2021 Digital Twin Engineering Excellence at Formula Student Germany – RWTH Aachen U. Team Excels!
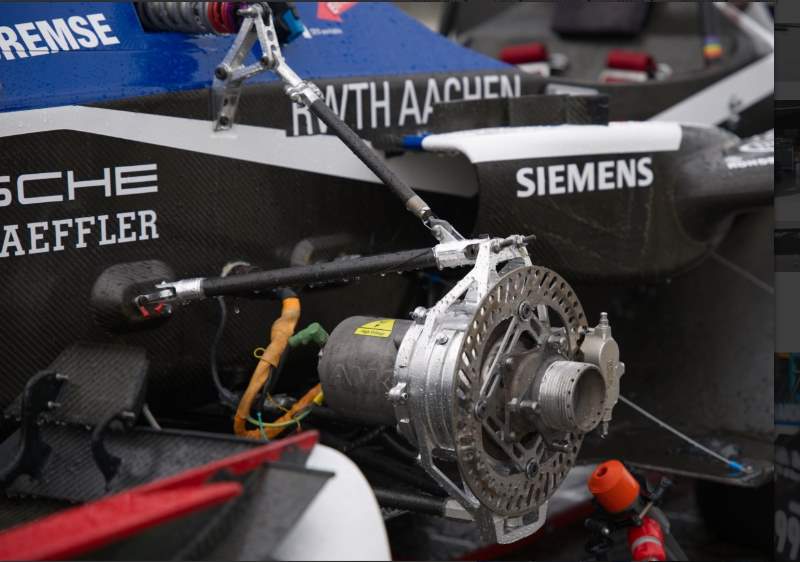
Formula student Germany (FSG) is one of the most sophisticated, most industry-engaged university competitions in the world. Siemens Digital Industries Software has been a proud sponsor of FSG for many years. In 2021, Siemens’ panel of expert engineering judges awarded the 4th annual ‘Siemens Digital Twin Engineering Excellence Award’. We applaud the teams who applied despite the very difficult 2021 pandemic situation.
The digital twin methodology, enabled by Siemens’ Xceleratortm integrated suite of design and simulation tools, has become a vital trend for industry – as well, every top-tier Formula Student team in the world uses digital twin style methodology, and enabling Siemens software, to a major degree. In this graphic below, see the results of FSG ’21. In the most competitive country Formula Student event in the world – the dominance of Siemens software centered teams is obvious.
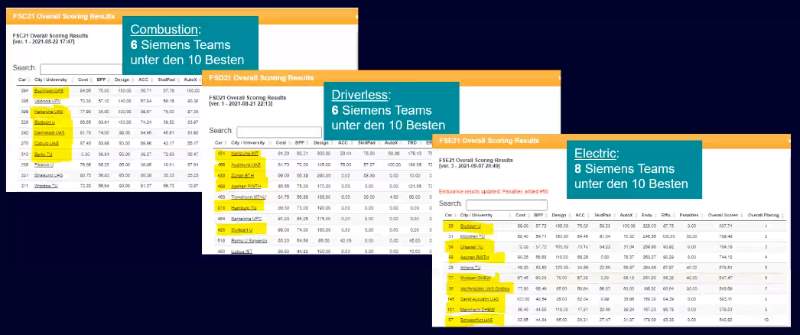
(pun intended, sorry
Electric drivetrain, Driverless/Autonomous and Combustion drivetrain.
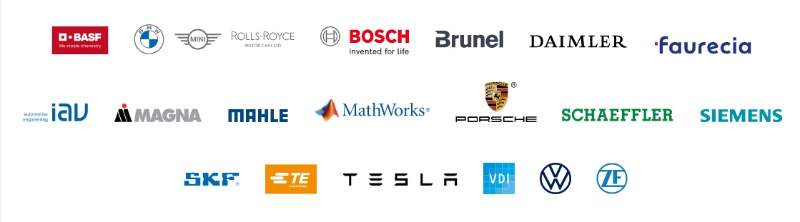
We encourage all types of student teams, not just Formula Student teams, to adopt the simulation-centric, feed-forward/feed-backward – digital twin method. This methodology will grow your own team’s sophistication and competitiveness in future years, plus give a boost to your career. You can find a few examples of digital twin methods at Siemens’ industrial customers at https://www.sw.siemens.com/en-US/digital-twin/.
- This quote from the Aachen team’s Digital Twin Award application document exemplifies the digital twin thought process:
“…the digital twin from the laptime-simulation is used to set a focus for all other design sub-teams. Test data from older cars is used to parametrize the car for simulation. The results of both twins are then compared and through a feed-forward/backward loop, the laptime simulation is aligned with the log data. Afterwards, new goals get set and groups work together to find designs for parts to reach the desired result. After an intense design process, the car gets finalized and manufacturing begins. The digital vehicle´s laptime simulation results gets compared to the newly manufactured cars log data and adjustments are made to both over the season. The entire process starts anew with the next season… The development takes place as a full digital vehicle model in Siemens NX.”
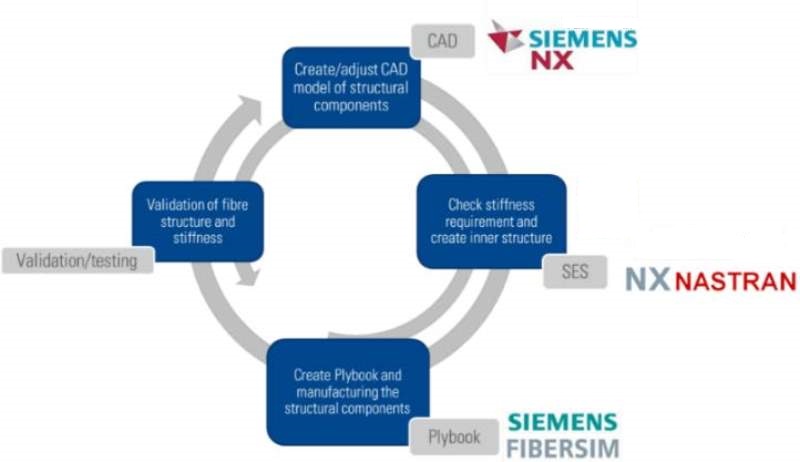
In past years, pre-pandemic, a lot of teams applied for this prestigious award. For 2021 there were two years of cumulative impact on teams, plus another european FS event reset too close to FSG’s start date. Knowing this, we reached out to a number of top German teams to see if the Covid restrictions and other factors made it too difficult to finish their racecars AND write a special-award application. The answer was “yes, it is EXTREMELY difficult this year”. However we decided to keep continuity, a symbol of normality, and EUR rewards for even a small number of teams that might find the time. Well, only two teams were able to submit an application. But to be very clear – our judges were very impressed with these two teams’ understanding of the digital twin methodology! – The winners very much deserve these awards. Even compared to 2019 when we had many applications to choose from, the 2021 applications had excellent merit.
The 1st place winner of the 2021 Siemens Digital Twin Engineering Excellence truly impressed our judges as they explained their digital twin process across multiple engineering disciplines (mechanical, electrical, software, systems-integration, data management), and how they maintain and grow their organization’s expertise and knowledge base over the years despite student graduations and the pandemic.
The top Digital Twin expert team award winner for 2021 was RWTH Aachen University’s Ecurie AIX team! The team designed, built and competed two race cars in two classes. In the Formula Electric class they came in 4th place overall in this hotly competitive category of 38 teams. The team also scored a 4th place in the incredibly difficult autonomous Formula Driverless class. Just prior to FSG, Ecurie AIX also won 1st place overall in Formula Electric at Formula Student Austria,
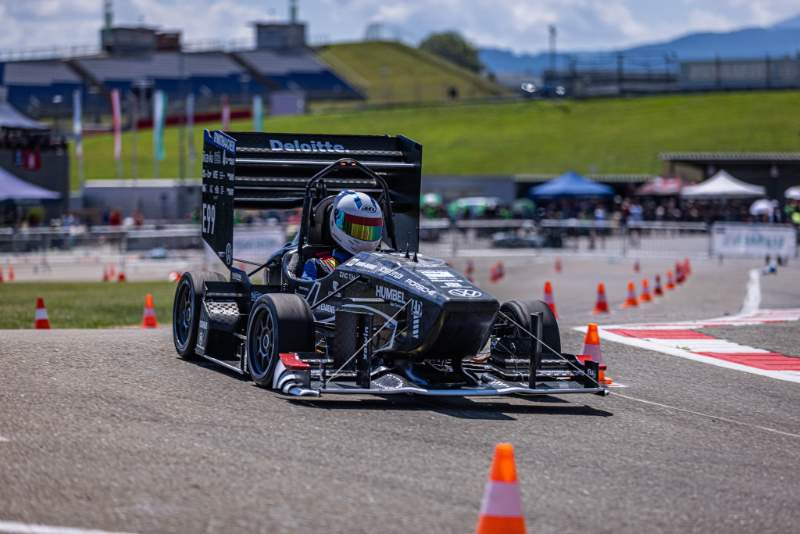
The Digital Twin Award 2nd place team focused their application document on how they developed and used a digital twin of their Formula Electric battery system and drivetrain. This ‘digital twin expert’ team is the Technical University of Berlin’s ‘FaSTTUBe Electric’ team! See more information about the team at https://fasttube.de
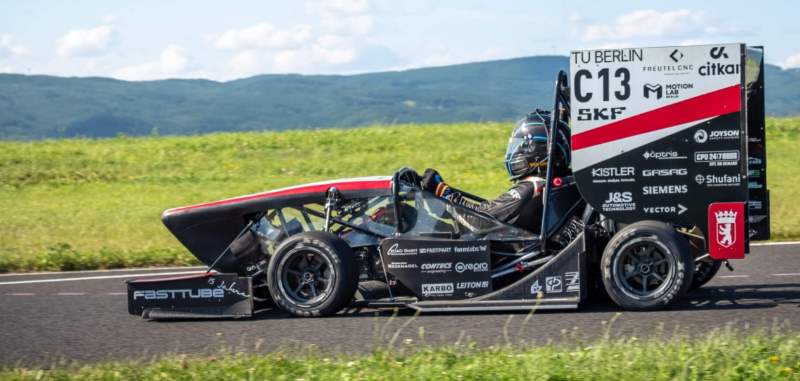
The remainder of this article focuses on the RTWH Aachen team’s Digital Twin Award application.
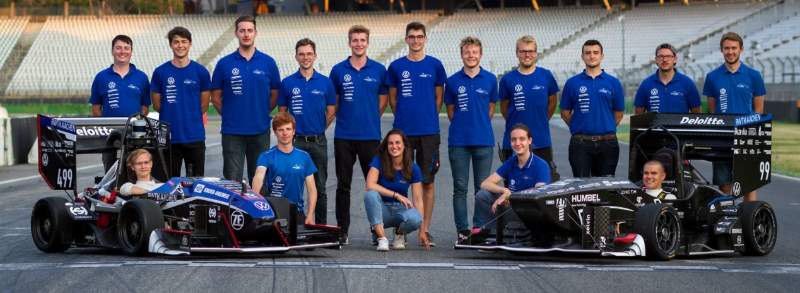
The team also described their aerodynamics-downforce digital twin style process. (Downforce enables incredible cornering power, like a pro Formula-1 car – but optimized for a much tighter race course at lower speeds.)
“The process starts with identifying problems in airflow and getting target benchmarks from the performance department. After concepts are designed, a full car model for simulating aerodynamics is made using Siemens NX. Afterwards, we compute the airflow at the most common driving states, identified in the laptime simulation, using Star-CCM+ on the HPC from RWTH Aachen. With the help of our innovative pre-modelled, automatized curved or strait wind tunnel and kinematics included car model, it only takes 15 seconds to load and replace parts of the digital car. Furthermore, by using Siemens Star-CCM+ and a computer cluster, a full car simulation with complete evaluation-ready images takes only 3.5 hours. Those images are then used in our in house built system which identifies differences between the images and shows them in real time, cutting down on time spent simulating. We iterate through a feed-forward/backward loop with other design sub-teams until we achieve our design goals, and the part can be manufactured. The real product gets validated in various track tests and the results are analyzed to improve our airflow-simulation accuracy as well as our next seasons starting point.”
For the 2021 racecar, the team ”made major changes in the HV battery design, since our lap time simulation yielded that we could finish endurance with a much lower battery capacity than in the previous cars. With a smaller battery, we can save a significant amount of weight but also run into new problems such as overheating or running out of energy during the race. To address these problems, we developed an electric-thermal co-simulation of our battery in cooperation with Siemens. Using real-world measurement data, we were able to parametrize an electric-thermal battery model in Simcenter Amesim. By linking the electrical simulation in Amesim with a CFD simulation of the battery container in Star-CCM+, we established a multi-physics digital twin of the battery. The CFD simulation models the air flow through the battery container. The electrical model is running on data from an endurance race, and the generated heat in the cells is exported to the cooling CFD simulation. With returning the simulated temperature of the cells back to Simcenter Amesim, we close the loop of the simulation. This digital twin of the battery is also used to improve the SOC estimation and ensure safe driving behavior to prevent under- or overvoltage errors, which would end the race for us. By establishing this process, we can choose the suitable cooling fins, fans, battery container layout, cooling strategy and other parameters even before the battery is built.
“We used Siemens’ Fibersim composites design and simulation software to get the shapes of the carbon fiber plies and then cut them out using a CNC cutter. This helped with the manufacturing of the carbon wheel rims, which proved hugely beneficial as all rims … are just 8 g in weight apart.”
“The frame design goals require the rear of the monocoque chassis to be large, due to the higher torsional stiffness. With these conflicts in mind, a CAD model is designed in Siemens NX. The model gets evaluated by both the aerodynamics and frame departments in a feedback loop until all design conflicts meet the mutual agreement.”
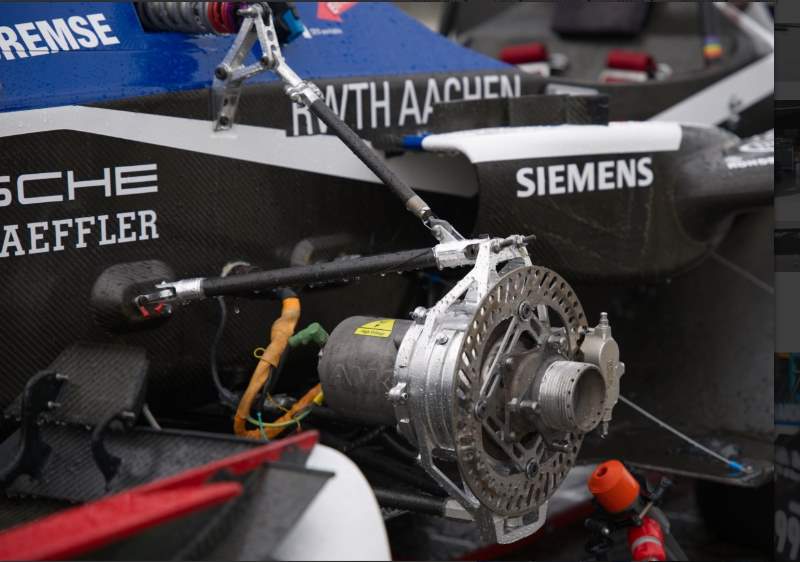
The team went on to state: “Another part of the car where we leverage software to our advantage is the wire harness. Capital and NX allowed us to streamline the production process and resolve possible issues before they could arise. For the wire harness the real work starts after the first plans on which electric devices to include in the new car. Capital Design helps in this process by creating an overview with all electric components and their connections between them. Over the years we developed an intricate color code for different signals so even when facing a bundle of numerous wires later in the car it is possible to identify the wire’s role. But Capital Design is not only great at displaying wires in different colors, we also utilize its material library. We inventoried our store and included all wires, connectors, etc. into the Capital Library with their materials, weights, colors, etc… While working on the electric part of the wire harness, the development also continues on the mechanical side. Packaging is one essential task of designing a harness as you need to reconcile the limited availability of space with electrical necessities like signals taking the shortest possible path to ensure their quality. For these considerations NX was able to throw in its support. Here we could position all devices and reserve spaces for the harness.”
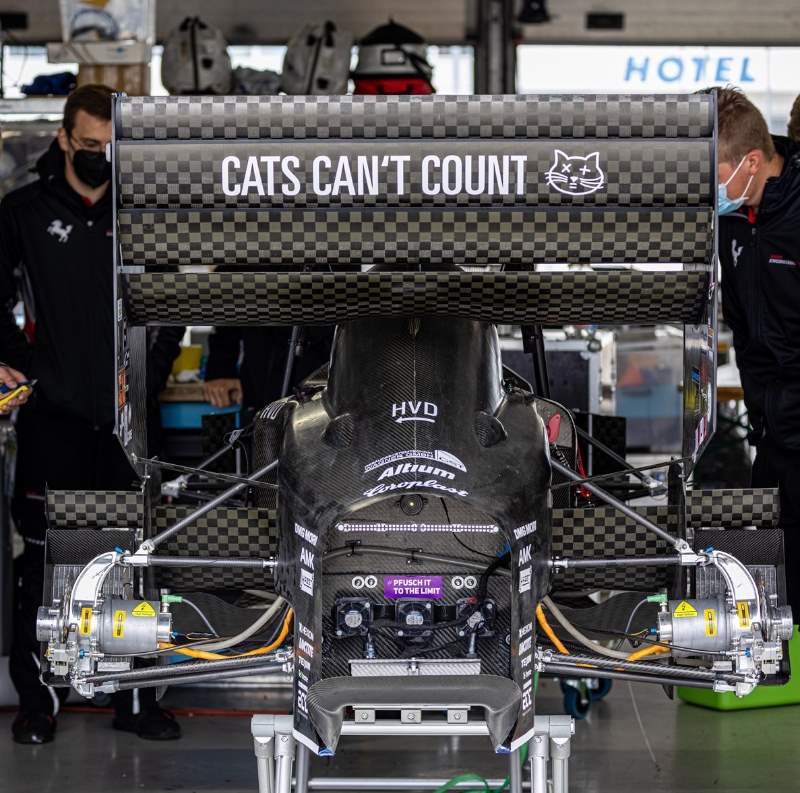
“…But this has not been the biggest advantage we got from the software. Capital and NX showed their true potential by using them together. Capital knows the connections between all devices and also the type of wire used to connect them, thanks to its library. This data can be imported into NX which then maps Capital’s wires to the devices positioned in the car’s chassis model. NX routes the wires between the devices along the predefined pathways. Now it is possible to determine if enough space has been reserved for the wire harness or some refinements in the packaging are necessary. Doing these steps can save many hours or even days compared to traditional wire harness manufacturing after the chassis is built.“
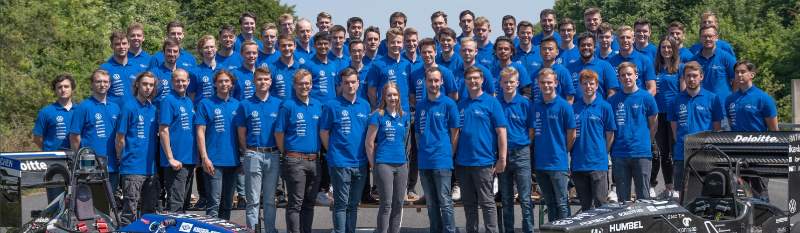
Here are the brilliant, hard-working student-engineers and marketing/business members of the 2021 Ecurie AIX team!
“..even the manufacturing process itself can benefit from the full power of Capital and NX. The geometric data from NX can be imported back to Capital where extensive material lists can be generated giving a detailed overview over all necessary materials. At this point software again saves critical time on our way to a fully functioning race car as the chance of not ordering the right materials is greatly reduced. The third software product used during harness manufacturing is Capital Harness. Here we position all connectors and devices connected via bundles as they would be in the car. Capital Harness then displays useful information like connector type and wire colors directly next to the actual connectors. This harness plan can be printed out and laid on a table, so you directly know where each device should be in the harness. The last step where we get a huge software boost is the actual manufacturing process. Capital Design can generate a very detailed list of all wires in a harness with wire colors or diameters and connected ports. But most importantly they can also include the exact wire lengths as we imported the geometric data from NX. This way we can process one wire after the other from the list and laying them on the harness plan from Capital Harness. By just using this generated list we ensure that we do not omit any wires and have all data in one place necessary to cut the wires and assemble them on the table. Thus, Capital and NX streamlined the harness manufacturing in multiple ways and therefore saved invaluable testing time due to a reliable and thoroughly planned wire harness.“
How did the Aachen team get through 2 seasons of the pandemic?! – building incredibly complex racecars while operating at a world-class level. The answer is they are very intentional about personnel management and communication:
“Every person joining to our team has an 8-week probation time where they will be introduced to the overall workflow at Ecurie Aix. In those 8 weeks, everyone gets an introductory task to learn working at the digital and/or real product. It is very important for us, that knowledge gets passed on from generation to generation.”
They also use various software such as Zoom, Slack, and a wiki package to keep the team progressing and coordinated.
In addition to technical judging, Siemens delivers on-site workshops at events, plus online training and tech support. There are even technical resources specific to challenges of different competitions. Student teams around the world that create FS cars, solar cars, airplanes, rockets, robots, underwater autonomous vehicles, and other competitions benefit from such things as Formula Student or solar car or rocket – aerodynamics CFD simulation templates.
Get your Team a No-Cost Software Grant!
Student competition teams can get free student editions at this site, or apply for full commercial functional software packages, (some of which don’t have student editions) using this online form.
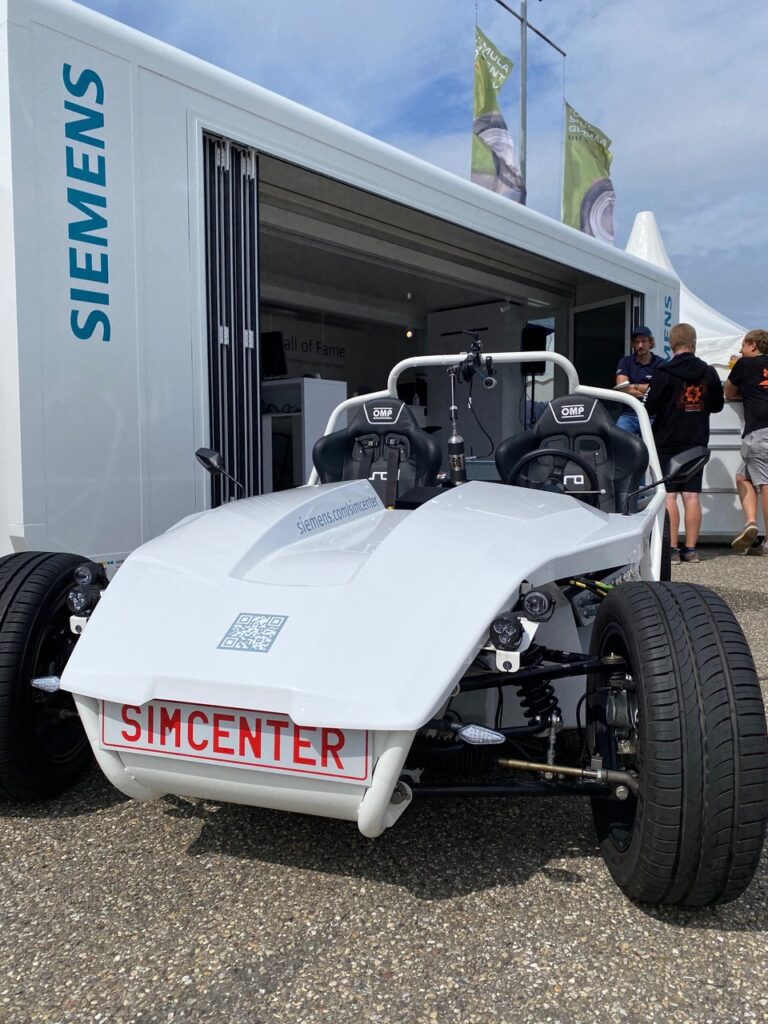
Congratulations to the 2021 Siemens Digital Twin Engineering Excellence award teams, and we we hope to get back to a more normal situation for FSG 2022!
Comments