so it’s a testament to the ‘engineering process‘ quality of the GreenTeam.
I have a question about alumni because clearly from your story, that’s one of your key success factors – especially with the high turnover that all student teams have to overcome. I’m curious how far back in years alumni are still showing up to help and what are special things you do to keep them engaged and attract them to help?
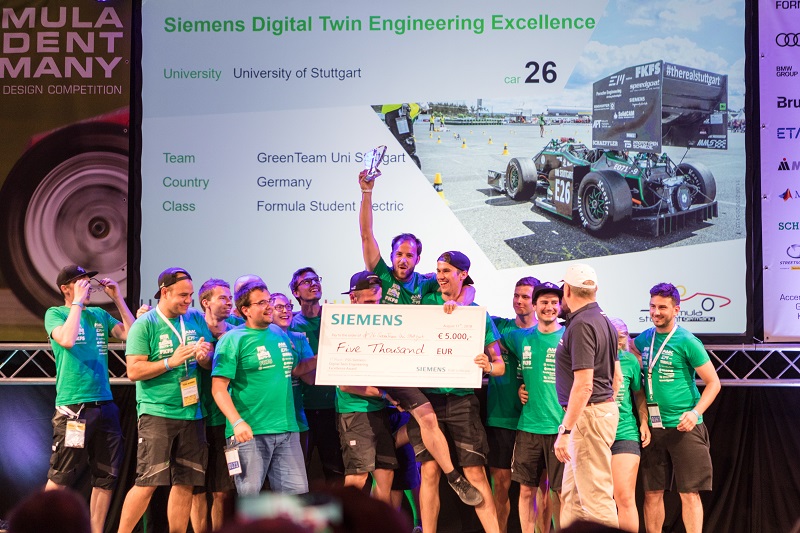
Alumni: Most alumni that are most active are from the last season’s graduates, because they still have some small projects they do in the team but we try hard to also keep the contact to alumni who were active even 4 or 5 years ago or even later – especially to the main design presentation or concept presentation – where all alumni is invited and the new team – sometimes there are alumni who were 10 years ago active and for those, it’s more about the spirit they give to the new team members – they tell them stories about how they overcame hard obstacles, for the new team members these are inspirational stories – so they think I want to do it just like them I want to have my own story. We also have those regular times – the alumni night every week where the alumni are invited to come over to the workshop and just chat with each other have a having a good time and a great opportunity to get into advice on current help find solutions. It’s not only about the technical experience that alumni can give to the team – it’s also about the personal point of view – the soft facts – they can give you motivation and raise spirits by telling stories about the tough times they lived through.
Type-of-students: Siemens – Are graduate students intentionally recruited to be leaders or is it balanced, how is the balance of undergrad and graduate students?
It’s about 50/50 undergraduate vs graduate students I think. We have both bachelor and master levels at our university – we recruit from bachelor beginning at the third semester because at our university the students have to take some important exams – so if they haven’t done them, we say okay just take one more semester or one more year then you can join the team and from there on there are students in the fifth semester and a bachelor or masters.
Siemens – that’s a pretty high percentage of graduate students – a lot of teams there are maybe 2 to 4 grad students as the leaders – with the rest being undergrads.
It’s very important to get the best out of every person I am currently undergraduate in physics fifth semester bachelor and to the time I came into the team I didn’t really know right away the topic to take on. If you are into electrical studies then that is clear you do something in the electronics sub-team but for me that wasn’t really clear because physics is a very broad and general study – that was why I took on the team captain position while other people who had more knowledge in other topics go into their relevant sub-team, and so we just try to get the best out of everyone – a very important point.
Siemens – Another question – which is the balance and how much intentional effort you put into getting different majors into the teams? In the U.S. it tends to be overwhelmingly mechanical engineers and not enough electrical or software engineering students. Can you comment on the balance of different majors and how you recruit the other talent needed besides mechanical?
Wow that’s an issue. It’s about never giving up to be recruiting and recruiting and recruiting and at some point you will be in contact with the people you need – be persistent. Yes it’s hard and it’s a huge management process but we also try to get alumni to help recruiting because they can tell the people how much fun it is and how great this whole experience is – and they love to tell them about their car when the car is on display on campus for recruiting and the people walk by. That type of in-person promotion you need to do very often then the team candidates will come. You always have to be flexible so we start recruiting in general over the whole university all topics all majors but sometimes for example your presentation is more oriented or more exciting for mechanical students – so you have the problem you don’t get that much that many electrical students into the team – and then you have to adapt to the situation – so you have to have an eye on how many people you have in the team – what kind of people – what kind of majors you have in team – then you have to adjust in the recruitment phase. We for example figured out we have not enough electrical members, not enough software members – so we said we will focus on that and we will make more efforts to go the to the right institutes/departments and make our recruitment focus more there – you have to adjust all the time. Do you have Questions for Greenteam? If readers have questions, you can just send us questions directly. It’s always nice to get in contact with other teams to help each other. That’s part of the great spirit of Formula Student. info@greenteam-stuttgart.de is the team email.
—————————————- RWTH Aachen team ———————————
RWTH Aachen Ecurie AIX Team Interview
Team Organization Best Practices (& with Covid)
https://www.ecurie-aix.de/
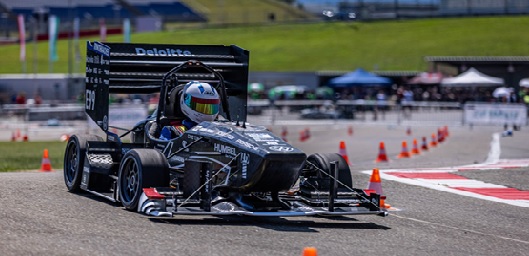
2021 Formula Student Austria – 1st place Formula Electric
2021 Formula Student East/Hungary – 3rd Place Autonomous, 4th in Formula Electric
2021 Formula Student Germany – 4th Place Autonomous, 4th in Formula Electric
RANKED #6 in the world for Formula Electric
out of 203 teams, as of 3/22
RWTH Aachen Formula Student Team Interview:
See a video specifically on the technology development of their cars at: https://www.youtube.com/watch?v=lotYXZW4xU8
See the first place autocross lap from an on-car camera for their Formula Electric car at 20221 Formula Student Austria https://www.youtube.com/watch?v=0WPRK_FA-DU and the team’s related FSA video https://www.youtube.com/watch?v=rrFjt_12KaU
Intro: We bundled our answers a bit by the topics that Siemens suggested. Our team was founded in 1999. Since then we built from 1999 to 2013, ten combustion racing cars and nine electric cars as well as three driverless cars. We have now achieved in 2019 and 2021 top five placements at FSG each time – gaining something over our previous points records and this season we actually achieved our first overall win on an official competition which was Formula Student Austria – and also this year with the driverless we achieves two podium positions. Last week we actually were at Formula Student Italy and we managed to beat the competition in all the dynamic disciplines we were just lacking a bit in statics which is why we missed 1st place overall by a slight margin. So that’s us that’s our ’21 season successes.
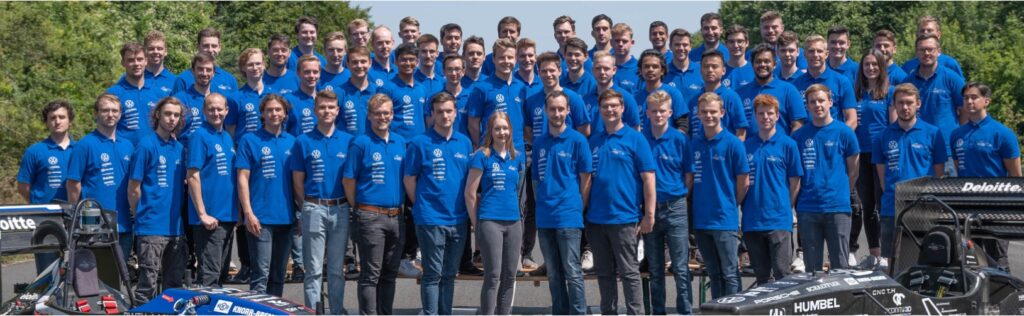
Recruiting: Regards the recruiting phase – first of all we always try to publish as much as possible on social media so we keep the students in Aachen or around the world up to date what we are doing and so we are on different platforms like Instagram, Facebook, LinkedIn and YouTube. Our most popular platform is Instagram. For recruiting itself we always do twice a year info day (or virtual-info day as needed for Covid) – so actually on this Thursday we’re doing an open workshop day where all the students who are interested in our team can come and visit the workshop and every team or sub team explains their tasks. In the COVID times we did it virtually – so we had a zoom call and invited everyone in the university all the different majors and so there were i think around 100 to 150 people in these zoom calls from the university. Also in this call we split up into different groups and explain what the main tasks are and yes so these are the two mandatory recruiting events we will do – in the beginning of the year around mMrch and around September-October.
Recruiting: The main criteria what we’re looking for is a team-spirit, strong motivation and interest in the motorsport area – so we don’t set the tasks or set the goal we want only we want only to have the best students in the university so we don’t ask for any grades what they achieved until now – so the most important thing is that they are motivated to learn and to be part of the team and another thing is that they should find a task which they really like and which motivates them because otherwise it won’t work – in the whole team in the season – and so in the beginning when we decide to get the people into the team after a conversation – we have eight weeks training so they aren’t fully part of the team yet – so we look if they work together with the people – if it’s socially okay and if it’s technically okay – they do their job well. So after these eight weeks of probation we can decide okay is it time to split or is it time to go full in membership, and they are 100 percent part of the team this is our way to go and until now it worked really well because it’s hard to determine the people who will work out or not. \
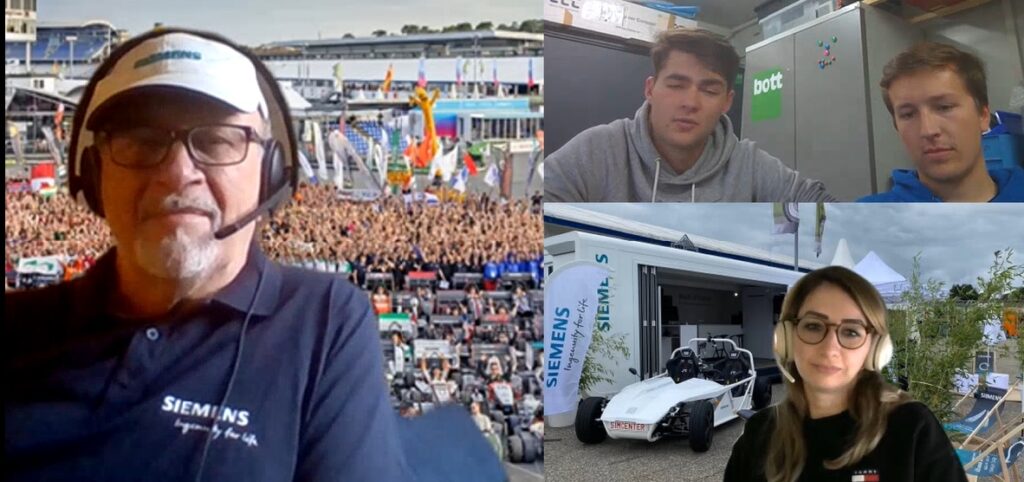
On-boarding Members: Member training is vital – so once people are accepted fully into the team we have a couple of different mechanisms. First up we have internal resources that we keep to document every part development. We have a wiki system where for every car, every season, every single part gets documented and every assembly. The people that are responsible for the developments are advised to do very detailed captioning of what of their process is – there’s protocols and documentation for every development meeting so that everybody can see where decisions come from or where input gets delivered – every member has access to the complete model (digital twin) of the car and can see what other people are are working on. There’s internal workshops to orient new members- it’s very common that we will have meetings that include alumni in order new members to learn for example some tricks in the software because while people get acquainted with – for example Siemens’ NX CAD in university in Aachen that’s a part of the curriculum for mechanical engineers. But the course doesn’t cover the very deep end of the software such as how to create surfaces very nicely – so that’s where most of the time like coaching from alumni for example would help virtually during COVID because none of this could be done in person and we actually started recording these sessions which is rather nice because you know you have these courses you can use for a lot of people – for example where one alumni just sat down for a day teaching advanced CAD and now everybody can profit from that for the seasons afterwards which is quite nice – so there’s an upside to what happened with Covid and how it forced us to change our behavior in that way. I think that’s for training most of it yeah so and there’s Siemens’ Xcelerator Academy online learning we use that it’s a nice training tool yeah.
Documentation: We always try to be very transparent and document everything, so that the knowledge the people gather during the season they always have to update it and after they finish their product or their part they always have to do a summary – and in our team meetings we also do little speeches where every team member or from every sub-team someone explains their tasks and their parts so the knowledge gets spread in other groups – so you’re not focusing on your part only – the car is a highly integrated system – so it also helps for people to see what the other groups are actually doing and constructing – so sometimes members move to a different sub-team after the season is over (sometimes in-season) – when they say oh this is much more interesting or I like it more and I’m better in it than my previous task. In the beginning, it’s more the smaller tasks we give to new people because we do not expect them to be the greatest constructors in Europe – so we always start from zero everyone who comes in the team – it starts really from nothing almost and so we always try to step up the task later – and the group leader or sub-team leader helps a lot and says oh let’s have you try this and this – and then so you have the direction to guide the new people – and you can see if the people are already more creative or trying new things – and yeah so they get bigger tasks and more complex tasks – so it all builds up over the season and most of the time in the second season when you have a full season done – the tasks are the more complex tasks which have a lot of interfaces with other groups and it is our way we are going right now – and another big thing in our team is alumni.
Alumni: We have really strong support from alumni. Sometimes an alumn will present in our team meeting about their company experience, or there are a lot of alumni who actually are in our communication channels frequently during the season – and they give feedback so they say – oh we did the similar approach a few years ago but we had such and such problem – so you should try this and that – so there’s a constant feedback we get from alumni who already built a car – this is the main factor which I see as a critical point because we have a lot of people who didn’t build a car before – because here we built a new car in September 2020 and a lot of members of that team left the team in October 2020 after the car was built – so we had a relatively new team last season – now we are building a new car and so to go on the next season where only a handful of people have actually built a car. It’s a really big task so it’s a huge help to have support from alumni who advise on how to build a car and could help us in manufacturing and designing parts.
Siemens: Do you have a specific outreach program for alumni? Do you have a specific way of notifying or motivating the alumni to give feedback?
Alumni: Yeah so our project plans have alumni feedback built in, so first of all we discuss it in our active team and after that we present to the alumni so we have a specific date where they can check our designs and look it over. We don’t have the problem that our alumni aren’t motivated – they are always almost every few days they are in or every day they are on our communication channels and discussing with us our projects so in this case we have a really strong alumni presence. There’s a handful of core alumni though that are from like past three seasons that are pretty active – like the we use a virtual workspace to communicate so they’re also in there – the alumni going further back are not as active but they are kept informed by a weekly newsletter – so whenever we have the weekly team meeting there’s a presentation compiled by all the groups with all the things that happened in the week – whether it’s testing or designing the car – or anything else. This is also sent around to the alumni just to stay up to date though maybe they cannot come to the team meeting or they don’t have time for the team meeting anymore because they’re working – but they can always get up-to-date by reading those couple of slides of presentation on what the status looks like.
Goal-Focus on Winning: For team motivation it’s also an important point – it’s about achieving the top three at FS Germany – you want to beat your previous points records – you want to just on the top steps of the podium at FSG – and build a car that is capable of it that. It is what everyone basically has to work for and believe in – and which people if they’re really motivated for the project if they’re motivated for motorsports and they can identify with that and that’s something everybody can work towards – it’s how the right decisions get made for the car – and to have a team have a really successful winning team you obviously need to be one unit that needs to be very integral – no disparities between the people and to bind them together – so we do a lot of team building events and that’s something that was hard during COVID – we used to have the irregular ad hoc team building activities or even the design weekends where we just go out into the countryside to a house and put up our computers and just keep designing all weekend all day or night…
Covid: but these in-person activities just couldn’t happen during COVID – which we obviously tried to make up for by doing similar thing with virtually and also virtual team building activities we just you know everybody’s cooking in his own home and we’re all connected via call and you know drinking beers at same time, and stuff like that it’s things that we did to accommodate for that – now luckily we’re in the position again where things like team buildings in person can be done safely because you know every i think at this point basically every team member is vaccinated so you can meet up again in the workshop so that is a good thing to be safe.
Program Management: Let’s move on to the next topic which is around project planning – from the beginning of the season the team leaders get together and set a plan for the season which is the main structure when do we want to fabricate the car – so that determines when is the design-freeze – when we do our public rollout of the car – and when do we do our first test drive with it. So we do the main structure beforehand – after that we go to our sub-teams and sub-team leaders and discuss with them what needs to happen to achieve these goals or on these deadlines for example there are more complex parts for example gearbox and engine and so these projects need to have a focus – so it’s a plan we set in the beginning and with the group leaders and set goals and steps in between – so first of November is the design freeze – so from this point on – every design or concept decision is made and after that we are only designing the final production – and because we do it these steps and the deadlines – we always can check it if we are ahead of the time plan or are we behind and how much and why is it so. This is our way to control ourselves because sometimes it’s easy and it’s really fast that you lose the control of the time and your priorities and dependencies, but yeah so these are the little steps and every team member then gets a task from the group leader and also in communication what are they able to put in into the project – and how many hours a week – and how much time and knowledge can they give the team – so yeah this is our way to plan the season. But there’s always some things you can’t plan for – for example if a sponsor manufacturer cancels their part fabrication or has delays, but in these cases we always gather together and set a compensation plan really fast and/or create a special task force so we have a few people which are chosen to – for example look for new sponsors or manufacturer and then call them and do all the arrangements – and the other part of the group or the team still works on their parts so it doesn’t happen that the whole team stops because one piece is delayed, to keep the whole team running.
Do you have one person who’s kind of the project management specialist and keeps up the Gantt charts or whatever?
So the goal is that the team leaders the team captains are the main people who control the project plan, and after that – we have our sub-team hierarchy where the captain looks over the overall plan and Gantt charts after that the group leader for each sub-teams, and so with our talks between group leader and sub-team leaders we always check it in every at least every week and see what’s the status.
Simulation: Let’s change topic over to simulation. There’s the different design phases – first preliminary concept design and then later on the actual part design once concepts have been decided. There’s structural FEM simulation for example structural simulation along all the way – so for preliminary design to check viability of certain concepts and they are put into an FEM those are parts that are obviously not optimized very much but we use different simulation tools for that – so yeah so it’s a structural simulation.
Our car is highly dependent on aerodynamics so CFD simulation with Siemens STAR-CCM+ – is a very big part of the overall concept and there’s I think millions of hours of CFD simulation done every year with the help of the university computing capacities. Which is rather amazing that they’re able to provide us with that much computer horsepower. To validate these simulations we are obviously also doing physical testing. For example when you are doing the carbon monocoque chassis design you’re validating your structural simulations by just testing the panels which you need to do for the structural equivalency calculation – there’s also things like FlowViz paint for validating the aerodynamics on the testing days I think that was done last week on the car, so you know postseason you’re just starting to like if there wasn’t time before – so in the postseason you’re looking at your designs again whether everything from simulation worked and for example the numbers for the rear wing or the undertray actually correlate with what happens when you place little strings or FlowViz paint on the car with the available resources. Often time is a very limiting factor – with an infinite amount of sensors we could measure everything on the car but that is very much the limiting factor why we only do a certain amount of testing.
Post-season validation really pays off for the next season’s car design. The simulation data follows us around the whole season because with the all the aluminum parts and carbon parts, these structural parts always get simulated and yeah so in this season we did a few posts or test validation tests because we had a little bit more time because we had a car in a workshop but not that we tested everything we could to refine the simulations for next season. This is a vital step for the digital twin type methodology applied to Formula Student.
Documentation: Yes the importance of documentation and how we get people to comply with documenting things well – so there’s knowledge-preservation. To go through the whole process – when someone gets a new task or a task assigned – people firstly have to put up a new documentation site for their part so it’s the name after the part in which they’re designing or constructing – and after that the people have to work on it and with it because in every group session the group leader should check the documentation to see if the people keep the site updated! – you have a list structure there with the requirements for the part we want to build – and then the rules which what do we have to what routes this part has to comply with – so we go through the whole documentation process and development process in this site – after a few weeks or the concept decision – we did that last year we will do it this year again in a few weeks.
Another key to quality docs – we do a cross reading when people chang the documentation – so someone from another group has to read the documentation for example an aerodynamic guy has to read a documentation from the gearbox or suspension sub-team. So they need to understand it and they have a formula where they say okay i understood everything or if they can’t, then the author must improve their documentation to pass the ‘stranger readability test’. On top of that we have a design report which after for every part itself there’s a conclusion in PowerPoint or summary PowerPoint where the rough concepts, the main goals – the biggest problems and the stuff are collected and put together – which then help us to build our design – but also this helps the people to summarize everything they did in this season and to make it a bit nicer to watch because the documentation are sometimes long or they’re just CFD pictures and comparisons between a few different angles. So, with this design report you can just summarize it into a clear presentation. When you get a new task you always first read the related documentation from the past year – so they see what did we did last year with this part because an upright will still be there in two years and so you can see what design process have we done and what are the concepts we did – and why didn’t we choose concept a, b, or c. So this is the main documentation process and on top of that there are these presentations in team meetings and those ‘cross readings’ which help us as well.
Siemens: What do you use for storing design data or managing it or what kind of software to use for storing the documentation?
Documentation happens in our internal wiki – so that’s where all these documents are laid out in with a basic text editor or some html editing. The design data it’s just in file management basically so all the CAD files from the car are just held in storage where everybody has access to with specific rights management so that everybody can access basically all of our all of our data.
Engineering Software: Our tool chain consists of Siemens’ NX CAD – plus the integration of STAR-CCM+ for fluid dynamic simulation really quickly. For me personally I’m a chassis guy so I personally love Siemens’ Fibersim – it’s an important tool for me and it all happens in one integrated suite of software which is you know quite nice. We’d like to integrate Teamcenter in our daily workflow and I’m working on it. Also from what I’ve heard from other teams, the integration of all the tools into NX is really deep – so you basically never need to leave it in order to you know open and work with your parts in different ways – so in our own experience the integration is really tight – really helpful – what we work with on a daily basis.
Siemens: We have talked about the ‘digital twin engineering methodology’ and one of the hallmarks of that is that you not only feed-forward from simulation to design and testing but when you get test results you then update the virtual model – is that a process that your team follows?
Digital Twin/Simulation, Aa: Yes – for example the FlowVis paint test we did last week is used to validate CFD in STAR-CCM+ for the aerodynamic simulations – so if the simulation is equivalent to the real life – so we can see if we need to change anything in the CFD parameters. I think until now the data is not fully analyzed yet – but I think so far the STAR-CCM+ simulation is quite accurate.
We have a new suspension we built ourselves this year – so it was a little gamble with all the stresses we have on this whole suspension – so we did a tensile test and now for next suspension we want a little bit more safety margin because we heard from a lot of teams that they had a few suspension problems – but that’s nothing to do with the simulation – so we have the tensile test to see if this simulation is correct and if there are manufacturing errors from our side so this is an important part.
Wrap-up: well thank you for giving us the opportunity for FS teams to help each other – that’s really the spirit of Formula Student – so when Siemens asked us to do it there was really no question and yeah it’s a great thing I think so I’m really looking forward to what the other teams are going to say.
——————————– TU BERLIN INTERVIEW ——————————–
FaSTTUBe – Formula Student Team of TU Berlin
https://www.youtube.com/user/Fasttubeengineering
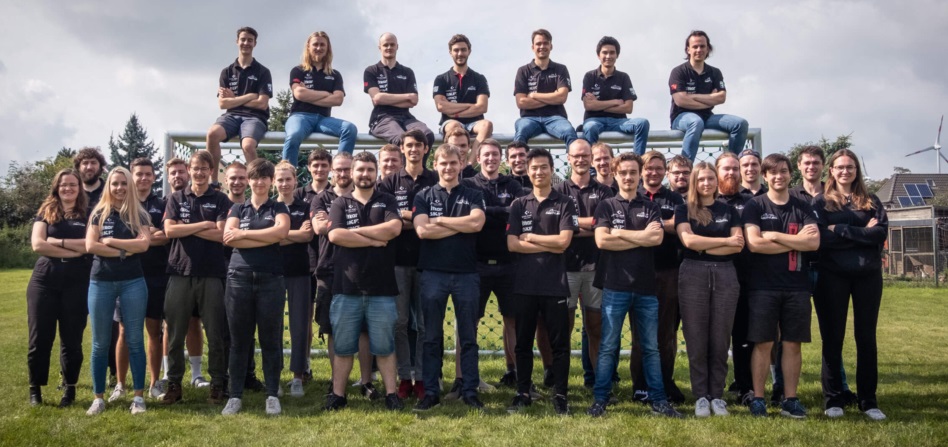
RANKED #40 in the world for Formula Combustion
out of 612 teams, as of 3/22.
Intro: I’m Philip. I’m the former team captain from last season. We’re a team which used to build three race cars. For at least two years now we started with a combustion car. The team started 16 years ago. This year (2021) we were really happy that we were awarded with the great Siemens Digital Twin Engineering Excellence award – and we hope to progress our journey with even greater goals for next season.
[Max] Thank you Phillip – I’m the former technical-leader. I’ve been in that role for two years of the last three seasons and the one before that for our electric car – but not for the combustion or driverless car. I also managed a lot of the engineering software including our Siemens Teamcenter and PLM data structure. Now to Felix because he’s my following guy because he’s doing our CAD management in charge of managing the whole PLM and Teamcenter operations.
[Felix] I started at Fasttube in 2017. I worked in the aerodynamics department first – making wing parts – then i led the aerodynamics department for one year. Now I’m basically taking care of the CAD admin process which I’ve done last year for the front-end team support and teaching our team members. This year I’m like getting the full picture and also do the back-end software support so server and installation guides and all of that.
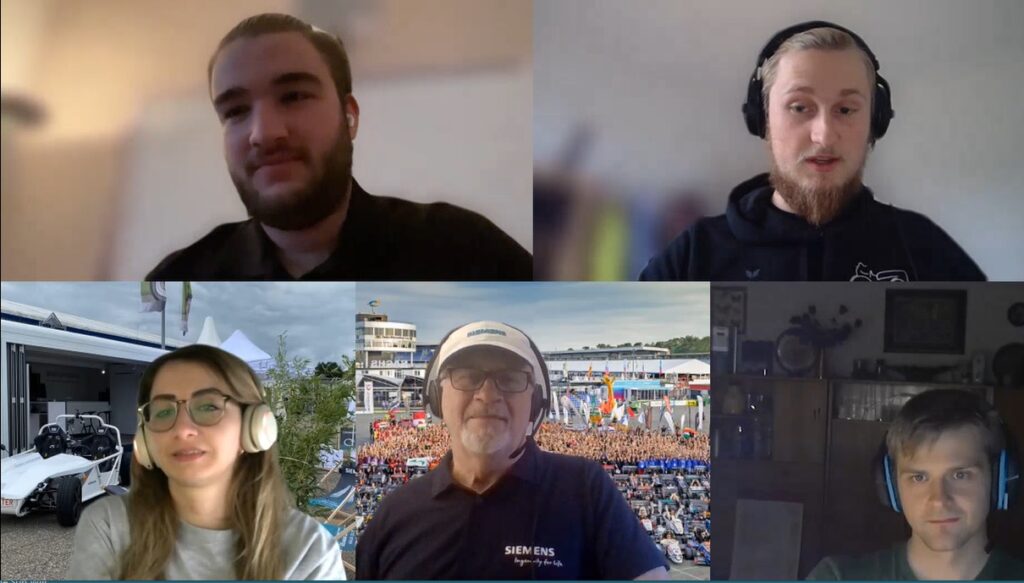
For TU Belin team achievements, i could start listing off our positions at certain events but I don’t think that’s really the biggest achievement here – i think why other teams should listen to us is because we’ve turned out a competitive consistently car every year since our inception many years ago – we even built 3 cars last season despite Covid, and we didn’t miss our rollout times – we didn’t miss any Formula Student events – we have our cars ready to pass inspection and compete year after year like clockwork – that is a good enough reason for any team to consider our advice because there are many teams out there who struggle with this kind of consistency, and if you’ve made it to the event with a running car you’re already a winner regardless of position you end up with – because you’ve made something that so many other students couldn’t even dream of doing, and i think that is something that you should be proud of.
Onboarding Members: In all formula student teams that’s always the problem, but we rely on certain tools and workshops – our knowledge transfer still has a verbal part where we try to get the alumni to teach the new upcoming generation – and particularly we do that down to the sub-module level. For example we try to show them how to design things in CAD. We just try to maintain all the knowledge across years, such as simulation knowledge and put all that in our Siemens PLM software, Teamcenter.
Our new member training is structured so we have a basics and an advanced course. The basic course is compulsory for every team member where you learn the absolute basics – such as how to open a design, how to use Teamcenter, how to open a part in Teamcenter to look at it – also how to construct a simple part in CAD- not really a parametric one, which is going to be in the advanced course. So that everyone can take on some kind of technical role right away even if those people are just in the team for organizational reasons, so we have this as a culture in the team that everyone can do some technical tasks to a certain degree, and in the four weeks we teach them the basics on NX CAD construction – then assemblies – how to create simple drawings and manufacturing details – and in the end how even marketing/business members can clean up the CAD for 3D rendering! – for external comms so that marketing people can put compelling images in newsletters and on social media. This course is not only to transfer knowledge it’s also one of the methods to evaluate how technically sound our applicants are – so it’s also a part of member quality control for us to see how motivated someone is – how do they work – are they working on tasks immediately – or are they waiting till the deadline to finally start so we can see what kind of roles you can you can give a team member – especially a new team member. If you can get this kind of information about members early, it’s very important.
Yeah i think that’s a very, very important part that you just said because we follow a little different philosophy in recruiting members than other teams. Some other FS teams start with tests, and they only look for members who were in the highest semester of their studies and all that – but we try to follow the slogan – ‘you don’t have to be a full engineer if you want to come to us or a full professional – you just have to want to become one’ – and that’s how we collect as many people as possible – focusing more on the will or the motivation to be part of the team seriously, so we don’t have to invest in a person then they drop out, or they don’t always find the specific certain role that they love for example. Motivation and passion is number one, not necessarily they are tops in academics.
That one week introduction – which we usually try to do or at least two or three times early in the season, is where we try to find those best tasks or position for those members so they can freely orientate to their best role – they do the NX CAD course as foundation, and then they see oh maybe I really like to participate in simulation for aerodynamics, or i want to help the team in other roles, so then we can move them for example to operations where they can help with the custom manufacturing report or some other role.
Motivation & Covid: The motivation and the emotions we feel with our competition to the members and that’s what the main goal is we don’t have to actually show them what the right things are what we do it’s more like yeah – you’re participating in a high-performance motorsports team – you get the idea – so that’s what’s driving us primarily – besides internships and stuff – but for example we had some difficulties this season with a few members and motivation – maybe we can talk some about that how we try to keep the team rolling despite some motivation issues.
Yeah motivation is a big topic due to Covid because in our experience the most motivating motivation core of FasTUbe is that before we could come to the shop to sit together, work together, and maybe drink a beer together after working, and this wasn’t possible due to corona – so we had to find another way around it – how can we motivate our members – the leader, or the technical leader or the team captain or who else in the leadership has to be the first person in the office and the last one is going home – so there is one person which you can anytime talk to – if you have a team member you have some concerns about your part, or your assembly, or if you’re not motivated enough, or you have personal problems with time – and fitting team tasks and private stuff into your timetable — there’s a person which you can always talk to. This is one of the core motivation things that members can come talk with us every time you need – and it was really hard to compensate due to corona – because we weren’t in the office at all – so you have to find a way to transport this team leadership/mentoring philosophy to a virtual medium, and i think we did this really really well – because we created a regular timetable online with zoom and teams meetings where people can come without making an appointment – and for example do their university homework not even something that’s team related – and they can come together help each other, and yeah we were trying to create this in-person office spirit online – and yeah we did this really well my opinion – but it was really really hard – and some people left the team because they told us they don’t have their motivation anymore, they can’t bring it – so it was quite hard but for most of the people yeah we can still go on.
Some other things we did during Covid – so usually engineers love to play games so we held game nights, board game nights – as well digital games obviously – but it was all about getting the team-feeling again – as well as seeing those faces – we try to reduce the amount of meetings we have – although we say okay we have to social distance – we feel like those virtual meetings aren’t always as productive as in-person you know obviously – you have someone on the phone or something – but you don’t always see if this person on the phone is really paying attention, and that was our philosophy reducing the length of the meetings – but making more quality of working meetings – as well as having social fun meetings – not as just for work.
Knowledge-Organization: Going back to what good examples we have of how to keep the knowledge in the team we always like to point out our “lessons-learned paper”, and based on that – the development of our requirement sheets which how we try to avoid making mistakes from prior seasons.
Yeah i can give you an insight so as you probably know, requirements are the backbone of every project, and because of the Formula Student rule set and because of our high ambitions, we have quite a lot of requirements to track. In the aerodynamics department, where i spent most of my time, there are quite strict rules and goals. The difference between a very good aero downforce package and a mediocre one can be quite minuscule in the details – – so what we used to do is to have to start a season off with validating all outstanding requirements from the season before– usually we have the goal to have our car fully validated by the first event – but the aerodynamics department usually brings updates as time goes on during testing – so we have a little bit left open the first step to ensuring a quality car for the next season – is to get that done to a point where we know the old car inside and out and then we give the new members of the team these old requirements – and give them the task to create the new requirements sheet – not the ones that really know everything – they are the ones that then go to a controlling function – they will look at what you guys have done and figure out the things they missed where there is a little bit more potential and then they will finalize that for design review – one which we just like had a week ago – where it is presented to the rest of the team – not only the people that worked on it – but the others as well – and this process really helps to get everyone on board – you don’t have only senior members that decide everything – you have a senior leadership that helps out where it’s needed – but everyone else has a chance to make their own experiences and bring in their own ideas so you take the high level of creativity you get from people that are not affected by a previous season – and you get the benefit of experience in the end as well – and after we’ve done our requirement sheet, it is then finalized for the step below, so you start in a big overall concept for the overall car – then for the sub team (such as aerodynamics, or suspension, or electronics – and then from there, you go into the assemblies and modules – so you basically have a top-down approach for requirements that are then inherited down the list – until we end up with our part requirements and this process ensures that there’s nothing that gets forgotten and that the level of detail is manageable at every stage – so that’s how we like try to uphold our high quality standard that we try to impose on every car that we build.
Siemens: Can you give an example of a mistake or a dead-end design direction that you have documented that won’t be repeated because you documented it?
Yeah – a good one is the 2019 aerodynamics development of the front wing. In this season, we had a personality issue – we had not the most compatible people in our CFD department and also not the best communicators. They designed an aerodynamic part for the main plane of the front wing in such a way that it obstructed the further development of the underbody panel so we lost quite a lot of downforce due to that one part – and since we locked down the design very early as it’s a front wing, and you just do downstream development usually we couldn’t change that much on the car, we couldn’t get that mistake out. But we’ve made sure that this is something that everyone knows about and it’s also one of those issues mentioned earlier where even a tiny detail – it was the angle of attack from the center section which was off by about only five or six degrees and that that really hindered the rest of the car’s downforce and cornering grip. So this is one important information that’s been documented and passed down – it’s also in the requirement sheet for this year’s car – it’s still inherited onward because we always start with the prior season’s requirement sheet and that caution is in there – it has a red exclamation mark “don’t do this again!”.
Alumni: To reinforce what Felix said is – and what i think is the foundation – is have a strong alumni culture – the better your alumni culture, is the better your team will be. For example, the different seasons team shirts, what we call our classic shirts, we keep wearing, it’s a minor thing but that’s a thing you keep people not just from one season but from multiple seasons together as a group – so they become something greater which we call the classics – to have a special status – usually they are there to be as well teachers they come for well for example they don’t have to be there all the time to help but they get invited as alumni to the design reviews – where the new team shows them all the great exciting things they’ve came up with – and their job is to say okay guys that’s a great thing that maybe think about it because we did that previous season and it didn’t work out – so that’s how we try to include alumni into the team without actually forcing them to spend too much time – and obviously you can offer them beers and stuff – and that’s how you get them there and you try to keep them connected – alumni can really help keep the team rolling – and they’ll be there in hard times too if you really need work and if you need workforce – and you really need people who know how to do a wire harness for example – they’ll be there and that’s why ‘m really happy to be part of it now and really happy that we had that in the last season and those people you need to keep those people together yeah.
Siemens: How do you keep alumni engaged?
My oldest alumni contact was all the way back from the founding years – i think the next oldest alumni is from 2012, so about 9 years back. i think the most important way to keep them in engaged is that they have fun with our project after they graduated – we do have an instant messaging group where we collect all the phone numbers of alumni, i mean it’s voluntary. we post updates to alumni – such as fun things that happen and they’ll remember that they had fun there as well – so this keeps them engaged in our project – and usually when there’s a big event like rollout of a new car ceremony – they’re all excited because there’s an exciting new car – and as the quality of the car has improved over the years you kind of see that they are proud to be to have been part of that evolution – to be part of this history-making team as well – which is also a major factor i think that people are proud of their work, what they achieved as part of the progression over the years – regardless of how well or how poor the season went – it’s an achievement to build such a challenging racecar – it’s not normal for students to be able to do such an amazing design-build – there are many students who wouldn’t be able to do that – so this is something that we can’t forget about and this kind of winning, progressive team culture is upheld throughout the classic alumni culture – we don’t take this for granted it’s a hard-fought victory whenever the car starts up.
Siemens: Can you comment on what software you use for knowledge preservation design management etc.
Tools, Berlin: We heavily relied on our network attached storage – where everyone would upload their design and manufacturing documents so we have several terabytes of data – i know that’s not the best way to do it, so we started to using an online management tool called podio, it’s from citrix group and there you can organize the entire team into handy little apps – and we have a knowledgebase in there where you can basically write a condensed version of what you’ve worked on – what were the problems – what went well – and then you link your network attached storage with all your documentation and design data – and you have a short blurb on this – very organized, very easy to read web page and then you have the full data behind on our network attached storage. We’re currently looking at integrating that with Siemens’ Teamcenter- – and we’re wanting to do the requirements engineering there as well – I’m hopeful to implement Teamcenter this season.
The Crucial Manufacturing Sub-team: Regarding team structure, we have a specific department for manufacturing – really creative which helps the designers from the construction to the manufacturing to the testing time – they help the designers to know if their part is actually manufacturable on our machines – and help you to get the part perfectly done in our workshop – or with the sponsors and external fabricators. This sub-team works with every single other department in the team – so they work with suspension and frame – with aerodynamics – with the powertrain guys – as well as with the electric guys maybe those with the electric guys because often our electrical guys are not that expert at manufacturing – something that is not electrical or not cables or PCBs – so yeah they help every people out and this is really core of our process – and really good thing, if you want to keep a big team running well especially if you have to manufacture such a lot of parts.
And this manufacturing department get some special praise when it comes to the cost report judging because those are the guys who present at every meeting when we discuss making the parts – so they have a good overview of what’s actually on the car they’ve been there at all stages of development. We have a dedicated cost report crew, but it really helps to have someone who says well did you actually think about this one part and I made a few changes – so have you checked whether you have the updated version because it sometimes slips through the cracks especially late changes, and for replacement parts those usually are easy to miss – because sometimes you have to go off a script of design because something broke and testing and all your documentation – all your careful planning can protect you from something going wrong it happens – then you need a quick fix for that and to have this available and ready for the events is one of the more hidden benefits of having this kind of manufacturing department around because they know they had the headache of dealing with it and they will know and maybe in addition I think the manufacturer guys are the most hardcore team members – because if something broke during vehicle testing, these are the guys who are in the workshop for 10 hours and maybe until five AM – to save the next day’s testing we have to have the replacement part quickly – so we’re very grateful to them.
Siemens: One other topic before we go is how you approach what we call a digital twin methodology the whole simulation feeding into design and then testing feeding back into your virtual models – I find the top German teams are really quite good at that.
Digital Twin: I would go with our digital twin award application – which we presented at FS Germany this year – due to corona we had a lot of time and in the home office and one of these evenings Philip already mentioned one of the team members had the crazy idea – yeah maybe let’s get into some battery modeling – and we said yeah why not? It was crazy because none of us had any experience with battery modeling or with digital twin electrical, so we started with really small chunks of how can i approach the capacity of our battery cell – and then it started to grow and it went on to become a quite big topic after one or two months – and this was the point when we said okay we can’t handle it at ourselves and we called some some alumnis, to ask what can you tell us about digital twins and this is how we started and how we ended up getting the Digital Twin Engineering Excellence award from Siemens – and yeah we used quite a lot of Siemens software, also Teamcenter and NX CAD – for the whole product data management and the construction as well so the physical thing was all in Teamcenter and NX CAD, and some electrical stuff was in Matlab but we are thinking about how to get our Matlab model and stuff into Siemens simulation software for the integration.
Siemens: There is some nice battery modeling capability in Siemens’ Amesim simulator. Amesim can be a lap time simulator for all the car’s sub-systems, even a tire simulator, not only some really nice battery modeling features.
Conclusion: i think the best thing i can recommend to other teams – is cooperate – what our experience was all the Formula Germany teams – is although we’re competing each against each other hard – we love to help each other out – if it’s just parts manufacturing knowledge – if you lost something on the way don’t hesitate to ask other teams – they’re happy to help you and even provide you with the necessary test data that you couldn’t collect last year due to Covid – and i think that’s the foundation you’re not alone with the struggle – with the problems you have and if you’ve faced them together you can come up with great ideas together.
Yeah, I’d like to add on to that – i think one of the most important things is even if it sounds a bit shallow – is to have fun at what you’re doing! I’ve seen teams at events that are so stressed out beyond belief – of course some of them are because stuff broke – but some just are for no real reason – so have fun at what you’re doing – it’s all volunteers here – and don’t forget that – I mean a certain level of professionalism is important – but a certain level of having fun and being a student – being a young person at an event, that’s also important. Siemens: Well thanks so much to you and all 3 german teams for sharing their winning ways.